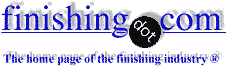
-----
Conversion coating influence of split waveguide?
Does anyone know if microwave waveguide used diecasting on Aluminum or Zinc. At present we split a waveguide into two equal pieces. With that we insert one septrum which is very thin into the middle of the splitted waveguide such that we can combine them together. Can you tell me what influence the conversion coating takes on the electric properties of such waveguide?(such as contact resistance...) That is to say, I want to know the effect of metal contact in such condition. Thank a lot.
Petter Chen- Hsinchu, Taiwan
Our experience with aluminum waveguide parts that have been treated with an Alodine finish is as follows: There seems to be no significant loss at 100 GHz if your waveguide length is short (of order 1"). Of course, our components at that frequency are very small. I would expect that at lower frequencies, the loss would be even less of a problem although your waveguide would be correspondingly larger. I would recommend making a (relatively long) test piece of waveguide with and without Alodine finish and measuring the loss. You will probably find that the insertion loss is not significant in your application. (I would love to know the results!)
Alodine finished parts seem to have reasonably good electrical conductivity. That is; when Alodined aluminum waveguide halves are joined, there are no significant losses. This is usually dominated by the flatness of the pieces and the number of fasteners you have used to ensure good contact. Hope that I was of some help!
Ronna EricksonRadio Astronomy - Amherst, Massachusetts
Who had experience and can be talk to me, what the effect of waveguide insertion loss with coating and non-coating silver. Other component such as transitions, filter, bends,...ect. if it test in hight frequency(20-30G) and base material is aluminum.
Thanks!
Petter Chen- Taiwan
For use at 20 to 30 GHz, why bother coating the aluminum with anything? Aluminum is lighter, less expensive and easier to machine than copper. The performance of aluminum is not significantly different from other metals in most RF applications. If you use 6061 Al, you would be hard pressed to notice any difference from waveguide components made of copper unless you have a particularly stringent application. If for some reason you wish to silver-plate any metal you use , it will only improve performance if the silver is exceptionally pure and it is thicker than the skin-depth at the frequency of operation. Old fashioned coin-silver waveguide does not have better conductivity than plain copper (or plain aluminum, for that matter). We have used 6061 aluminum for feedhorns, transitions, filters, amplifier housings (with waveguide input and output), isolators, etc. without suffering significant losses. The components are used in very low-noise, cryogenic receivers operating at 100 GHZ.... which is a good deal more demanding than operation at 20-30 GHz. Unless your application has particular requirements that you haven't stated, you could probably let your manufacturing process determine the best material for your waveguide components.
Ronna EricksonRadio Astronomy, University of Massachusetts - Amherst, Massachusetts
Q, A, or Comment on THIS thread -or- Start a NEW Thread