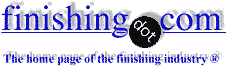
-----
Rumor - EN Adhesion on Bar Stock
I have recently had some adhesion problems with EN on 1215 steel. Obvious possible causes aside, I was told that when plating bar stock, you need to remove a significant amount of material from the exterior of the metal. During the forming process, a layer of metal can be created that causes problems with plating. Is there any truth to this?
- Kansas City, Missouri
"SIGNIFICANT" is a very wide open word. Actually, for optimum, when you see a bright machined metal, you should have no problem. If you are plating raw bar stock, it does have a variable depth of "mill scale". This is an oxide layer and you will suffer problems with adhesion. It will require a pickle step which is more aggressive than an acid etch. The quickest way is to abrasive blast the stock.
Finally, was ther an "L" after the 1215 or was it labeled "free cutting"?. These are alloyed metals and frequently require special handling. Unfortunately, most machine shops do not realize that it makes a difference to the plater, and regularly forget to pass that information on.
- Navarre, Florida
I am currently removing 1/16" (.063) per side from the stock. I was told to remove 1/8" (.125) per side to be safe. I will check on the alloy.
Thanks.
- Kansas City, Missouri
One way to find out if it is required (I do not think so). Take some drops of your bar stock, take off a pass of 0.030,
0.040, 0.050, 0.060, 0.080, 0.100 and 0.125 in parallel strips of say 1/4 inch wide and full length of the drop.
Plate a dozen of these and you will soon find out what is required.
First, I would look and see if there is any silicon in your cutting fluid. If there is, get rid of it.
Next, is there any silicate in your caustic cleaner after machining. If so, rinse sooner and better of switch to a non silicate. The plater can not help you if either of these are present.
Finally, try two other platers.
- Navarre, Florida
Q, A, or Comment on THIS thread -or- Start a NEW Thread