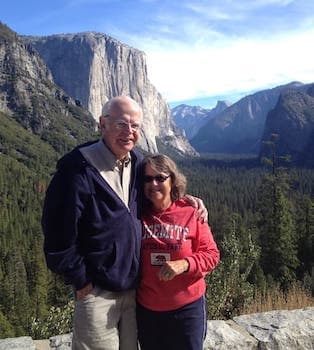
Curated with aloha by
Ted Mooney, P.E. RET
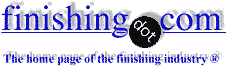
The authoritative public forum
for Metal Finishing 1989-2025
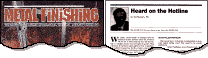
-----
Zinc oxide production by French process?
2006
Dear All,
Discussion on French process is very fruitful and interesting for getting such valuable knowledge from all of you,
my question is that what is the best combination of input material in oil fired furnace normally top drosses are available available in domestic market it containing Alumina /Zinc alloys due to this only top dross charging is very difficult to use in the oil fired furnace what is the best combination of raw material to be use for getting desired yield and reduce furnace oil consumption please participate.
chemist - India
Hi Mr Patil,
Dross contains several percentages of iron and aluminium that have higher melting and boiling points. Iron and aluminium vaporise at 2862 and 2520 °C, respectively; while zinc at 907 °C. The final Zn-Fe and Zn-Al eutectics may have boiling points exceeding 1000 °C, which may justify higher furnace oil consumption. Moreover the oxidised product may contain iron oxide and aluminium oxide that may produce yellowish/brownish tones to zinc oxide. You may use coke as a fluxing agent to lower the boiling point, and in doing so, you will be merging the French process with American process. Due to appreciable levels of impurities in this French-American zinc oxide, potential applications would be lower end ones.
Regarding fuel supply for crucibles, I suggest that you use electric heating in the form of SiC globars that are heavily used in many furnaces that I used to work with, whereby the process efficiency can double. There is no heat loss via exhaust duct since there is no exhaust. Most of the heat produced by the globars is transferred to the zinc ingots. You may need 8 SiC globars for each furnace at a price USD 300 per globar (I think) excluding the control panel, and the globars can last for 10-12 months.
I hope you will find my suggestion fruitful.
Best wishes.
- Penang, Malaysia
2006
Dear all,
I am a Spanish Chemist, and I am interested in putting up a zinc oxide plant. It is a new project for my company. We would use zinc dross, including zinc powder. Any advise about the implementation would be highly appreciated.
Best regards,
ZINC PLANT - Vigo, Pontevedra, SPAIN
2006
Dear Mr. Shahrom Mahmud,
We highly appreciate you for attempting,
We are using Oil fired furnace that place couple of silicon carbide crucibles its heat up through burner- Furnace Oil as a fuel.
Please suggest us for use of fluxing agent (as coke) at what temperature along with its conditions.
Regards,
D.T.PATIL
- DAMAN
2006
dear sir,
we are manufacturers of Zinc Oxide by using French method,
use Zinc Dross of 94-95% pure.Now a days as Zinc Dross /metal price go big higher we are looking for cheap replacement as in our another unit of Ceramic raw material we are consumer of Zinc Oxide.
is it possible to produce Zinc oxide from Zinc Hydroxide ?
we have some source of Zinc hydroxide which is byproduct for them so it is cheap also.
please explain.
- Morbi, Gujarat, India
2006
Dear Mr.Kantilal Patel,
Ceramic manufacturer are using french process zinc oxide because this zinc oxide is amorphous white in colour.Oxidation process from hydroxide rout Zinc Oxide colour becomes yellowish and after calcination pulverisation is also require. Yellow zinc oxide is suitable for Tyre and rubber compounding but it is also depending upon process control parameters ,Surface Area, Purity and other impurity level ,I think French process is better option for Ceramic application.
D.T.Patil.Daman
- Daman
2006
A. Zinc hydroxide has great surface area than zinc oxide french process. and hydroxide is also directly used in ceramic frit product.
Hardik Vamjachemist - Morbi
February 9, 2022
Re calcination of yellow zinc oxide -
before I started work on ZnO (and that's some time ago)the company where I worked used a small addition of sulfur
⇦ this on
eBay
or
Amazon [affil links]
to reduce the grittiness caused by calcination. The process had already ceased when I joined the company so I have no actual experience of this possibility.
- Fergus, Ontario, Canada
2006
2006
Greetings fellow ZnO enthusiasts, With respect to calcination of yellow ZnO, a possible route to reduce grit levels may be to add around 0.5% of sulfur powder to the ZnO before calcination. This practice was used decades ago with French process ZnO to make product suitable for paint coatings. I have no first hand experience of this but understand it was a commercial process that operated for several years. (Apologies - my earlier submission slipped away before I had chance to add to it)
I have seen electron micrographs of calcined yellow
(hydrosulfite process) ZnO. Rather than calcination
(coalescing of individual particles), the mechanism appears to be re-formation of the ZnO with a different crystalline structure. Although the material was white it had an unacceptable level of grit for most applications,
For readers with a keen interest in the early development of the Zinc Industry, I found an interesting paper describing archeological work carried out in India-
http://metalrg.iisc.ernet.in/~wootz/heritage/zn.html
Many thanks
- Fergus, Ontario, Canada
2006
DEAR SIR,
I will appreciate if you could help us about this problem.
we have a ZnSiO4 mine to produce ZnO out of this soil we have built a site with wales furnace.
we are planning to produce ZnO with 60% purity.
would you give us the information of a suitable method for extracting ZnO from ZnSiO4 soil and whether is our method (wales furnace) alright or not?
thanks.
best regards,
- IRAN
Re zinc silicate orebody & extraction process
Most modern mode of operation for a zinc silicate concentrate is to use solvent extraction techniques as used at the Skorpion, Namibia zinc mine, for example. The decision to use this technology rather than a Waelz kiln will depend on other factors such as the other metals of value that may be present and also the scale of the operation.
- Fergus, Ontario, Canada
2006
Dear friends,
We are using zinc metal for manufacturing of zinc oxide with lead, <20 ppm as required by the Indian Pharmacopoeia. However due to steep rise in price of zinc metal we are unable to be viable. As such material is available at prices slightly higher than that made from dross, means that dross can be used for making pharma grade lead-free material.
Could you help me with the process parameters for producing this kind of material from dross? Any kind of guidelines would be greatly appreciated.
Sometimes we do get this material from dross but that is a very rare chance.
Regards -
zinc oxide manufacturing - Kanpur, UP, India
2007
Q. We are a dental material/cosmetics manufacturer and we consume zinc oxide pharmaceutical a lot. Due to price increase of this material the cost of our production has gone up and we are not competitive anymore.
We have zinc metal available in Iran and also fuel as well as low wage labour cost in Iran leads us to contemplate to produce this material in our plant.
We will appreciate a lot receiving proposals/guidance/suggestion enabling us to decide.
- TEHRAN, IRAN
2007
Q. Production of 95% ZnO
Dear all friends
I am already producing ZnO (99.97%) from French Process. I need to develop a process for ZnO (95%)-Low purity.
Can you suggest me?
chemicals - Lahore, Pakistan
2007
A. I work for an international company that manufactures ZnO as well as many other products.
We routinely recover 122% ZnO from HG and 110% from galvanizing top dross. These conversions are achieved whether using a 2 MT per day furnace or a 30 MT per day furnace.
At one time our organization thought 120% was adequate, but we have learned to achieve better results.
These results were not achieved overnight, but through years of improvements.
- Pittsburgh, Pennsylvania
2007
Q. Dear Sir,
We are interested in putting up zinc oxide plant using zinc hydroxide (a byproduct of sodium formaldehyde sulfoxylate) as raw material. Any assistance shall be highly appreciated.
Thanks,
- Baroda, Gujarat, India
2007
Q. Hi, Friends:
I meet a problem in manufacturing the high purity (>95%) of zinc oxide and looking for help:
The problem is zinc oxide always containing 2~3% of lead oxide which we hope to reduce to <1%. Our manufacture is dry process. Right now our only solution is control the ore quality, but it is very difficulty and costing.
Any idea, Please help !
We also looking for expert who have interesting to open the business in manufacture Aluminium Oxide in China.
Chemist - Rockville, Maryland
2007
Hello,
we have been manufacturing zinc oxide (lead free grade, electroplating grade,silver seal,white seal, 99.5%- 99.9%) for the last 15 years and with the hard work of all our employees and well wishers have been able to live up to the expectations of our valued customers in delivering a quality product.
Now we want to start manufacturing active zinc oxide through wet process. we are totally new in this field and any kind of help in this regard ( process of manufacturing, raw materials and substitutions, applications, discharge of effluents and wastes, recycling of wastes etc)would be duly appreciated. people who are already into this should please forward their experiences so that we can also learn from their valuable ideas and experiences.
please share your ideas.
Thanking You,
CEO - RAJPURA , Punjab, INDIA
2007
2007
REALLY NICE TO FIND SUCH A ONLINE GROUP.ANYWAY PLEASE ALL READER ARE REQUESTED TO PROVIDE US WITH YOUR SUGGESTIONS.
WE ARE MINING ZINC WHERE WE OBTAIN THEM IN THE FORM OF LUMPS WHERE WE WASH,PULVERIZE,DRY AND PACK THEM.IT IS WHITE COLOUR POWDER ZINC OXIDE WITH ZnO - 80% AND ZINC Zn ALONG 65+ ALONG WITH THIS WE ALSO FIND LEAD Pb - 3 PPM, MAGNESIUM Mg-7%,CALCIUM Ca - 4%.WE UNDERSTAND AND AWARE ITS REALLY A RARE FORM OF DEPOSITS.
ANYWAY I WISH TO KNOW FOR WHAT ALL PURPOSE THIS MATERIALS CAN BE USED?
CAN ZINC METAL BE EXTRACTED BY USING THIS AS RAW MATERIALS. CAN THIS BE CONSUMED OR USED BY CHEMICAL INDUSTRIES TO PRODUCE HIGH GRADE ZINC OXIDE.
IS IT POSSIBLE FOR US TO PRODUCE HIGH GRADE THAT IS 99.5%+ ZnO - IF SO UNDER WHAT METHOD WE HAVE TO MAKE A PLANT.ALSO PLEASE PROVIDE ME YOUR VALUABLE SUGGESTIONS.
THANKING YOU,
REGARDS,
DIRECTOR - INDIA
2007
Dear all,
we are leading manufacturer of Zinc Oxide in India by French process. we are using raw material zinc dross containing impurities like Pb, Fe, & Al We are facing problem for raw material containing higher
% of iron (Fe) i.e. up to 4-5% when we charge such material in a crucible, saturation of Iron takes place at bottom of crucible after
2-3 duty crucibles volume get decrease. I want to know is there any specific flux available for removing iron content from crucible.if it is please let me know. your information is highly appreciated.
Q. A. Manager - Jammu, India
Dear MARIA ABELEDO,
As you are new in this zinc oxide mfg. field you have to take care for lot of things like raw material quality,Suppose If you are using raw material containing higher impurities like Lead & iron it will affect your product as well as increase the f. o. consumption . Most of impurities will get settled at the bottom of crucible which increase the thickness of crucible & due to increasing thickness consumption of F.O. consumption will increase.Secondly process parameter is most important you should have control on your process parameter like evaporation period, Blower RPM, collection of Zinc Oxide at diff tank etc. Thanks
Q. A. Manager - Jammu, India
2007
Please can anyone tell me what is exactly the French process of making zinc oxide of 99.99% purity with zinc dross.Where can I get the plant and machinery from.And what will be the cost for 10 MT/day plant.
Thanks
buyer - Ludhiana, Punjab, India
2007
2007
Dear Ravi Rajput,
This is the problem of all zinc oxide manufacturer but nobody can search this type of flux.you have two way to avoid the problem, first you take furnace cleaning after 3 days, second you blend the material like top and bottom dross and lower impurity with higher impurity material.
then you feel 80% realisation.
R.R.Yadav
zinc oxide - India
2007
Dear Mr Shaurya Mittal
Zinc oxide was discovered by Cramer in 1750 while the French process was popularized by LeClaire in 1844 during when he mass-produced ZnO for white oil paint. Pure zinc metal was used then. The use of cheaper zinc dross has been popular lately due to the zinc high price LME of USD 3440 per MT. However the French process is not designed for recycled raw materials since there is no convenient way to leak out the accumulated dross impurities during operation, i.e., there is no leaking valve on the crucible. If there exist a crucible with a leaking valve, it would have lower working life due to intricate design. Dr Robinson and I suggest that the best practical way is to purify the dross to a purity of above 99.9% zinc before charging into the French process furnace, meaning a purification plant is required.
Best wishes,
- Penang, Malaysia
2007
Dear Mr. Shahrom Mahmud,
For producing zinc oxide 99.9% pure from dross, can we go by using self-refluxing column for fractionation of incoming vapours. As new jersey process is used for zinc fractionation with external refluxing of liquid zinc and the purified zinc vapours are condensed to get pure zinc above 99.9% purity. The same process can be used for purification of zinc vapours and subsequent oxidation will give us pure zinc oxide. This oxidation will happen far above floor level so contamination of atmospheric dust (foreign particles)will reduce. Instead of purifying zinc dross to zinc metal, this process will help for lower cost manufacturing as energy is major part of manufacturing cost.
Please revert with your valuable inputs upon this issue,
Thanking you,
Umesh
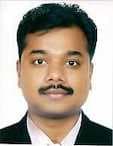
Umesh Charki
- Thane, India
2007
Dear Mr Umesh Charki,
I agree with you that the best way to purify zinc dross is by vapourising it. If you can build a furnace that can vaporize dross into vapours, you can oxidize it to make ZnO and you can obtain a good purity if you oxidize the vapour far above the ground level, as you said earlier; however, the particle size and morphology will be different than that obtained from French process. The French process is based on high velocity zinc vapour at speed of Mach 0.1 followed by rapid air-quenching. ZnO size and morphology are highly sensitive to temperature and Zn/O ratios. You may have to spend money and time to experiment on several furnace designs in order to simulate the French process. Perhaps you need professional help to expedite results.
Good luck.
- Penang, Malaysia
2007
Dear Mr. Shahrom Mahmud,
Sir, I have tried this process in 500 Kg/ day furnace for experiment trials. We got 5.5 square meter per gm with 99.86% zinc oxide. 65% of total production by the setup was of this grade. lead was 16 ppm. Dross used for this trial was 94.5% zinc with lead 0.4%, which is normal grade of dross available.
Sir, I was working as COO with one of the leading zinc oxide manufacturer in India. I have installed 24 zinc oxide furnaces in last 5 years and 6 for zinc metal recovery. I have tried zinc metal distillation, zinc dross to zinc metal for experiment which gives 93% recovery of 99.3% pure metal from dross. All these experiments are carried on 500 Kg/ day capacity furnace. Scale up of these trials on
4 MT/Day furnace is easily possible as equipment sizing is already completed.
I am also interested in nano zinc oxide by hydrothermal discharging-gas method and second is flame spray pyrolysis.
As nano zinc oxide is in increasing demand for various applications.
Anyone who are working on the same please share.
Thanking you,
Umesh
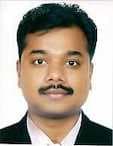
Umesh Charki
- Thane, India
2007
Hello Umesh,
You have done great engineering innovation by building your own distillation furnaces for zinc recovery from dross. To my knowledge, flame pyrolysis has not been commercialized yet. There is one professor from ETH Zurich, Prof Pratsinis Sotiris, who has been doing flame synthesis on ZnO for many years. You may contact him for advice from this link http://www.ptl.ethz.ch/people/director/pratsinis . He has synthesized nano particles of ZnO at a lab scale.
Good job!
- Penang, Malaysia
2007
Dear sir,
we are manufacturer of Zinc Oxide by French process for last 20 years.
We are facing problem with Zinc Dross having aluminium content more then 2%.
When ever we have to use this kind of dross it doesn't melt in the furnace,and starts evaporating instantly,and we are not able to clean the Dross of impurities.the result is that the ZnO formed is blackish in colour.
Can anybody suggest any chemical,which can be mixed with dross ,while charging it in to crucibles,so that the Dross gets cleaned,and the resulting Zinc Oxide is white in colour free of impurities.
Hope to receive an answer,and early date.
thanks,
CEO - RAJASTHAN, INDIA
Mr. Ankur Agrawal,
I have experience in processing dross up to 4.5% aluminum. In the same process we can't skim liquid metal. So we can go with aluminum in the liquid metal. Try to skim liquid metal with ammonium chloride and Keep @8 inches space below crucible cover. Take care of splashing liquid metal. If you will not skim non-metallic impurities with ammonium chloride it blocks the hole for vapors in cover, and the crucible cover can throw away by zinc vapors. Because of this liquid metal got flashed and can cause hazards in the plant.
For high aluminum containing dross better to go for high capacity crucibles furnace.
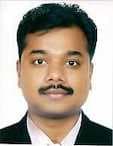
Umesh Charki
- Thane, India
2007
2007
Dear Readers:
(1)I came across the thread very recently and amazed that people have taken lots of interest. I shall be pleased to know how many persons have been benefited with this discussion.
(2)I am with Zinc Oxide industry for last more than 30 years serving all area of working of the industry. During course of my marketing I faced lots of problems faced by the consumers and I had to interact with our Technical people for the proper quality products.I have been able to pursue and solve the problems faced by the manufacturers of Zinc Oxide who are investing huge amount of money.
(3)I have understood that main impurities like Iron, Lead, Alu. etc are contained in Zinc Dross are most in form of compounds (oxide, sulphate, carbonate etc) depending on the process adopted by the Galvanisers (there are several different processes) that is why the material purchased by the ZnO Mfgrs are not found uniform and they face end product problems. It is understood that at about 800 deg. C. Temp. most of the Iron, Lead etc compounds are decomposed to metallic particles and if it is allowed to stand for few hours after stirring at the same temp. metallic particles will settle down leaving zinc to be free from these impurities. Use of Fluxes will add some other impurities such as chloride etc which are not desirable in certain grades of ZnO.
(4)For economy of the fuel, I shall seek advise from my friends, while only surface area of Zinc in the crucible is reacted to form zinc vapour, what is the necessity to keep the whole 500 to 700 Kgs of Zinc in one crucible boiling for hours consuming valuable fuel?
I think instead of more depth more wide with less depth crucible should be used and continuous molten zinc should be fed. Such device could be done. I feel since standard sizes of crucibles are available
(which are used for melting of iron and other metals and alloy and are more in demand they are being produced) other suitable for zinc oxide is not desired/demanded by the ZnO mfgrs.
(5)I can say that ratio of Zinc HG should be Min. 100:123 and for Zinc Dross (from Steel Plant continuous process) it could be 100:115. This result is regularly achieved.
(6)For Furnace Oil consumption, Burner with auto-control with proper insulation with latest refractories materials, etc will improve on fuel consumption.
(7)I had tried wet process for making Zinc Oxide from Zinc Ash, but due to pollution problems could not proceed but achieved the quality.
designer, consultant - Kolkata, West Bengal, India
2007
We are producing zinc oxide by French process. I have come through some material that is used to clean residue of iron from bottom, which is a major headache.
unfortunately I do not know the name of the material but it is like crystals of sugar and bluish in colour. it gives us good results in cleaning bottom iron. can any one throw some light on it?
2. when we use dross with aluminium it is difficult for us to clean ash and other impurities from top and we get inferior quality zinc oxide in off white colour. can any one solve the problem?
director - Morbi, India
Dear Ranashayer,
Lot of thanks for your suggestion. Already we are doing same exercise. Thanks,
Q. A. Manager - Jammu, India
2007
Dear Mr. Shah, Kolkata
we are at present producing zinc oxide white seal from Dross.
we mainly supply to ceramic industry. when we use dross with Al we find zinc oxide which is not as white compare to bottom dross of structure galvanising. but in terms of % both are more than 99.5%. can you solve our problem?
we are also interested in producing oxide from ash.
can you help me in this way?
industrialist - Morbi, Gujarat, India
2007
HI,
EVERYBODY,
CAN ANYONE TELL ME WHAT IS ZINC OXIDE FEED GRADE, AND MOST IMPORTANTLY HOW CAN IT BE PRODUCED AT JUST HALF THE PRICE OF WHITE SEAL ZnO.
WHAT IS THE METHOD ADOPTED TO KEEP THE HEAVY METALS LOW.
HOPE TO RECEIVE EXPERT ADVICE AT AN EARLY DATE.
THANKS
- INDIA
2007
Pls. clarify how to calculate the capacity of the zinc oxide plant keeping in view the size of the crucible,Two No. of crucibles/furnace and output of zinc oxide /hour viz a viz weight gain and type of raw materials employed by zinc oxide industry.
RAHUL
STUDENT - JAMMU, India
2007
2007
Dear Rahul Sharma,
I am answering your queries step by step,
1) Capacity of ZnO furnace- two crucibles per furnace is most suitable combination of ZnO furnace. And Not only crucible size but burner capacity also have very important role in capacity calculation of ZnO furnace. Vapourising rate of zinc metal is important factor in productivity of ZnO furnace. Holding is defined by crucible size but it does not affect zn vapourisation rate.
2) Output of zinc oxide furnace is not easy to determine by per hour basis. as vapourisation rate does not remain fix over time because this is not continuous process but batch process. Crucible cleaning also interrupt production. ZnO furnace capacity is defined by vapourisation rate per day after deducting downtime like charging time, heating time etc.
3) Weight gain is weight of oxygen added to zinc while formation of zinc oxide. It is theoretically 24% weight gain. But in actual there is 22% of weight gain, When we minimize by products generation, and loses in the processing. Weight gain for dross and other scrap is defined by, {wt of zinc oxide =%metallic zinc content * 1.2}
4)Raw materials:- French process is concern only to metallic zinc content in raw material and raw material is deciding factor for quality of zinc oxide formed. So in ZnO industry we use raw material with more metallic zinc content above 88% metallic zinc.
Galvanisers dross is major source of RM. zinc roofings, scrap, turnings, scores, wires,blowings,etc.
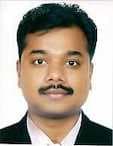
Umesh Charki
- Thane, India
Respected sir,
Mr. Charki,
I am very impressed to your all answers in finishing.com. Sir I know you are a expert in about zinc oxide plant.
I am working in zinc oxide plant As a officer production from last three years,Now I understand all the process parameters in the plant but I want to know from you about French process from beginning to End. I want to know process in between zinc Dross to Zinc Oxide.
sir, I hope you will give me reply.
employee - India
2007
2007
Mr. Ramashare,
Zinc Dross to Zinc oxide is very simple gas phase reaction between zinc vapours and oxygen. Metallic zinc from zinc dross vapourises and due to high temp ( 950 degree C) it starts spontaneous oxidizing with atmospheric oxygen. This is as simple to burning of carbon in air, as it gives CO2. Zinc combustion gives zinc oxide.
This reaction happens in fraction of seconds, and after zinc oxide formation we can not purify it. So it is very important to set parameters proactively to form desirably pure form. Controlling factors for this process are flow rates of zinc vapours and air, which gives different partial pressures of reactants; as well while and after formation temp. control gives desired physical form means particle size distribution for ZnO. And dispersion of zinc vapours in air while oxidizing is important for complete combustion of zinc, as zinc oxide forms impermeable and hard coating over unreacted zinc particle surface.which gives free metallic zinc in zinc oxide.
I hope you have cleared most of your queries,
I request to you all fellow ZnO enthusiasts to be environmentally careful while manufacturing zinc oxide. It is very much important as French process is energy intensive process and Major problem in this industry is air pollution.
Thanking you,
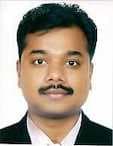
Umesh Charki
- Thane, India
2007
Dear all,
I am an engineer from a non-ferrous metal powder company. In French process how zinc vapour is collected from furnace and react with air
(O2).what are the precautions to made avoid explosion?after the reaction completed how you cool and collect the ZnO powder?
Thanks
Engineer - Madurai,Tamil Nadu, India
Dear muthupandi,
Good inquiry but its very difficult to explain so that you must be visit any ZnO plant for your query.
- India
2007
Dear Ramashare yadav,
thanks for your kind reply.
Engineer - Madurai
2007
2007
Dear Muthupandi,
I think you have gone through the total forum.I am explaining you the process,
1)In French process, crucibles are used to boil zinc metal, Crucibles keep covered by refractory tile with 2-3 inches hole for vapour outlet. When zinc metal starts boiling, vapours come out with velocity of 0.1 mach ( 30 m/s) and enters in hood above the furnace. continues air flow maintained in hood with help of blower, this air used for oxidation; carrying away zinc oxide to collection system and sudden cooling of zinc oxide.
2)As explosive limit of zinc dust
⇦ this on
eBay or
Amazon [affil links]
in one cubic meter air at 600 °C. but in this process zinc vapours starts burning spontaneously as they comes out of crucibles and contacted with air. This process is exothermic so temp. of flame suddenly increases to 1500 °C. When it comes in contact with air flow at 30 °C formed zinc oxide quenched to below 450 °C. This quenching define zinc oxide particle properties. how fine it should be?
3)This formed zinc oxide at 400-450 °C carried through long duct, where it gets cooled further by natural convection. It passed through settlers to separate heavy particles. after cooling below 100 °C air filtered to separate zinc oxide.
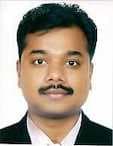
Umesh Charki
- Thane, India
2007
Dear all,
I have learn a lot from your discussions. I am an Engineer for refractory-Crucible and have one customer to manufacture zinc oxide. This customer use 2 kinds of different crucible furnaces for French process, one is for high pure zinc ingot and one is for zinc dross, both try to use the fuel efficient. For the high purity zinc ingot, the crucible can be used for over 3 months. For zinc dross, the average lifetime for crucible is about 40 days; There are much dross left in this crucible, the dross will be powdered after a few days when they shut down the furnace. Analysis shows that there are much Fe/Al/Pb/Sb in the dross, I think these comes from galvaniser and these impurities result in the short life of crucible. does anyone find this problem before? how is the crucible lifetime in your plant?
I have searched the internet, all the zinc oxide plant I found use a similar furnace as shown in Dr. Shahrom Mahmud's paper. What I have seen in my customer is totally different, I believe my customer's experience can use the fuel more efficient.
- Suzhou, China
I making zinc oxide with French process since two years .I want to know how I can make active zinc oxide
Anurag Jain- Ganga Nagar, Rajesthan, India
2007
Dear all,
We are one of the Zinc Oxide production in Thailand using French process. As we know, the Fuel oil price is very high now. Could anybody suggest us for replacing FO to Natural gas?
Also, we have problem with contamination from FO combustion (carbon from FO flame) in our Zinc Oxide product. We think Natural gas will help us for this problem.
Last question, we set the target for fuel oil per Mt ZnO at 200. Would it be correct for 200 Lit/mt ZnO?
Best Regards,
Production manager - Bkk, Thailand
January 3, 2008
February 23, 2008
Zinc Oxide Yield using PWG Grade Zinc
Dear Readers,
I am running 4 furnaces and using both SHG and PWG grade zinc.
I am mixing PWG grade zinc in a 10-15% but have a notices a drop in pure oxide
yield from 1.20% down to 1.17% . I was expecting a drop in yield of
1% only.
Can anybody help & explain on how to control this Yield ?
thank you,
- Bangkok -Thailand
March 4, 2008
Dear Mr. Vinay Dhawan,
PWG zinc( prime western) contains up to 1.5% lead. Which does not converted in oxide. only zinc is converted in Oxide with additional oxygen weight. Reduction of yield could be because of loss of zinc in bottom of crucible with lead, increase of by-product like ZnO pipe on vapour opening. There are many reasons for reduction of yield.
Also mixing of PWG zinc gives increased lead content in zinc oxide. As lead comes with zinc vapours at 0.005 times percentage of lead in liquid metal in crucible.
Regards,
Umesh
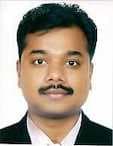
Umesh Charki
- Thane, India
May 24, 2008
Dear All,
I am in this field for last 7 years. I have installed 24 ZnO furnaces till date. Now While thinking over rising oil prices. I think electrical furnace will be better option. Oil 150 ltrs/ MT is std. consumption which we are getting. but for 1 MT ZnO production electrical furnace consumes 450 KWH power. which is most cheap in some part of world. This furnace is producing 3 MT/ day ZnO. This furnace cost is also same compare to oil fired furnace(with combustion control system).
I think this will be most profitable furnace in these days for rising oil prices.
Any input regarding this are most welcome.
Umesh Charki
- Thane, India
Q, A, or Comment on THIS thread -or- Start a NEW Thread