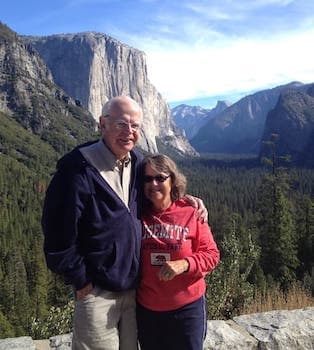
Curated with aloha by
Ted Mooney, P.E. RET
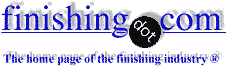
The authoritative public forum
for Metal Finishing 1989-2025
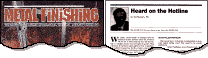
-----
Passivation / Electropolish -- Proper Sequence?

Q. Reviewing the Process Routers for several similar Stainless Steel parts. Both are machined, then heat treated. One calls for "Passivation followed by Electropolish". Several other reverse the sequence, calling for "Electropolish followed by Passivation." What is the rationale for determining proper sequence. If Electropolish is the secondary process is the result a part without a Passive Protective Layer. IF electropolish provides a Passive surface what is the need for the preliminary Passivation process?
Lyndon T [last name deleted for privacy by Editor]- Mishawaka, Indiana
2001
A. Hi Lyndon. Compliance with specs is probably the only reason to both passivate and electropolish, since electropolishing is believed to offer the best known passivation.
silly :-) So I'd do the best finish as the final, and the 'just to comply with the spec' process first :-)
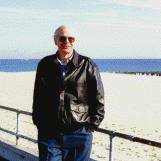
Ted Mooney, P.E.
Striving to live Aloha
finishing.com - Pine Beach, New Jersey
2001
A. Hello Lyndon!
I can't see the point of passivation before electropolishing. Regarding the passivating effect of electropolishing, take a look at specification ASTM B912, on "Passivation of Stainless Steels Using Electropolishing". It notes that a film from electropolishing should be removed before you run your passivation verification test. If you do a post electropolish film removal dip, you may be fine stopping there.
Good luck!

Lee Gearhart
metallurgist - E. Aurora, New York
2001
A. Lyndon:
There is no logic to passivation before electropolishing, since you would remove the passive layer in the EP process. Electropolishing normally provides a good corrosion resistant surface. However, if you want the BEST corrosion resistance and the highest chrome oxide layer on the surface, you should passivate after electropolishing. We have data showing considerable improvement in chrome oxide content on the surface using this process with our citric acid formulations.
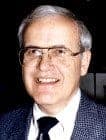

Lee Kremer
Stellar Solutions, Inc.

McHenry, Illinois
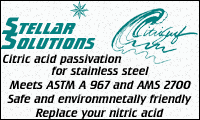
2001
A. The reason for passivating either before or after electro-polishing is that the spec. says so. There is no engineering reason for this. Electro-polishing will provide the best passivation possible.
The film left by electropolishing is the passive film and this should NOT be removed.
Proof of the passivating effects of the electro-polish have been confirmed by ESCA and plasma stripping of the surface.
This mistake is not uncommon. I receive parts to be passivated and pickled or passivated and electro-polished every week. Usually a brief discussion with the engineer responsible for the spec clears things up and the expectations of the customer are satisfied without going through a dual step process.
John Holroyd- Elkhorn, Wisconsin
2002
Q. We had a service fellow climb into our tank to prep for a spot electropolish. Would passivation be warranted for the rest of the vessel which did not benefit from the localized electropolishing which took place only on the bottom 5% of the vessel?
Eric Bishop- Chaska, Minnesota, USA
July 7, 2008
Q. We get lots of white marks after electropolish and have been told that passivation reduces this problem. Has anyone else found this?
Mike ParsonsOncam - London, UK
August 14, 2017
A. Hi Mike. Have you done any examination of those "white marks" to see what they might be? Might they be areas of etching caused by problems like insufficient current density or excess water in the solution?
Regards,
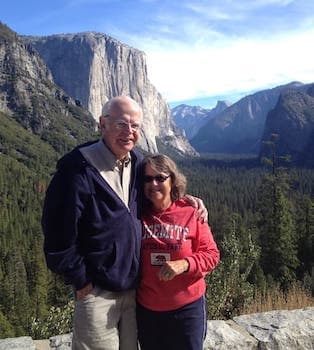
Ted Mooney, P.E. RET
Striving to live Aloha
finishing.com - Pine Beach, New Jersey
August 2017
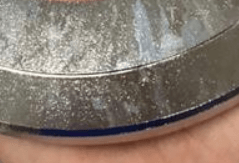
Q. Not really Ted, they are being done remotely. I will add a photo for reference.
Mike Parsons [returning]Oncam - London, UK
August 15, 2017
A. Hi Mike. I think I'd be amazed if passivation fixed that problem. To me, that surface doesn't look even vaguely like an electropolished stainless steel surface should. Please tell us what the part is, what grade and form of stainless steel it's made from, and why it is supposed to be electropolished.
And if you could put a coin or pencil or tape measure or something into the picture for a sense of scale and resolution, it would probably help because I'm not sure whether this is a 'visual' scale photo of a rough sparkly surface, or an extreme closeup where you are concerned with the ghost-like drippy areas. Thanks.
Regards,
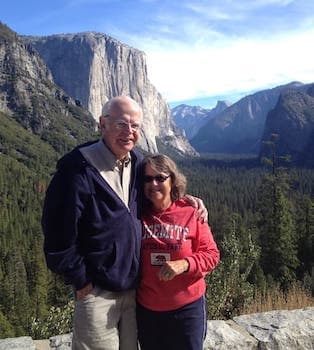
Ted Mooney, P.E. RET
Striving to live Aloha
finishing.com - Pine Beach, New Jersey
August 2017
Q. Hi Ted, the diameter of the part you can see is 160 mm (~6").
The material 316L, investment casting.
The parts are pretty consistently stained like this.
Best regards,
Mike
Oncam - London, UK
October 3, 2017
A. Mike,
Any other surface treatment before electropolishing? Castings don't have a great surface to begin with, it's usually good to sandblast/beadblast, or maybe for parts your size something more like tumbling.
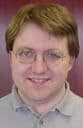
Ray Kremer
Stellar Solutions, Inc.

McHenry, Illinois
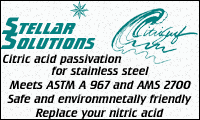
October 4, 2017
Q, A, or Comment on THIS thread -or- Start a NEW Thread