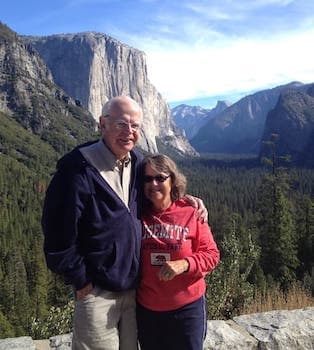
Curated with aloha by
Ted Mooney, P.E. RET
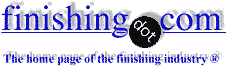
The authoritative public forum
for Metal Finishing 1989-2025
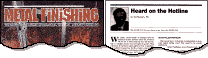
-----
Mechanical Zinc/Tin plating effluent recovery
I am assessing effluent/ materials recovery for a mechanical barrel plating process. The process operates several barrel lines coating fasteners with zinc and tin before passing to a chrome plating line using dichromate.
The plating process consists of: loading fasteners, loading a glass bead media, surface conditioning using a proprietary product containing H2SO4, adding antifoam, adding copper sulphate ⇦ this on eBay or Amazon [affil links] solution to carry out a "copper flash", adding stannous chloride, adding leveler, then adding powdered zinc and tin in 5-6 steps all whilst the barrel turns causing the media and parts to tumble. The barrel is then filled with water and then inclined to drain the water out (but not the parts and media) up to 5 times until the pH rises to above 4.5 at which point the parts are discharged. The rinse waters contain a lot of zinc and tin (up to 9000 mg/l) including particulate zinc and tin as well as dissolved zinc and tin.
We wish to recover both the solid metal by filtration and dissolved metal by reverse osmosis and return this concentrate back to the barrel for the next batch.
Is anyone aware of an effluent recovery system on this type of process and if so what form did it take?. What are the limitations in a)treating the rinse water using R.O and b) returning the concentrate back to the barrel? It is proposed to introduce the R.O concentrate after the copper flash step.
Any comments would be appreciated
Matthew Harrison- Melbourne, Victoria, Australia
I think that your desire to recycle this waste stream is commendable, but you are facing some nearly insurmountable problems.
It is likely that the first and the second rinses contain too many suspended solids and too high a TDS concentration to send to a recycling system. It may be possible to capture and reuse the first rinse as make-up water to the next batch. It may also be possible to recycle rinses 3,4, and 5, but it may not be worth the effort or expense. Most people would batch treat all of the wastes and hope to find a reclaimer who would accept the sludge that is produced.
Lyle Kirmanconsultant - Cleveland Heights, Ohio
Q, A, or Comment on THIS thread -or- Start a NEW Thread