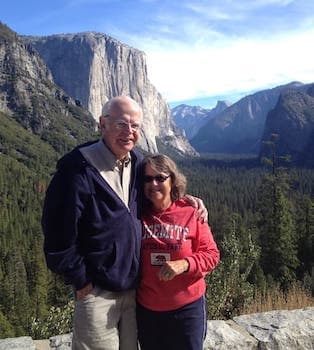
Curated with aloha by
Ted Mooney, P.E. RET
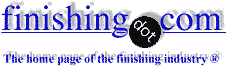
The authoritative public forum
for Metal Finishing 1989-2025
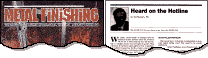
-----
Difference between Nickel plating and Electroless Nickel plating
Current question and answers:
Q. Dear Sirs,
We are performing a nickel plating combination on 7075 Aluminum alloy. Our procedure is similar to some already mentioned on this forum; after double zincate we immerse the parts in mid-P electroless nickel which gives us perfect results, layer thickness around 8 µm - however the customer wants the color and brightness of our electrolytic nickel. After water rinsing we immerse the parts into Ni strike for a couple of min and later in electrolytic Nickel (2.2 A/dm2 current density). The problem is that sometimes the reaction and gas forming is really vigorous and produces defected surface (dark silver stains). Our baths are regularly analysed and optimized and this happens on particular parts only. The most confusing part is that they look perfect after EN but have this vigorous reaction in electrolytic nickel. Any thoughts? Thank you, happy 4th of July :)
- Tuebingen, Germany
July 4, 2019
A. Hi John. 8 µm may seem like a lot, but on a rough and intricate surface, and followed by a nickel strike (which can dissolve some of the nickel), it may not be enough. Aluminum or zinc may be exposed. I would suggest, if practical, applying more electroless nickel to the problematic parts and seeing what happens.
Regards,
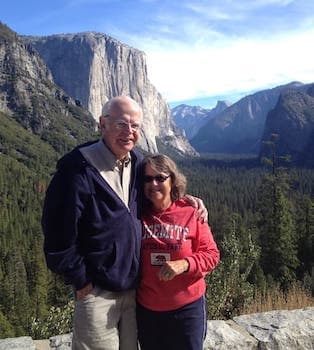
Ted Mooney, P.E. RET
Striving to live Aloha
finishing.com - Pine Beach, New Jersey
July 2019
A. This has been my experience too, my best advise is to treat the aluminum with Zincate, copper plated with an alkaline copper solution, then bright copper plating following by electrolytic nickel plating.
marvin sevilla- Managua Nicaragua
July 7, 2019
Q. Your answer helped a lot so thank you for that - we applied slightly more EN and shortened the immersion time in Ni Strike. Everything was going well until last week when we prepared a brand new EN bath. Regular Al parts from the same material looked fantastic, the ones that were sand blasted (cca. 50% of those parts) had bright spots or stripes in the direction of gases leaving the bath. The procedure is the same as described above in the OP, so they become more visible after electrolytic Nickel. We tried a few runs without Ni Strike - same result, also with different current densities in Electrolytic Nickel. My question is - do you think it is possible that sandblasting material has anything to do with this? Sometimes Copper is EN plated in the same bath after Ni Strike - is it possible that this could be an issue? Thanks and best regards!
John Potochnik [returning]- Tuebingen, Germany
June 24, 2021
⇩ Related postings, oldest first ⇩
Q. Can anyone explain the end physical properties difference between electroless and electrolytic nickel plating. Would hard chrome offer improved corrosion and/or physical properties.
Glen McIntosh- Wisconsin
2001
A. Electroless nickel is far superior to electrolytic nickel for corrosion resistance. That is because it is an amorphous glass-like nickel phosphorous alloy and because the thickness distribution is far superior so there will be no thin spots. Hard chrome is not really corrosion resistant since the cracks extend through to the substrate.
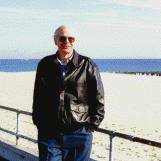
Ted Mooney, P.E.
Striving to live Aloha
finishing.com - Pine Beach, New Jersey
2001
A. Electrolytic nickel is deposited using DC current, while Electroless Ni is an autocatalytic deposition. Electroless Ni produces plating of uniform thickness all over the part, while electrolytic Ni plates a thicker deposit in high current density areas. Electrolytic nickel is more ductile than electroless, which tends to be brittle and glasslike. Typical electroless Ni baths use hypophosphite reducing agents and deposit phosphorus along with the Ni. Mid-Phosphorus (5-8%P) deposits are bright, hard, and magnetic as deposited. High phosphorus (9-15%) deposits are nonmagnetic as deposited, semi-bright, and slightly softer than mid-phos. High-phos Ni has greater corrosion resistance than lower phos deposits. All electroless Ni deposits can be altered by heat treatment at temperatures as low as 800 °F. Electrolytic deposits are Ni-Sulfur alloys if a brightener is used. The sulfur in the deposit reduces corrosion resistance.
Michael Brewington- Salisbury, Maryland
2001
A. Hi Glen:
You already got two professional answers, but adding to Ted and Mike, here are some other physical properties that you asked for. Chromium is harder (900-1100 HV), has a lower thermal expansion (around 8/1000000) and has a higher melting point (1875-1920 °C) than any nickel, either electro or electroless. Most of the time it is stressed and cracked, so it is not an impervious barrier to isolate substrates chemically, but it will resist nitric acid and other strong oxidants better than either electro or electroless nickels.
Guillermo MarrufoMonterrey, NL, Mexico
2001
A. There is one thing that I would like to add on top of the comprehensive explanations that you already received, the low phosphorous EN deposit is almost as hard as hard chromium. That is why some platers use it as a substitute to hard chrome.


Sara Michaeli
Tel-Aviv-Yafo, Israel
2005
A. I just want to add one important thing that should be taken in consideration now with RoHS and WEEE regulations : most of the formulations of these electroless Nickel bath use Lead and Chromium as stabilizer and brightener. And these 2 elements co-deposit with the Ni alloy.
Some substitutions are coming on the market but are not yet common.
- China
2005
Ed. note: Franck's posting is a few years old and most suppliers now offer electroless nickel free of lead or cadmium stabilizers.
Q. I want to know which method takes more time electrolytic or electroless.
dilip patelplating shop employee - gujarat-jamangar, India
March 25, 2009
March 30, 2009
A. Hi, Dilip. Electroless nickel usually takes significantly longer. Plating times of 1 to 2 hours or more are fairly common, while a half hour is a long time for electrolytic nickel plating. But please don't read too much into that answer, because 'productivity' is almost never any consideration at all in choosing electroless vs. electrolytic.
Regards,
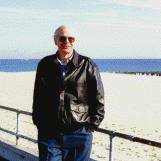
Ted Mooney, P.E.
Striving to live Aloha
finishing.com - Pine Beach, New Jersey
Q. Hi.
We are using MIL standard QQ-N-290A [link is to free spec at Defense Logistics Agency, dla.mil] for Ni Plating. It states Nickel Plating (Electrodeposited) on its header. I cannot make it out whether this is Electroless or Electrolytic process.
Secondly, we are much concerned about RoHS environment. So can you give suggestion what process we should follow, Electroless or Electrolytic?
Thanks
Mihir
- Sydney, NSW, Australia
January 15, 2012
A. Hi, Mihir.
"Electrodeposited" equals electrolytic, so QQ-N-290A describes electrolytic nickel plating; but it is cancelled, so please obtain AMSQQN290.
Many suppliers have reformulated their electroless nickel processes to be free of cadmium and lead for RoHS compliance, but you should check. RoHS compliance may be required for your parts, and is advisable in any case, but is not a driver in deciding whether to use electrodeposited vs. electroless nickel.
Regards,
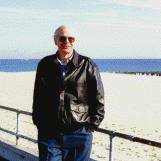
Ted Mooney, P.E.
Striving to live Aloha
finishing.com - Pine Beach, New Jersey
Q. Which nickel process gives the best solderability? How best to reduce/eliminate peeling on Al 3003? We see this a lot when using chloride based fluxes.
phil hughes- Santa Clara California USA
March 21, 2012
A. Hi Phil. Sulphamate nickel plating needs no sulfur-based brighteners so it has less heat sensitivity than other electrolytic nickel plating. Electrolytic nickel is probably easier to activate for soldering than most electroless nickels, but Nickel-Boron electroless nickel plating can be soldered with RMA (rosin mildly activated fluxes).
Plating on aluminum involves an "immersion plating" of zinc from a zincate bath; this is usually the weak link in adhesion. We have dozens of threads on the subject if you put "plating on aluminum" into the search engine.
Regards,
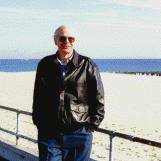
Ted Mooney, P.E.
Striving to live Aloha
finishing.com - Pine Beach, New Jersey
![]() |
Q. I read that nickel plating is used for a basis for chrome plating and comprises 2 layers: semi-bright and bright. What are typical nickel plating thicknesses needed for exterior application corrosion resistance? Tom WardHolland, Michigan May 8, 2012 A. Hi Tom. 25 microns for general outdoor use, 30 microns minimum for automotive, 35 microns for long-term automotive use. The semi-bright layer should compose 60 to 75% of the thickness, and micro-cracked or micro-porous chrome plating should be used. Per ASTM B456. Regards, ![]() Ted Mooney, P.E. Striving to live Aloha finishing.com - Pine Beach, New Jersey |
Q. Environment: Part is exposed to tap water, chlorine, bleach and detergent.
Currently using a Dull Nickel Electroplate and it is rusting very early in life.
Would High Phosphorous Electroless Nickel plating offer a significantly increased corrosion resistance? What is the average salt spray resistance?
- Louisville, Kentucky
May 29, 2012
A. Not many affordable platings will stand up to that environment very long.
For electro nickel, thickness is very important; the more the better. For Electroless Nickel a high phosphorous will work better than a middle one. Boron EN will frequently do better yet. Here again, thickness is critical. With a problem, I would not use any less than 0.0015 inches (1.5 mils).
Consider putting a high phosphorous EN over a good base coat of electro nickel for even better results.
It will probably be cheaper to go to the part made out of 316 stainless or an even more exotic stainless.
- Navarre, Florida
May 31, 2012
Q. Hi,
How can analysis differentiate the Electroless nickel and Electrolytic electrolytic nickel plating? Is there any physical or chemical or instrumental testing methodology available? Please explain.
Divahar S
- India
August 17, 2012
A. Hi Divahar,
Dependent on the technology used, electroless nickel coatings will contain either phosphorus or boron, electrolytic nickel coatings tend to contain small amounts of sulfur. A suitably sensitive X-Ray Fluorescence (XRF) will be able to tell the difference by detecting the non-metallic component. Also Scanning Electron Microscope (SEM) with an EDX attachment would do the same job.
Aerospace - Yeovil, Somerset, UK
August 21, 2012
Q. Is the film produced by electroless nickel plating catalytic in nature ? (i.e., it can work as a catalyst in combustion reaction?)
Harsiddha DaveB.V.M. Eng. College - VALLAH VIDYANAGAR, GUJARAT, INDIA
January 27, 2013
A. Hi Dave. When we in the plating industry say that electroless nickel is catalytic, we mean that the nickel plating catalyzes the reducing agent for continued deposition of more nickel from the plating solution; we are not talking about combustion. I know nothing about combustion engineering, but I have no reason to suspect that electroless nickel plating would catalyze more complete combustion.
Regards,
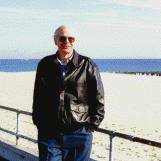
Ted Mooney, P.E.
Striving to live Aloha
finishing.com - Pine Beach, New Jersey
January 29, 2013
Q. Does the Electro Nickel plating process change the molecular structure of the base metal? (not Electroless)
Q. Does it heat the base metal at all?
Q. How well will it last in a mild caustic wash down situation?
- Nelson, New Zealand
October 30, 2014
A. Hi Derek. Electrolytic nickel plating could possibly cause hydrogen embrittlement of high strength steel. And if a heavy layer were plated on a very thin object, the tensile stress of nickel plating could possibly compressively stress the object.
Nickel plating is done by immersion in an aqueous based bath at 140 °F, and the part could be slightly warmer, and might approach the boiling point of water earlier in the pretreatment process.
Nickel plating of reasonable thickness, so it is free of porosity and pitting, should stand up to a mild caustic wash down.
It would probably be better to describe your intended application, because that way readers might be able to warn you about potential issues rather than you having to try to imagine them. Another problem with abstract questions is that you may be concerned about the overall process whereas readers might respond in terms of just the one nickel plating step per se rather than the usual prep steps; another potential problem is that different substrates may involve different issues. Good luck.
Regards,
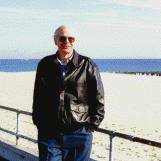
Ted Mooney, P.E.
Striving to live Aloha
finishing.com - Pine Beach, New Jersey
December 2014
Q. Hello, could anyone tell me when and why should I go for the electroless coating rather than the electrolytic? What will be the major difference in their end results?
Vimal Adzenhan- Surrey, England
January 10, 2016
A. Hi Vimal. Electroless nickel generally offers significantly greater corrosion resistance at significantly greater cost. There are many responses on this thread which attempt to answer your question in terms of corrosion resistance, consistency of thickness, hardness, magnetic effects, temperature resistance, speed of deposition, etc. If you give us the specific application & situation, I think people can answer you very directly about which type of nickel plating would be best for that situation and exactly why.
But there are many different types of electroless nickel plating, many different types of electrolytic nickel plating, and idiosyncrasies everywhere -- so while a two-paragraph internet response might suggest the best finish for a highly specific case, it is unlikely to educate someone enough for them to be able to make the choice in a more general case. Metal finishing consultants usually acquire many decades of experience before they presume to predict the applicability and service life of a finish; the previously linked books by Mallory & Hajdu, and by Dennis & Such should be a good intro though. Good luck!
Regards,
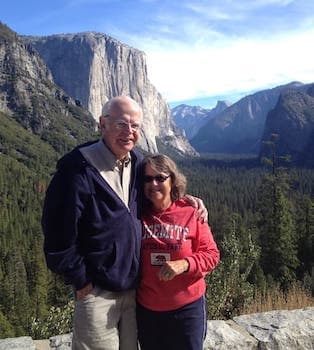
Ted Mooney, P.E. RET
Striving to live Aloha
finishing.com - Pine Beach, New Jersey
January 2016
Q. What will be the process sequence for Antique brass plating on mazak?
Presently we are doing copper + bright nickel + brass + black nickel (all are electrolytic), and antique finish by brushing the black nickel.
But rejection rate is huge; can we do electroless nickel instead of bright nickel?
- Pune, Maharastra, India
September 16, 2017
December 7, 2017
A. Hi Krishna,
Where is your failure occurring? You state the reject rate is "huge". Is it due to the antique finish not being what you want once the black Ni is polished back? What would the bright electroless Ni be fixing? It seems, based on your post, you aren't satisfied with the imitation patina you end up with. If it isn't inconsistencies in the antiquing that is causing the rejects then what is?
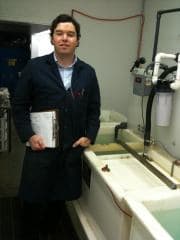
Chance Dunstan
Electroplating/Forming/Coating Manager
Placerville, California USA
Q.
Dear Sir/Madam
I want to plate Brass Material, and electrical conductivity is our consideration. So, in term of conductivity, which one is better, electrolytic or electroless Nickel Plating?
Thank you for your kind response.
Best regards,
- Batam, Indonesia
February 20, 2018
A. Hi Dallas, electrolytic nickel is better. For details please see Sjamp van Esch's excellent response on topic 18940. Good luck.
Regards,
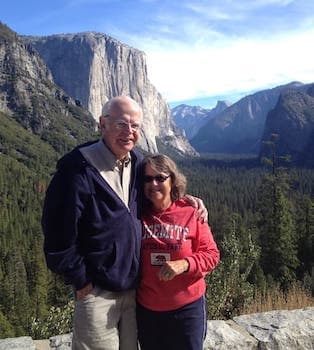
Ted Mooney, P.E. RET
Striving to live Aloha
finishing.com - Pine Beach, New Jersey
February 2018
Electroless Nickel isn't resisting bleach
Q. Hello. I've sourced components to be electroless nickel plated (high phosphorus) in an effort to improve corrosion resistance as compared to clear zinc in an environment with high humidity and periodic exposure to dilute chlorine bleach that is used for sanitizing purposes. The EN plated parts performed very well compared to clear zinc in salt fog testing however we're experiencing the complete opposite with daily misted exposure to a 50/50 mix of commercial chlorine bleach and water. This is not what I expected. Are there recommendations on where to start with root causing this or recommended alternatives that might perform better (not changing the substrate as I'm trying to avoid re-tooling). BTW, the substrate is low carbon steel. Thanks much!
Michael ColemanMechanical Engineer - Noblesville, Indiana US
November 9, 2018
November 15, 2018
A. Of course zinc with a clear chromate will not withstand repeated exposure to bleach.
I'd expect electroless nickel to do very much better, but that will depend to some extent on the surface preparation and EN thickness. In this aggressive environment, I'd suggest at least .001" thick, maybe more.
However if your standard is hundreds or thousands of exposures, then you're going to have to change material.
If plastic will work, then there are multiple choices - PVC, polypro, teflon, etc. There are metal alloys too.
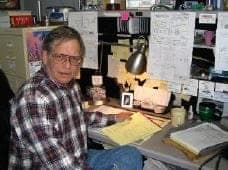
Jeffrey Holmes, CEF
Spartanburg, South Carolina
November 2018
A. Hi Michael. The reason it's performing worse than zinc is that zinc is anodic to steel and preferentially corrodes, whereas nickel is cathodic to steel and -- once breached through a pinhole or porosity -- will accelerate the rusting.
As Jeff says, as a first step it must be thick enough to be completely free of pinholes & porosity.
And thanks for reminding our readers, through example, that salt fog testing should not be used for trying to compare the corrosion resistance of one finish to another :-)
Regards,
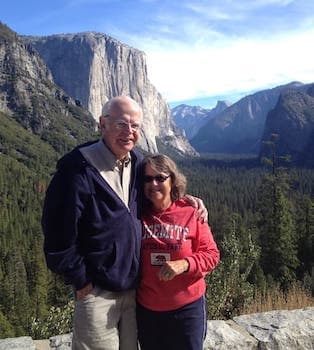
Ted Mooney, P.E. RET
Striving to live Aloha
finishing.com - Pine Beach, New Jersey
Q. Thanks for the feedback Ted and Jeffrey. I'll likely pursue a heavier nickel deposition in parallel with analysis, maybe SEM, to see what might be going on at the grain level with porosity. Some further background that I didn't mention was that the components are being stripped of clear zinc plating prior to EN. I don't know if this might have an etching effect at the grain boundary that might increase porosity and make the parts more difficult to plate adequately.
I mention this because after EN plating over a fc-0205 powdered metal component its performance was substantially poorer in salt fog and as a result will follow a different protocol for that component. Porosity is always a concern with plating powdered metal components needing corrosion resistance that are not either resin impregnated or copper infiltrated. Have anyone experienced issues as a direct result of the stripping process? The stripping process is acidic but other than that I don't know the specifics.
Another option I'm looking at is zinc-nickel. I've seen impressive salt fog results compared to clear zinc and zinc dichromate (the hex chrome component is driving obsolescence here). Testing is just getting underway with sodium hypochlorite exposure. Any feedback with zinc-nickel / chlorine bleach corrosion exposure would be greatly appreciated.
Thanks! This is a great resource!
- Noblesville, Indiana, USA
November 19, 2018
A. Hi again. I personally think that if EN is affordable and practical it is the right solution. When you are studying grain structure, maybe see if you can confirm what I have heard for many years, that smoothness of the substrate is key to corrosion resistance of electroless nickel. I assume that it is true and that it is because a thickness which is sufficient for a pore-free finish on a very smooth surface may still have dislocations and consequent porosity on a rougher surface.
Regards,
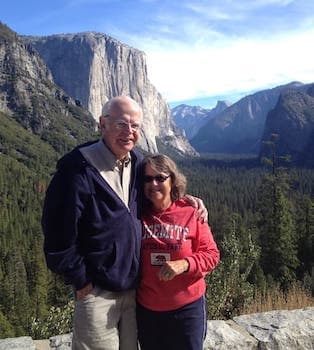
Ted Mooney, P.E. RET
Striving to live Aloha
finishing.com - Pine Beach, New Jersey
May 7, 2019
Q. Hi I am Manikandaprabu, many of the comments here are very useful for our development thanks; I have a query again:
Currently we are using SS304 in drive assembly spintube attached with the agitator shaft of laundry machine, for cost effectiveness purpose I have planned to replace that with Electroless nickel plated low carbon steel. After hardening, will it give me required properties like salt spray test (5% NaCl) withstand of 500 Hrs with 40 Hrc hardness, if there is any alternate plating please suggest.
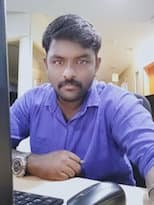
Manikandaprabu Janarthanam
- Thirubuvanai, Pondicherry, India
A. Hi Manikanda. Electroless nickel is an exceptionally corrosion resistant finish for many reasons including full coverage, even thickness of deposit, and glassy finish. I don't think you can do better. But I'm not quite clear whether you are heat treating the steel or the electroless nickel coating -- my understanding is that you can obtain that hardness without heat treating the nickel, and you'll get the best corrosion resistance by not heat-treating and by using the highest phosphorous which will deliver enough hardness. My understanding is that the smoother the finish, the better chance you have of reaching 500 hours salt spray resistance. Good luck!
![]() | We'd appreciate feedback regarding what you ultimately decided to do and what you learn! This is a public forum where we all learn by trying to help each other, and finding out whether the suggestions actually work is crucial to making it better. Thanks again. |
Regards,
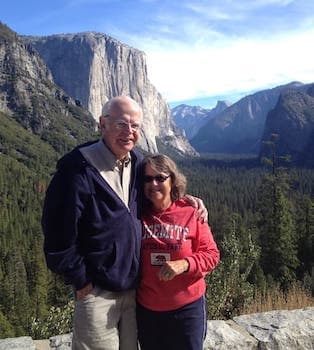
Ted Mooney, P.E. RET
Striving to live Aloha
finishing.com - Pine Beach, New Jersey
May 2019
June 15, 2019
A. Dear Manikanta,
The replacement of steel instead of SS on the drum component won't work, there is little chance you will get to 500 hours with only EN, you will wind up giving rust stains free of cost on the clothes.
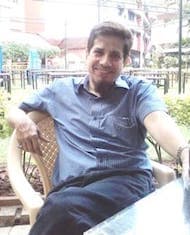
Khozem Vahaanwala
Saify Ind

Bengaluru, India
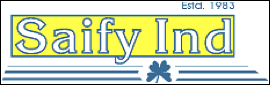
Q. We are in need of a Metallic or Non Metallic coating in one of our Drive parts which is used in Laundry machine, Part dimension is 300*28*3mm and Material: EN8D, Anyone can suggest a suitable coating that can withstand 500 Hrs of Salt spray resistance as per ASTM B117 and excellent wear and abrasion property, Thanks in advance!
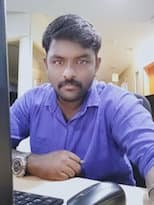
Manikandaprabu Janarthanam
- Thirubuvanai, Pondicherry, India
February 27, 2021
February 2021
A. Hi cousin. In response to your question almost 2 years ago, I suggested trying electroless nickel, whereas Khozem expressed the opinion that only stainless steel will hold up on the wet components within a washing machine.
I think what is most absent at this point is feedback on what you've actually tried and what you're actually learning from it.
There's an expression courtesy of the bridge players of the world: "a peek is worth a thousand finesses" :-)
Luck & Regards,
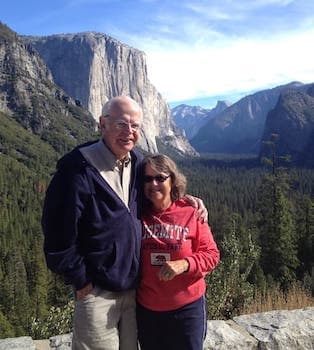
Ted Mooney, P.E. RET
Striving to live Aloha
finishing.com - Pine Beach, New Jersey
Q. Hi Mr. Ted, Happy to hear from you, meanwhile in this 2 years we have tried varieties of coatings like Zinc nickel, Electroless Zinc Nickel, Black passivated in EN8 Material -- but at the end of 500 hrs salt spray everything is getting failed with 300 Hrs of the testing. Need your suggestion on the same.
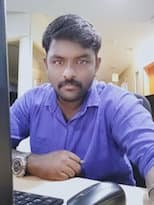
Manikandaprabu Janarthanam
- Thirubuvanai, Pondicherry, India
March 2, 2021
A. Hi again, Manikandaprabu. Electroless nickel can hold up to salt spray testing for over 1000 hours but it does depend upon good, smooth, surface preparation and sufficient thickness (which may not be practical for this component).
If you remain unreceptive to Khozem's answer, then here's a final one for you: hot dip galvanizing followed by anodization of the zinc coating. Decades ago Fred Perlstein found this finish remarkable and, to my understanding, it was at one time used on some washing machine components :-)
References:
https://www.pfonline.com/articles/zinc-anodizing
https://www.finishing.com/125/88.shtml
https://www.finishing.com/136/06.shtml
Luck & Regards,
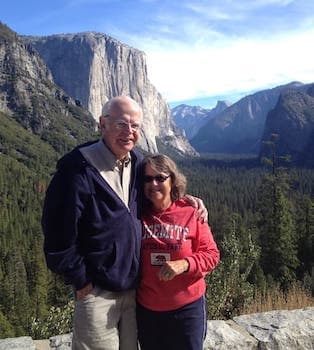
Ted Mooney, P.E. RET
Striving to live Aloha
finishing.com - Pine Beach, New Jersey
March 2021
Thanks for the suggestion, Mr.Ted; will try the coating and let you know.
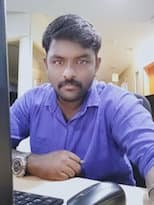
Manikandaprabu Janarthanam
- Thirubuvanai, Pondicherry, India
March 3, 2021
Q, A, or Comment on THIS thread -or- Start a NEW Thread