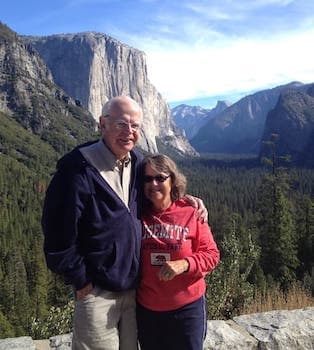
Curated with aloha by
Ted Mooney, P.E. RET
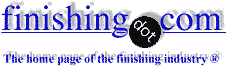
The authoritative public forum
for Metal Finishing 1989-2025
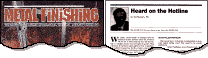
-----
420 Stainless Steel Corrosion
Dear Sir:
We're a cooking ware manufacturer, and I'm responsible for the engineering design and product development. I've heat-treated 420 Stainless Steel at 980 °C, and quench it immediately. It starts corrosion with rusty spot just after 1 hr salt-spray test.
1. As the metal part need to be hand-polished to get a gloss finish, would this destroy the protective oxide layer?
2. As the substrate (420 SS) with composition as shown below does not contain any traces of Molybdenum, and Nickel, would this affect the corrosion resistance?
3. I found that 420F Stainless Steel contains 0.6% Molybdenum, should I switch to this instead of 420SS?
4. As deformation is very serious if the heat-treatment temperature is increased to 1050 °C, so I adjust it to below 1000 °C (right now,it is 980 °C). Would this increase the chances of inter-granular corrosion as the precipitation of M23C6 carbide increased, or the "sensitization" happen?
Could you please advise me how to increase the corrosion resistance of this 420 Stainless Steel?
Element C Cr Mn Si S P
Composition 0.24 12.2 0.23 0.21 0.01 0.021
[%wt]
I will be grateful if you could suggest me how to solve the above problem.
Thanks and best regards,
Alex Au- Hong Kong
Forget about type 420 if you want to assess corrosion resistance by a salt spray test. It won't last. It's only got about 12 Cr in it, which gives resistance to rusting when exposed to normal atmospheric environments, but not much better than that.
420F has Mo as an OPTIONAL extra. The significant thing about 420F is a high sulfur content to give improved machinability. As a side effect, the high sulfur also reduces corrosion resistance, and the Mo is then added so that the harmful effect of the sulfur is not as bad as it would be without the Mo. If 420 falls short of your corrosion-resistance requirements, 420F will fall short even more.
The heat treatment that you are using will give you maximum strength, maximum brittleness, and maximum corrosion resistance - but as I said above, the maximum corrosion resistance of this material is not up to salt spray standard.
What type of cookware are you talking about? Cutlery? Pots and pans? What mechanical properties do you need - high hardness to hold a cutting edge? - ductility so that it will dent or bend if hit or dropped, rather than crack? - etc? What corrosive environment or service conditions do you actually need resistance to? Is a salt spray test, at whatever temperature you use (which you didn't mention), an appropriate test in view of the application?
All these aspects are related to each other in that you can't very often change just one thing without it affecting other aspects. They are also related to the chemistry of the stainless steel - principally (but not only) the C, Cr, Ni, Mo and N contents.
First define the properties you want, mechanical as well as corrosion-resistant, then choose a stainless steel that has those properties. It is not useful to first arbitrarily nominate a grade of stainless steel and then try to find a way of making that particular material deliver the properties you want.
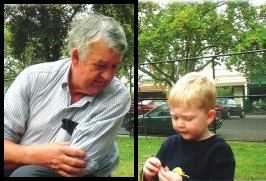
Bill Reynolds [deceased]
consultant metallurgist - Ballarat, Victoria, Australia
We sadly relate the news that Bill passed away on Jan. 29, 2010.
Dear Alex, in addition to Bill Reynolds response I propose: if you anyway need heat treatment about 980-1000 °C then you could add a gas phase in chromizing step to enhance Cr concentration in the surface region. There is a clean thermal CVD/HPHC process available.
Best regards,
Dr. Andreas Szabo- Ludwigsburg, Germany
Dear Sir:
As I need to do shape forming (a spatula) before heat-treatment. The reason for heat-treatment is that a hardness of 48 HRC is required for abrasion test purpose. Could you suggest an appropriate grade of stainless steel? I have tried 430 SS, but it cracks during shape forming, as 430 is very brittle. I was using a hydraulic forming machine [200 Tons].
Alex- Hong Kong
430 is inherently brittle, and also cannot be hardened by heat treatment. Seems unsuited to your application.
If the moderate corrosion resistance of 420 is acceptable, you could stick with that. First heat treat it at 650 to 700 degrees C for maximum ductility and formability, then press it to shape, then heat treat at 950 to 1000 °C with air cool to get hardness.
For better corrosion resistance while still being able to get hardness around the level you are seeking, 431 stainless would be a good option. It is typically 0.2 carbon, 17 chrome, 2 nickel. 17 chrome is a lot better than 12 chrome for corrosion resistance, even though you're not really looking at a particularly aggressive environment! The nickel is sufficient to make the steel heat treatable. Same heat treatment as for type 420 would be OK. 431 stainless will be a bit more expensive than 420 or 430, because of the cost of the nickel.
Past that point, you can get more corrosion resistance while maintaining hardness, but the cost will start going up quite sharply.
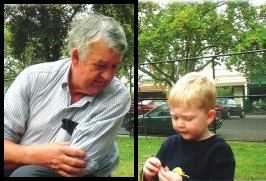
Bill Reynolds [deceased]
consultant metallurgist - Ballarat, Victoria, Australia
We sadly relate the news that Bill passed away on Jan. 29, 2010.
March 5, 2009
our company is looking to manufacture steak knives and we wanted to see which grade of stainless steel would be best. We are thinking 420 but wanted your opinion.
The rest of the knife will have full tang blades with a thickness of 2.5 mm with solid brass bolsters and rivets. The handles will be curved and made of resin so it can go in the dishwasher.
Your feedback is appreciated.
product designer - Passaic, New Jersey
Q, A, or Comment on THIS thread -or- Start a NEW Thread