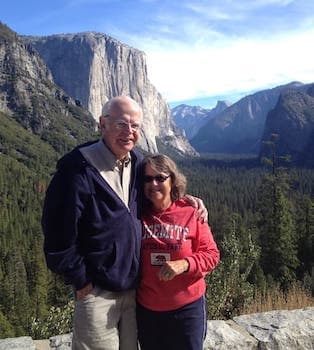
Curated with aloha by
Ted Mooney, P.E. RET
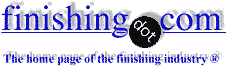
The authoritative public forum
for Metal Finishing 1989-2025
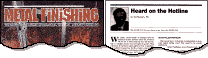
-----
Black spots on anodized surfaces

May 15, 2022
Q. Hello, we receive from our customer 6060 aluminium parts to be anodise. Customer use cotton gloves. We receive boxes of 120 parts, and we anodise them in three batches of 40 parts. For some reason we have an issue somewhere, because many times we have zero parts with corrosion in two batches, and in the last batch appear corrosion as you can see in the attached pictures.
Could you please advise what can make appear this corrosion?
Juraj Horváth- Slovakia SK
A. Hi Juraj
It is almost impossible to know what conditions the parts were subjected to prior to your receipt of the parts. For example these parts may have been wet and then stacked up and left to dry. They may have been in a toxic environment or even left outside...
We as anodizers almost never know, and yet many times the blame for the defect falls back on us. You may already be aware that anodizing enhances or magnifies any type of flaw that is in the material prior to the anodize process. As for the parts in the pictures you supplied, it most assuredly looks to be corrosion of some sort. If the parts were given a grain or time save sanded prior to anodize, it is evident that the grain texture was not sufficient to remove it. At this point there is not much you can do because a strip and reprocess is probably not going to hide it any better. Something has to be done to change the surface texture. The disappointing part is that it was not noticed prior to anodize where your person racking the part might have noticed it and brought it to someone's attention.
My first rule of thumb is always go back and look for any unprocessed parts and see if that condition exists. By finding unprocessed parts in that condition you can then approach your customer and make them aware of the parts and how they were received and what to expect as an outcome for a finished part.
supervisor - Cicero, Illinois
Saporito Finishing Co.

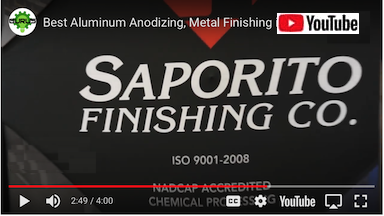
May 16, 2022
A. Hello,
There are several types of corrosion such as atmospheric corrosion, finger print corrosion, paper corrosion, traffic marking/fretting corrosion. It seems (to me) atmospheric corrosion but I am not sure due to not knowing the story of these corroded parts. As advice, the parts which you delivered should be monitored before loading. Despite lack of any trace of corrosion over profile before loading that does not mean these parts won't corrode. Actually, corrosion issue is literally metallurgical reaction. I have an abstract which includes corrosion defects and solutions. I can send you this paper if you want.
Good luck
- sakarya, Turkey
May 21, 2022
----
Ed. note: Apologies everyone, but this is a public forum -- not a private matchmaking service. For each poster with a problem there are a hundred or more readers who are following the discussion whom we do not want to disenfranchise. For this and other reasons, we don't put readers into private contact. If anyone wants to share a non-commercial document with all the readers rather than one specific reader, we'd be happy to put it into our on-line library.
A. Hi Juraj.
I've been seeing a lot of mill finish defects on extruded alloys in the last couple years, even from sources that are usually dependable.
Some of them are superficial defects that can be etched off, though that sometimes leads to worse finishes. When I catch them in time, I suggest red scotchbrite pads with Liquinox lab soap to fix the surface- but if the defect goes too deep, you may not be able to fix it without dimensional change.
I still recommend using red AlOx scotchbrite pads to break the "mill finish" of your parts so that you can reduce etch time and potential unwanted etching or pitting.
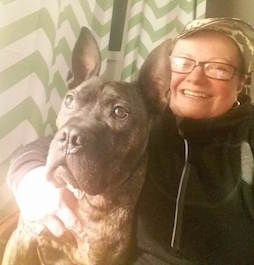
Rachel Mackintosh
lab rat - Greenfield, Vermont
May 25, 2022
⇩ Related postings, oldest first ⇩
Q. Hello:
I'm working on chromic acid anodizing plant (22 volts, 45 g/l free chromic acid). The sealing is performed using dilute chromates process. the material treated is wrought aluminum alloy 2024 and 7075 series. The problem I have is the presence of black spot on the surface of coating . The examination of the surface is done after sealing by X15 and X30 magnifier.
I ask if anyone may help me to understand the probable origin of these black spot and what is it?
Thank you for any help,
Said Ziane- Montreal, Canada
2001
A. This problem of black spots may be due to corrosion before anodising.
How do the parts come in to you - are they dry (not oiled)?
Are they degreased and left hanging about?
Try answering these questions and if you find the answer is yes to either of them you may have found your problem.
Walk the line with then and see if there is any step were corrosion could happen.
The corrosion has been halted by the anodising process but the parts need a concession, strip and re-process if you have tolerances to allow for the loss of base material from the strip op.
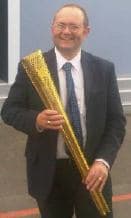
Martin Trigg-Hogarth
surface treatment shop - Stroud, Glos, England
2001
June 30, 2008
Q. Hey all
Did you have any luck?
We have 1 mm anodized aluminum sheet which develops black spots.
We have not found the cause. We degrease the sheet with an acid based hydrocarbon degreaser, but if there were any imperfections, the acid should make white spots. it only seems to occur when we send the goods to a warmer region.
Dishwashing liquid removes the spots. is this because it is alkaline?
Bahrain sheet techies think it is foreign matter on the sheet which in some way is removed after anodising and leaves small mill finish spots which in turn corrode.
How can we neutralize the corrosion in an economical way?
All suggestions welcome
Regards
signage - Melbourne, Victoria, AUSTRALIA
July 3, 2008
A. What is the thickness of the anodic coating? Is this thickness uniform all over the thin panel? Dimensions of the panel? How is it sealed? How reliable is the seal? Does it pass the ASTM B136 seal test?
It is very difficult to get thickness on thin panels.
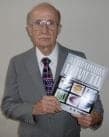
Robert H Probert
Robert H Probert Technical Services

Garner, North Carolina
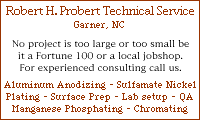
A. Hi Fons,
I would like to ask more questions about the nature of the black spots. For example, are they smooth and hard or of a "fluffy" nature like corrosion products often are? However, here a some comments and suggestions.
Perhaps the Bahrain techies are right and there spots on the aluminium which the acid fails to remove. If so, perhaps a light alkaline etch might be effective.
My own suspicion is that the problem lies in corrosion occurring in the sealing stage. Sometimes intermetallic compounds within the aluminium form electrolytic cells causing holes (pits) in the coating. The effect is usually most severe if racks have electrical contact with tanks and cooling coils. Titanium racks (where electrical contact is unavoidable) can also exacerbate the problem. However the electrical potential from the intermetallics can be such that corrosion occurs with the surrounding aluminium.
Actions to take are to electrically isolate racks from tank: strips of plastic will do the job. Keep the seal water at a low conductivity.
Whatever the cause, as the problem only happens when you send parts to hot climates, I wonder if they are completely dry when packed? If not, you will be dispatching them in a mini corrosion cabinet complete with heating to accelerate any corrosion. This will be particularly troublesome if you are wrapping in polythene.
Of course, even if you can avoid the problem during transit, the question of whether the product will corrode in use remains. The questions raised in the previous reply by Robert Probert take you back to fundamentals.
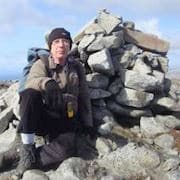
Harry Parkes
- Birmingham, UK
July 7, 2008
September 11, 2009
Thank you Mr Parkes and Mr Probert for your response. Sorry it took a year to respond but I am new to this internet game.
The shipping in a mini corrosion chamber probably was the culprit. these aluminum panels had acrylic faces on them, which in turn sealed in moisture and slightly moved around during transport thus creating bold spots at the high points on the alum sheet, moisture got in and the rest is history. happy days. we inserted paper in between and no more spots.
Stay tuned for my next adventure into the insane.
sign industries - Melbourne, Victoria, Australia
Q. Gents
I have problem in black spots occur after Anodize the position of black spots is random though on extrusion profile I have quick chat with an expert in Anodizing process he said that this come from extruded operation I not 100 percent believe him yet cause I think the Anodizing process parameter is once of root cause.
If an expert in Anodizing process suggest is right what should I could improve or avoid?
Thank you for your cooperation.
- Lamphun , Thailand
July 20, 2009
A. If your anodizing expert is really an expert, you should believe him - unless you have a strong reason to not believe him.
Guess what-he is correct. The black is highly probably the release agent used on the extrusion die. Sometimes you can not see it because a very thin coat of aluminum is smeared over it. The etch process prior to the anodizing step will remove that film and expose the black material.
The extruder can control this, but many are so interested in product out the door that they care very little about the problem until they lose customers.
I hate extrusions for this reason and have refused to do some customer's work unless they agreed to accept the horrible product. With the right light and the right angle, you can spot many of the spots before they are processed. They are just a lot harder to find.
James Watts- Navarre, Florida
July 23, 2009
? More information: alloy, titanium or aluminum racking, material of dye tank stainless or plastic, process sequence, free acid, dissolved aluminum.
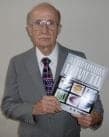
Robert H Probert
Robert H Probert Technical Services

Garner, North Carolina
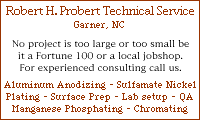
July 23, 2009
Q. How about chemical composition in Alloy? I always found it in Al6061. Do we need to look into Alloy composition?
Nakaret Rukstaya [returning]- Lamphun, Thailand
August 17, 2009
Q, A, or Comment on THIS thread -or- Start a NEW Thread