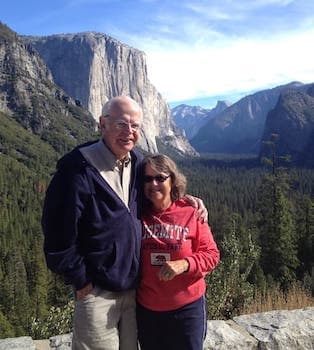
Curated with aloha by
Ted Mooney, P.E. RET
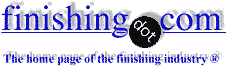
The authoritative public forum
for Metal Finishing 1989-2025
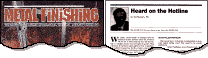
-----
Superfinishing Case Hardened Gears by "Abral Process" vs. Electropolishing vs. Low-friction Lube?
Q. Hello-
I own/operate a small machine/fabrication shop and I'm interested in the "Abral Process". The "Abral Process" is a three stage process. Case Hardened gears are immersed in a bed of small zinc chips, water, and aluminum oxide powder. The container is vibrated for several hours and the grade of oxide powder is increased in fineness in several stages. Is anyone familiar with this process? I do know the process is being applied in the aerospace industry and Formula 1. I've researched the subject but come up empty handed. Desire the grit and zinc dimension. Also who could supply this material? I have the vibrators.
Thank you for your help.
- Amelia Island, Florida, USA
A. You might want to check Italy. I think this is a proprietary system.
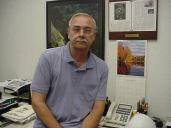
AF Kenton
retired business owner - Hatboro, Pennsylvania
A. Try www.abralux.it/finit.htm
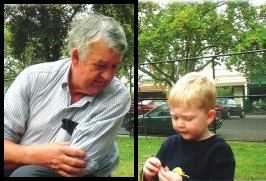
Bill Reynolds [deceased]
consultant metallurgist - Ballarat, Victoria, Australia
We sadly relate the news that Bill passed away on Jan. 29, 2010.
A. Just thought I'd add something here. When a customer asks for a specific process, it might be better to ask your end customer what he wants to achieve. There are a number of ways to cross a river. This process and a number of products are usually similar and achieve comparable results. It's a great way to hook people into brand names and processes. Also they usually cost more and achieve the same results as those that are more familiar. I'd go back to your customer.
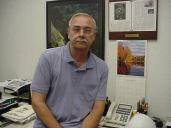
AF Kenton
retired business owner - Hatboro, Pennsylvania
Low friction coatings for gears
Q. I am working on a project. I do not yet know much about coating steel (small steel gears, shafts, etc) with a material that has low friction. I want a lower friction coefficient (<<0.09). So far, I glimpsed at Nickel Boron and Argonne. I heard that Nickel Boron had in the past, had a peeling problem, but they might have improved since. Please write me with your suggestions and knowledge on these or other coatings.
Thank You,
aerospace engineering - Santa Clarita, California, USA
2004
A. Myna, you will find there is no "one size fits all" optimum coating. I mean if all you want is a slippery coating, I suggest grease. Oh, you want it to last in service? Try a diamond-like coating. Oh, you were going to apply heavy contact loads? Why didn't you say so! And on and on...
You can likely learn a lot by chatting with some vendors who offer a variety of coatings and note in their advertising that they have done gears. General Magnaplate is one. Good luck!

Lee Gearhart
metallurgist - E. Aurora, New York
2004
A. We have seen various examples where cryogenic treatment of steel has reduced its coefficient of friction. Ideally, the steel should be treated before final polish, but it also benefits many steel pieces in their finished state. I do not know if you will realize your objectives by this method, but it may worth a try. Other benefits include residual stress relief and increased resistance to wear in higher carbon steels.
Robin RhodesWorcester, Massachusetts
2004
A. The July/August 2004 issue of Gear Technology has an article from ZF about two types of coatings for gears: boron carbide (B4C) and tungsten carbide-carbon (WC/C). In addition to coatings, you should evaluate chemically accelerated superfinishing, as the resultant surface finish (Rz = 0.5 micrometers) can improve friction as well.
Toby PadfieldAutomotive module supplier - Michigan
2004
Electropolishing of case hardened gears
Q. I must electropolish gears made by case hardened steel (18NiCrMo5) that is ground with Ra 0,2. My goal is to lower the roughness as much as possible, the target is Ra 0,05 or lower. Pieces are about 200 mm length 40 mm diameter. I am looking for the better solution, temperature, voltage or A/surface, time.
Thank you in advance for your answer.
- Modena, Italy
A. It is typically quoted that Ra's can be reduced by a half using electropolishing. You are starting at .2 and want to reduce it to .05. That may be more than is reasonable. I have gone beyond a 50% reduction but that requires the removal of a lot of metal from the surface. I would then worry about removing the case hardening and making your gears too soft.
Gears can be difficult because of the Faraday cage effect. You will get the best results with a conforming cathode. With non-conforming cathodes I would guess that you are seeing some pitting as you get deeper between the teeth though this will depend upon the precise geometry of the teeth. As for current density you should maintain a current of .15 Amps per square centimeter or higher at a temperature of 50 to 65 °C.
I hope these comments help and good luck with your project.
- Elkhorn, Wisconsin
Q. I'm looking for comparative data between superfinishing and electropolishing in terms of gear fatigue life. Both methods seem to increase life. What are the pros and cons of both methods ?
Thanks
product designer - Montreal, QC, Canada
2007
Q. I have large gears made from maraging steel 250 KSI and using WEDM to cut the teeth. The WEDM process leaves an unacceptable .0004 thick layer of untempered martensite that appears to be approx. 60-65 Rc. I have tried different methods to remove this "white layer" but due to not being able to control dimensional changes once the martensite layer is penetrated, have stopped. I'm currently spending hours and hours hand polishing the gear teeth and would like to find a more controlled and less expensive solution.
Will electropolish or other finishing solution do the job?
- Fridley, MN, USA
2006
A. .0004" can be quickly and easily removed in an appropriate electropolishing solution composed of phosphoric and chromic acid.
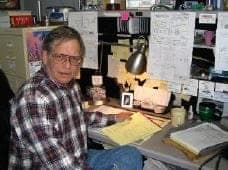
Jeffrey Holmes, CEF
Spartanburg, South Carolina
2006
A. Bill, I'm not sure but what about a pickling agent to help clean the gear up?
Kevin W. Gallich- Freemansburg, Pennsylvania, USA
2006
Q. I have not tried pickling, I didn't think it would penetrate that far. If it were to remove .0004 of the hard material, wouldn't it remove much more of the softer base material. Since this is a precision gear sector, consistent material removal is key. I will look into it though.
I thought of electropolish but the problem is I can't find anyone local who will electropolish carbon steel, and we don't want to set up tanks in our facility. Thanks,
- Fridley, Minnesota, USA
2006
![]() |
A. I agree, you don't want to set up electropolishing in-house. Too much investment and trouble. There are shops which EP carbon steel. Find a good one, communicate your needs clearly, and you'll solve your problem for a few dollars per part. If you're now spending hours hand polishing, the cost of shipping for electropolishing would be small by comparison. Please don't try acid pickling. You'll likely end up with hydrogen embrittlement -- a serious problem. ![]() Jeffrey Holmes, CEF Spartanburg, South Carolina 2006 A. Don't mess with chemical methods, that's not the way. Have them ground in a special gear grinder. Precise, controllable, able to cut through hard materials and leaves an even and quality looking surface finish. Guillermo MarrufoMonterrey, NL, Mexico 2006 |
Q, A, or Comment on THIS thread -or- Start a NEW Thread