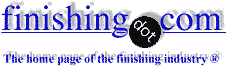
-----
Powder coating gray iron castings
Powder coating castings(gray iron to ASTM A48 [affil. link] class 25 specs has created a problem with gasouts or fisheyes that are unacceptable for a finished product. We presently pre-cure the castings @400 deg F for 2-3 hours, powder coat, and cure for 1/2 hour @400 after coating. Even though we have filled all visual voids and blemishes, there are craters, or gasouts that appear after curing. Would like to know if anyone else has had the experience.
Ronald A. Mongeon- Middleboro, Massachusetts
You can use an additive for non-gassing. In Germany the comp. BYK-CHEMIE GmbH delivered those products. You can use Ceraflour 962. This product can you mixed through our powder.
Good luck,
Jan Rijn- Goes, HOLLAND
Castings just seem to be a continual problem. I think you are on the right track considering all you've tried so far. I too would ask the powder vendor to either reformulate the powder or add an additive to combat craters. You may also want to try flocking the powder onto the part. Flocking is when powder is applied to a hot part. The drawback is the application is not evenly distributed onto the substrate and you will use more powder. You just have less control and you are really just dumping the powder onto the substrate. I personally have found that this is the only way I have managed to get rid of craters "on some" substrates due to porosity. The heated substrate seems to draw the powder into the surface.
![]() Bob Utech Benson, Minnesota |
![]() Ed. note: Bob is the author of: "High Performance powder Coating" on eBay or AbeBooks or Amazon [affil links] |
You are on the right track wit the pre-curing if the craters are a result of out-gassing. The casting probably contains some trapped moisture and air which expands as it is heated which is then "popping" through the powder coating before it finishes gelling. A casting grade additive will slow the gel time and allow more gas to escape. Another idea is maybe not pre-cure or de gass for so long but at a higher temp. The gases will be forced out faster and when you cure the final coat (at the lower temp) you should have little gassing or popping. Try it , it won't cost you anything.
Michael Lind- Queensland, Australia
Q, A, or Comment on THIS thread -or- Start a NEW Thread