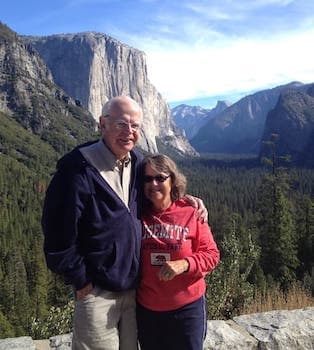
Curated with aloha by
Ted Mooney, P.E. RET
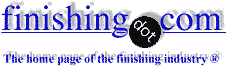
The authoritative public forum
for Metal Finishing 1989-2025
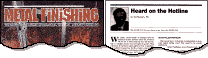
-----
Breakdown and leaks in Black Oxide and Iron Phosphate Tank
Q. We are experiencing a problem here that at this point is almost impossible to explain. We operate a black oxide process where the solution consists of sodium hydroxide, sodium nitrite, sodium nitrate ⇦ this on Amazon [affil link] , nickel nitrate, and water. It operates at 280 - 290 °F. Three years ago we replaced a mild steel black oxide tank that had been in operation approximately 25 years with a new tank made from a mild steel A36 hot roll pickled and oiled and MIG welded with ER 70S wire.
Both, the old and new, tanks were double walled, a tank inside of a tank, with a 4" air space used for insulation. A few weeks ago we noticed that the 4" had filled up with black oxide solution and started leaking from the outer wall on a corner. After examining the tank closer, we found that the tank seemed to be corroding from the inside.
Our question is: "What would cause a high pH caustic solution to attack mild steel in only three years?" There is no "stray current" whatsoever checking from tank to ground.
Thank you,
- Charlotte, North Carolina
A. Hi David. Sorry, but this one is a mystery to me as well. It seems there may be 3 possibilities:
First, that some other chemical like a fluoride salt or a dry acid salt got accidentally added at some point. But I would expect a very strong reaction had this occurred, and damage to the production work as well.
Second, that the corrosion actually started in the air space, despite the fact that it doesn't look that way to you.
Third, that there is a stray current at certain times that you haven't found at the times you were checking.
In my experience a plain steel tank is resistant to attack from the black oxide solution almost indefinitely.
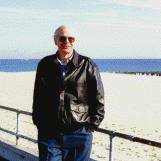
Ted Mooney, P.E.
Striving to live Aloha
finishing.com - Pine Beach, New Jersey
A. It's probably too late now, but the material was probably not heat treated prior to fabrication. If this is the case, the tank will probably start to leak at most of the welded seams (due to the additional heat stresses in those areas).
Ed Simpson- Hamden, Connecticut
A. Thanks, Ed, although I am not familiar with ever specifying stress relief for a mild steel black oxide tank, maybe I've just been lucky. I always specified the same hot rolled mild steel plates for all of the non-stainless and non-plastic plating and process tanks I've designed.
But I've never designed a double wall mild steel tank -- which raises another possibility. Welding of tanks is usually done both inside and outside. Obviously, with a double-wall tank with a 4" air space, you can't double weld both the outside of the inner tank and the inside of the outer tank. Is it possible that the inner tank only had a single weld instead of a double weld? (When I've designed insulated tanks, it was a conventional inner tank, then the insulation, then bolted cover panels to protect the insulation).
Regards,
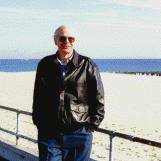
Ted Mooney, P.E.
Striving to live Aloha
finishing.com - Pine Beach, New Jersey
October 18, 2012
Q. Dear sir ,
We are using iron phosphating for a pre-treatment process in powder coating application .
Our iron phosphating tank is leaking; please suggest what are the conditions of tank replacements, i.e.,
* What metal do we have to use.
*Should there be any type of lining (FRP, RUBBER, ETC.) on inside portion of the tank.
plating shop employee - Haridwar, Uttrakhand, India
February 23, 2009
A. Hi Arjun.
Mild steel tanks are no good for iron phosphate, which can have a pH as low as 4.5, i.e., reasonably acidic. My own preference wherever it is suitable, which it probably is in this case, is a vinyl ester fiberglass tank. But a polypropylene tank or a steel tank with a PVC liner would be okay too.
Regards,
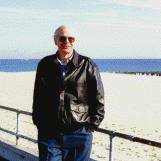
Ted Mooney, P.E.
Striving to live Aloha
finishing.com - Pine Beach, New Jersey
October 18, 2012
Material of Construction for Black Oxide Tank
Q. I am using a mild steel tank for Blackodize process. So is it right?
gosai jaydipheat engineering works - surat, gujarat, India
April 22, 2014
A. Hi Gosai. We appended your question to a thread indicating that it is not always trouble-free, but in my experience I think it will be fine. Other opinions are always welcome.
Regards,
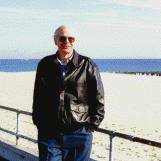
Ted Mooney, P.E.
Striving to live Aloha
finishing.com - Pine Beach, New Jersey
April 2014
Q, A, or Comment on THIS thread -or- Start a NEW Thread