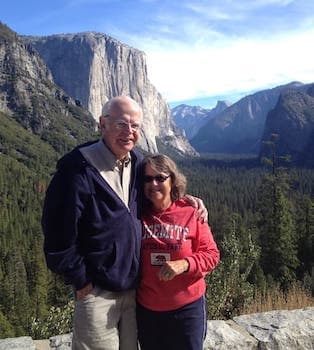
Curated with aloha by
Ted Mooney, P.E. RET
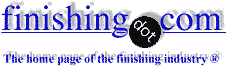
The authoritative public forum
for Metal Finishing 1989-2025
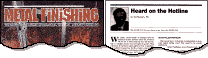
-----
Requirements for Passivating Stainless Steel
I am in the Aerospace Industry in Alaska and working on expanding my capabilities in overhauling some of the components used in my system. In overhauling an engine isolator assembly there are some stainless steel plates approximately 4.5 by 6.25 by .5 inch thick that need to be passivated for return to service.
My questions are:
1. What equipment and materials are needed to passivate these plates?
2. Is the cost reasonable enough to do this in low volume or would it be preferable to find a plating shop to send these to and not attempt the process?
- Anchorage, Alaska, USA
If you are only planing to passivate a few parts, you are better off taking them to a plater. While passivation is a simpler process than most plating processes (no current is applied), you have to research to find which is the best solution make-up, temp. and immersion time for your stainless steel alloy(s). In addition passivation solutions are highly acidic, which brings up safety/storage issues. Lastly, many passivation solutions contain sodium dichromate which may pose disposal problems. For more information on passivation check out ASTM A967.
Good Luck,
laboratory. - Baltimore, Maryland
Brian:
For small quantities you can go to a job shop, or you can safely set up a small lab process with a citric acid system. This allows you to do it safely and without environmental hazards. Let us know if you need help with your particular need.
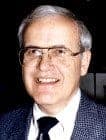

Lee Kremer
Stellar Solutions, Inc.

McHenry, Illinois
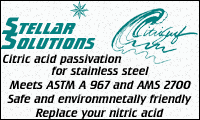
If you want an oversight as to the passivation process for aerospace application, I recommend you review
AMSQQP35
[canceled] (Society of Automotive Engineers). Depending on the size and complexity of your parts, it is possible to do this as a "bucket operation" . The most common Type of passivation is nitric acid, but depending on the base alloy of your hardware, you will probably need to use an elevated temperature.. Some of the solutions require, again depending on alloy type, require a chromate addition to the nitric acid, which gives you a disposal issue. Other thing to consider are existing coatings, braze joints and complex geometry (entrapment) that will require masking or may prelude passivation altogether.
Are you an FAA Repair Station and /or work to Service Manuals / Bulletins? These may limit what "type"of passivation you are permitted to use. Finally, you may have testing requirements...from a simple copper sulphate
⇦ this on
eBay or
Amazon [affil links] swab up to immersion, humidity and / or salt spray corrosion resistance tests.
- Mason, Ohio
A couple follow-up questions re: passivation (nitric acid) of stainless steel surgical assemblies. 1. Is it necessary to place individual components and sub-assemblies through passivation prior to final assembly? 2. Can a complex instrument be passivated as long as subassemblies are in an "open" position? (We want to ensure that all threaded areas, bolts, "nooks & crannies" etc. receive adequate treatment.) Since these instruments are sterilized as a final assembly, would it be reasonable to passivate the final assembly as such?
Thank you.
- Traverse City, Michigan
February 11, 2009
Hi, Karen. If the passivating solution can reach all of the important surfaces, and if there is only one type of metal involved, I think passivating the item as an assembly should be fine.
Regards,
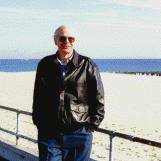
Ted Mooney, P.E.
Striving to live Aloha
finishing.com - Pine Beach, New Jersey
February 11, 2009
Thank you, Ted. The component metals used in the assemblies are
300 series stainless steel (303, 304, 316). Does this pose an impact, having the varying grades of ss?
Thanks.
- Traverse City, Michigan, USA
February 12, 2009
All of these types of stainless would use the same passivating solution; I don't think it is a problem to passivate as an assembly, but let's see if other readers have comments.
Regards,
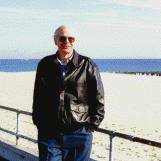
Ted Mooney, P.E.
Striving to live Aloha
finishing.com - Pine Beach, New Jersey
February 13, 2009
Karen,
In theory, any two dissimilar metals in contact in an acid bath can cause a galvanic reaction, even different grades of stainless. However, I would not expect any meaningful galvanic reaction to actually occur if your assembly is all
300 series grades.
There's probably no problem with passivating your parts in the assembled state, just be sure you rinse it thoroughly after the chemical baths.
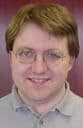
Ray Kremer
Stellar Solutions, Inc.

McHenry, Illinois
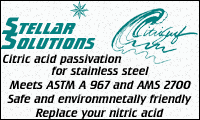
February 24, 2009
My opinion and it is opinion only. For mating parts, I think that they should be passivated before assembly. If you use any steel tools during assembly, then the assembled part should be passivated again. Rinsing can be extremely difficult for an assembled part. Consider using a dilute solution of bicarbonate of soda after the first rinse to neutralize any remaining acid.Then use a DI hot water rinse after the bicarb rinse. Dry immediately to avoid spotting.
James Watts- Navarre, Florida
February 25, 2009
Q, A, or Comment on THIS thread -or- Start a NEW Thread