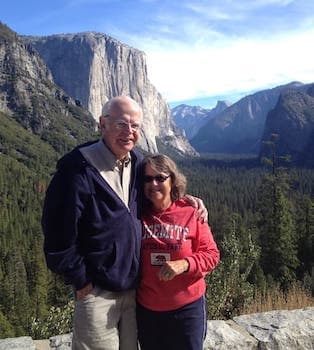
Curated with aloha by
Ted Mooney, P.E. RET
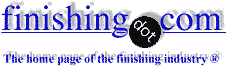
The authoritative public forum
for Metal Finishing 1989-2025
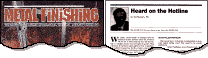
-----
Conditioning aluminum test coupons for Taber Test (ASTM D 4060)
Q. Hello there! I'm the Quality Manager at an anodize house. We just got written up for this requirement in our last Nadcap audit. We are working on getting a humidifier (we were only at 23% the day of the audit) but am curious on the intent of this requirement. Is there any risk to product for previous tests not conditioned in the proper humidity?
Brian Harries- New Britain, Connecticut
January 30, 2023
⇩ Related postings, oldest first ⇩
Q. I am working with hard anodized aluminium and its abrasion resistance, for this I am constructing a FALEX abrasion testing machine according to standard ASTM G65-04 I need more information about conditions of anodizing, film formation, and about the abrasion test.
thanks.
ENRIQUE RODRIGUEZNATIONAL UNIVERSITY OF TRUJILLO - PERU
1998
Q. I perform QA audits for the aerospace industry (NADCAP). Subcontractors anodizing aluminum alloys perform monthly abrasion resistance tests by the Taber Method per ASTM D4060. The anodized 4-inch test coupons must be "conditioned" (per paragraph 9 and "unless otherwise agreed upon by the purchaser and seller") at least 24 hours at 23± 2 °C and 50 ± 5% relative humidity. My auditees have no problem with the time & temperature requirements, but cannot easily maintain the humidity. I would like to be able to help them conform; not just issue the ever-popular Non-Conformance Report. I seem to remember years ago doing this in a standard laboratory dessicator, replacing the usual calcium sulphate "Dryerite" dessicant with another material--perhaps one of the lithium salts? Does anyone know this technique?
Doug Hahn- Mason, Ohio
2001
A. Use a slush of calcium nitrate and distilled water to hold the 50% relative humidity. Get some good commercial or reagent grade calcium nitrate, not the fertilizer. Put the coupons in a clear plastic dessicator cabinet. Wax the sides of a plastic pan that will fit in the bottom of the dessicator cabinet. This keeps the calcium nitrate slush from crystallizing on the sides of the pan and going everywhere. For better control, get one of those tiny "muffin fans" used to cool the CPU of computers. Hook it to a big battery or a 12-volt power source. Tape it inside the cabinet to blow air across the surface of the nitrate slush pan. This brings the cabinet to 50% RH faster. Tape one of those cheap small electronic RH meters to the back wall. As the temperature in the cabinet falls, the RH will rise: at 18.5 °C., RH=56%. At 24.5 °C., RH= 51%. If the slush dries out, squirt a little more water.
Good luck,
Phil Possonaerospace - Phoenix, Arizona
2002
Effect of humidity on Taber abrasion test of hard anodize
Q. Has anybody done a study on the effect of humidity on Taber Abrasion test?
Would you share your results.
plating shop. - Gardena, California
2007
Treatment &
Finishing of
Aluminium and
Its Alloys"
by Wernick, Pinner
& Sheasby
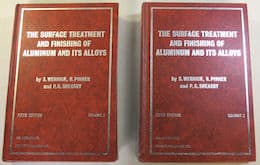
(note: this book is two volumes)
on eBay or
AbeBooks
or Amazon
(affil links)
A. Testing by abrasive jet after atmospheric exposures of up to 6 months shows a decrease of abrasion resistance of unsealed hard anodize with time. The decrease was attributed to humidity, and was similar to the decrease resulting from hydrothermal sealing. The decrease was much greater for anodized 2024 than 6061.
-- pages 793-795 in The Surface Finishing and Treatment of Aluminum and its Alloys
[adv: suggestions on
AbeBooks,
Amazon &
eBay affil links], 6th Edn.
Also, humidity absorbed by samples during Taber testing affects the accuracy of the weight loss measurement.
-- page 1006, ibid.
- Goleta, California

Rest in peace, Ken. Thank you for your hard work which the finishing world, and we at finishing.com, continue to benefit from.
A. "Has anyone done a study...?"
I've pondered the question myself especially in wake of a recent Nadcap audit and finding. I argued until blue in the face that the "unless otherwise specified" humidity and temperature conditions noted in the relevant ASTM method were for testing paints and other soft coatings. I countered that since the various mil specs never referenced such testing conditions, these implicitly implied room temperature conditions. They didn't buy it - I was found guilty. I now have this monstrosity of a temperature / humidity controlled environmental chamber to run the test in. I still claim that it's irrelevant! If enough voices were raised, perhaps we could get ASTM to listen and get some language applicable to testing anodize added.
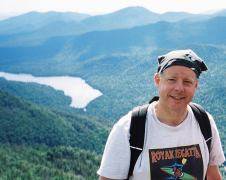
Milt Stevenson, Jr.
Syracuse, New York
A. From page 1006 referenced above:
"Once again humidity variations can play a significant part, as shown by Lerner (see also Chapter 6). Thomas also points out that a freshly exposed anodic film (particularly when unsealed) takes up water vapour readily, and this increase in weight can largely offset the decrease in weight occurring during abrasion. Thus, whilst the Taber test is clearly a useful one, the problems of reproducibility have so far made it impossible to produce an international standard on Taber testing of anodic coatings."
M. Lerner, Plating and Surface Finishing, vol. 66, no. 12, pages 40-43 (1979).
R. W. Thomas, Trans. Institute Metal Finishing, vol. 59, pages 97-103 (1981).
Some good citizen with access to the 2 referenced studies can perhaps post helpful summaries.
Perhaps, 24 hrs. at the humidity and temperature of the Taber Abraser site would sufficiently stabilize the abrasion resistance and weight.
- Goleta, California

Rest in peace, Ken. Thank you for your hard work which the finishing world, and we at finishing.com, continue to benefit from.
Q. Good day.
This is regarding Taber testing. My solution is at 389 g/l total and 370 g/l free sulfuric, aluminum 3 g/l, oxalic 14 g/l., temp. 30-40 °F as per spec., ramp time 5-15 mins depending on the alloy. This is the spec for which I am working towards.
Unfortunately, ASTM D4060 has been selected to supersede FED-STD-141 Method 6192 from MIL-A-8625 / MIL-PRF-8625
[⇦ this spec on DLA]. D4060 does suggest refacing every 500 cycles BUT the specification is used for ORGANIC coating, i.e., paint, urethane, varnish, powder coat, etc.
As per ASTM D4060: "9.1.2 A load of 1000 g (per wheel) should be used, unless 'otherwise agreed upon by the interested parties' ". 9.1.5 Resurface the wheels by running them 50 cycles against the resurfacing medium.
Warning -- Do not brush or touch the surface of the wheels after they are refaced.
NOTE 7 -- The wheels shall be resurfaced in this manner before testing each specimen and after every >500< cycles.
10.2 Unless otherwise agreed upon between the interested parties, condition the coated panel for at least 24 h at 23 ± 2 °C(73.4 ± 3.6 °F) and 50 ± 5 % relative humidity. Conduct the test in the same environment or immediately on removal therefrom."
At 10,000 cycles you need to reface 20 times, 7 minutes apart. My previous spec called for refacing every 10,000 cycles. With a 500 gram load I am getting 9-12 mgs weight loss. With a 1000 gram load, the results are not favourable. This concerns the "mutual agreement" regarding weights.
I place the panels in a desiccator 24 hrs. prior to both initial and final weighing.
My question is, how are you all performing this test, and what are your results? I am hoping to see similar numbers, to rule out a process problem. Can some thing be done to modify the specification?
Looking forward to all replies.
Regards,
Lab Tech. - Whitby, Ontario, Canada
December 18, 2014
Q. Good day all.
I do have some clarification upon receiving AMS2469, finally!
Briefly, the desiccator may be used in lieu of conditioning (prior to initial and final weighing) as stated in ASTM D4060 and resurfacing of the wheels shall be done prior to each test and at least once every 10,000 cycles.
Now all I am required to do is to determine which is the predominant alloy we process and which one I would choose to use for the testing.
I would very much like to see responses regarding weight loss/alloy/bath concentrations.
Regards,
[returning]
- Whitby, Ontario, Canada
A. Hi Eric,
Before we shut our internal plating shop and off-loaded it to our supply base we used to carry out the Taber Test, resurfacing every 500 cycles. It added a huge amount of time to the testing.
The figures for weight loss did increase, but not significantly. When doing a straight 10,000 cycles we used to have a weight loss around 2-3 mg, by resurfacing it increased to 6-8mg, with no breakthrough of the anodic film.
9-12 mg doesn't seem unreasonable, but the specification requirements are for 1.5 mg per 1000 cycles (MIL-A-8625
[⇦ this spec on DLA]) for low copper alloys (less than 2%), or 15 mg per 10,000 cycles and 2.5mg per 1000 cycles for copper containing alloys above 2%, or 25 mg per 10,000 cycles. If you are not meeting these numbers then I would be worried that there is a process issue.
Aerospace - Yeovil, Somerset, UK
Q. Good day Terry.
Thank you for the info. At what ASF are you operating?
The AMS2469 Rev J spec revised 2014 02 states a maximum wear index of 3.5 mgs/1000 cycles for al alloys having a copper content of 2% or higher.
I have a weight loss on 2024 alloy of 12-16 mgs. and am resurfacing every 10000 cycles.
I am experiencing some "burning" on the coating weight panels (3x3), but none on the 4x4 (as they are thicker) which I think is giving me a softer coating, as the oxide layer is probably dissolving.This is at 20-24 ASF.
I need to vigorously increase the air agitation to solve this, and make a double line sparger, positioning closer to the cathodes.
I am working to achieve 36 ASF for a Bombardier spec., and for this reason, I will try 7075 alloy.
Regards,
[returning]
- Whitby, Ontario, Canada
A. Hi Eric,
Dependent on alloy we could be operating anything from 25 ASF to 40 ASF. We did use a sulfuric acid concentration of 400 g/l nominal, running at -5 °C to -10 °C. Sparged air was also used and that had to be pretty darned vigorous! We had no special additives in the tank, so we tried to run as cold as possible, preferring to be nearer -10 °C than -5 °C.
Another thing we found that had a much greater effect on the panels than we expected was the conditioning. The 24 hour stabilization we found was critical to passing the test consistently.
Aerospace - Yeovil, Somerset, UK
Q, A, or Comment on THIS thread -or- Start a NEW Thread