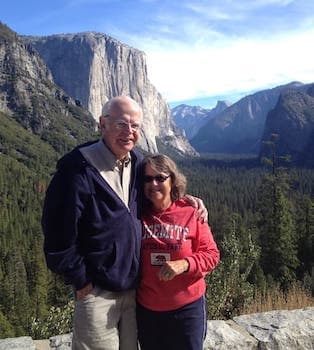
Curated with aloha by
Ted Mooney, P.E. RET
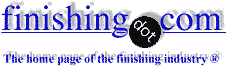
The authoritative public forum
for Metal Finishing 1989-2025
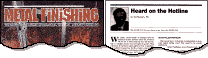
-----
Electroless Nickel Plate / Life testing
1998
We are using electroless nickel to plate mild cold rolled steel equipment frames. These frames are complex shapes with a significant amount of welds. We are homing in on a process to control the plating but the management guys want to be assured the plate will last and protect for ten years.
Is there some accelerated life test anyone knows about the we can run and makes some sense?
Our user environment is pretty benign. Worst case, assume a poorly controlled computer room. Temp 28C ± 10C and 40 to 90% RHI.
Gary EppKLA-Tencor
1997
All accelerated tests are for corrosion in a specific environment. Salt spray for instance, does not prove much and can be manipulated by the testing agency. It does point out gross failure, however.
The packing material has a lot to do with the failure. Fingerprints and other handling after plate will affect time to failure. Abuse will have more to do with it than most other things.
Thickness of your EN will be a major factor in how it will stand up.
Finally, what statistical reliability are you looking for, 1,2,3 or more sigma.
James Watts- Navarre, Florida
1998
Gary,
We also plate E.N. and have gone through similar situations of how long will the coating last. For our high corrosion finish we apply a high phos E.N. followed by a chromium seal. The thickness also plays a major part, and do not believe what chemical suppliers say when it comes to their particular system, giving 1,000 hours.
When looking at E.N. with respect to high corrosion protection, or any other property you want from E.N., always start with 1.0 mils. Porosity is a major factor on the finished coating, so make sure you do an acid copper test. ( it shows up any exposed base metal )
If cost is a factor, I have had good experience plating 0.5 mils, but "bumping" the parts for the first 60 seconds. I can have this lower coating thickness go up to 1400 hours to R.R.
Finally, do not expect fast plating rates. We typically plate between 0.25 and 0.3 mils per hour. This reduces porosity and favors the phos content, required for corrosion protection.
How long will the coating last? Many years ago, I had a discussion with a General Motors specification guru. His rule of thumb, was that for every year you wanted a part to last on your car, before it rusted, make sure the part tested for 80 hours in N.S.S.
Regards,
Ray
INDUSTRIAL PROCESSING
Responding to the question on level of assurance: one failure in 100 systems over ten years would probably be tolerable.
Roughly half of the systems will be in an extremely tightly controlled (clean room) environment. Temp 23C ± 2C and RHI 40% ± 5%. Significant formation of Fe2O3 or nickel flaking on these systems would be detectable and considered a failure.
The other half of the systems will be in rooms similar to computer rooms. Temp 28C ± 10C and RHI 30-65% with occasional peaks to 95%.
Gary EppKLA-Tencor
1998
ENP has been "frowned upon" by the Military for the plating of connector shells, due to corrosion in a salt atmosphere. Does anyone happen to know why only certain MIL connector specs have been changed to reflect this ?
Tom Lambert1998
All military specs are on the way out and are being cancelled after a lot of discussions and inputs by various agencies involved. These will be replaced by commercial specs when all agencies agree upon it spec-by-spec. I am not surprised that some are changed because a decision was reached quickly. Others may wait till eliminated. Spec change can be a long drawn out process, about 3 to 4 years, sometimes.
Mandar Sunthankar- Fort Collins, Colorado
1998
1999
I am searching for a supplier of Nickel Plated Mild Steel Wire (daimeter range--2.5 mm to 5 mm) preferably in India. Any leads worldwide welcome. HELP!
Deepak OberoiQ, A, or Comment on THIS thread -or- Start a NEW Thread