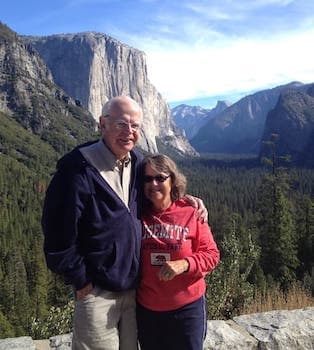
Curated with aloha by
Ted Mooney, P.E. RET
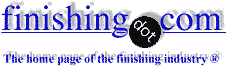
The authoritative public forum
for Metal Finishing 1989-2025
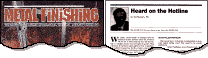
-----
Electrical Properties of Passivated Stainless Steel
Quickstart:
Stainless steel can get minute particles or dusts of plain steel/iron on its surface as a result of machining, steel wooling, or other operations.
These particles not only rust themselves, but they serve as initiation points for wide scale rusting and pitting.
Passivation is an operation entailing immersion of the stainless steel into nitric or citric acid, which dissolves any iron on the surface, and helps build a chromium-rich surface.
this text gets replaced with bannerText
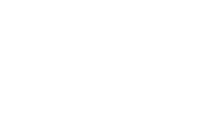
Q. Hello everyone,
I have a question related to the passivation of the stainless steel. As we are using 304, and after a while of subjected to heat, it becomes yellow due to heat tint. So, my question is: can I measure the electrical conductivity of the stainless steel before using and after it has a heat tint, as a validation of the performance of the passivation layer?
- Cairo, Egypt
December 27, 2024
A. Hi Mahmoud. Proper passivation is about freedom from iron, and possibly a higher chromium content. It strikes me as extrapolation to think that we are able to judge such purities from surface conductivity. But maybe I'll learn something here 🙂
Luck & Regards,
Ted Mooney, P.E. RET
Striving to live Aloha
finishing.com - Pine Beach, New Jersey
A. Ted,
There are devices on the market that purport to quantitatively measure the stainless passive layer by means of conductivity, per the differential between the conductivity of the raw stainless alloy composition versus the conductivity of the iron-depleted (and therefore higher chromium & chromium oxide) passive layer.
However, given the incredible thinness of the passive layer, I will leave it to the reader to render an opinion on the practicality of actually measuring this in a meaningful way. I will however note that this method is not recognized by the major modern industry passivation standards.
As to Mahmoud's question, I'm not sure how heat discoloration comes into this. The performance of the passive layer (to resist the formation of iron oxide corrosion) is completely independent of the tendency of stainless to discolor under high heat (the prevailing theories I've seen on this seem to relate it to the formation of carbides). I'm also not sure if he's alleging that heat-tinted stainless will have yet another different conductivity value.
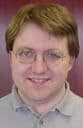
Ray Kremer
Stellar Solutions, Inc.

McHenry, Illinois
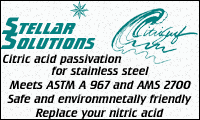
January 2, 2025
⇩ Related postings, oldest first ⇩
Q. I am trying to determine the electrical properties of the passivation on 303 stainless steel. I need to know either resistivity or conductivity and any associated conditions (e.g., measured using a contact area of 1 square inch and 100 lbs of force).
The reason I'm seeking this info is that we use stainless steel body RF connectors in our equipment and from time to time have bonding impedance problems between the connector shells and the AMSC5541 class 3 finish on our aluminum chasses.
Any help or insight would be greatly appreciated.
Thanks
Donald Matteson1998
A. The electrical properties of stainless steel are poor at best. For materials that have helicoils installed in the case, grounding should not be a problem. Normally the abuse of bolting two pieces together will break the chem film enough for contact. If you are having a problem, can you add inside star lock washers? they will definitely break thru. Or, have I misunderstood the question?
James Watts- Navarre, Florida
Q. Does passivating a stainless steel component interfere with its conductivity? I.e., should bonding surfaces have the passivation layer removed?
Kelly Lively-Jones- Nova Scotia, Canada
2001
A. Hello Kelly!
No, you don't want to try to remove the passive layer. First because it doesn't interfere with the electrical properties: heck, we in the aerospace industry even bond over type 3 conversion coating, which has got to be worse. Second, because the risk of getting corrosion in the bond area if you activate the surface is real, and corrosion products are usually non-conductive. Better to passivate.
Good luck!

Lee Gearhart
metallurgist - E. Aurora, New York
Electrical Properties of Anodized Stainless Steel
Q. My question is similar the one that initiated this thread. My question is how to induce a slight electrical resistance to the surface of 303 or 304 Stainless Steel. Between two point probes about 2 mm apart, of a standard ohmmeter touching a surface, we need achieve a resistance between 100 and 1000 ohms.
We are seeking a technique that would achieve this surface resistance, but not be attacked by water. It could be any surface modification including plating.
Thank you.
- Plymouth, Massachusetts USA
December 22, 2014
A. Hi Harry. 100 - 1000 ohms is approximately the resistance range of incandescent household lightbulbs. I would imagine than this could be accomplished with a thin anodized layer but I'm not sure. A stainless steel anodizer like B&M Finishers / Prismatic Stainless Steel [a finishing.com supporting advertiser] can probably advise you of the typical contact resistance of their Prismatic anodized stainless steel surface.
Regards,
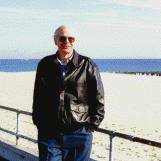
Ted Mooney, P.E.
Striving to live Aloha
finishing.com - Pine Beach, New Jersey
A. Hi Harry,
My own field of experience is in the anodizing of aluminium. I have no idea whether anodized stainless steel gives significant surface resistance. But if it does, the use of ohmmeter standard test probes is not appropriate for the measurement. The bulk of the total resistance will be made up by the film. So the surface area of contact becomes critical. If a value for resistance is given, it will be in the form of resistance for a given area. The sharpness of the prods and pressure applied (hence the area of contact) will be all important.
It maybe inappropriate in your application, but consider the use of external resistance.
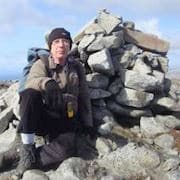
Harry Parkes
- Birmingham, UK
A. Hi Harry S. Perhaps an adhesive graphite pen (for applications < 100 °C) or an adhesive graphite paint (for applications < 200 °C) will suffice. If the graphite offers too much electrical resistance for the specific application, a carbon-based adhesive paint could be an option because they generally are an order of magnitude more electrically conductive in comparison to graphite. One nice feature of a carbon-based system would be a wider temperature range (for example: -40 < t < 260 °C).
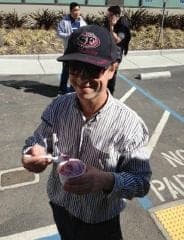
Blake Kneedler
Feather Hollow Eng. - Stockton, California
Q. We are currently using our RF products for gold plated finish stainless steel. We decided to passivate the finished stainless steel product, but facing the conductive issue and reflects our VSWR test low frequency poor performance.
Need to know the passivated plated stainless electrical conductivity act as like gold plated material?
employee - CHENNAI,tamilnadu, India
July 7, 2022
A. Hi gokulraj. I'm not sure if I am correctly reading your question, but passivated stainless steel is absolutely nothing like gold plated stainless steel. Gold plating is a perfect finish for electrical conductivity; stainless steel whether passivated or with just the natural passivation layer is a terrible surface for conductivity. Plus, plating only adheres properly to raw, active metal -- not to the oxides of passivation. I suspect that the nickel strike before gold plating completely destroys the passivation anyway.
Luck & Regards,
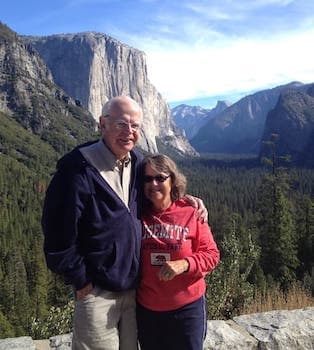
Ted Mooney, P.E. RET
Striving to live Aloha
finishing.com - Pine Beach, New Jersey
Q, A, or Comment on THIS thread -or- Start a NEW Thread