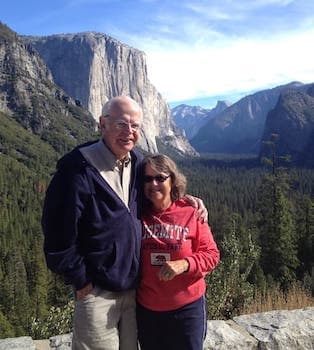
Curated with aloha by
Ted Mooney, P.E. RET
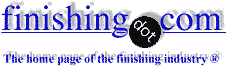
The authoritative public forum
for Metal Finishing 1989-2025
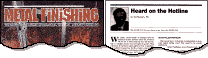
-----
What to plate new Aluminum Kitchen Appliance with?
Q. Hello! I have a question and would love to get some of your advice. I have been reading a lot of your posts and learning a lot.
I have a piece of kitchen equipment that my brother and I invented for food processing. We have have tested various coatings including nickel plating and passivation. With passivation we put the component in the dishwasher within 1-4 wash cycles it would turn dark grey/black. Right now we have electroless nickel plated coating on there that works well for dishwasher safe, looks beautiful, etc, but it is a very expensive process and we have a lot of defects/scrap.
If you were using aluminum for a food preparation product, would you recommend anodizing or perhaps even a "hard anodizing". I was reading some prior posts and hard anodizing might be an option for us to test. If we did anodizing or hard anodizing, would it be dishwasher safe? From one of the posts it seemed like eventually anodized coating would run out as well and also yet another post said it would not be dishwasher safe.
Any other recommendations? The other thought is to go with anodizing and make clear labeling to show the parts are not dishwasher safe.
Chris
Inventor, Engineer - Chicago, Illinois
October 15, 2016
A. Hi Chris. Anodizing isn't dishwasher safe. Some hard anodized cookware now claims to be dishwasher safe but it is by virtue of additional non-stick coatings; and even then, many customers are complaining on Amazon that the life is short -- plus, hard anodizing will be gray not shiny.
You proven to yourself what the right finish is, wibutth two problems remain: excessive defects and high cost. Reducing the defects is the focus of today's quality assurance systems, and should substantially reduce the cost as well.
Just personal opinion, but I remember buying rooftop carriers for my car from K-Mart for $19; it's what everybody did ... then times changed, and I haven't seen that junk in decades. Instead we have Thule "rooftop systems" that start at over $200, with another $150 for one accessory, and $175 for another, etc. We are in an age/cycle of panache and if you offer a cheap, low quality, non-dishwasher-safe kitchen accessory, somebody will copy it, fix it, add pizazz, and sell it. Work is more fun when you can concentrate on keeping your product the best it can be rather than the cheapest. Again, only personal opinion, but take advantage of the times because they'll change :-)
Regards,
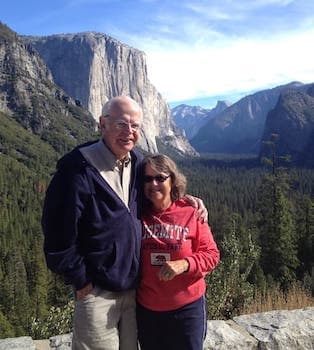
Ted Mooney, P.E. RET
Striving to live Aloha
finishing.com - Pine Beach, New Jersey
Q. I really appreciate your response and guidance. We will continue to work with the supplier to improve quality.
The issue they have is just with this 1 part (out of 5). The coating on the inside is where they run into problems. The test I am going to conduct with them next is to polish the inside of this component prior to coating it. I believe that will improve the results.
Any other thoughts or tips on how to fix this problem that comes up from time to time?
Chris Vaisnoras [returning]- Chicago Illinois
A. Hi again. I think you are on the right track and that mass finishing (very low labor cost) will solve your problem of polishing the interior, and may (I'm not sure) provide a sufficiently polished surface for the outside without need for further buffing. Must the very sharp corner between the interior and the machined face of the flange area be maintained or is it okay if it becomes a bit rounded? Look into "drag finishing" as a possible method for the mass finishing if it is necessary for you to mass finish some areas more than other areas.
Regards,
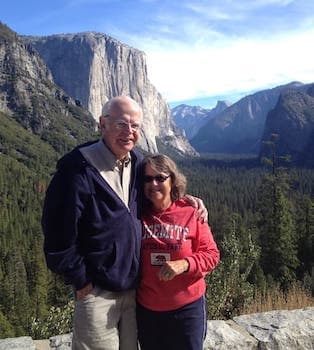
Ted Mooney, P.E. RET
Striving to live Aloha
finishing.com - Pine Beach, New Jersey
Q. So I met with a coating company here in Chicago and they stripped the part down. They are guessing with the brightness of the part, how the coating came off in their process, and the copper base they felt they saw ... that this part was never electroless nickel plated but that it was electrolytic nickel plated.
When they recoated (without doing any surface treatment), the inside coated perfectly... And the outside coated ok but not shiny because it wasn't polished.
Any ideas? Tomorrow we are testing their EN Process on an original polished part, and a stripped part that was polished. What they are concerned is that they won't get the brightness that our originals have.
- Chicago, Illinois USA
A. Hi. Electroless nickel will not be as bright as electrolytic nickel plus chrome plating, but should be pretty bright if optimized. Bright electrolytic nickel plus chrome would be the flashiest and could be tried as well. But here you'd need to be real careful because most garden variety plating would not hold up to automatic dishwashing for long; you'd need to get automotive quality plating.
Luck & Regards,
Ted Mooney, P.E. RET
Striving to live Aloha
finishing.com - Pine Beach, New Jersey
Poor coverage on interior of nickel plated Aluminum Casting
Q. I posted this question earlier. I thought our supplier was doing Electroless Nickel but they are doing a Nickel Chrome (copper base). Basically they handled everything, it came out totally perfect for last 4 years, and they went out of business and a new supplier took over and now we have a big problem. So I apologize for my newbieness. I have learned a LOT in the last 6 weeks...
So... here is where we are at.
Problem - black spots, and red type spots on the internal dimensions of a part. The outside coats completely fine, the inside has defects like you see in Photo #1. This is a photo only of the inside of the part. Our previous supplier that went out of business did them perfect as you see on the left and I have never been involved because of this.
Current process - See the photo below, Photo #2. This is how they are being fixtured for the process.
I spoke with 2 different coating people. They suggested that either we add an "anode" to the inside of the process or we do something where we add additional current to the inside of the part. They felt the inside had enough space where there should be enough solution/flow to just try adding 2-4 more touch points of current. Basically there would be a bar that extends into the middle of the part and then 2 copper wires that extend from it to touch the part in 2 locations where the trouble spots are. This ideally creates enough current to plate it properly.
Please comment to make sure I am in the right direction. I meet with the plating supplier on Monday and hope to look like I know what I'm doing and proposing the best solution to test out. The next solution would be to put an anode but that seems more complicated with the part geometry.
Chris Vaisnoras [returning]- Chicago, Illinois
December 9, 2016
A. Hi Chris. In my opinion additional contact points on the interior of the part will not help; the aluminum casting probably carries enough current for proper plating. But "internal anodes" will definitely help. The ions essentially follow the path of least resistance and without an internal anode it's a much shorter trip to the exterior of the part than the interior.
Regards,
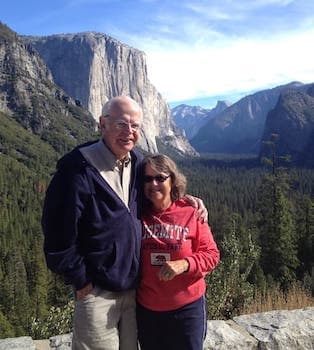
Ted Mooney, P.E. RET
Striving to live Aloha
finishing.com - Pine Beach, New Jersey
Q. Got it. So for the ultra novice learning at the moment that will need to run a test this coming week.... what should my anode look like, be made of, and how should it be hooked up? Anything I should be careful of?
I did some searching, google learning, etc and I believe it should probably be a nickel anode and something insulated so it doesn't touch the part but also exposed to the solution. Then it should be large enough so that it can create the desired effect on the inside of the hopper.
Any thoughts or guidance would be well appreciated. The supplier I am working with is not so cooperative but since I'm here on their doorstep, they are working with me to sort this out.
- Chicago, Illinois
A. Hi Chris. Your postings prove you're a smart guy and fast learner, but I think such a problem would be best addressed by an experienced plating consultant, not an "novice" trying to manage a "not so cooperative" plating shop. If your company can retain a consultant for a few days, the "not so cooperative" shop will usually change their ways because they can't snow people who know as much as they do :-)
Ideally you would use a DSA (dimensionally stable anode) made of platinum-clad niobium or possibly platinum clad titanium. Shops who plate aluminum alloy wheels will probably be familiar with these. The platinum will not de-plate or oxidize to useless as most other metals will, and the nickel values would come from the solution and the other nickel anodes. But these are very expensive and, since this is development work, I would try a nickel anode for starters ... but it will dissolve away on you and need to be replaced. It must be connected to the anode bus bar; for development work an alligator clip jumper cable might do.
Electroplating occurs in accord with Faraday's Law: for every two electrons, one ion of nickel in solution will deposit as a nickel atom. The basic problem is that electricity sort of takes the path of least resistance, and most nickel ions don't make it all the way to the inside of the part, but are captured by high points, closer areas, etc. Get an anode (connected to anodic current) into that recess and you get plating there. Optimizing the thickness distribution will probably be work though.
If you can find a shop that chrome plates car wheels, they will know how to do everything from auxiliary anodes to automotive quality plating.
Regards,
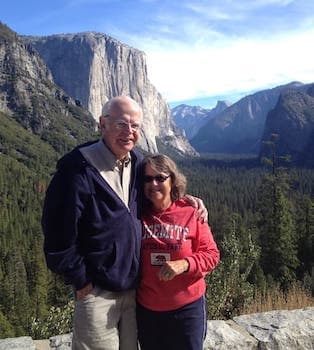
Ted Mooney, P.E. RET
Striving to live Aloha
finishing.com - Pine Beach, New Jersey
Spec for copper-nickel-chrome plating?
Q. So, yes, we took your advice and what we are actually going to do is find another supplier.
All that said, does anyone have a pretty standard Nickel Chromium specification that I can send/add to my print for my parts that I can use to send to a number of prospective suppliers that would do this? I'm hoping this is something pretty standard and easy...
- Chicago, Illinois
February 23, 2017
on eBay
(unavail on last check) or
Amazon
(Available on last check)
(affil links)
A. Hi again. See if by chance you can get from nasf.org a copy of the MFSA Quality Metal Finishing Guide for Copper-Nickel-Chromium Coatings. It's a short booklet, about 28 pages, covering just the essentials. It is sometimes listed on Amazon. You could also check eBay ⇨.
And sometimes in this rapidly changing world you can find it on line. It will tell you everything you need to know to spec out what you require.
Regards,
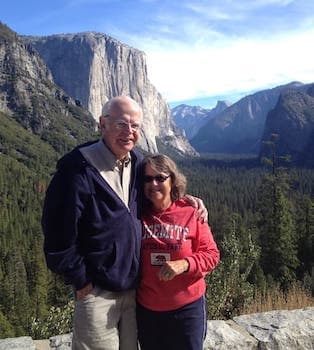
Ted Mooney, P.E. RET
Striving to live Aloha
finishing.com - Pine Beach, New Jersey
Q, A, or Comment on THIS thread -or- Start a NEW Thread