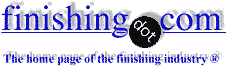
-----
Critical parameters for alkaline degreasing bath in hot-dip galvanizing
2001
Q. We are an environmental consulting company stated in Bogota, Colombia. We think you can help us in our effort of getting information about some critical parameters dealing with the alkaline degreasing bath in the hot galvanizing process of low carbon steel pipes of 6 meters length.
The sodium hydroxide content of the bath is about 12.13 kg NaOH per cubic meter of degreasing solution. There aren't any special substances (carbonates, phosphates, etc) added to the bath. The operation temperature is 82 °C and is kept by the injection of saturated water vapor. The solution that is carried out of the tank is replaced by the addition of fresh water at room temperature. There is only one water rinsing bath and it's carried out solution is replaced with fresh water at room temperature, too.
Our questions are referred to the following items:
Critical operation conditions of the bath.
Maximum grease content.
Maximum ferric oxide content.
Operation temperature range or interval.
Optimal temperature.
Special additives added to the bath. This is because of an actual trouble while degreasing pipes. After 15 minutes immersed in the degreasing bath, the grease remains on the pipe's ends, whilst the middle of the pipes are properly degreased. Have you any information about the type and quantity of emulsifiers (surfactants) used to solve this problem?
Bath general operation(Continuous, batching, etc).
Exhaust bath treatment.
Warming bath system.
Best regards,
Juan Carlos Matallana Arenas- Bogota, Colombia
A. You need a properly formulated, modern alkaline cleaning solution to solve your problem. The choice of alkalinity, complexing agents, emulsifiers, skimming equipment, etc. will affect all of the parameters you mentioned.
1. Maximum grease content - Do you want to emulsify the oil, or do you want to formulate the cleaner so that the oil can be skimmed off for recycling?
2. Maximum ferric oxide content - Not the major problem.
3. Operation temperature range or interval. Depends on #1 above, and the melting point of the oils in question.
4. Optimal temperature. See #3.
5. Special additives added to the bath. There are available hundreds of surfactants. Some will decompose within a few minutes of use in the bath, some will be useful over the life of the bath. Formulators are constantly searching for the best additives for the particular base metal, configuration of the part, the kind and amount of grease present, cost, etc.
6. Bath general operation.(Continuous, batching, etc). Depends on the selection of chemistry. -- Exhaust bath treatment. Treating the exhausted bath is complicated by the organic additives, but since you are having a problem with a straight caustic solution, we have no choice to address those issues. Warming bath system. Steam in steel coils is used extensively in the U.S.A. for alkaline cleaner tanks.
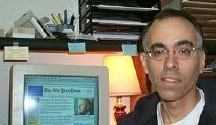

Tom Pullizzi
Falls Township, Pennsylvania
2001
February 21, 2008
by Kuklik & Kudlacek
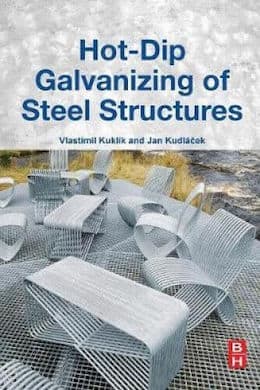
on eBay or Amazon
or AbeBooks
(affil link)
Q. We are a galvanization plant in Lagos, Nigeria. We guess you can help us in our effort of getting information about some critical parameters, calculations and chemical formulations dealing with the alkaline degreasing bath in the hot galvanizing process of mild steel.
The sodium hydroxide content of the bath is about 48%w/v of degreasing solution(450 g/L); wetting agent (5 g/L); after 85 °C is reached sodium metasilicate
⇦ on
eBay
or
Amazon [affil links]
(150 g/L) is added 50 kg per hour to the bath; The Capacity of Tank is 82500 L. There are two water rinsing bath and its carried out solution is replaced with fresh water at room temperature, too.
Our questions are referred to the following items:
Critical operation conditions of the bath.
Maximum grease content.
Maximum ferric oxide content.
Operation temperature range or interval.
Optimal temperature.
Special additives added to the bath.
Bath general operation, Maintenance (Continuous, batching, etc).
Exhaust bath treatment.
Warming bath system.
optimum composition and formulation of the compounds of the bath
optimum calculation of the composition and formulation of the compounds of the bath
Best regards,
employee - Lagos, Nigeria
June 1, 2009
A. Hi, Lilian. Please, if possible, phrase your questions in terms of the responses that Tom has already offered. After he already attempted to answer those exact questions, simply cutting & pasting the same questions in a second time is rather unproductive for all of us :-(
Perhaps the central point of Tom's answer was that the suppliers of metal cleaning solutions have invested decades in the development of optimum formulations, and they retain these formulations as trade secret. You can, if you wish, take advantage of their work by buying their proprietary cleaning solutions.
If you want to formulate your own chemistry, a good source of information would be expired patents, text books, a computerized search of published literatures, etc., but there is a lot to it: surfactants, builders, buffers, detergents, sequestering agents, chelates & complexers, whether you can you employ electrocleaning, and much more. These are broad topics which must be covered in a book because it is impossible to distill it down to a length appropriate to an answer here.
If you can find a copy, the Garden State Branch AESF "Electroplating Course Manual" has an excellent 16-page chapter titled "Fundamentals of Metal Cleaning" which explains emulsification, detergents, diphase solvents, acidic cleaners, inhibitors, the effect of pH, saponification, wetting, deflocculation, chelating/sequestering, buffering, and testing for cleanliness.
The "Electroplating Engineering Handbook" .
is more readily available around the world, and has a nice 12-page chapter on alkaline cleaning. Indeed most plating textbooks offer at least some info on the subject.
Best of luck.
Regards,
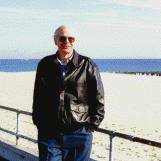
Ted Mooney, P.E.
Striving to live Aloha
finishing.com - Pine Beach, New Jersey
Q. Please tell me why we are using more alkali degrease at High Temp.?
And Which are reactions takes place like saponification, emulsification?
Can we use acid pickling before Alkali Degrease for rust removal, as I heard that we cannot use but, for rusty part we are using one product for pickling before loading.
I want to know. Please clarify on above issues.
Automobile - Gujarat , India
August 9, 2010
A. Hi Anand. Please try to fully detail your situation. I don't know whether you are claiming that you have raised the temperature of your alkali degreasing process, and now it is consuming more chemicals (for one thing it may be cleaning better, thereby exhausting more cleaning chemicals) or whether you are asking why people are more likely to do their cleaning at high temperatures (because such chemical reactions proceed faster due to the extra thermal energy).
Saponification occurs if the greases are animal fats, not if they are petroleum based. As for emulsification and other mechanisms, what, if any, chemicals besides alkali are in your cleaners?
Acid dipping is usually done after alkaline cleaning, not before (except for scale-breaking & pickling by the steel mill). It is possible to do acid cleaning but, except in special situations, it is more expensive and troublesome than doing alkaline cleaning followed by acid activation.
Regards,
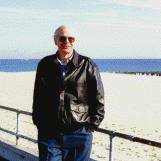
Ted Mooney, P.E.
Striving to live Aloha
finishing.com - Pine Beach, New Jersey
Q. In Degreasing, what happens during removing the grease & oil from metal body. Explain with reaction?
Atul Jaradstudent - Pune, Maharashtra, India
January 30, 2016
(affil links)
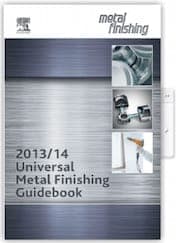
free pdf is currently available from academia.edu
A. Hi Atul. We've added a link above to the on-line edition of the Metal Finishing Guidebook, which will explain a lot for you. Cleaning is generally not a single reaction but a combination of many simultaneous processes as explained above, including detergency, solvency, emulsification, saponification, sequestration, etc.
But please get back to us with what grade you are in, and what your project is. Good luck.
Regards,
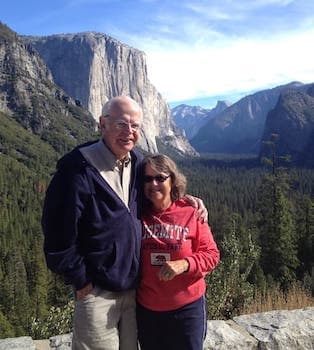
Ted Mooney, P.E. RET
Striving to live Aloha
finishing.com - Pine Beach, New Jersey
January 2016
Q. I'm currently doing a study on batch galvanising and was looking into the degreasing stage of the process. I was wondering if you could possibly shed some light as to why the optimum temperature for degreasing agents to operate is between 80-85 °C?
If anyone could provide some scientific knowledge to the subject that would be much appreciated.
- England, UK
December 22, 2016
A. Hi Martin. The thing is, 80-85 °C does not give optimum cleaning, 100 °C would be better because of greater chemical activity. But operating a cleaning bath at boiling temperature greatly increases the energy cost because of the rapid evaporation, and leads to the need for greater exhaust requirements as well, and may preclude the use of certain very useful materials of construction like polypropylene. So somewhat lower temperatures are often employed, and 80-85 °C is a pretty common compromise value.
Regards,
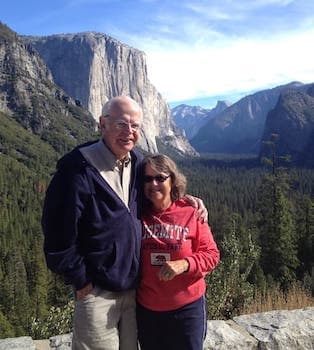
Ted Mooney, P.E. RET
Striving to live Aloha
finishing.com - Pine Beach, New Jersey
December 2016
Thank you for your reply.
- England, UK
December 22, 2016
Q. I would like to know if I can use caustic soda ⇦liquid caustic soda in bulk on Amazon [affil link] alone as a degreasing agent for hot dip galvanisation process.
Essie Atholere- Kampala, Uganda
August 15, 2017
A. Hi Essie. caustic soda ⇦liquid caustic soda in bulk on Amazon [affil link] is the principal ingredient in alkaline cleaning, and could be used alone, but that is far from ideal ... as you can read in this thread which we appended your inquiry to.
Regards,
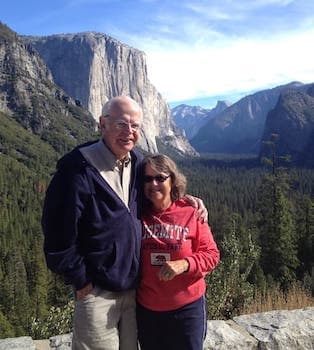
Ted Mooney, P.E. RET
Striving to live Aloha
finishing.com - Pine Beach, New Jersey
August 2017
Using Grass as a Degreasing Agent
Q. Dear Team
I work for a new galvanisation plant. We are currently doing electroplating.
We put greasy nails in a blaster and then added grass followed by 18 liters of hydrochloric acid. The nails became degreased and we did galvanisation. Is there any effect of using grass on the aqueous solution in the kettles?
- Kampala, Uganda
August 17, 2017
A. Hi Essie. Although you used the word 'grass', you probably are referring to a material which is more like hay or straw than soft green suburban lawn grass. If it rinses well, with no stains and no troublesome little flecks stuck to the parts, my guess is that it's not a problem.
Regards,
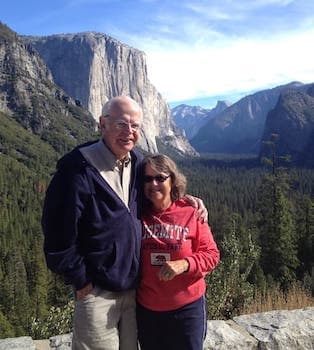
Ted Mooney, P.E. RET
Striving to live Aloha
finishing.com - Pine Beach, New Jersey
August 2017
Q. DEAR TEAM
I currently work for a plant manufacturer in the finishing industry. Is there a set number of turnovers needed for de-greasing agent for a set volume per hour? I need to spec the pump needed.
Regards
- Heidelberg, Gauteng, South Africa
June 6, 2019
June 2019
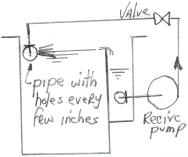
A. Hi AJ. There are many different ways to formulate a metal cleaning solution, but if you are speaking of a hot alkaline cleaning tank, it is rather common practice to build them with a grease trap and riffle pipe as illustrated. In this case you want to drill holes in the riffle pipe that are large enough to not plug frequently, and closely spaced enough that they sweep the grease off the whole surface, but not with such pressure that they could squirt solution out of the tank. An all iron centrifugal pump, perhaps 2 GPM for each foot of tank length might be good.
Regards,
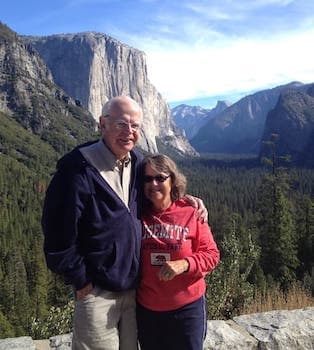
Ted Mooney, P.E. RET
Striving to live Aloha
finishing.com - Pine Beach, New Jersey
Q. Thank your quick answer Ted
It will be a hot alkaline degreaser. We do build the tanks with a overflow weir, and an oil skimmer running along the top of the weir. We then circulate that water through the tank, dosing and adding make up water as needed. I saw an article somewhere that said you need at least about 10 turnovers on degrease tank if it is moderately clean, meaning to move the entire volume 10x per hour.
Regards
- HEIDELBERG, GAUTENG, SOUTH AFRICA
June 10, 2019
A. Hi AJ. I've heard of such rules of thumb for filtering plating tanks, but am not familiar with any such guideline for alkaline cleaners.
Most plating lines use a soak cleaner tank followed by an electro-cleaner (sometimes with a rinse between). The pump for the riffle pipe on the soak cleaner which I described probably meets or exceeds 10 turnovers per hour, but many plating lines have no recirculation pump at all on the electrocleaning tank.
Regards,
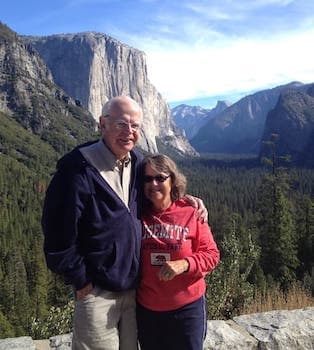
Ted Mooney, P.E. RET
Striving to live Aloha
finishing.com - Pine Beach, New Jersey
June 2019
Q, A, or Comment on THIS thread -or- Start a NEW Thread