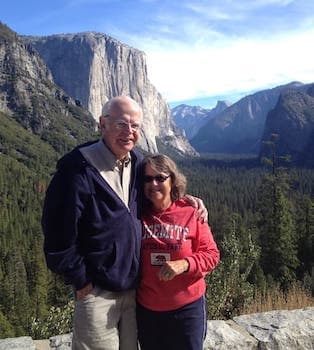
Curated with aloha by
Ted Mooney, P.E. RET
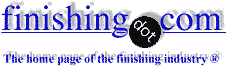
The authoritative public forum
for Metal Finishing 1989-2025
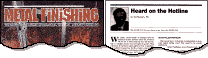
-----
Testing for Passivation
Q. I am product development engineer and we have a bracket, which is made out 316 SS. The bracket is passivated during our manufacturing process to give it a stronger corrosion layer. Since the material is already in a passivated state before we passivate it. I need to know if there is a test, which can detect the difference between the two passivated states of the part. I have already tried a galvanic passivation tester and it can only give me a range, which informs me if the part is passivated or not. I need a test, which is more sensitive and can distinguish between a weak and stronger passivated state.
Eduardo Acuoa- Glendora, California
A. Are you having field failures? As far as I know, passivation is like being pregnant - you are, or you aren't. I've never heard of having degrees of passivation. Many parts are tested using a copper sulphate ⇦ this on eBay or Amazon [affil links] test that is a pass/fail type test. If your current test shows passive, I would be inclined to believe that the parts are processed correctly.
Dan Brewerchemical process supplier - Gurnee, Illinois
A. Eduardo:
316ss is a very corrosion resistant material. However, the degree of corrosion resistance is dependent upon the degree of passivation you give it (how iron free is the surface). You can get a considerable increase in the corrosion resistance by passivation, obtaining a very high chromium content on the surface to give you an excellent chrome oxide layer. We have not yet found a galvanic tester which gives accurate results of the degree of passivation. If you find one, let us all know. You can run expensive ESCA & AES tests that will give you good comparisons of the degree of passivation of the surface. These tests are normally run by the companies in the semiconductor and orthopedic industries. There are a lot of tests which are pass/fail type tests, but these will not give you a relative passivation comparison. You could try to run salt spray to failure to get some comparison (ASTM B117 run to failure instead of 2 hours).
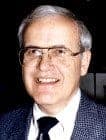

Lee Kremer
Stellar Solutions, Inc.

McHenry, Illinois
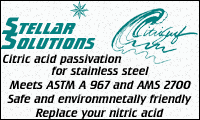
Passivity meter: We use a galvanic type meter made by HMV Corrlab bv in The Netherlands. This company was recently taken over by CorrOcean from Norway. We have tested the reliability of these meters using three different meters and got the same readings.
We have compared air passivated and chemically passivated test coupons and seen the benefits of chemical passivation. The meter comes with a simple manual. Our company has no link with the supplier of the meter, other than as a customer. We think it's a good and quick check of passivity. Sometimes, our customers question the meter's ability to test for SS passivity. It's easy to scratch passive SS and test the scratched surface. The result will be that the steel is active at that place. Repassivation and retesting shows that passivity has been restored.
What is really needed is an clear, unambiguous and internationally accepted standard for testing passivity of SS. Current yes/no methods such as the palladium chloride test are,in our opinion, inconclusive and do not satisfy clients' needs, especially in the pharmaceutical sector. I'd like to point out that to passivate the SS surface an oxidizing agent is required. Nitric acid can both remove free iron and oxidize (passivate) the SS surface. It will not remove oxides (as an example, if a non-pickled SS weld seam (i.e. with heavy oxidation in the heat affected zone) is immersed in nitric acid at, say 20%w/v for any length of time, the oxide layer will remain. Nitric/HF mixes remove both free iron and oxides,as well as some of the steel's surface components. After this the steel is active, and can be passivated for example by Nitric acid or hydrogen peroxide. Complexed citric processes, unless incorporating an oxidizing passivation step, do not themselves passivate (i.e. oxidize) the steel, but rely on oxygen from the air to do the job. citric acid is not an oxidizing agent.
Trevor Tipton- Singapore, Singapore
Trevor & all:
Thank you for this information. I will follow up on this equipment, as I have tested other passivity meters and found them totally unreliable. I am looking for a device that will quantitatively measure the degree of passivity without expensive surface analysis.
The OLD school of thought was that an oxidizing acid was necessary to get good passivation. This has been proven wrong many times, by many companies. Passivation is a process of first removing as much of the iron (and other materials) from the surface of stainless steel as possible. This creates the chromium rich layer that then oxidizes very readily in air to form the passive layer.
Proprietary citric acid formulations have shown the ability to get HIGHER chrome oxide ratios on the surface, and better resistance to corrosion than nitric passivated surfaces. This, in the end, is the true measure of how passive the surface is-- better corrosion resistance. That is why we passivate.
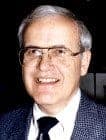

Lee Kremer
Stellar Solutions, Inc.

McHenry, Illinois
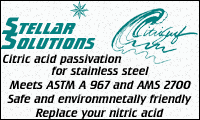
The main indication of passivation (transition of metal from active to passive state) is a sharp decrease in speed of metal dissolving, and visible shift of metal potential towards positive. It is a common assumption that passivity is determined by existence of thin oxide (hydroxide) film, which separates metal from the environment. The thicker the film - the higher the passivation, and the corrosion resistance. The thickness of the passive film can be estimated in connection of E - potential from t - time during the current on anode. Electrolyte in such experiments must not dissolve passive film. The sooner we reach potential of oxygen dissolving, the thicker is the film. We have conducted such experiments while developing new environmentally friendly non-electrical method of passivation for food industry. As the results we have obtained passivating film thicker than the film produced by traditional methods.
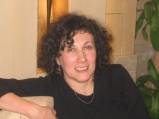
Anna Berkovich
Russamer Lab

Pittsburgh, Pennsylvania
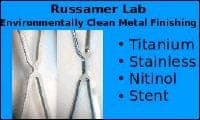
Your customer seems to want the very best in passivating and you have received some accurate and valuable advice in the replies you have received. The ultimate in passivation of stainless steels comes from electropolishing. I have done salt spray testing running into weeks with no degradation of the surface on electropolished parts. The quality of the passive surface has been confirmed by auger electron spectroscopy. Electropolishing is also called bright passivating.
John Holroyd- Elkhorn, Wisconsin
Although recently canceled, the most commonly referenced industry specifications regarding passivation are Federal Specification
QQ-P-35C (canceled) [link is to free spec at Defense Logistics Agency, dla.mil]C, which is now superseded by ASTM A967 andASTM A380
. All are well-written, well-defined documents that provide guidance on the entire process, from manufacturing to final testing requirements. If you are not sure what you need, they can be referenced in full or selectively. The testing requirements can be used or waived, depending on the individual situation.
One of the most commonly specified verification tests is the copper sulphate test. Passivated parts are immersed in a copper sulphate solution for six min, rinsed and visually examined. Any copper (pink) color indicates the presence of free iron and the test is considered unacceptable.
Other validation tests include a two-hr salt spray or 24-hr high-humidity test. These tests are performed by placing passivated parts in a highly controlled chamber that creates an accelerated corrosive environment. After subjecting the test pieces to the corrosive atmosphere for the prescribed exposure periods, the parts are removed and evaluated. Although results can be somewhat subjective,ASTM B117 is an excellent reference in determining acceptability. It is important to note that each of the test methods mentioned have different advantages and limitations. Care should be taken to select the appropriate test methods based on alloy type and end-use environment.
- Buffalo Grove, Illinois, USA
The Passivation Tester by Koslow Scientific Co. has been found to be effective at finding surface free iron on stainless steel surfaces. It was developed with the Federal Spec QQ-P-35C (canceled) [link is to free spec at Defense Logistics Agency, dla.mil]C document in mind. The QQP 35C mentions that testers are available for determining the passive state of stainless parts. The major advantage for using a tester over the ferroxyl and copper sulphate is, the elimination of hazardous chemicals and the elimination of mixing of chemicals.
Wolf KoslowKoslow Scientific Company

Englewood, New Jersey
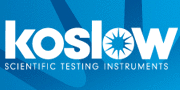
June 16, 2010
Need passivated stainless fasteners to survive 150 hour salt spray test
July 11, 2016Q. HI ALL !
I DO TWO TYPES OF PASSIVISATION ON THREADED FASTENERS
1) NITRIC PASSIVISATION - 30 MIN- 60 °C
2) CITRIC PASSIVISATION - 30 MIN- 60 °C
BOTH SAMPLES FAIL IN SALT SPRAY TEST 5% NaCl
BUT BOTH SAMPLE RED RUST ON THREAD WITHIN 48 HOURS.
SO MY QUESTION IS HOW TO IMPROVE AT LEAST 150 HOURS IN SST TEST?
ss fasteners manufacturer - rajkot, gujrat, India
A. Hi Ria. Who has determined that the stainless fasteners should be expected survive a 150-hour salt spray test? 2 hours of salt or 48 hours of humidity seems more reasonable for lower grades of stainless. We'd like to know what kind of stainless steel the fasteners are made of, because some stainless alloys are much more corrosion resistant than others. I believe that electropolishing the parts will increase their salt spray resistance more than passivation, and that 316SS will outlast lesser grades. Good luck.
Another possible problem with the requirement of 150 hours salt spray is "What / how are you defining failure?". Salt spray testing specifications like ASTM B117 describe the mechanics of the test equipment, not what constitutes failure. Many plating specifications define what constitutes failure for the specified finish, but if you ask for 150 hours without quoting a spec that defines failure, it can be rather vague.
Regards,
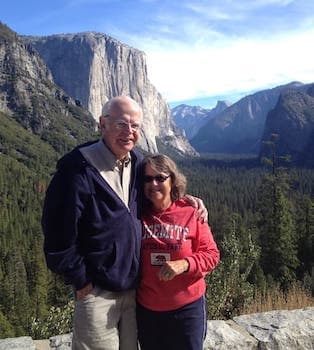
Ted Mooney, P.E. RET
Striving to live Aloha
finishing.com - Pine Beach, New Jersey
July 2016
Q, A, or Comment on THIS thread -or- Start a NEW Thread