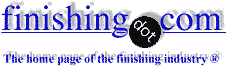
-----
ZrN (zirconium nitride) coatings
Q. Hi,
I'm studying some coating and I would have some information about ZrN coating. Please inform me about advantages of this coating and what is the process.
Thanks,
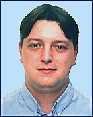
Christophe Petit
- Chicago, Illinois, USA
2001
A. Hello Christophe!
ZrN is a commonly applied physical vapor deposition coating. When done right it looks like gold in color, and is more wear resistant even though it is quite thin (about 2 to 5 microns). I know Richter Precision does this process, and can tell you a lot more about it. Do a search on "PVD coatings" and you'll likely find others.
Good luck!

Lee Gearhart
metallurgist - E. Aurora, New York
2001
A. ZrN is a hard coating, somewhat harder than TiN, but otherwise very similar in nature. It is used on cutting tools, but to a lesser degree than TiN, as it is somewhat more expensive to deposit. It is better than TiN for decorative purposes -- much closer in color to gold, and provides better corrosion resistance. By adding a little carbon, you can achieve a brass color. The gold drills sold at Sears are ZrN coated, as are many high-priced faucets and door knobs.
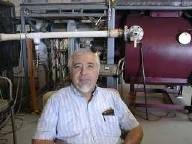
Jim Treglio - scwineryreview.com
PVD Consultant & Wine Lover
San Diego, California
2001
Zirconium Nitride Plating on Steel
Q. Our facility though not a metal finishing company utilizes many finishing processes to enhance metal surfaces for our end product. I am currently researching potential processes and formulas to add to our electroplating facility. Our one and only electroplating process is a non alkaline zinc on 1008 Steel. What processes are available which will enable our organization to add titanium or zirconium nitride plating? The ultimate goal is to add a gold finish to an existing product, but keep our zinc electroplating as well. What options are available to us to enhance our current plating line to add another finish? What are the waste treatment liabilities and options for adding a zirconium nitride process?
Michele La Vasseur- East Bloomfield, New York
2002
A. Hi Michele. Titanium nitride and zirconium nitride are not applied by electroplating. They are applied by PVD processes (gaseous processes) in a vacuum chamber. However, it is often desirable or necessary to include an electroplated underplate--perhaps nickel plating--underneath the PVD coating.
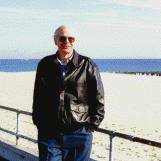
Ted Mooney, P.E.
Striving to live Aloha
finishing.com - Pine Beach, New Jersey
2002
A. Just to add to the previous response, it depends very much on what you are looking for in a finish. For decorative coating purposes, a thin ZrN is usually deposited over electroless nickel, sometimes with a hard chrome interface. For wear applications, a much thicker ZrN coating is applied directly on the substrate. As the ZrN is deposited by PVD, there is no waste stream.
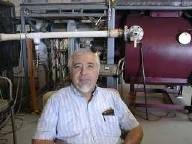
Jim Treglio - scwineryreview.com
PVD Consultant & Wine Lover
San Diego, California
2002
A. Ted is correct that an electroplated layer is needed. TiN and ZrN like coatings are noble in nature and will cause severe corrosion in steels if applied directly. You need to seal the steel similar to that in decorative chrome. These need to be applied as the final finish. Also, severe difference in thermal expansion coefficient will result in cracking of nitrides if applied directly. Depending on size and shape, there may be a limitation where it can be applied.
Mandar Sunthankar- Fort Collins, Colorado
2002
![]() |
Isn't zinc one of the elements that sublimes in vacuum when it gets hot? If so, depositing ZrN or TiN over the zinc plating might be very difficult. The plating will be coming off when the coating is going down. ![]() John Davis - Berthoud, Colorado, USA 2002 It is generally a bad idea to heat zinc coated objects in a vacuum system. In fact, it's not a good idea to put them in there in the first place. Zinc has a very high vapor pressure, and will contaminate the chamber. ![]() Jim Treglio - scwineryreview.com PVD Consultant & Wine Lover San Diego, California 2002 Hi John. Hi Jim. Thanks for warning us about that issue. But I didn't read it that Michele wanted to put zinc plated parts through the PVD process. Regards, ![]() Ted Mooney, P.E. Striving to live Aloha finishing.com - Pine Beach, New Jersey |
Residue after ZrN coating
Q. I have a surgical blade that has a ZrN coating (2-5 microns thick). The blades have set on a shelf for a month or so and leave a blackish residue when wiped across with a piece of paper. A soft cloth yields no residue only paper. The blades are cleaned in 40KHz ultrasonic bath using 1.5% Citranox Citranox
[affil links] cleaner for 2 minutes (any longer turns the light gold color to a rust orange color). Rinsed in DI water and sealed in a porous pouch for sterilization. Any ideas as to what the black residue is?
Thanks in advance!
- Vermilion, Ohio USA
March 21, 2014
Question: Are the blades sitting on the shelf before cleaning, or after cleaning, i.e., do you see the black residue after you have removed them from the sterilization pouch?
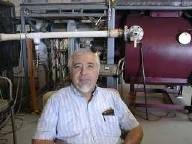
Jim Treglio - scwineryreview.com
PVD Consultant & Wine Lover
San Diego, California
March 27, 2014
Q. The blades are sitting on the shelf after coating (which have the residue). Once an order is placed, we pull from stock and run through the ultrasonic wash (which we have determined does not remove the residue).
I have heard that the ZrN coating can leave a "dust" that is nearly impossible to clean off without rubbing the surface that was coated.
Thank you,
- Vermilion Ohio
March 27, 2014
A. The coating was likely deposited by cathodic arc. In this process, an intense arc is formed on the target that locally evaporates and ionizes the metal. It also forms a pool of molten metal on the surface. The pool spits out droplets of molten metal which land on the substrate and solidify. These macro-particles might be what you are seeing.
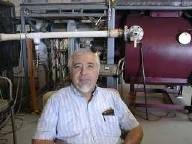
Jim Treglio - scwineryreview.com
PVD Consultant & Wine Lover
San Diego, California
March 28, 2014
Distance from target to object for ZrN coating
Q. Hi everyone!
Could I have your suggestions on the best distance between the object under coating and the ZrN source?
Thank you all!
Shahab
Medical Imaging and Instruments - Irvine California
August 21, 2019
A. It depends on many factors- type of PVD - cathodic arc or sputtering, operating pressure, number of objects you need to coat in a batch, jigs you are using etc. Generally for cathodic arc distance is not too critical. If the operating pressure is too high the ions/atoms coming from the PVD source would get scattered and the flux on the substrates could be considerably reduced. I had encountered this problem while sputtering gold and had to keep the distance less than 50 mm.It is for the operator to optimise the distance unless the manufacturer of the machine has specified it.
H.R. Prabhakara - ConsultantBangalore Plasmatek - Bangalore Karnataka India
August 24, 2019
![]() |
August 25, 2019 Dear H. R. Prabhakara, Medical Imaging and Instruments - Irvine, ca A. Probably not a good idea to get too close to a cathodic arc source. The plasma comes from a rapidly moving spot less than a micron across. If you are too close, less than 50 mm or so, the plasma intensity can initiate arcing on the substrate. ![]() Jim Treglio - scwineryreview.com PVD Consultant & Wine Lover San Diego, California August 28, 2019 |
Q. Dear Jim,
Thank you for tour comment on this!
As the coating has been utilized by PVD, this is not going to be a sputter plasma arc. It's just evaporation.
I'll be really delighted to have your comment on this condition and your recommended distance between the boat and substrate.
All the best,
Shahab
Medical Imaging and Instruments - Irvine, California
September 2, 2019
A. Physical vapour deposition has different versions and the one you are using is the oldest one. For a single 10 mm substrate distance is not critical unless you are too close to the tungsten boat.A distance of 10 - 20 cm should be good enough. Larger the distance lower will be deposition rate which falls as the square of the distance. You would not get a uniform coating on all surfaces if that is what you are looking for irrespective of the distance.
H.R. Prabhakara - ConsultantBangalore Plasmatek - Bangalore Karnataka India
September 3, 2019
September 26, 2019
Dear H. R. Prabhakara,
Thank you for your detailed description. I understand you meant when the the electron gun's being used.
As this project's for surface empowerment of a drill, not a precision coat as with the optical filters are required. I'm hence using the thermal evaporator boat.
I will test the distance you mentioned and will update you with results; probably post the result images here if would be possible.
Best,
Shahab
And special thanks to Ted for this rich environment where we are able to collaborate!
Medical Imaging and Instruments - Irvine, California
Q, A, or Comment on THIS thread -or- Start a NEW Thread