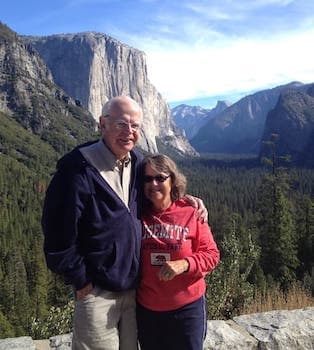
Curated with aloha by
Ted Mooney, P.E. RET
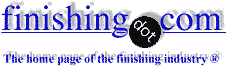
The authoritative public forum
for Metal Finishing 1989-2025
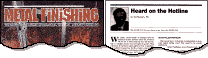
-----
Definition of 'passivated'
Q. Dear Sir,
I am RD engineer of a producer of outdoor furniture (aluminum base)
So far we apply 7-tank pre-treatment
1.Degreasing/Cleaning/Etching
2.Rinse
3.Rinse
4.Phosphating
5.Rinse
6.DI Rinse
7.Passivation.
I've checked many materials but can not tell the difference between phosphating and passivation.
Please advise (in chemical reaction) the procedure of each stage. Does passivation deactivate the phosphating layer?
Thank you
RD Engineer (chemical pre-treatment) - Di An, Binh Duong, Vietnam
February 3, 2022
A. Hi Minh. The problem is the word 'passivation' itself because it is used in many different contexts.
'Passivation of stainless steel' has a fairly standard meaning because there are specifications with that or similar phrases right in their title; so its aim and the required steps are fairly straightforward. But the moment that you are no longer talking about stainless steel, the meaning of the phrase becomes extremely fuzzy ...
• Some people call the processes done to render the plain carbon steel in steam boilers less subject to corrosion 'passivation'
• Some people call the chromate conversion process done on cadmium & zinc plating 'passivation'
• Some people call the chromate conversion process done on aluminum (also called Alodine, Iridite, or chem-film) 'passivation'
• Some people call an extra step after phosphatizing (often a dip in dilute chromic acid) 'passivation' -- so your description of your 7 steps is not wrong: that final process step is indeed often called 'passivation'.
However, those 7 steps are of very limited value for corrosion-proofing aluminum. The best conversion coating for aluminum is probably chromate conversion coating, not iron phosphating. Your process will etch the aluminum and slightly improve its corrosion resistance, but is certainly not a satisfactory final finish like chromating is, and it is only a mediocre finish before paint or powder coating.
Luck & Regards,
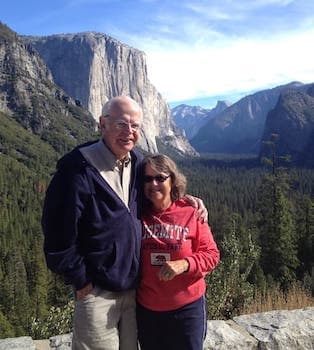
Ted Mooney, P.E. RET
Striving to live Aloha
finishing.com - Pine Beach, New Jersey
Q. OMG
Dear Ted Mooney,
You are my destiny guidance.
I am Minh from Scancom. Aluminium furniture outdoor.
Many thanks for your value advice. I have realized that I should focus on the keyword Anticorrosion.
Henkel provides BONDERITE M-PT 54 NC (Known as Deoxylyte 54 NC) for the "passivation" (tank 7)
H2ZrF6 and (NH4)2ZrF6 are two main components of the chemical solution.
In tank 4 [the Iron (Fe) phosphating] is BONDERITE M-FE 1070 WB I am informed that Fe phosphating has many advantages for powder coating (compared with Zn phosphating)
-adhesion
-no grey surface after phosphating
-no stuck in the nozzle (we apply high pressure jet spraying)
Since there are many sources advised that "passivation" is no need for this line. I wonder, could we remove it. (just Fe phosphating for powder coating adhesion) By the way, the passivation as informed might react the Fe phosphating or not
RD Engineer (chemical pre-treatment) - Di An, Binh Duong, Vietnam
A. Hi Minh Quoc Le.
There is an American idiom: "Too many cooks spoil the broth", which means you should follow one plan, not mix Henkel's advice with finishing.com's advice with stuff you've read claiming that Iron Phosphate is better than Zinc Phosphate ... and end up with an unpalatable mess :-)
But anyway ... you seem to want to start with Bonderite M-FE 1070 Iron Phosphate, and then top this off with Bonderite M-PT 54 NC.
You should check with Henkel whether this is a reasonable & sound sequence for their two chemistries (I suspect that it is not, Henkel seems to be saying that the Bonderite M-PT 54 NC is for use on zinc phosphated surfaces, not iron phosphated surfaces) ... but maybe, since iron phosphate won't really 'take' on aluminum anyway, Henkel will feel that it is okay. Regardless, you are discussing processing aluminum through a treatment cycle normally used for steel; you should be using one optimized for aluminum if you are processing no steel on the line. Again, this should be resolved by Henkel, not helpers on the internet.
Ed. update Oct 2024: Links to Henkel TDS's were removed because they broke (the TDS's were no longer publicly accessible). I am not a Henkel customer and no longer have access to them, so I can't comment regarding your problems. Apologies.
But your claim that iron phosphate is 'better' than zinc phosphate is dubious; zinc phosphate is a more complex, more expensive, more corrosion-resistant, pretreatment -- although iron phosphate does have some advantages such as economy, simplicity, and sometimes better formability after painting without loss of adhesion.
Luck & Regards,
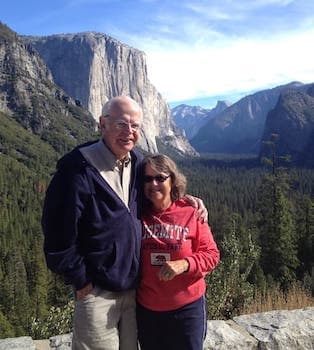
Ted Mooney, P.E. RET
Striving to live Aloha
finishing.com - Pine Beach, New Jersey
Q. Dear Ted Mooney,
Many thanks for your advice and share.
Please consider me as newcomer who comes here to learn about this industry.
Henkel has the reason to set up pre-treatment like that.
Of course, so far, it is running and might not change (I am not sure). Just ignore the current pre-treatment from Henkel.
I have known that Scancom regulation: NO CHROMATE
Please advise, which kind of chemical is the best for Aluminum to increase adhesion.
By the way, I am confused about the chemical below. Please correct me if I am wrong.
Nanoceramic is for anti-oxidization?
Si04 is for adhesion?
Thank you very much.
RD Engineer (chemical pre-treatment) - Di An, Binh Duong, Vietnam
A. Hi again. Sorry but I cannot "just ignore" what Henkel says :-) While it is perhaps possible that you have received poor advice from one specific representative, the suppliers of these pretreatment systems as a whole know more about the subject than the users or people like myself :-)
Ed. update Oct 2024: Again, I no longer have access to Henkel TDS's, so I had to edit my comments as I have no way to verify things about those processes. Apologies.
But I think, generically speaking, that the best pretreatment for aluminum -- not only from an adhesion standpoint but from a corrosion-resistance standpoint as well -- is chromate conversion coating. When you want a hexavalent-chrome-free answer, the substitute trivalent TCP coatings described in MIL-DTL-5541 [⇦ this spec on DLA] are probably the best.
Luck & Regards,
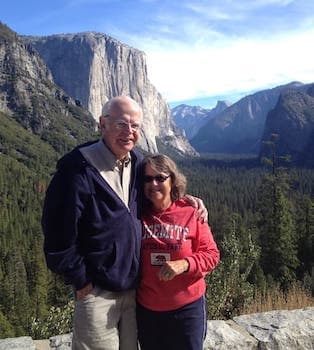
Ted Mooney, P.E. RET
Striving to live Aloha
finishing.com - Pine Beach, New Jersey
Q. Dear Teddy,
I have just receive an advice from Henkel about the conversion coating that Zirconium and Ti02 (nano ceramic) could be a good conversion coating but the cost shall be higher.
Regarding your experience, is it possible to change the current (Fe phosphating) to Zirconium on Alu.
I am looking forward to hearing your feedback about this.
Best Regards
Minh
RD Engineer (chemical pre-treatment) - Di An, Binh Duong, Vietnam
A. Hi again Minh. As per previous responses, you are getting your processes from Henkel and they are more knowledgable about what they offer than I am. But to my knowledge Fe Phosphating doesn't really achieve much on aluminum, so a zirconium or TiO2 coating sounds in principle as good or better, although to the best of my knowledge chromates and trivalent chromium substitutes remain the best conversion/passivation coating for aluminum.
Luck & Regards,
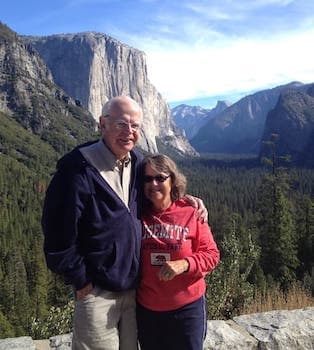
Ted Mooney, P.E. RET
Striving to live Aloha
finishing.com - Pine Beach, New Jersey
⇩ Related postings, oldest first ⇩
Q. Hello,
I would like to know what the term "passivated" means related to metal finishing.
Thank you,
Daniel C. Starkey- Longmont, Colorado, USA
2001
A. Daniel, "passivated" to me, means a zinc surface has been treated with a hexavalent chrome compound. The purpose of the passivation is to increase the amount of time before corrosion of the zinc begins. Some examples of zinc surfaces would be zinc die cast parts, galvanized steel sheet stock, or electrogalvanized sheet stock.
Another definition of passivated implies the protective oxide layer on stainless steel has been restored or regenerated after the parts have been fabricated or welded.
If you give the details of your own situation and the context of how the expression 'passivated' was used, I may be able to pick the best definition for that context.
Roy NussTrevose, Pennsylvania, USA
A. Hi Daniel. 'Passivated' essentially means 'de-activated'. It doesn't have just a single meaning as a surface finish, however. Two very common meanings refer to the treatment of stainless steel in nitric acid or other materials to make it less prone to rusting, and the application of a chromate conversion coating to zinc or cadmium plating.
But there are other meanings too. For example, nickel anodes can become passivated, which is a bad thing rather than a good thing, because the anodes won't dissolve into the plating solution and it will run out of nickel. As Roy suggests, try to give us the context.
Regards,
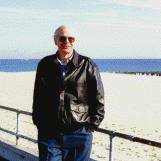
Ted Mooney, P.E.
Striving to live Aloha
finishing.com - Pine Beach, New Jersey
A. Daniel:
There is a good explanation of passivation in ASTM A967.
Passivation of stainless steel is basically the removal of exogenous materials and iron from the surface, thereby "chromium enriching" the surface. This is followed by oxidation of the chromium to form a corrosion resistant layer of chrome oxide on the surface. There are various ways to do this, as explained and detailed in that .
As an example, you can take 316L stainless steel, which is 18% chromium, and by passivating the surface reach up to 90% chromium in the surface layer. This chromium oxide layer is much more resistant to corrosion than the original surface.
Let us know if you need further information.
Regards,
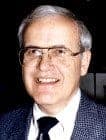

Lee Kremer
Stellar Solutions, Inc.

McHenry, Illinois
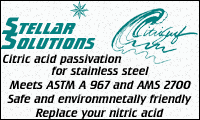
A. Another definition. A passive surface is formed over some metals or alloys when exposed to oxygen or other chemical reactions. This is a very thin and, most of the time, invisible layer that interferes or prevents adhesion of another layer on top of the original surface. It also interferes with on-going oxidation, leading to a kind of "protection" to the surface against environment.
Guillermo MarrufoMonterrey, NL, Mexico
⇦ Tip: Readers want to learn from Your Situation 🙂
many readers skip abstract questions.
Q. Would it be fair to say that most commonly manufactured stainless steel products (i.e., fasteners & hardware) have not been passivated as that would add to the final cost of the product? Is the passivation process visible to the naked eye, or merely a structural action?
Craig Wilson- Ottawa, Ontario, Canada
July 28, 2009
A. Hi, Craig. It would add to the cost, but I would suspect that most such items ARE passivated as it would be wasteful to bother making something of stainless steel which cannot perform like stainless steel because it was not passivated. You probably can't see immediately whether it has been done or not; but if it gets rust spots under more benign conditions than expected, it probably wasn't. Please tell us the situation. Thanks.
Regards,
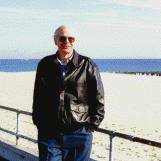
Ted Mooney, P.E.
Striving to live Aloha
finishing.com - Pine Beach, New Jersey
Does Passivation hinder Dye Penetrant Inspection?
Q. Good morning,
I hope that this post is still active so here goes:
We sent 1.5" diameter pins machined from 455 stainless out to be passivated prior to getting the liquid dye penetrant inspection performed. With the "cleaning" of the surface already performed - would that process hinder the discovery of any anomalies present in the material with dye penetrant techniques?
I have a second question with regards to 455 stainless that was used to machine some 1.5" pins.
I asked the plating house that we use this question and they are still pondering their response since this hardware is flight hardware designated. SAE AMS 2579 wants hydrogen embrittlement to be performed within 4 hours of having the parts passivated. If the work order did not direct the plating house to perform the hydrogen embrittlement bake cycle then the question is can the pins be repassivated and then exposed to the bake cycle to satisfy the requirement?
Thank you in advance for your help with this.
- Merritt Island, Florida
February 4, 2015
A. Hi Tom,
Firstly I would not expect passivation to affect dye penetrant results. We actually require certain castings to be passivated before dye penetrant as it actually enhances the results.
Secondly why do you require a hydrogen relief bake out? Passivation is regarded as a non-embrittling. AMS2759/9 does not mention passivation. The Chem column is for pickling, milling and other aggressive processes, which can cause hydrogen embrittlement.
Aerospace - Yeovil, Somerset, UK
A. I agree, passivation doesn't do anything that would affect what the dye penetrant test does.
I don't have a copy of AMS 2579 to check what it says, but I know that concerns about hydrogen embrittlement from nitric acid passivation do exist. (Nitric passivation is pretty close to pickling, that could be why.) As opposed to citric acid passivation, with which hydrogen embrittlement has never been observed. Not sure about the 4 hour thing. I rather doubt the baking is rendered non-functional just because some extra time has passed. Another passivation treatment shouldn't hurt anything, but it's a shame to waste time and resources on being silly just to "satisfy the requirement", though I'm sure it happens all the time.
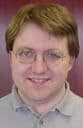
Ray Kremer
Stellar Solutions, Inc.

McHenry, Illinois
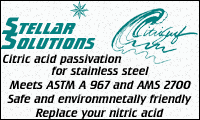
A. Hi Ray,
Neither ASTM A967 nor AMS2700 specify any form of hydrogen bake out. Nitric based solutions are considered non-embrittling, they will not react with stainless or corrosion resisting steels, only with free iron, if it is present. Citric based solutions do not cause embrittlement either, for exactly the same reason, that is why they are considered safer alternatives to nitric based solutions.
The hydrogen bake out delay time is critical if hydrogen embrittlement is possible. The effects of hydrogen on high strength/high hardness steels is time dependent and steels with a hardness over 36HRC or a UTS above 1100MPa are susceptible to hydrogen embrittlement and must be stoved as soon as possible to prevent damage to the alloy. My point is that the operation is superfluous as hydrogen embrittlement is not a risk with this process.
Aerospace - Yeovil, Somerset, UK
Brian,
Point well made. I do get several requests every year for data showing that citric passivation will not cause hydrogen embrittlement, so it seems that many people are not aware that it's not a concern for passivation treatments.
(But then, it's a common thing in this industry I think for people to be afraid of boogeymen that are actually completely unrelated to the process in question. Once people get used to checking for monsters under the bed, they start checking under the couch and in the closets too.)
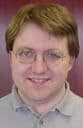
Ray Kremer
Stellar Solutions, Inc.

McHenry, Illinois
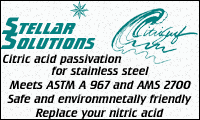
Q. Brian,
And I am looking right now at a company internal passivation spec that one of my customers must follow. It is directly based upon an old version of ASTM A967, but they did add a Hydrogen Embrittlement Relief section assigning a bake time within 1 hour after exposure to any acid for grades with a high UTS. ASTM F519 and ASTM F1940 are referenced.
Clearly there is a wide belief in the industry that passivation at least potentially can cause hydrogen embrittlement, though assuming you are indeed correct on this, it certainly wouldn't be the first wide belief in the industry that is wrong and causes wasted effort.
Just out of curiosity, can you point us to any good references on when hydrogen embrittlement is NOT a concern?
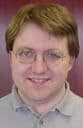
Ray Kremer
Stellar Solutions, Inc.

McHenry, Illinois
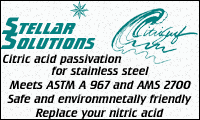
A. The concept of steel passivation can be quite complicated and unless broken down, nearly impossible to understand.
I always point my students to the http://passivationprocess.wordpress.com blog. There is a video section which also really helps.
- Naperville, Illinois
A. Thanks for the URL, Susan. It's fine but the one thing I would add is that, in a lifetime career in this industry I've never heard alcladding or anodizing processes on aluminum referred to as 'passivation' anywhere but in that blog; I think it's a a stretch and we should not call them 'passivation' :-)
Luck & Regards,
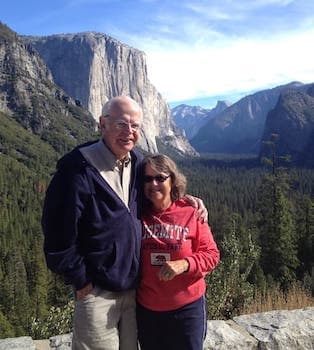
Ted Mooney, P.E. RET
Striving to live Aloha
finishing.com - Pine Beach, New Jersey

this text gets replaced with bannerText
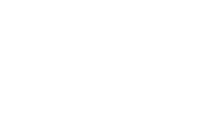
Q, A, or Comment on THIS thread -or- Start a NEW Thread