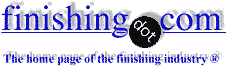
-----
Deposit by electropolishing
Hi there,
I want to deposit one of these two metals (Nickel or Chromium) on stainless steel 316L using electropolishing method in order to have in the final stainless steel with some layers of Ni or Cr. Can you help me please solving this problem.
Thanks a lot,
Tiqar tahar- Champaign, Illinois, USA
Dear Tiqar,
Electropolishing only removes metal. It never adds or plates metal onto the surface. What you may be thinking of is that electro-polishing causes enrichment of nickel and chromium on the surface of stainless steel. This is accomplished by removing more iron than nickel and chromium. This results in relative enrichment of these two metals in the surface layer.
Email me if you need further information or help with this process.
Regards,
John Holroyd- Elkhorn, WI
I am not really sure what you want as you cannot electrodeposit metal by electropolishing. Metal deposition takes place when the workpiece is cathodic, whilst electropolishing removes metal from the workpiece by making it anodic. Do you want to coat 316 stainless steel with nickel and chromium or do you want a stainless steel surface enriched with nickel and chromium? When you electropolish 316 stainless steel, the surface becomes enriched in chromium; this helps to provide the chemical resistance enjoyed by the electropolished stainless. However, the chromium is only very thin and of no engineering use, although because of its inertness it does offer a decorative benefit. I also believe that electropolishing will increase the amount of nickel on the surface relative to the level in the bulk metal, but again it is of no engineering use. Of course, what you do get is avery bright and reflective stainless steel surface that has an improved corrosion resistance. On the other hand, if you want to coat the stainless steel with engineering thicknesses of nickel and chromium, you will first need to plate the stainless steel with a nickel strike. This comprises nickel chloride 240g/l and concentrated hydrochloric acid 86ml/l. Other strikes are based on sulfuric acid but, in my opinion, they are not as good because they do not offer the corrosive properties of the chloride ion. (No doubt this will start a debate, but never mind). When using the chloride strike, operate at 3A/dm2, but for the first 2-3 minutes run it anodically (when the chloride ions start to chew up the stainless steel and give a good surface for the nickel to adhere to). After the anodic treatment, plate cathodically for a further 6 minutes or so. Everything works at room temperature. Once you have got this thin layer of nickel, you can thicken it with more efficient nickel baths. If you want good corrosion protection, put a duplex nickel down. Once the stainless steel is coated with nickel, you can deposit chromium from either a hexavalent or trivalent bath.
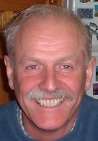
Trevor Crichton
R&D practical scientist
Chesham, Bucks, UK
Q, A, or Comment on THIS thread -or- Start a NEW Thread