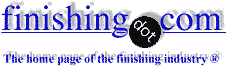
-----
Zinc Plating
Q. Details about Zinc Plating Process Management and about NCZ e.g., plating.
MohanrajDubai Wire - Dubai, UAE
A. For general overview of zinc plating baths, get a copy of the Metal Finishing Guidebook, available through Metal Finishing Magazine. For more detailed information on a specific chemistry, ask for a copy of the technical sheets for the chemicals the plater is using (the tech sheets, not the MSDS sheets). You can get a copy of the tech sheets from a plater using that solution or from the chemical supplier. This will give you information on what variables like temperature and pH that need to be controlled in the baths. If you need even more detail, take a trip to a good plater and look around at the equipment and ask about the processes.

Tim Neveau
Rochester Hills, Michigan
Q. We are about to establish our new section of Tin-Zinc Electroplated coatings. We would be very appreciated if you could send us the information of the complete process of this kind of plating.
Pakdee Jiradejsopon- Bangkok, Thailand
1999
Q. I wish to know some Zinc Plating information:
a. Zinc Plating is a stable coating? will peel off easily? will have finger print if touch on it?
b. Need special handling after go through this process?
c. This coating is good corrosion resistance?
Regards
TEI KMconsumer - Singapore
2005
A. Zinc (as a hot dipped or as an electroplated coating) provides corrosion protection by gradually corroding. The corrosion takes place on the zinc surface instead of the on the base (underlying metal). It is therefore referred to as a "sacrificial" coating. Zinc is relatively inexpensive and is easily electroplated, making it a popular coating on commercial goods. The plating is usually followed by a chromate passivation which slows the corrosion (Oxidation) process.
There are much better methods to prevent corrosion, but which one to use depends on the product being coated, and the expense factor as well.
The passivation may help prevent fingerprinting to a small degree, but the acid that naturally occurs on the human hand will cause fingerprinting, particularly in a humid atmosphere.
Both electroplated and hot dipped zinc coatings adhere well if the surface to be coated is properly prepared.
Hope this helps.
Happy New Year!
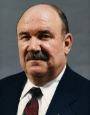
Daryl Spindler, CEF
decorative nickel-chrome plating - Greenbrier, Tennessee
2005
Q. What types and thickness of zinc plating are there? How can I measure or check zinc plated parts?
David B [last name deleted for privacy by Editor]casters - Jonesboro, Arkansas
2001
A. There are many varieties of zinc (not "zink") platings. There is normal zinc plating, and there are zinc-alloy platings like zinc-nickel, zinc-cobalt, zinc-iron, and tin-zinc. There are also different chromate conversion coatings that go on top of the plating. The conversion coating determines the final color of the part. There is zinc-clear, zinc-yellow, zinc-bronze, zinc-olive drab, and more. You can combine the two to get things like zinc-nickel-yellow and zinc-iron-black.
Measurements depend on what your requirements are. The typical measurement is plating thickness, which is measured in microns (metric) or mils (English). There is a whole host of destructive and non-destructive measurement devices, depending on your measurement needs.
Zinc platings are also usually tested for corrosion resistance using the salt spray test according to ASTM B117. The pass/fail criteria for this test is an agreed amount of hours to white corrosion and/or red rust depending on the application.
Other measurements you may want: friction, surface finish, appearance, adhesion, resistance to stone impingement, and more. Again, most of the measurements will depend on what the needs of the application are.

Tim Neveau
Rochester Hills, Michigan
2001
Q. We observed white and black spots on entire area of Zinc plated plates after 2 to 3 days after plating. Size of spot is very less @.5mm dia. Is it a white rust? whether it will affect anti corrosion property of plates.
DHANANJAY BHAGWAT- Thane, Maharashtra, India
2006
Q, A, or Comment on THIS thread -or- Start a NEW Thread