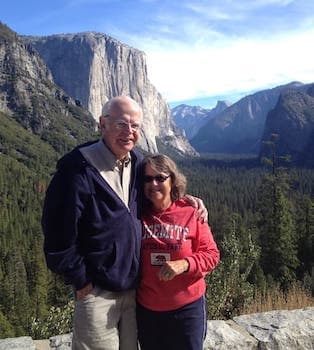
Curated with aloha by
Ted Mooney, P.E. RET
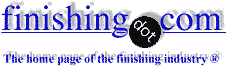
The authoritative public forum
for Metal Finishing 1989-2025
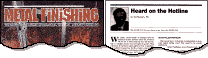
-----
Zinc oxide production by French process
< Prev. page (You're on the last page)
Q. I have plant for production of zinc oxide by French method but I have a problem related with accumulation of zinc oxide over the molten zinc which need to be skimmed. I don't know what are the reasons of this accumulation? may be due to fallen of zinc oxide from suction inside the crucible or may be due to oxidation of the outer surface of molten zinc.
What is the remedy of this problem?
- Cairo, Egypt
July 2, 2019
A. Hi Mr. El- SADEK, I think your problem has to issues. Firstly, the suction may be less and secondly the removal of candles near the opening of crucible may not be proper. They must be dropping the candle oxide inside the crucible. Also check the opening size, for a crucible with 145 litre capacity that gives production of of 2MT per day, the opening size should not be more than 2 inches. Try these suggestions.
ABHAY NAGLESelf Employed - VADODARA, Gujarat, India
October 17, 2019
Dear sir,
Can me suggest you that what have should be speed form rpm of suction blower with connected 20 HP 3-phase motor which has 1400rpm and its suction only from one furnace?
- morbi, gujarat, India
July 4, 2019
A. Hi Bhavin, difficult to comment based on motor HP and rpm.
ABHAY NAGLESelf Employed - Vadodara, Gujarat, India
October 17, 2019
Q. Dear Experts;
We are beginners in zinc oxide production by French method and we have several problems with our burn oil furnace like escape of black fumes that have negative effect on the quality of zinc oxide product, crucible lifetime, low yield and high fuel consumption.
Because of these problems, we are thinking to replace the oil furnace with electric or induction furnace. I want to know your opinions about using electric or induction furnace instead of burn oil furnace.
- Cairo, Egypt
July 20, 2019
A. Hi Mohsen, I do not have experience at handling electric furnace but that should be a good alternative. However, your problem of black spot entering the finished product can be solved by simply sealing the crucible refractory joint. And if you use gas, the impact will be much less.
ABHAY NAGLESelf Employed - Vadodara,Gujarat, India
October 17, 2019
A. Suddenly some drought on this thread. I will try some technical tips...
Many ZnO manufacturers in India still use primitive open bag houses located on discharge side of the fan. But a few have gone ahead with reverse pulse-jet type and that is certainly a better solution. I will restrict myself to such bag filters.
Here the entry to the filter should have a one or two degree downward slope to direct the flow to the bottom.
The inlet must extend inside the filter but it should only be half-round inside, only the top portion, open at the bottom.
The inlet and outlet should preferably be oriented at 180 degree.
There should preferably an air receiver near the filter with capacity 1.5 litres per LPM of expected consumption. This will reduce loading unloading of compressor. There is no need to dry the air unless you are located very close to the sea shore and fear corrosion.
Self Employed - Vadodara, Gujarat India
October 8, 2019
Q. Will there be any benefit of having fins (Extended Surfaces) on the cooling duct after furnace up to bag house?
Lesser the length, lower the static pressure required by the ID Fan & hence lesser the power consumption.
Regards,
Dinesh
Engineering - Vadodara, Gujarat
October 12, 2019
A. You are spot on. Fins will help. There are other methods too.
ABHAY NAGLESelf Employed - VADODARA Gujarat India
October 15, 2019
Happy Diwali to all of you. May it bring a lot of success to your Zinc Oxide business.
Self Employed - VADODARA Gujarat India
October 25, 2019
Q. Dear Mr. Charki,
How to control Lead content in ZnO manufactured by French Process? We are using Secondary Zinc as raw material.
Regards,
- Raipur, Chattisgarh, India
November 12, 2019
A. hope you will not mind if I answer your question. Apply Roult's law and you will get the answer. To simplify, you need to increase charging frequency, to increase zinc percentage in the crucible with respect to lead. Umesh has done some excellent work on Zinc distillation to reduce lead, but that is for purification of RM. Give more details for a specific answer.
Self Employed - Vadodara, Gujarat, India
November 13, 2019
![]() |
Self Employed - Vadodara, Gujarat India January 9, 2020 January 2020
Regards, ![]() Ted Mooney, P.E. RET Striving to live Aloha finishing.com - Pine Beach, New Jersey Thanks Ted. Let us continue the discussion. ABHAY NAGLESelf Employed - Surrey, BC CANADA January 13, 2020 A. Hi again. I'm merely the site curator, charged with maintaining its 50,000 topics, and not knowing enough about some of them, including this one, to contribute anything :-) If you wish to contribute an article about 'Zinc oxide production by French process', or any other topic, to our on-line library it would be gratefully received. Regards, ![]() Ted Mooney, P.E. RET Striving to live Aloha finishing.com - Pine Beach, New Jersey January 2020 |
Q. We are manufacturing Zinc Oxide using bottom and top dross with proper systems to ensure no insoluble matter in our final product.
Sometimes in our regular zinc dross 95%-96% Zn, we get the purity of zinc oxide 98.8%. What is the best method to be practiced for getting minimum zinc oxide purity of approx. 99.5 and above. Please share the possible reason or required design changes.
Is it possible to have very high surface area in Zinc Oxide from french process?
- Gurgaon India
February 16, 2020
March 19, 2020
A. Hi Tanishq
At 95 - 96% Zn, I think it is top dross.
Please reply to the following questions
How much is the Aluminium content of dross?
What do you do to remove Aluminium?
In ZnO, do you get high Acid Insoluble?
Are there other impurities in ZnO?
Self Employed - VADODARA Gujarat India
Hey guys, lock down is the time when we can interact. Shoot your questions.
Self Employed - Vadodara Gujarat India
April 17, 2020
April 17, 2020
Q. Dear Mr. Abhay and Mr. Umesh,
It's very nice of you to help the manufacturers with the processes and we can come together to provide better outputs and utilise lockdown.
As to my earlier question, I would like to answer to your replies.
1) We are using bottom dross which doesn't have aluminium much in it.
But in some batches we received purity of 98.7% or less than 99%.
As white seal is said to be having above 99% ZnO, some manufacturers claim white seal minimum 99.5%. Is there any changes in cooling of Zinc vapours or air inlet. Please share the possibilities.
2) We are trying to manufacture Zinc Oxide Active with surface area above 35 cm3/gm. I understand from the thread that by reacting Zinc chloride & sodium carbonate, we can manufacture Zinc Carbonate. After that calcination to be done. Can you please share more info regarding calcinator, temperature, wet cake or dry ZnCo3 to be used, what should be ZnCO3, Zn% and process.
3) Also, we want to convert Zinc Oxide white powder of french process to pellets. How can we do so without binder chemical.
4) We are using Zinc remelted ingots of Zinc 95%, 3-4% aluminium, 0.3 copper, 0.1%, problem is after the zinc vaporization we get al alloy material at the bottom, due to which our crucibles are getting broken at only 30 tons life. Please suggest any solutions
5) Our FO consumption is 200-225 L per ton. How can we save our fuel costs.
I am thankful to you for keeping our spirits on in this unprecedented time and I hope all of you are safe from this pandemic.
Warm Regards
- Gurgaon, haryana, India
A. hi Tanishq
1 Check what are the impurities. Normally purity from bottom dross should not be a problem.
2 Active and High Surface Area Zinc Oxide are not the same and 5hey are prepared differently.
3. Without removing Aluminium, there could be issues on crucible life. It would be interesting to note the composition if bottom residue.
Oil consumption can be easily brought down below 150. Check the combustion.
Sorry I forgot to mention, pellets are made without adding any binder whatsoever.
Self Employed - Vadodara. Gujarat, India
April 29, 2020
July 18, 2020
A. Dear Mr. Tanishq,
I am trying to reply your queries as follows,
First of all try to understand that quality and yield (output) is depend upon processing / methods.
1) French process is distillation of zinc metal and so it produces highly pure zinc oxide at least 99.3%, anything below is contamination from dirty operations on furnace. The impurities in dross are not able to reduce purity of zinc oxide as they are high boiling impurities (Fe, Pb and Al). in normal course of using dross @ 92% you will able to produce @ 99.3 purity. If you are using 96% dross then regularly it gives @ 99.5 % minimum purity.
2) French process is only capable to produce surface area from 2 to 10 sq. meter/gram. If you want to produce higher surface area then you have to opt other wet processes, which are capable to manufacture high surface area. Zinc chloride and sodium carbonate process gives problem of NaCl salt, so it is not preferable.
3) Zinc oxide pallets without binder is manufactured by compression of zinc oxide powder. The pressure used is above 250Kg/cm2 minimum. These kind granulation machines are available in international market. In India we don't do the palletization / granulation as there is no value addition as customer is not ready to pay extra.
4) It seems the crucible life at your facility is due to other reason than the zinc input quality. Only iron impurity in zinc dross / ingots damages crucibles, due to heavy depositions. Your remelted zinc has high aluminum and it easily come out of crucible in molten form.
5) FO consumption reduction can be reduce by 5 - 10% by improvement in process and some small changes in firing system. But if you want to match FO consumption to 150 ltrs/MT then you need to replace furnaces by automated and improved designed furnaces.
I hope most of your queries are answered.
Regards,
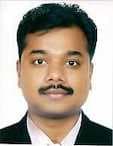
Umesh Charki
- Thane, India
Q. Hi,
We are would like to set up a zinc oxide manufacturing plant using metallic zinc in Rajasthan. We are new to the field and would like to first understand the financial and practical aspects of it.
- Bikaner, Rajasthan, India
April 18, 2020
? Hi Mahima, can you be more specific? Giving an entire project report will be out of place here.
ABHAY NAGLESelf Employed - Surrey, BC CANADA
April 22, 2020
"I took a course in speed reading and was able to read 'War and Peace' in 20 minutes. It's about Russia." -- Woody Allen
A. I have found people confusing high surface area Zinc Oxide with Active. While HSA ZnO is a porous particle, active ZnO is a Nano particle. The methods of manufacture are different too.
ABHAY NAGLESelf Employed - Surrey, BC CANADA
May 15, 2020
Q. Hello everyone, I am a new investor in this area and I lack information and experience. I want to ask questions about the material used for the crucible cover, the diameter of the refrigerated channels, and their length, noting that I have two furnaces with two crucibles, i.e. 4 crucibles with a total capacity of 140 liters each. I stop checking the density knowing that the capacity of the big bag 1000 can only support 300 kg, and why
Abdelbasset Arab- Boumerdes, Algeria
September 29, 2020
![]() |
A. Dear Mr. Abdelbasset Arab, ![]() Umesh Charki - Thane, India October 14, 2020 A. That is a very good question Mr. Arab. I will reply in detail Abhay Nagle- VADODARA Gujarat India October 14, 2020 |
![]() |
A. Hi Mr. Arab, you must know metallic impurities and metallic Zinc. Lead Cadmium Iron and Aluminium are the commonly encountered impurities. - VADODARA Gujarat India October 14, 2020 October 16, 2020 A. Dear Mr. Abdelbasset Arab, - Vadodara, Gujarat, India |
A. Hi Mr. Arab, I think Umesh has given a very detailed analytical reply to your query. He is right, you need to remove occluded air to improve the bulk density. You may use a ribbon blender to increase it to 0.7 - 0.8 gm/cc or you may use a pelletizer to increase to 1.2.
Abhay Nagle- VADODARA Gujarat India
October 19, 2020
Q. Welcome everybody. Thank you very much for your valuable answers, which helped me a lot in improving the product quality. However, I am still facing some problems cleaning the crucibles. I do not know whether it is because of the quality of the raw material or is there another reason that I do not know. Thanks for your interest.
Abdelbasset Arab [returning]- Boumerdes, Algeria
October 20, 2020
A. Hi Mr. Arab, when there is a lot of Fe in the raw material, there more chances of encountering problems with crucible cleaning. Combination of Fe and Al helps in avoiding this problem. Addition of external Fe or Al as required to form Fe Al complex and remove it but any removal of this complex may sacrifice yield so you have to look for a trade off.
I have heard about use of silica (being an acidic flux) at about 800 degrees C to help easing out cleaning. But do not have hands on experience. So I cannot recommend it.
- VADODARA Gujarat India
October 22, 2020
? Why is the group dry?
ABHAY NAGLE- VADODARA Gujarat India
November 17, 2020
Q. Good morning all. Thank you all for answering all the questions. I want to consult with you on the issue of crucibles breaking during the cleaning process, and for this I will use a new type of cast iron crucibles. Please what are the disadvantages of this type, is it valid for the zinc oxide manufacturing process and what do you recommend as solutions. thank you very much
abdelbasset Arab- Boumerdes, Algeria
December 7, 2020
A. You cannot use cast iron crucibles for zinc oxide manufacture.
ABHAY NAGLE- VADODARA Gujarat India
June 5, 2021
Q. Good morning all. I am very impressed with the valuable information I found on this forum and the level that Zinc Oxide producers have reached in India. But the problem that most zinc oxide producers still suffer from in the French process is the unwanted deposits that remain inside the crucible, as new producers in this area find it very difficult to clean the crucibles.
I ask those responsible for this forum and those who have more experience in dealing with this problem to provide us with information on the materials used to facilitate the cleaning process or any method that allows us to facilitate the cleaning process. Please reply as soon as possible.
Thank you so much Ted Mooney.
Bilal Dali- Algiers, Algeria
December 24, 2020
----
Ed. note: Thanks for the kind words, Bilal. I (Ted) provide the space and mechanism for posting, but I have no knowledge of the French Process. Umesh Charki and Aghay Nagle have provided nearly all the answers on this thread :-)
Q. Hello everyone.!
Very glad to see so many zinc oxide experts here together!
I work for a zinc oxide manufacturing company. I have a problem regarding the crucible lifespan and looking for a solution to it.
We use silicon carbide crucibles BUC400 for vapourising Pure zinc ingots to get ZnO of high purity. The issue is that the crucible sometimes...say around 20-30 tons of use, gets cracked by itself after charging the ingots. The crack is a thin hairline type and the metal then leaks from the crucible. Can anyone please help me know the reason for this and what would be the solution.
We use furnace oil and the furnace temp. is around 850 °C
Thanks & regards
- Kolkata, West Bengal
May 4, 2021
Q, A, or Comment on THIS thread -or- Start a NEW Thread