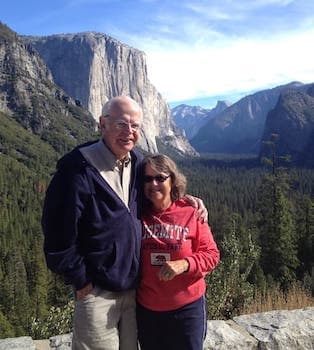
Curated with aloha by
Ted Mooney, P.E. RET
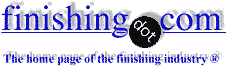
The authoritative public forum
for Metal Finishing 1989-2025
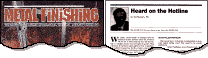
-----
Porosity in electroplated zinc
Our supplier is electroplating zinc over 1010 steel. We are seeing a lot of porosity of the zinc deposit. It is a chloride-zinc bath, so the deposit should be laminar in formation. What factors are important to minimize the porosity of the deposit? Suggestions regarding plating bath chemistry and/or the plating process itself are welcomed.
With regard to quantifying the porosity of the deposit, I would appreciate suggestions. ASTM B809 lists a "flowers of sulfur" test. SEM analysis and viewing a cross-section @ 500+X are a little costly, and time-consuming. Other tests that provide a relatively quick & reasonably accurate answer are welcomed.
Steve Engel- Aurora, Colorado, USA
Steve, need more information. What do you mean, porous zinc plating? Pits, unplated areas, etc.? Why are you trying to check the porosity? It should not be.
Bill Hemptech svc. w/ chemical supplier - Grand Rapids, Michigan
The surface of the zinc looks like a matte finish when viewed @30X. The coverage is consistent and uniform.
The troublesome part (flange) is wrapped around a pressurized device. Prior to shipping, the assembly is placed in a leak test chamber, which draws a vacuum and analyzes the gas, to determine if the pressurized device is leaking. The zinc deposit of the flange is porous and is significantly increasing the amount of time required to attain a high vacuum level. If the deposit is stripped down to bare steel, this "outgassing" does not occur. The flange is plated with zinc and yellow chromate to meet salt spray requirements.
Steve Engel- Aurora, Colorado, USA
I'm doing some tests to determine the adhesion of zinc onto aluminium. I'm plating at 440 A/m2 from a zinc sulphate bath ([Zn]=
55g/l, [H2SO4]=160 g/L) at 38 °C. The plating time is 30 min and I calculate the thickness of the deposit to be around 30 microns. Before peeling the zinc off the aluminium I'm gluing a brass block to the electrodeposited zinc with Selley's SupaGlue.
Would the zinc at this thickness and deposited under such conditions be sufficiently porous to allow the glue to permeate through to the aluminium substrate?
- Perth, Western Australia, Australia
June 25, 2010
I am facing a similar problem like the one mentioned above...
We are sending a CRS chassis to a zinc plater (acid bath zinc plating)... after powder paint applied on it...We tested the unit on a salt spray chamber.... after 72 hrs in the chamber... tiny red spots shown up on the surface... In your search, did you find an answer why the zinc coating can be porous ? is some gas coming out from the zinc plating after the bath? ... why?
I would really appreciate your kind comment..
Best Regards
- Guadalajara, Jal. Mexico
Q, A, or Comment on THIS thread -or- Start a NEW Thread