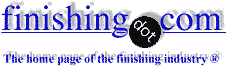
-----
Molybdenum high temp protection
Can any one let me know how we can prevent the oxidation of Molybdenum at high temperature? If we can coat with MoSi2 for this how we can evaluate this coating ? What are the tests that may require to conduct.
Shekar B Chandrashekariaih- Pittsburgh, Pennsylvania
Hi Shekar!
You say 'high temperature' but you DON'T say what the temperature is, do you? One must have all the facts. Nor do you say what this process it, which may/may not help any answers.
Certainly in the ultra high NiCr alloys, like Nimonics, it was found that after welding them that the Moly content, to quote the chief metallurgist of Wiggin, UK (now known as Speciality Metals Wiggin) had 'evaporated'.
There is a point or temperature at which ALL metals will vaporize.
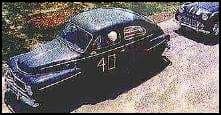
Freeman Newton [deceased]
(It is our sad duty to advise that Freeman passed away
April 21, 2012. R.I.P. old friend).
Dear Freeman Newton and All,
To be more specific the material is TZM (Ti 0.5%/Zr 0.1%/Mo 99%). The temperature which it sees 125 °C to 1400 °C. Unfortunately above 700 °C the material gets rapidly oxidized and starts to disintegrate. Moreover the material is subject the thermal cycling at this temperature. Which will cause the life time to deteriorate further. At present we have limited to 600 °C. But we would like to have a coating that can prevent this oxidation and improve the life of the material significantly. The coating should be conducting and close to the properties of TZM.
Shekar B Chandrashekariaih- Pittsburgh, Pennsylvania
Dear Shekar,
Pardon me but I'm totally clueless what this TZM alloy is for or what shape it takes. Certainly there is no plastic coating that comes anywhere near to your requirements.
Your max. l600 Degr. C temp. is 350 degr. more than iron's melting point, ie. damnably hot.
I'm not a chemist and have only a slight metallurgical background but maybe, who knows, maybe if you gave your service conditions (you sure DIDN'T mention an iota about the chemistry!) to Speciality Metals USA, they could tell you if Nickel plating might serve ... or try, too, the manufacturers of chrome.
Sorry, but I can't help you any further.
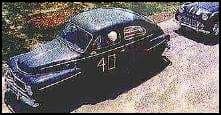
Freeman Newton [deceased]
(It is our sad duty to advise that Freeman passed away
April 21, 2012. R.I.P. old friend).
Shekar,
You need to convert the surface region to a silicide or aluminide. Oxidation will then form a protective SiO2 or Al2O3 on the surface.
Donald M. MattoxSociety of Vacuum Coaters
Albuquerque, New Mexico
"Handbook of Physical Vapor Deposition (PVD) Processing" (2010) [on AbeBooks or eBay or Amazon affil links]
and "The Foundations of Vacuum Coating Technology" (2018) on AbeBooks or eBay or Amazon affil links]
If the TZM alloy is used in the temperature between 600-1100degree,the MCrAl coating can be used. If the temperature is over 1200 degree, MoSi2+50%SiC spray coating & Mo-16.4Si-10B spray coating can be applied with a sound protection effect.
Duyezhitech.center - xi'an shanxi province, China
Looking at your temp. range - Molydisilicide coating by pack diffusion process should do the job. Plasma spray coating is fine too, but if temp. is fluctuating- chipping can occur, also porosity density needs to be low to prevent any gas going thru' coating.
Nilesh Pandya- Anaheim, California
We have a MoSi2 based coating that works on TZM up to 1150C. You really don't want to run TZM much above 1250C due to recrystallization issues.
Ted Paquettecomposites - Glen Burnie, Maryland
2006
For TZM at 1100 C, rather than using a coating, what level of vacuum would be required to prevent oxidation?
John PaulManufacturing - Bluffton, South Carolina, USA
July 11, 2011
Q, A, or Comment on THIS thread -or- Start a NEW Thread