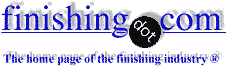
-----
Does Teflon Coating Improve Corrosion Resistance of Anodized Aluminum
Q. We have a customer that has experienced better corrosion resistance on Teflon coated, anodized aluminum than with non-teflon coated. Can Teflon coating be applied to Type II anodize or only Type III? Does the teflon coating actually ADD protection? Is there a salt spray rating on teflon coating as compared to plain anodize?
David Lair- Phoenix, Arizona
A. It does impart added protection if you have observed this. Why don't you get some standard aluminum panels, and do a small experiment yourself?
There doesn't seem to be any reason why an additional coating on a surface wouldn't improve protection, but you need to define the corrosive atmosphere and test it. It may improve the protection in one condition and not in another.


Tom Pullizzi
Falls Township, Pennsylvania
A. Teflon coating over anodized surfaces is fairly common, however, the anodize must be left unsealed in order for the Teflon to adhere to the surface. As far as corrosion protection, you will basically have the corrosion resistance of the Teflon (PTFE, PFA, FEP, ETFE) at the surface. Teflon (fluoropolymer) materials are very chemically inert and hold up better to many chemistries than anodize, but they are softer (50 - 70 shore D) and have maximum operating temperatures of 300 °F (ETFE), 400 °F(FEP), or 500 °F (PFA, PTFE).
Jim Sloancoatings - West Chester, Pennsylvania, USA
August 19, 2010
Q. Hello,
Does anyone have an explanation for corrosion forming on an aluminum ring which has been anodized and finished with a PTFE coating?
The corrosion spots form all over the ring -- which should be a sealed and protected surface due to the anodizing and PTFE finish?
- The Netherlands
December 4, 2013
December 2013
A. Hello S. May be assume that you are speaking of a finger ring (jewelry), and that you are a consumer asking about a single ring, rather than a process engineer encountering a production problem?
How long have you worn this ring? It sounds to me that the thickness of a Teflon coating on jewelry must be minimal. I might guess that the remaining Teflon is now porous rather than encapsulating the ring, and I don't think anodized aluminum makes for very robust jewelry. Perhaps okay for rarely worn items like bracelets or necklaces, but not for the prolonged wearing, and hard wear, of rings. Just my opinion, for which I'll probably be lambasted by suppliers of such :-)
If you can flesh out your situation, a more detailed response may be possible. Thanks.
Regards,
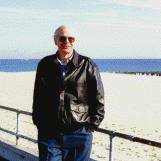
Ted Mooney, P.E.
Striving to live Aloha
finishing.com - Pine Beach, New Jersey
Q. Hello Ted,
No, I am not a consumer. It's a ring on a helicopter drive shaft. This ring is on the shaft to protect it from a damper that is there to dampen the translation vibrations on the shaft while spinning up to full RPM.
There are 2 rings on the drive shaft one as a spare in case the other one gets worn so the shaft can be turned.
Now both rings on some of our helicopters are heavily corroded, which results in rejection of the shaft. The manufacturer of the shaft can't give us a satisfying answer on this problem.
Regards Stefan
- The Netherlands
December 12, 2013
December 12, 2013
A. Stefan,
One idea is to discover if the current process has .05 mm minimum thickness for the main coating and .005 mm minimum thickness for the Teflon. The anodic coating thickness can be increased to .2 mm as desired, which would probably provide more protection. The Teflon coating thickness can be increased and probably should be Type III per MIL-A-63576 Rev. A such that a thermosetting resin containing PTFE is used and cured. If it is not a heavy duty part, it could be that more surface prep prior to coating is needed due to pits or you may need to go with a denser grain structure. If used in a salty environment, the current coating method might not be adequate and a completely different process may be required although you should be able to get a long life (1000+ hrs salt spray) from a proper coating per MIL-A-63576 Rev. A Type III. I assume you don't have cold rolled steel or another metal that reacts with Aluminum adjacent. Certain grades of Al work better for this coating type. Examples: 2024, 6061, 7075. Also, if the assembly is coated and not the individual rings, that wouldn't be recommended. You should see a nice water break-free surface prior to coating to confirm everything is clean. Specification 63576 has a lot more information if interested.
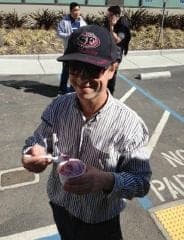
Blake Kneedler
Feather Hollow Eng. - Stockton, California
Q, A, or Comment on THIS thread -or- Start a NEW Thread