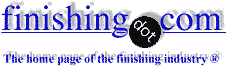
-----
Passivating welded stainless steel
Q. I have a question regarding the need to passivate welds on a 304L tank assembly. This tank will be exposed to a pH of 3-4. My concern is with the carbon migrating due to the heat of the TIG welding. I am currently looking into a MIG process called STT which should help the heat affected zone. Will passivation protect the surface only and also, will the pH of the solution the tank is being exposed to remove the passivation process?
Bob Young- Lancaster, Pennsylvania
2001
A. Bob:
Any time you weld stainless steel the welds, at least, need to be passivated if you want them to be corrosion resistant. What you end up with in the weld and heat zone of the weld are alloys that are totally different than the base metal.
Once you get the welds passivated, they should withstand the pH of 3-4 with no problem, unless you are talking about bleach, HCl or other halide containing material. These can do bad things to stainless and to welds.
pH 3-4 will not destroy the passivation layer unless it is one of the above materials or similar.
Both nitric acid and our citric acid based formulations give good results in passivation of the welds. There are pastes available if the units are too large to dip in tanks.
(adv.)
Contact us if we can help.
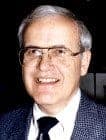

Lee Kremer
Stellar Solutions, Inc.

McHenry, Illinois
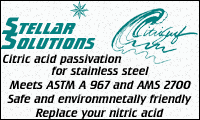
Less hazardous citric acid based passivation of stainless steel
Q. We currently use a nitric/HF paste to passivate our weld joints after welding. We have read that we could use a citric based paste to accomplish the same task. We are looking for a less hazardous material to use. Any help would be appreciated.
Jerry Reitz- State College, Pennsylvania
2001
A. We weld stainless steel and eliminate the weld burn using an electrochemical process involving phosphoric. This reduces the oxide material and passivates as well. However, to be on the safe side we also passivate using a solution of citric acid in water (10% m/v).
Nick Winstone-Cooper- Bridgend, South Wales, UK
A. Jerry:
Yes, there are excellent citric acid based products on the market that will give you good passivation of welds and other surfaces. These products do not, however, remove all of the weld discoloration like nitric/HF. To get excellent passivation and good aesthetics, you need to either remove the discoloration with Scotchbrite (TM) or other non-iron containing abrasive (316 stainless steel brush is okay) before passivation with the citric product; or you can use a good electric wand to do this. The end result is usually as good or better than using nitric/HF.
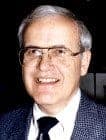

Lee Kremer
Stellar Solutions, Inc.

McHenry, Illinois
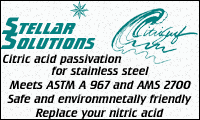
Passivating s/s weld zones
Q. I'm looking into a job that requires passivating the weld zones on 304 stainless steel. The electrode used throughout is e316L. The job is a boat bow encasement. I appreciate any info on this.
Respectfully,
Dan Mccrickard- Vancouver, BC, Canada
2003
A. There are a number of ways that you can accomplish the cleaning and passivation of the welds. First, we assume that you need to clean the welds to make them aesthetically good.
1) You can use a nitric acid/ hydrofluoric acid paste to clean and passivate the welds. This is very hazardous, but relatively easy. It will dull the surface where you apply the paste. There are a number of products on the market to do this, with varying formulations.
2) You can grind the surface free of the discoloration with Scotchbrite (TM) or other NON-IRON containing material, or a 316ss brush, and then passivate the surface with a variety of materials. The safest and easiest is to use citric acid based materials that are available on the market. There are gelled products that work well for the passivation.
3) You can bead blast the surface of the welds to remove all of the discoloration and then passivate the surface as in #2, above.
4) You can also do it easily and safely with a welder and a good product designed to remove the discoloration and passivate the surface. This is similar to a localized electropolishing operation on the weld.
adv.
Let us know if we can help.
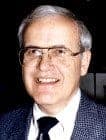

Lee Kremer
Stellar Solutions, Inc.

McHenry, Illinois
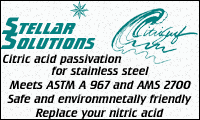
Q. We have a 316L SS container which will be used to hold a methanol and water mixture. We will be having the container passivated. My question is, once the inside is passivated and we have some spot welding on the outside of the container, will there be a problem with corrosion on the inside at those spots?
Angela Das- Richmond, BC, Canada
2001
A. Not if it's done right, Angela. The use of 316L should preclude sensitization, and I can't think of anything which would put iron particles on the inside after it's passivated.
Good luck!

Lee Gearhart
metallurgist - E. Aurora, New York
A. In general I agree with Lee but I have seen pitting take place quite rapidly in such areas. While methanol [affil links] and water sound fairly benign it depends on what is in the water. Evaporation can cause concentration of dissolved solids. Spot welding could destroy the passive surface in the area where you have welded. If there is weld tint, that area will not auto passivate and may be susceptible to attack from chlorides or similar chemicals. The fix is easy. Clean off the weld tint using pickle or even a 3M Scotchbrite pad. Clean the area thoroughly and leave it to auto passivate. Or if you want to get picky swab it with a little 20% nitric acid.
John Holroyd- Elkhorn, Wisconsin
Q. Good day, please I am doing a passivation job on an FPSO, using Weldbrite as a pickling gel. After applying it I will let it on the surface for 20 minutes, then wash off the surface and dry. Thereafter I will apply S-eld on the surface and let it for one hour before washing it with a portable water.
Please, after all this the surface is not clear; I am still having some dotted shaded area on the surface and something like brush marks on the surface as well.
Please can you help me out in these situation.
I will appreciate your help thank you.
quality control - Nigeria
March 27, 2012
A. Ubon,
I am not familiar with these products offhand. What chemistry do they use? Are we talking nitric-HF pickle paste here? You may be causing some light surface etching on your stainless. It's likely just a cosmetic issue, you should be okay as far as corrosion resistance goes. I don't know how important the appearance is for you, I know plenty of places where it shouldn't really be a requirement but people make it a requirement anyway.
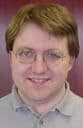
Ray Kremer
Stellar Solutions, Inc.

McHenry, Illinois
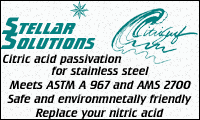
Q. We are welding 17-4 PH stainless steel end caps (.035" wall) to a 17-7 PH stainless steel tube (.035" wall). Do we need to passivate each part before the weld AND the assembly after the weld OR will it be okay to only passivate once after the weld?
Patricia PirrottaProofing mfg process - Chatsworth, California, USA
June 12, 2013
A. Patricia,
Just once, after the welding, should be sufficient.
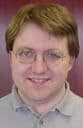
Ray Kremer
Stellar Solutions, Inc.

McHenry, Illinois
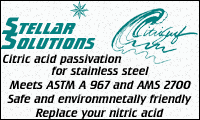
Q. Hi
We did a passivation (citric acid ) on a 5000L tank, (previously polished with Formax compound) with a spray ball according to the ASTM A967 standard. Passivation was done using the sprayballs and circulating the acid inside the tank. We had a hard time removing all the dirt inside following the mechanical polishing. After degreasing and passivation, wipe test was performed and results were conform. The shine in (discoloration) the welded areas (heat affected zones) is different than the base metal and on some part of the spray Balls (round spots). Our toughts are that it is probably caused by the heat during welding and the difference between the chemistry of the base material (316) and the welding electrode? The passivation and degreasing process took a total of 8 hours (many cycles of degreasing, until clean, before passivation) to be sure to remove all dirt and smut, and the white discoloration can be seen on the spray Balls (round spots) and on the welded areas.
What is the cause? Does the citric acid change the resistance of the stainless steel to products after passivation?
Thank you!
- Montreal, Quebec, Canada
June 13, 2013
A. Remy,
I'm a little confused by your question. Yes, passivation with citric acid (or nitric acid also) changes the resistance of stainless steel to corrosion, it increases it.
The discoloration you refer to, might that be areas where the surface finish is different? If you are talking about places that were welded and then ground smooth, that would certainly be the case if it was not polished in a way that matches the surrounding areas. Nitric passivation has the ability to cause a light etch on all surfaces and might hide this effect somewhat, but citric acid does not etch the surface and so any differences in the surface finish will remain.
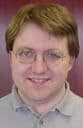
Ray Kremer
Stellar Solutions, Inc.

McHenry, Illinois
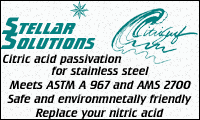
Mechanical and chemical passivation treatment for welded 316 SS for ultra pure water
Q. I just had a chamber for an ultra pure water bath (20-60 °C) built in our machine shop and need to treat it to prevent corrosion. I had it built out of 316/L stainless steel since it is going to be filled with ultra pure (18 M Ohm) water and would like to keep it rust free. Unfortunately, it has some significant weld discoloration and the sheets used for the walls weren't machined smooth before being welded in (they were annealed and hot-rolled by the mfgr: McMaster 9195K11 or similar). I don't remember what method was used for the welding, but the bead is about 1/8" wide and has brown and blue discoloration for the welded on flanges and there is some discoloration on the inside from the outside corner welds. I am trying to figure out how much I have to do to passivate it and ensure corrosion resistance. Here is a picture of some of the weld discoloration --
From searching around here and the internet it seems like what I need to do is:
- remove any grease (I've already cleaned it with Alconox
⇦ on
eBay
or
Amazon [affil links] )
- mechanically clean the surface of at least the welds (maybe optional)
- maybe pickle if it is bad enough
- passivate (preferably with citric acid )
Our machine shop guy suggested bead blasting to clean up the surface, removing any burrs and making it look prettier, but I am not sure. I know to put it before the passivation step if I do it.
Is bead blasting a good or bad idea?
Do I need to get the weld discoloration off with a wire brush or similar tool?
What about electropolishing, can that be done instead of or in addition too passivation?
"CURRENT METHODOLOGIES & CHEMISTRIES UTILIZED IN EFFECTIVE PASSIVATION PROCEDURES" by Daryl Roll seems to indicate that I don't need to remove the discoloration if I passivate and that electropolishing may not be as good, but is attractive for smoothing the surface.
Do I need to pickle? I don't think I have scale, but I'm not sure.
Researcher - Atlanta, Georgia
February 23, 2015
![]() |
- Diksmuide, Belgium, Europe A. I've already spoken to Justin about his application, but for posterity, as long as he passivates the weld, discoloration shouldn't hurt anything. Bead blasting would be okay (which will remove the discoloration as well), with passivation afterwards. ![]() Ray Kremer Stellar Solutions, Inc. ![]() McHenry, Illinois ![]() |
A. Hi Justin. Everyone is welcome to give their opinion based on their own experience, and you've heard simultaneously from two people with differing takes ... who did not have the benefit of seeing the other's reply ...
When you look with a high enough resolution microscope, all mechanically finished surfaces look like plowed fields, whereas electropolished surfaces look like ocean swells. So for the ultimate cleanability, nothing matches electropolishing. But in the case of a tank that contains only ultrapure water, with nothing to clean, nothing to contaminate the next batch, I don't think Ray is wrong either. It would be great if you could make two tanks and we could have a real resolution :-)
Regards,
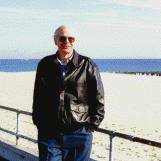
Ted Mooney, P.E.
Striving to live Aloha
finishing.com - Pine Beach, New Jersey
Q. Electropolishing is very attractive for the nice finish and other reasons mentioned, but from my short reading on it, the rather complicated chamber shape with ports, threaded holes, and stuff might make it difficult to set up an electrode for even current flow.
I will give it a go with light brush cleaning, sonicate clean with Alconox, rinse, passivate with Citrisurf 2050 in the heated sonicator (thanks Ray), hot DI water rinse, dry. I'll update if there are any failures or interesting results but I really don't want to make a second tank as this one took a while.
I unfortunately will end up having part of one of the ports be in (soon to be anodized) aluminum. I will be adding o-ring spacers to try to prevent any galvanic corrosion. Hopefully that doesn't hurt me too much.
- Atlanta, Georgia, USA
A. Hi again. I was only kidding about a second tank; people can't usually double their capital outlay for the sake of an experiment.
You can't have galvanic corrosion as long as the aluminum does not connect to the stainless metal-to-metal. Good luck.
Regards,
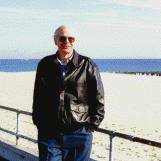
Ted Mooney, P.E.
Striving to live Aloha
finishing.com - Pine Beach, New Jersey
A. Local electropolishing, of welded area only,is the cheapest and optimal surface protection.
adv.
Contact me for more information.
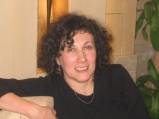
Anna Berkovich
Russamer Lab

Pittsburgh, Pennsylvania
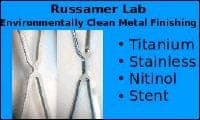
Q. Hi.
I have been asked to quote fabrication of a chemical processing tank for a custom plating company:
I.D. 18" cube
Material: 316 SS
Finish: 2B
Solution: 50% sulfuric acid at 200 °F degrees maximum
Immersion heated
No impurities
Adherent deposits
Open to atmosphere
Circulation >1.5 meters/minute
I would like to know what post-weld treatments you would recommend, such as stress relief, pickling, passivation, etc.
Thank you very much
- San Diego, California USA
June 25, 2015
A. Hi Michael. The short answer is 1). don't embarrass your company with shoddy work; 2). comply with the specs; 3). that's it :-)
I was involved in the manufacture of thousands of tanks for plating lines and don't remember ever having one stress relieved. The slag is removed from the welds and that's usually it, with any further leaching, etc., done by the buyer. Make sure the buyer has double checked that 316 is the proper material of construction, then suggest 316L (which these days is often the same price & spec as 316). Despite the very small size of the tank, consider making it out of 3/16" thick plate, welded inside and out, and you'll never have to worry about that tank again :-)
Regards,
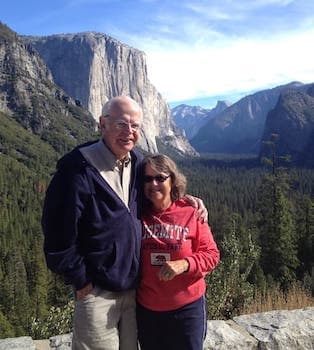
Ted Mooney, P.E. RET
Striving to live Aloha
finishing.com - Pine Beach, New Jersey
Polishing & passivating stainless steel conveyors & platforms
Q. I own a company that fabricates conveyors, platforms, and items for the food industry. We never really have a problem with any of our stainless steel, but I have noticed that in a few different rooms at different companies, some stainless steel is rusting. It may be our stuff, it may be from another company that specializes in stainless.
We currently just use scotch brite pads on die grinders [adv: die grinders on
eBay
or
Amazon [affil links] , with some minor polishing compound. We have to keep everything food safe so we don't use much in the field.
What are efficient ways to clean/passivate stainless in the shop, without taking it to a passivation shop. We always try to passivate, but our time frames may not allow that to happen.
Most things are just tig welded with no sanding of welds.
- New Jersey
August 20, 2015
A. John,
A lot of food equipment (and other large fabrications) these days are passivated with a citric acid based gel/paste type product. This allows you to do it yourself safely and with no immersion tank.
There are versions that remove rust as well as passivate that your customers can use on their affected equipment. Most of the time that will start popping up due to bleach or otherwise high chloride cleaners being used. Also unpassivated welds tend to go first, especially in instances of cross contamination with mild steel.
adv.
Let us know if we can help.
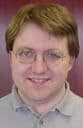
Ray Kremer
Stellar Solutions, Inc.

McHenry, Illinois
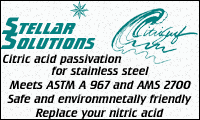
A. John,
There can be some ways to solve this problem:
1. Passivate by spraying or applying passivating gel locally (you can deliver the gel and instructions to your customers).
2. During conveyer manufacturing stage, add additional step of electropolishing it. This way you prevent ways ahead rusting problems.
adv.
See attached picture of our tests of continuous electropolishing of conveyor line.
Contact me for more information.
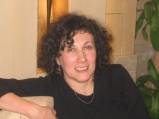
Anna Berkovich
Russamer Lab

Pittsburgh, Pennsylvania
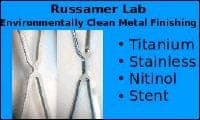
Protecting weld areas on 316L stainless steel from hydrochloric acid and sulfuric acid
Q. We produce welded rings made from 0.1875" diameter wire in 12.00" O.D.
These are used in coal fired electric plants. One of the by-products of burning coal is the production of both hydrochloric acid and sulfuric acid. These are produced in small amounts but continuously.
We produce these rings from type 316L stainless steel. We have not been passivating the rings and the welds have been failing.
Which will give us better performance, adding the passivation or adding an ecoat of Bis F epoxy? Or should we be doing both?
- Yonkers, New York USA
December 21, 2016
A. Hi Howard. The main reason that 316L exists is because of the well known problem that welding of 316 stainless steel causes a carbon segregation that leads to attack on the welded areas. Thus, if the remainder of the object is not excessively attacked, the first thing I'd suggest is making absolutely sure your plates and welding rods are actually the correct material.
Regards,
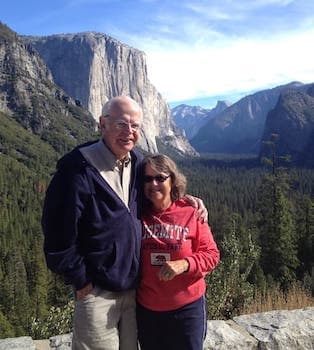
Ted Mooney, P.E. RET
Striving to live Aloha
finishing.com - Pine Beach, New Jersey
Q. This is a sacrificial welding process using argon gas. It is a highly modified version of standard welding equipment that was developed in house and the details of which I am not permitted to disclose.
But there is no welding rod or plate. We fuse the ends of the wires together.
So there should be no outside contamination involved. We supply heat to the joining ends and bathe the weld area with argon gas.
I wish I could say more but I am restricted in that regard.
We are running tests with 316L wire coated with epoxy Bis F. This adds quite a bit of cost. Indeed we are seeing costs for the passivating that are similar to the epoxy coating.
So are we better served with the epoxy coating or by passivating the parts?
Howard
- Yonkers, New York USA
A. Howard,
Hydrochloric acid is the worst thing for stainless steel. Even well-passivated 316 will not hold up to that abuse without periodic re-passivation treatments.
Also, un-passivated welds will always corrode long before the rest of the piece does.
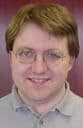
Ray Kremer
Stellar Solutions, Inc.

McHenry, Illinois
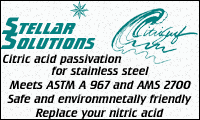
Q. We have to fabricate Duplex Stainless Steel tank with dish ends. After completion of one dish end welding pickling, passivation is carried out on nozzles & seams.
Now closing dish end welding is to be carried out.
Can we do welding on passivated area? After welding of closing dish end, passivation and redo pickling, passivation of affected area?
enpro industries pvt ltd. - Pune, Maharashtra, India
June 28, 2018
A. Chandrakant,
Pickling or passivation must be redone along the welds to restore full corrosion resistance, yes. A gel or paste type product is often used.
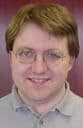
Ray Kremer
Stellar Solutions, Inc.

McHenry, Illinois
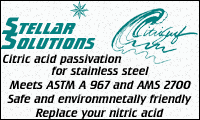
Q. I have done the welding SS304L piping and am required to do nitric acid passivation. After treatment with NaOH and HNO3 passivation, I found out that the welding joint is yellowish. So can anyone help me to figure out what is the yellowish on welding joint?
NG WEY KEAN- Sungai Bakap, Malaysia, Pulau Pinang
March 14, 2020
Q, A, or Comment on THIS thread -or- Start a NEW Thread