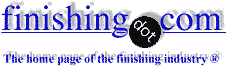
-----
Sulfuric Acid Anodizing Type IIB procedure & problems
November 10, 2020
Q. Hi, I was checking TYPE 2B (THIN SULFURIC ANODIZE), I have a current density of 16amp/ft^2, a thickness of 0.15 mils, coating weight of 600 mg/ft2. Everything is in accordance with MIL-A-8625, but in the corrosion test (salt spray method B117, 336hrs) I am having the issues shown in the picture:
Also I have the TYPE 2 CLASS 1 (SULFURIC ANODIZE) and it shows the same white stains but without pits.
Both processes are using the same tanks.
Do you think that it is from silicates or chlorides in the seal tank (sodium dichromate 52-75 g/L)?
For chlorides, we are at 78 ppm.
- Quer´taro, Mexico

⇩ Related postings, oldest first ⇩
Q. We are familiar with the sulfuric acid anodizing process. We have been asked to perform sulfuric anodize coating Type IIB. Can sulfuric acid anodize coating Type IIB be done in the same procedure and tank contents as sulfuric anodize coating Type II? In order to reduce the coating weight and thickness (from 1000 mg/ft2 minimum for type II to 200 mg/ft2 minimum for type IIB). What are the process parameters that can be changed (times, voltage)?
Keren Poran-Avrahamiaviation products. - Gilon, Israel
2002
A. Sorry I can't help with the thickness change, I knew 2B coatings to be dyed black.
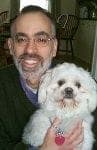

Tom Pullizzi
Falls Township, Pennsylvania
2002
A. Just to clarify and prevent confusion, note the difference between Type IIB "thin film sulfuric" and Type II Class 2 "dyed sulfuric". A Type IIB Class 2 would be thin and dyed (say, black, for example) but a Type IIB Class 1 would be thin and undyed.
I don't recall parameters, but I believe that Type IIB cannot be performed in a Type II process tank - it's not a matter of just varying the time or voltage, which might give you the desired coating weight but compromise coating performance. Concentration, temperature, time and voltage, as well as second order interactions will have to be worked out to get an adequate coating.
James Davila- Dayton, Ohio
? Hi James,
I must admit, I have never heard or read the term "thin film anodize". To which specification are you referring?
Thank you,


Tom Pullizzi
Falls Township, Pennsylvania
A. Hey Tom,
I was referring to MIL-A-8625 / MIL-PRF-8625 [⇦ this spec on DLA]F. Paragraph 1.2.1 lists "Type IIB - Thin sulfuric acid anodizing, for use as a non-chromate alternative for Type I and IB coatings..."
I notice it doesn't actually use the term "thin film" - I guess that's just something I've picked up along the way. (I have seen the term in industry specs)
James Davila- Dayton, Ohio
Thank you James,
I was looking at revision E, which does not mention the thin coating. What kind of coating weight or thickness are we talking about here? The E revision mentions 70 millionths of an inch, is that what you call thin? I don't see why the sulfuric bath can't provide a thin coating, or at least, I can't find a reference that says it can't be used.


Tom Pullizzi
Falls Township, Pennsylvania
A. Hey Tom,
As to coating weight, the MIL spec. calls out 200 to 1000 mg/sq.ft. Some might want to raise the minimum slightly if corrosion resistance is a big issue, and lower the maximum significantly if fatigue is a concern. For thickness; its been quite a while, but seems to me something close to, but under, a tenth of a mil was desired. A Type II sulfuric bath could provide a coating of that weight/thickness, but the bath/process is designed for the thicker coating. The coating characteristics (e.g. pore density and individual pore dimensions) are not optimized for the thinner coating and performance of the coating (esp. corrosion resistance) will be compromised. Of course, if one's customer acceptance criteria are looser than those in the MIL spec, a coating produced in a standard Type II tank might be just the ticket.
James Davila- Dayton, Ohio
Q. Hello Tom and James,
I made some experiments to get the type IIB coating. (The type IIB coating also appears as "thin film" in aircraft specification). The anodization was done in the tank of sulfuric anodize solution (same concentration, temperature and voltage). The results indicate that to get thin film of sulfuric anodization the times must be shorter 5-10 minutes instead of 15-20. We achieved the required coating weight and thickness, and now we are checking their corrosion resistance.
Do you know someone who is dealing with this kind of coating?
Keren Poran-Avrahami [returning]Gilon, Israel
Q. My Question is That the minimum criteria for Type II Corrosion resistance test is 1000 mg/sq. feet but when it is converted to thickness by a formula T= weight(mg) x 10 / (area x density of Alumina) the result comes out for 1000 mg to be 30 micron which is out of thickness range mentioned in the MIL standard. If someone can clear this please do.
Hammad Haseeb- Islamabad, Pakistan
October 20, 2012
A. Hi Hammad. I don't follow your arithmetic (you've only shown us a piece of it, without any numbers plugged in). What are you using as the density of the alumina, and what is the meaning of the "10" term?
But remember that the coating thickness is measured per side, whereas ^ some coating weight specs include both sides. Maybe you just omitted to divide the coating weight by two?
Regards,
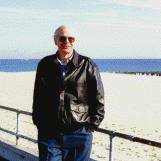
Ted Mooney, P.E.
Striving to live Aloha
finishing.com - Pine Beach, New Jersey
October 22, 2012
Q. Thanks a lot Ted Mooney!
The formula for thickness measurement I have seen in Canning Book for Metal finishing in which 10 was written as separate term and Alumina density as 2.7, the area in the MIL standard is 0.128 sq. feet, and if the minimum weight 1000 mg is put in grams as 1 g then the answer comes out to be 28.9 micron, i.e., 1 g x 10 / (0.128 sq feet x 2.7)
The second paragraph of your answer is a guess or a confirmed statement? Please reply.
Hammad Haseeb [returning]- Islamabad, Pakistan
October 24, 2012
A. Hi again, Hammad. For a formula or calculation to work, the units must balance. So let's check ...
If you want thickness, T, on the left side of your equation to be expressed in µm, [i.e., m/1,000,000] then the units on the right hand side of the equation must evaluate to m/1,000,000 ...
You have already said that the weight is expressed in mg [i.e., g*1000]. You have given us the density of alumina in g/cm^3 [i.e., g/(cm x cm x cm ), i.e., g/(m/100 x m/100 x m/100)]. So the only way the formula makes sense is if the area in the formula is expressed in cm^2 [i.e., cm x cm, i.e. m/100 x m/100]. Checking ...
T[m/1000000] = weight[g*1000] x 10 / (area[m/100 x m/100] x density[g/(m/100 x m/100 x m/100)])
So, indeed The Canning Handbook formula is:
T[µm] = weight[mg] x 10 / (area[cm^2] x density[g/cm^3])
If you want to use a similar formula but with the area expressed in square feet, you'll need to insert a conversion factor of 929 cm^2/ft^2:
T[µm] = weight[mg] x 10 / (area[ft^2]*929[cm^2/ft^2] x density[g/cm^3])
Doing the arithmetic with your numbers, I get T = 1000 x 10 / (1 x 929 x 2.7) = 3.99 µmThe second paragraph of my previous response turns out to not be applicable now that I understand what you are trying to calculate. And your factor of .128 ft^2 (the area of the test panel) isn't applicable either because the 1000 mg weight requirement is per square foot, not per test panel.
Regards,
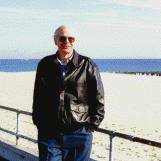
Ted Mooney, P.E.
Striving to live Aloha
finishing.com - Pine Beach, New Jersey
Thank you Sir!
Q. From your second para it is found now that the minimum thickness criteria (corresponding to minimum 1000mg weight) is 3.99µm. But I want to ask again is that the minimum thickness criteria for type II anodized layer in MIL standard 8625F ? Kindly reply.
- Islamabad, Pakistan
October 25, 2012
A. Hi Hammad. Sorry, I am not going to answer that one. It is a 20-page specification, with links to other specifications, and it says what it says ... I won't attempt to condense it and miss something. Further, there are frequent revisions. You'll have to read the spec and decide for yourself what you think it says with respect to your personal situation. Sorry.
Regards,
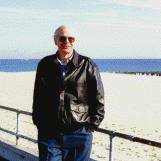
Ted Mooney, P.E.
Striving to live Aloha
finishing.com - Pine Beach, New Jersey
October 25, 2012
Thank you Sir!
Q. Sir,
If we convert 1000 mg to g, i.e., 1 g and eliminate 10 factor in the
numerator then we can get units of micron in the answer. What is you
opinion sir?
- Islamabad, Pakistan
October 25, 2012
A. Hi. No you can't skip necessary conversion factors like that. A
meter is 100 cm and a micrometer is 1/1,000,000 of a meter, and a
milligram is 1/1000 of a gram -- and you must always insert correction
factors for these conversions as necessary. As you start canceling
out these strings of conversion factors, we learn that if you express
everything on the right hand side of the equation in centimeters and
milligrams, multiplying by 10 gives you the thickness in
micrometers.
Regards,
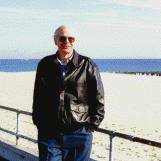
Ted Mooney, P.E.
Striving to live Aloha
finishing.com - Pine Beach, New Jersey
Q. Hello everyone,
I am Ander Echarri, Paint Process Engineer in Aerospace industry. We are discussing the compatibility of waterborne epoxy primers applied on thin sulfuric anodized aluminum surfaces. We discovered serious problems of adhesion recently, after changing from chromic anodizing to the thin sulfuric.
I would very much appreciate any piece of advice you can give me and all the information you can provide if you have seen this kind of evidence in other processes. Thanks.
Ander EcharriAerospace coatings - Berantevilla, Alava, Spain
May 30, 2013
A. Hi Ander,
Poor adhesion like you are seeing tends to be more to do with surface cleanliness rather than compatibility issues. That is not to say that the particular combination of thin film sulfuric anodizing and primer is not a problem. If you have been using this process for a while and this is the first time you have seen the problem then I would suspect cleanliness, if you have seen it frequently it could be a compatibility issue, but just as easily be a cleanliness one, problems with mixing of the primer, application issues, drying issues ... unfortunately the list goes ever on.
If you haven't done it yet then I would suggest you "walk the process", from anodizing through to final testing of the primer, that way you can pick out anything that is obviously wrong, put it right and see if it solves the problem.
Aerospace - Yeovil, Somerset, UK
June 3, 2013
June 6, 2013
Thank you very much Brian
As you recommended we have followed the entire process from the beginning. We visited our suppliers to ensure the conditions of the anodizing, the cleaning and painting. Some dust and excessive humidity might be the reason.
Anyway, we are changing to a new Chrome-Free primer. We have also performed the process in some trial specimens with both primers, and the adhesion is much better with Cr-Free one.
To sum up, the waterborne primer quality plus the non-strict conditions of the process generate those irregularities.
Thanks again for your help. I will keep you informed about our progress.
Kind Regards
Ander
Aerospace coatings - Berantevilla, Alava, Spain
How to color thin film sulfuric acid anodic coatings without sealing or dyeing
Q. I am investigating chrome free anodizing processes, i.e. Thin Film sulfuric Acid Anodizing (TFSAA) to replace chromic acid anodizing (CAA). TSFAA anodic coatings, however, are bright and surfaces look like etched/pickled surfaces contrary to CAA coatings which are dark grey.
I am looking for a way to color TFSAA coatings to grey, without using a seal step or deying step, in order to be able to inspect parts whether or not the anodizing was succesful on all locations. Supposedly additives like oxalic acid or sulfosalicyclic acid without using a seal or dye step should work.
Does anyone have experience using these additives or know what concentrations of these additives should be used?
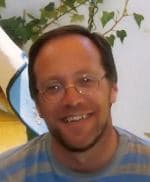
Arnold Langeveld
Engineer Surface Treatments - Papendrecht, The Netherlands
November 18, 2014
A. You didn't mention what your required thickness is. There are a couple of things an anodizer can do with just plain sulfuric acid anodizing to influence the color of the coating without dyeing (most seals do not impart any color to the coating).
1. Lowering the temperature of the anodizing bath leads to darker coatings
2. Increasing the current density will also lead to darker coatings.
3. Increasing the film thickness will lead to darker coatings.
Alloy selection also plays a role. 5000, and 3000 series Al tend to have lighter natural coatings, while 6000, and 7000 tend to be darker, as well as 4000 series.
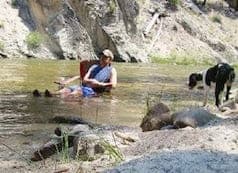
Marc Green
anodizer - Boise, Idaho
November 19, 2014
Dichromate color blotchy on Type IIB anodizing
Q. WE HAVE RECENTLY PROCESSED AN ORDER OF 6061 MATERIAL TO THIN FILM SULFURIC ACID PROCESS WITH A DICHROMATE SEAL. THE PARTS WERE IN THE DICHROMATE BATH FOR 23 MINUTES /RINSE/ RINSE / RINSE/ 1 MIN WARM WATER THEN A 10 MINUTE OVEN DRY. THE PARTS ALL OVER LOOK NICE AND UNIFORM IN COLOR EXCEPT 2 OUT OF THE 10 HAVE AREAS THAT ARE NOT COLORED AND LOOK BARE OF THE DICHROMATE. WE CAN RULE OUT POCKETING OR BLIND HOLE BLEED OUT. IS IT POSSIBLE FOR AREAS OF THE 6061 TO NOT ABSORB ENOUGH OF THE DICHROMATE TO CHANGE THE COLOR?
Darren Irving- DETROIT, MICHIGAN
October 21, 2020
A. Hi Darren. I personally haven't seen Type IIB anodizing done. But I'd suspect that the reason for it absorbing no color or insufficient color from the dichromate is the same as for Type II anodizing: no anodizing or insufficient anodizing in those areas of those pieces. Try to do an anodizing thickness test.
Luck & Regards,
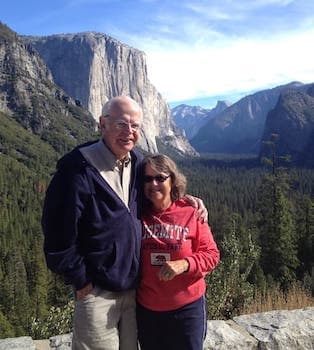
Ted Mooney, P.E. RET
Striving to live Aloha
finishing.com - Pine Beach, New Jersey
October 2020
A. Boric Acid is insoluble in mid-pH rinse water. It just will not rinse off by dipping. A 5% nitric acid "post dip" will remove the trace boric acid (but the Lockheed school boy engineers will not allow), otherwise, use high force spray hose rinsing. The dichromate "takes" better after the boric film is removed.
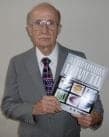
Robert H Probert
Robert H Probert Technical Services

Garner, North Carolina
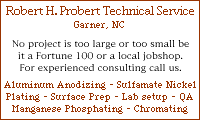
October 31, 2020
Thank you
There is no conductivity in the area but I will check the coating thickness for uniformity.
- DETROIT MICHIGAN
November 2, 2020
Q. I have completed a dye stain seal test and the parts are dichromate sealed in the uncolored areas. Could this be from heat or other contamination. I attach a photo.
- DETROIT MICHIGAN
November 6, 2020
November 6, 2020
"Could this be from heat or other contamination. I attach a photo."
Yes, heat or work hardening from the stamping.
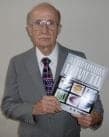
Robert H Probert
Robert H Probert Technical Services

Garner, North Carolina
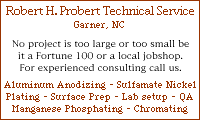
Q, A, or Comment on THIS thread -or- Start a NEW Thread