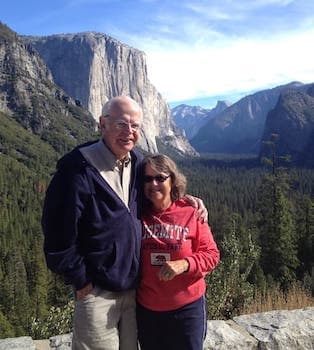
Curated with aloha by
Ted Mooney, P.E. RET
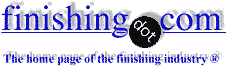
The authoritative public forum
for Metal Finishing 1989-2025
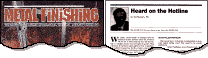
Thread 11/85
Tin Plating Problem: deposits on the anode bags

this text gets replaced with bannerText
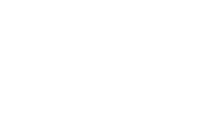
Q. My company is an electronic component manufacturer and as part of the production process we plate Ni and Sn for solder leads. Recently we have seen problems with our methane sulfonic tin bath in the form of a crystalline precipitate in the bath. Analysis of the precipitate revealed that it is mostly tin, but I cannot find any reason for the precipitation of such large amounts in the bath (pH, Sn concentration, and chelate additive levels have all been consistent during this time). One pattern seems to have emerged: the precipitation seems to start at the anodes and clogs the anode bags up within 3-5 days. Has anybody seen this before, or something similar? If you have any information or suggestions, please let me know.
Mark Carper1998
publicly reply to Mark Carper
A. I have seen precipitation start at the anode bags in nickel plating baths which contained very high sodium. Is this bath on an evaporator?
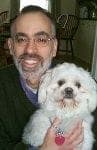

Tom Pullizzi
Falls Township, Pennsylvania
1998
publicly reply to Tom Pullizzi
Q. No, there is no evaporator for this Sn bath. Was it just sodium which precipitated? And do you know why it precipitated primarily at the anode bags?
Mark Carper [returning]1998
publicly reply to Mark Carper
A. It was mostly sodium, but if you are not concentrating and returning a lot of the tin bath back into the tank, the sodium is probably not building up. The speculation for the precipitating at the anode bags was that the total concentration of ions around the dissolving anode was higher that the solubility of the ions.
Another idea: The Canning Handbook [on eBay, Amazon, AbeBooks affil links], on their tin sulfuric/phenol sulfonic acid bath warns of passivity of anodes when the current density exceeds 20 amperes/square foot of anode area. Have you increased the current lately, or perhaps your anodes have been coated. Also the bags tend to tighten up over time.
You know, for barrel plating, you really don't need anode bags. Fines will settle to the bottom, it's true, but you can get a lot more current if you don't have to go through a bag. But; people become attached to their anode bags, and no one ever got fired for leaving them on. Personally, I think maintaining those bags is one of the most miserable jobs on this earth.


Tom Pullizzi
Falls Township, Pennsylvania
publicly reply to Tom Pullizzi
A. Mark,
Your problem of precipitation is one that afflicts all MSA (methanesulfonic Acid) based tin-bearing baths, both pure and alloy plate. The white or Bone colored precipitate is tetravalent Tin or "Stannate" ion which is sparingly soluble and therefore readily precipitates. You are probably doing little wrong, as precipitation of Stannate in this bath is spontaneous, and will occur if there is any dissolved oxygen present in the bath, which there will be if the bath surface is exposed to air. Divalent Tin, or Stannous Ion is the plateable species but is readily oxidized to Stannate ion by free oxygen in the bath. The vendors of MSA processes attempt to counter this by adding to the bath "antioxidants" (yes, precisely the same chemicals they are now selling as nutritional supplements). These antioxidants scavenge any free oxygen in the bath by outcompeting against Stannous ion for it, thereby depleting the bath of Oxygen potential and now the Stannous Ion conversion reaction is shut down due to lack of reactant (Oxygen). Sounds brilliant but it doesn't really work worth a DA__. But I do have some advise:
1. If you are air sparging, shut it off immediately and do something else for agitation.
2. This oxidation reaction is accelerated by stagnant flow conditions on the surface of the anode. As Tin dissolves at the anode, it first loses two electrons becoming Stannous, then can lose two more to become Stannate. As the "Plating Reactor Design Engineer", it is your job to provide a means of getting those newly hatched Stannous ions away from the metallic anode surface ASAP so that the anode does not have time to steal two more electrons from it forming Stannate. But you can NEVER solve this problem because the anode is immersed in Stannous bearing plating solution! But the "conversion ratio" can be minimized through correct reactor design. At first you may think to remove the anode bags to eliminate the stagnant anode condition, but this will cause nodules/rough-plate on your workpiece due to any unfiltered suspended Stannate formed by the above mentioned two mechanisms. So you still must do it through reactor design.
Regards,
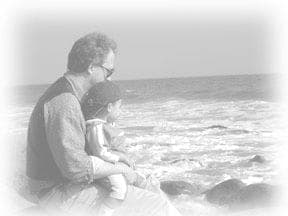
Dave Kinghorn
Chemical Engineer
SUNNYvale, California
publicly reply to Dave Kinghorn
A. Mark,
According to your description, this problem was mainly caused by the over-generation of stannate ion at anodes. As Dave said, stannous ion is very soluble in acid solutions while stannate ion tends to precipitate in the same solution. For a commercial tin plating bath, some tin-stabilizing agents are added to the bath to reduce the conversion of stannous to stannate ion, in addition to complexing agents. In your case, methylsulfonic acid is one of stabilizing agents. If this chemical is not in an adequate concentration range, it is unavoidable to generate stannate ions in the solution.
At tin anodes, three reactions could simultaneously take place: Sn to Sn(2+), Sn to Sn(4+), and Sn(2+) to Sn(4+) if anodic potential is quite high. The first reaction contributes to plating, while the second and third reactions contribute to the precipitation you observed. Under normal conditions, the first reaction dominates the anodic reaction. If any factors, such as high pH, bag clog, lack of complexing agents and overload, etc., lead to the significant increase in anodic potential, the second and third reactions will follow up.
Although you mentioned everything was consistent, something must be wrong. For example, I would like to ask if the pH meter was calibrated properly, standard solutions were correct, all meters functioned normally, and others. These things often happen in metal finishing shops in my experience. Regularly changing anode bags is very important. The dirt from tin anodes will initially clog the bags (you may not see it), and this leads to the increase in anodic polarization, which results in the second and third reactions. Then the precipitation of stannate oxide further clogs the bags, which causes a worse cycle mentioned above.
Ling Hao- Grand Rapids, Michigan
publicly reply to Ling Hao
A. Let's say every thing you're doing is correct. Meaning temperature control, only pump filtration for solution movement, no drag-in, proper pH, proper levels of Sn/Pb and of additive.
I have found insoluble Sn can be caused by a number of unlikely ways. One of the ways I've run across is city water rinse. It introduces salts that can migrate to the anode film and help to form these insoluble forms of Sn. Another way is poor rinsing of anode bags before using. Trapped chemistry from manufacturing of bag if not properly soaked can trap and form insoluble Sn. Or although unlikely if the mesh of the bag if to fine it may not be allowing proper flow around anode. To see if it being caused by anode bag you might try removing one of your anode bags for a short time and seeing if you still have the problem. If the problem does not persist try changing anode bags. If you still continue to have a problem, you may have to carbon treat or plate at a low current density to remove possible metal contamination. I do not believe that you are having these problems but they are possibility.
Bruce VammmenOcala, Florida
publicly reply to Bruce Vammmen
A. Hi, Mark. Please check the contact between the contact bar and the basket.
Zhou Heng- Singapore
October 30, 2010
publicly reply to Zhou Heng
![]() |
2001 A. Tin Solution for Still Plating.
- Ocala, Florida publicly reply to Britt M. Mulhollem ---- |
Will increasing acid stop tin precipitation?
Q. I am new to Sn plating, and would like to ask a follow up question. A lot of people here mention that Sn4+ is insoluble. But what compound with Sn4+ precipitates, is it SnO, SnO2, or something else? If it is one of the oxides, increasing the acidity of the bath should eliminate the problem of precipitation.
Igor Volov- New York, New York, USA
March 9, 2012
publicly reply to Igor Volov
![]() |
A. Hi Igor ![]() Harry Parkes - Birmingham, UK publicly reply to Harry Parkes A. Hi Igor, ![]() David Shiu - Singapore publicly reply to David Shiu |
Multiple threads merged: please forgive chronology errors and repetition 🙂
Q. Hi,
We are doing reel-to-reel plating of Ag, Sn, Ni, Cu, Au and PdNi. Recently we are facing two different problems in our Nickel and Tin plating process, as below.
1. During Nickel and Tin plating the metal starts depositing on the Anode bags through the baskets (against the Law of Faraday).
2. We supported the reel with help of an Acrylic guide. After few reels plated, Tin deposit could seen on the guide, which looks like a tree.
Can any one help us to sort these issues.
Thanks in advance,
Connector parts manufacturer - India
2006
publicly reply to D. DHANASEKAR
A. The only time I have seen metal deposit on the anode was when I was plating copper parts with nickel and I left the unpolarised copper in the tank at some of it dissolved. It then formed an immersion deposit on the nickel. Perhaps you are achieving the same thing from silver being dragged in the tin and nickel tanks.
As far as getting tin trees growing on your acrylic guides, I suspect you have got some metal peeling off strip and it has got stuck in the guide. When you pass the charged strip through the line, the metal gets charged and lets metal deposit onto it - hence the tin tree.
I suggest you strip your line down and make sure all your rinses make sure your rinses are working properly and you are not getting any cross contamination. Then check your acrylic guides are not impregnated with bits of metal flake.
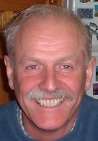
Trevor Crichton
R&D practical scientist
Chesham, Bucks, UK
publicly reply to Trevor Crichton
A. 1. Anode deposition through the bags, might be due to bi-polar effects?
Hamilton Solidum- Mays Landing, New Jersey
publicly reply to Hamilton Solidum
A. This problem will occur anytime an anode looses current yet is in the field of anode/cathode current transfer. As stated before, a bipolar effect comes into play making the affected anode both an anode on one side and a cathode on the other side.
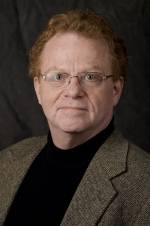
Bob Adams CEF
Tijuana, Mexico
September 20, 2012
publicly reply to Bob Adams CEF
Q. Dear All,
I am a Plating Process Engineer at a semiconductor company in Malaysia.
One of my plating line had several times encountered Pure tin plating deposited on the outside of anode bag.
I got to know that the deposition had developed when the output had quality issue of "excessive solders" on some leadframes. My team & I did a plating process cells' cleaning & during the replacement of anode bags, we often found it. We believe the excessive solders were detached from the deposit & travelled on the affected leadframes.
Does anyone in the forum had encountered this before? Appreciate if you can share your findings on the root cause and the actions taken to prevent it.
**we are using belting system whereby the leadframes are carried through the process cells in a vertical position.
Thank you.
Regards,
Fir
- City: Muar State: Johor Country: Malaysia
May 31, 2017
publicly reply to Fir Ismail
A. Hi Fir,
One possible scenario is conductive anode sludge or Sn(IV) colloid trap on anode bag surface whereby anode bag swollen during operation (strong solution flow, lose tie up to anode basket, etc) and accidentally touch lead frame (cathode) to cause tin plating extend to anode bag surface.
Regards,
David
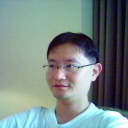
David Shiu
- Singapore
publicly reply to David Shiu
A. This appears to be caused by bi-polar currents. Conductive Anode fines collect on the bottom of the bag but are not in electrical contact with the electrode. This causes them to bipole.
Possible corrective actions are to clean the tanks and change bags more frequently, and also to investigate if your tin anodes contain additives that make them corrode more evenly and generate less fines.
Lyle Kirman
Consultant - Cleveland Heights
publicly reply to Lyle Kirman
Sn/Pb plateout
Q. I am running a Eutectic bath plating semiconductor circuits on a silicon wafer. It is an MSA based bath. I have constant issues with the bath plating out near the electroplating site adhering to the polypropylene surface. Does anyone have any experience with this? Adding additional MSA seems to lower the magnitude but does not solve the problem.
Jason WrightEngineer - Chandler, Arizona, USA
July 17, 2017
publicly reply to Jason Wright
Q. New information. I tested the plateout material using XRAY and it shows that it is mostly Tin at ~95%. My theory is that the Tin level is too high in the bath and that might be causing the plate-out on the polypro material. Thoughts?
Jason Wright [returning]- Chandler, Arizona USA
publicly reply to Jason Wright
A. Hi Jason,
It's unlikely tin plate out as metal on somewhere non conductive merely due to too high tin concentration in plating solution. Even it was, it should happen randomly rather than selectively per your describe "plating out near the electroplating site adhering to the polypropylene surface". Wonder if possible cause similar to my reply to Fir earlier.
To test out your theory, you may prepare an abnormal high tin concentration bath solution in lab with PP immerse inside to see if any tin metal plate out.
Regards,
David
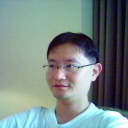
David Shiu
- Singapore
publicly reply to David Shiu
Analysis of MSA tin sludge
Q. Hi David Shiu and others colleagues,
I have a problem with analyse tin sludge after tin plating in MSA acid. I do my experiments with waste from this process and it is amorphous, but I do not know what is the main phase in. Do you think that it can be Sn(OH)4 or Sn(CO3SO3)2? Do you have an DTA/DSC of Sn(OH)4? Thanks
Technical University of Kosice, Faculty of materials, metallurgy and recycling - Kosice, Slovakia, Slovak Republic
April 26, 2018
publicly reply to Ivana Urban Kobialkova
A. Hi Ivana,
The insoluble tin colloid/sludge formed in MSA base tin plating solution was believed to be tin(IV) hydroxide, Sn(OH)4, arise from Sn(II) oxidation over time.
Sorry I don't have DTA/DSC ref of Sn(OH)4.
Regards,
David
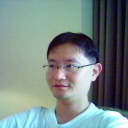
David Shiu
- Singapore
publicly reply to David Shiu
Q. Hello everyone, I am working on electroplating gold-rich Gold-Tin eutectic solder onto very small (tens of microns wide lines) areas of silicon substrates in a laboratory setting. My issue is control of tin deposit. I have no access to any sophisticated or large scale electroplating equipment, thus whole issue is quite problematic.
I built setup myself using potentionstat, glass beakers [beakers on
eBay
or
Amazon [affil links] on temperature-controlled hotplate with magnetic stirrer, Ag/AgCl ref electrodes and platinised Ti (gold plating) or Tin Sheet (tin plating) as anodes.
My substrate is coated with sputtered TiW and Au layers, and whereas gold plating tuns quite smoothly when it comes to plate tin (I use MSA-based solution without additives) it is nearly impossible to control- solution foams considerably during cycle, lots of sludge is formed and as a result I can't control thickness of deposit.
As I am new to the whole plating technology I would highly appreciate any help, comments, tips or whatever it is that would help me to deposit tin with some level of control. Thank you!
- Wroclaw, Lower Silesian, Poland
September 6, 2018
publicly reply to Mary Kaza
Q, A, or Comment on THIS thread -or- Start a NEW Thread