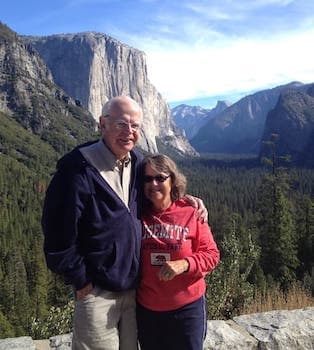
Curated with aloha by
Ted Mooney, P.E. RET
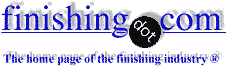
The authoritative public forum
for Metal Finishing 1989-2025
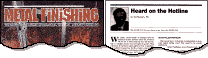
-----
Yellow Zinc Plating or Clear White Zinc Plating
adv.
Q. I frequently use hex nuts in arts and crafts projects such as paracord bracelets. I recently bought some grade 8 1/2" steel hex nuts plated with what looks like yellow zinc.
Wanted to make sure that this finish was nontoxic and safe to handle, especially with continued skin-on-skin exposure.
Martin Zzzzzzzzz- South Carolina
November 25, 2022
Tip: This forum was established to build camaraderie among enthusiasts through sharing of tips, opinions, pics & personalities.
The curator & some of the readers who publicly share their info are unlikely to engage with posters who don't.
A. Hi. Sorry, no can do. Zinc plating is inappropriate at best for jewelry and skin contact. If you find a carton of them which might end up in California, you'll probably see a Prop 65 Warning sheet in the box.
Luck & Regards,
Ted Mooney, P.E. RET
Striving to live Aloha
finishing.com - Pine Beach, New Jersey
⇩ Related postings, oldest first ⇩
Q. Hi,
The question is about the choice of Yellow Zinc Plating or Clear White Zinc plating. Zinc Chromate in the powder form is a known carcinogen. Is Clear zinc plating any better?
Madan Rangabasyam- Brampton, ON, Canada
2001
A. Hi, Madan.
Probably. Traditionally yellow hexavalent chromate was used for the optimum in corrosion resistance, while clear or blue hexavalent chromate was used for a brighter appearance where less corrosion resistance was acceptable, and clear or blue trivalent chromate was used where very little corrosion resistance was needed. So, just because the coating is clear or blue is not a guarantee that it is free of hexavalent chrome! So remember to ask your plater (or your supplier if you are the plater) whether the clear chromate is hex-free and RoHS compatible.
Ten years ago there was little trivalent chromate conversion coating. But changing standards are dictating that virtually all chromate coatings will be hex-free rather soon.
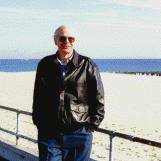
Ted Mooney, P.E.
Striving to live Aloha
finishing.com - Pine Beach, New Jersey
Q. Since this thread is about zinc plating, would like to post a few questions here.
I strongly agree that yellow zinc is the most corrosion resistant (I have seen extensive use of it in armored vehicle parts) compared to blue or clear zinc.
But when we talk about clear zinc, is it the same as white zinc we are referring to?
For blue, clear/ white and yellow zinc, are there any preference of its use in regions of the world (e.g., Europe, US or Asia). this sound silly doesn't it?
... and what is the difference between zinc plating and chrome passivate?
Very inexperienced at this, need some answers desperately!
thanks in advance.
Pho Boon Kee- Singapore
2004
A. Hi, Pho. Your last question first, so we are all on the same wavelength. Steel parts are never just "chrome passivated"; that process and that term implies that the parts were first zinc plated. Similarly, zinc plating without a subsequent chromate conversion coating is very rare -- almost unheard of. So, when you see terms like "yellow zinc" what is really meant is zinc plating followed by chromate conversion coating of a yellow color.
I believe that the answer is that 'white zinc' is not a generally accepted name, at least in the USA, but that the inquirer is probably referring to a clear chromate coating on zinc plating.
My expectation is that hexavalent chromates will eventually be banned throughout the world because of their toxicity and possible carcinogenicity. They are already forbidden on automobiles in Europe, which has meant that all car manufacturers throughout the world stopped their use; you may as well do the same on your products.
Because hexavalent chromium is inherently yellow, the yellow chromates have been in the past associated with high concentrations of hexavalent chromate. The clear and blue chromates were lower in hexavalent chromate and less corrosion resistant. The newer chromates are free of hexavalent chromate, and the yellow color is usually just dye. They are not as corrosion resistant or forgiving as hexavalent chromates, but with care and with topcoats of wax, lacquer, zirconium, silanes, etc., they can be okay.
Some people call the chromate conversion coating that is applied on top of zinc plating 'chrome passivate'.
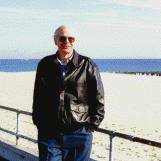
Ted Mooney, P.E.
Striving to live Aloha
finishing.com - Pine Beach, New Jersey
Q. Has yellow zinc, or perma-gold, been outlawed in Europe for finishing on all products. I'm wondering if this finish is available on construction materials like Unistruts.
Thanks
- seattle, Washington
January 13, 2010
A. It's a difficult question to answer, Jacques, because there are RoHS standards, and WEEE standards, and soon REACH standards. Some apply to some product lines but not all, etc.
But here's what might be an answer: Specify that the zinc and chromate finish must be RoHS compatible, and you'll be okay. Most plating shops have switched to RoHS compatible trivalent chromates anyway. You'd probably have a hard time getting a shop to do non-RoHS hexavalent chromating. Perma-gold sounds like a trademark that I'm not familiar with, but if it has been around a while, it's probably for hexavalent yellow chromate.
Regards,
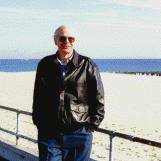
Ted Mooney, P.E.
Striving to live Aloha
finishing.com - Pine Beach, New Jersey
Q. What is the salt spray hour figure for standard trivalent chromates compared to the hex chromates of the past.
Also, I am fastener dist. and already running into the REACH requirements.
Thanks,
Jim
- Oakwood Village, Ohio, United States
April 13, 2010
A. Hi, Jim. The trivalent chromates today are marketed as 'replacement' for hexavalent chromates and offer, in theory, the same number of hours of salt spray resistance before white rust -- which was 96 hours for yellow chromates. Naturally, suppliers may claim theirs will last longer, while some plating shops claim that the replacement trivalent chromates don't really quite match the old hex chromates, and other shops say they're better :-)
Regards,
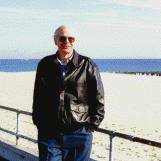
Ted Mooney, P.E.
Striving to live Aloha
finishing.com - Pine Beach, New Jersey
Q. DEAR SIR,
HOW TO DO ZINC YELLOW PLATING? What are the chemicals used in it, and what is the ratio is used for zinc yellow plating, and how much the cost, and how much area do we require to do the same?
thanking you,
yours faithfully,
EMPLOYEE - Bangalore, India
October 13, 2011
A. Hi, Satha.
"Yellow zinc plating" means zinc plating followed by a yellow chromate conversion coating. The process may be done in plating barrels or by racking the individual parts, and usually involves cleaning, activating, zinc plating, chromate conversion coating, and drying -- with good rinsing between each stage. Each of these steps requires process control. The cost and the area required can vary from very little for one part to a million dollars and the size of a basketball court for a fairly good sized line; and there is no real upper limit to cost and size.
If you have parts to be zinc plated you should contact a plating shop to outsource the work, or contact a consultant or supplier to consider installing a plating plant. The plating can be cyanide zinc, alkaline non-cyanide, or several 'flavors' of acid zinc plating -- the topic fills 300-page textbooks, so we are happy offer this introduction, but we can't explain it in full detail here. Good luck.
Regards,
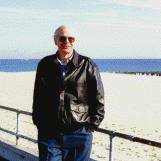
Ted Mooney, P.E.
Striving to live Aloha
finishing.com - Pine Beach, New Jersey
Q. Hello.
The Zinc yellow plating, according to ASTM B633 type II, has a corrosion resistance of 96 hours (Salt spray). Regarding this, I would like to know, what other finishing type that has the same corrosion resistance, but with Chrome VI-free?
Thank you in advance!
- Sao Paulo, SP, Brasil
October 26, 2011
Hi, Rafael.
Modern trivalent chromates were developed for the exact purpose of matching the corrosion resistance of hexavalent chromate, but they are highly engineered proprietary processes, and some may require a silane, zirconium, or other topcoat to reach that level. Good luck.
Regards,
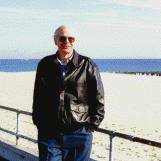
Ted Mooney, P.E.
Striving to live Aloha
finishing.com - Pine Beach, New Jersey
Q. Hello folks,
How are Retailers handling the change of Hexavalent finishes to Trivalent Finishes? Most Retailers (NAPA, Home Depot, TSC, Pep Boys) carry bins in their retail store and customers can distinguish between Grade 5 and Grade 8, by the color of the product. Since Grade 8 becomes Hex-free, is loses its "yellow" coloration. Will Manufacturers and Distributors be moving to another color to call out the Grades?
- Quakertown, Pennsylvania, USA
May 8, 2012
A. Grade 5 and grade 8 are specifically marked on the head. Three hash marks for Gr5 and six for Gr8. If hex chromate is banned, and color desired, there are dyes available in any color.
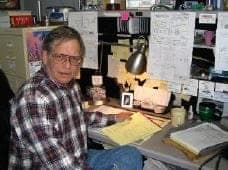
Jeffrey Holmes, CEF
Spartanburg, South Carolina
Q. I have a problem on my painting line, our process after plating White Zinc Chromate, in painting black Gloss.
Problems: bubble spot or popping after painting are appeared.
To know "why" and the Defects after painting and to find out solution of popping problem we try to paint 25 pcs without Zinc Chromate before, the result is all 25 pcs are OK no defects at all, so we assume the cause is zinc chromate is not compatible to my painting.
How is your suggestion, to solve my problem..
Thanks before.
- Serpong, Banten, Indonesia
September 14, 2015
A. Hi Aris. There was a mad race to make trivalent chromates equal in corrosion resistance to the hexavalent in salt spray testing, with a focus on nothing else. So several different approaches were commercialized; the various approaches are proprietary and involve thin vs. thick films, topcoats vs. no topcoats, one type of topcoat vs. another, etc.
The result is that these proprietary trivalent chromate processes offer differing adhesion, differing contact resistance, differing resistance to subsequent post treatment chemicals, differing compatibility with paints, etc. It may be that another plating shop can offer you a zinc plating and chromate conversion coating process that is compatible with your painting. Skipping the chromate conversion coating process is probably not a good idea. Good luck.
Regards,
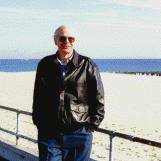
Ted Mooney, P.E.
Striving to live Aloha
finishing.com - Pine Beach, New Jersey
Q. What is the functional difference between clear zinc and yellow zinc? If a drawing requirement calls for yellow zinc is it always an obvious yellow in color or can it appear clear sometimes? Does paint stick better to yellow zinc than clear zinc?
Gary Workman- maple grove Minnesota
December 29, 2015
A. Hi Gary. Until around the year 2000 there was a substantial difference between clear and yellow chromates. The yellow color came from hexavalent chrome, and the salt spray resistance to white rust was 96 hours vs. only 12 hours for the clear chromates with their significantly lower hexavalent chrome content. Too dark yellow meant too thick, so the chromate film could shear.
But today most chromates are trivalent, and most of the trivalent chromates are clear. When yellow is required, those chromates are simply dyed. It's a complex situation, though, because some of the proprietary thick film trivalent chromates are yellow.
Since it is usually only a matter of dye, the adhesion of the paint doesn't depend on the color. But back to the complications: these proprietary trivalent chromates differ from each other and it is clearly possible that the adhesion of paint to one trivalent system may be better than the adhesion to another. It makes it hard on the end user to spec what he needs, but it's probably best to include some sort of paint adhesion requirement in your specification if you intend to paint them.
Regards,
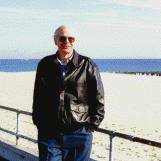
Ted Mooney, P.E.
Striving to live Aloha
finishing.com - Pine Beach, New Jersey
Q. After reading all of this I am really curious about something. So if yellow zinc used to be way more corrosion resistant than clear but now the chemicals used in yellow zinc have changed so with what is used *today, which is more corrosion resistant? Yellow zinc or clear zinc?
Keith Johan- Queensburry, New York, USA
March 20, 2019
A. Hi Keith. There is probably no significant difference because the yellow coloring is usually just a dye -- they both have the same active ingredient, trivalent chromium.
Still, there remain a few shops offering hexavalent chromating such that the yellower the coating, probably the more hexavalent chromium, and the more corrosion resistant. We can explain how it all works and why, but we can't do much about the fact that it's a big, wide, wonderful world and just because things are the commonplace they may not be the universal :-(
Regards,
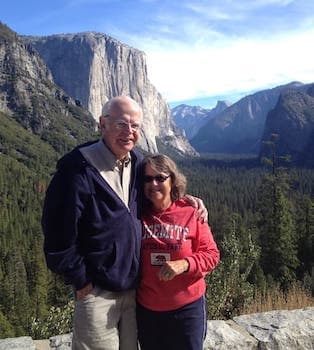
Ted Mooney, P.E. RET
Striving to live Aloha
finishing.com - Pine Beach, New Jersey
Q. I have a free standing ash tray that I had professionally zinc plated which yielded a yellow iridescent color that works well with my amber glass ash tray. Is there some sort of protective final coating I should use to retain its luster or is it good just as it is?
- Buffalo, New York USA
May 20, 2019
A. Hi Nathan. I'm surprised how well that turned out; I hope you're happy with it :-)
Plating shops sometimes include a water-soluble lacquer as the last step of the plating process, but yellow zinc plating usually does not receive a clear coat and I don't think it's necessary. Good luck.
Regards,
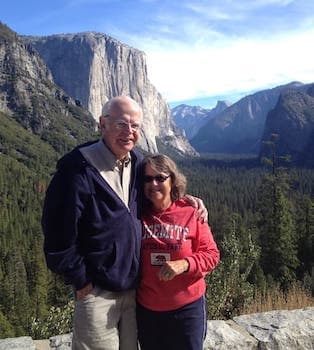
Ted Mooney, P.E. RET
Striving to live Aloha
finishing.com - Pine Beach, New Jersey
A. I may be a bit late to the party, but -
What you have is zinc plating with a chromate coating.
The iridescent hues of yellow/blue/pink exist because the chromate coating is very, very thin, on the order of the wavelength of visible light. If you topcoat with something, say clear lacquer, the iridescence will vanish, and it will be the silvery color of zinc. On the other hand, it might stay shiny longer.
If you like and want to keep the iridescent colors, be careful cleaning. Strong detergents or hard rubbing will remove them.
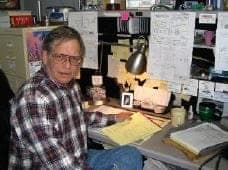
Jeffrey Holmes, CEF
Spartanburg, South Carolina
Yellow chromate of clear zinc plated fasteners
Q. Hello everyone, I have a likely silly question, especially on this forum. However, is it possible to use yellow chromate on clear zinc plated fasteners that I have purchased? This is for an automotive application with limited exposure to the environment. I appreciate the help. Thank you
Ian PenedosRestorer - New Jersey, USA
July 31, 2019
A. Hi Ian. It's not a silly question, but the zinc plated fasteners you bought already have a clear chromate on them. The chromate is a "conversion coating" which reacts with the zinc, so it's not a matter of now dipping those clear chromated fasteners into yellow chromate -- it probably will not react or stick. Sorry.
You might, however, be able to find a gold or yellow toned paint or dye if that doesn't interfere with your needs.
Regards,
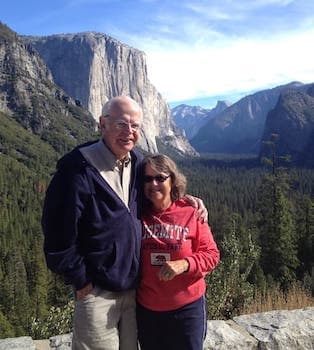
Ted Mooney, P.E. RET
Striving to live Aloha
finishing.com - Pine Beach, New Jersey
Q. Thank you Ted, that's what I was thinking. I saw a forum thread where a guy was dipping off the shelf clear zinc fasteners in yellow chromate and they were staying yellow.
https://rennlist.com/forums/944-turbo-and-turbo-s-forum/1064965-yellow-zinc-bolt-nirvana.html
- New jersey
August 2, 2019
A. Hi again, Ian. I can't argue with the guy's success. I was of the belief that this would not work too erll, but it obviously worked for him. However, I don't really know if his Porsche bolts are the same as hardware store bolts or not; and I don't know if his unspecified "degrease" step removed the existing chromate. So all I can really say now about your inquiry is: "Sorry, I don't know".
Regards,
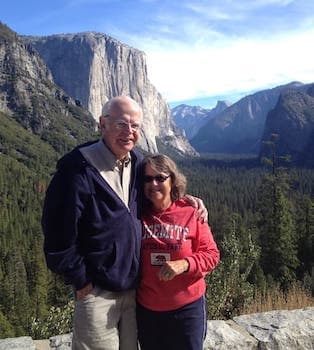
Ted Mooney, P.E. RET
Striving to live Aloha
finishing.com - Pine Beach, New Jersey
Q. Hi, honestly I don't have good knowledge about yellow zinc finishing. I have products we need to do yellow zinc plating on as my customer's requirements. But, after doing plating (sending to vendor for this process) my parts appear with such chemical marks (white patches on certain area).
Based on my vendor, it comes from pitting holes on raw materials. Is it possible? ... because from naked eye I can't see these pitting holes as per mentioned.
Fathi JunQC - Penang, Malaysia
April 9, 2022
A. Hi Fathi. Yes, it's possible that the raw material has pitting which is causing or contributing to a problem, but a plating defect sounds more likely, especially because it's hard to directly connect white patches to pitting. Without good photos, micrographs, and detailed pre-inspection, I don't think we can say for sure though.
If practical I think the best idea might be to simply try another plating shop, but send pics to mooney@finishing.com for posting here if you can.
Luck & Regards,
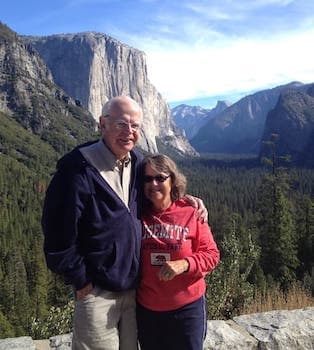
Ted Mooney, P.E. RET
Striving to live Aloha
finishing.com - Pine Beach, New Jersey
Q, A, or Comment on THIS thread -or- Start a NEW Thread