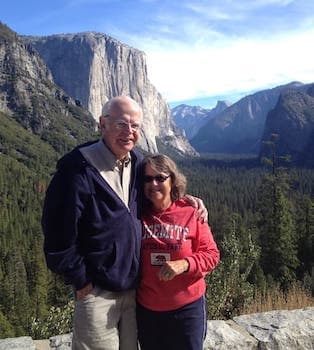
Curated with aloha by
Ted Mooney, P.E. RET
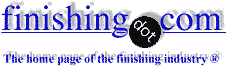
The authoritative public forum
for Metal Finishing 1989-2025
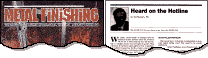
-----
Improving throwing power of tin bath
I need to increase the throwing power in an acidic tin process. I use the traditional formulation but my problem is to plate inside a tube with 2 inches in diameter without auxiliary anodes that means I need better throwing power. I am not sure if an alkali formulation should be a good aim.
Thanks in advance.
Jose CestaServico Nacional de Aprendizado Industrial - Sao Bernardo do Campo, Sao Paulo, Brasil
What type of acid tin are you using? We have fluoborate, MSA and sulphate tin processes in our shop, and I find that the sulphate tin has the best throw of all. In fact, with only one anode in the bath, it will throw behind a flat part, coating both sides. Hull cell panels of these baths are coated front and back.
Michael Brewingtonplating shop - Salisbury, Maryland, USA
Usually alkaline processes have better throwing power than the corresponding acid process. Alkaline tin has comparable throwing power to cyanide copper.
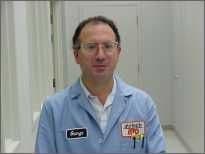
George Shahin
Atotech - Rock Hill, South Carolina
HAVE A GOOD DAY.
The problem is as follows: I need to plate tin inside a tube 5 inches long and 2 inches in diameter. I can not aplly auxiliary anodes because I intend to use a automatic line. The only way is to use a tin bath with the best throwing power. My sulphate tin process with nominal strenght do not work well regarding my needs because I have only a few tin in microns in the inside of the tube. Maybe somebody know a good literature about new developments in tin bath?
Thanks in advance,
Jose Francisco CestaSENAI - Sao Paulo
You could use non-conductive shielding on the racks to improve throw inside the tubes. If the tubes' ends are facing the anodes, fixture a plastic panel near the end of the tube. The panel could have a hole cut in it that's smaller than the ID of the tube.
Michael Brewingtonplating shop - Salisbury, Maryland, USA
Q, A, or Comment on THIS thread -or- Start a NEW Thread