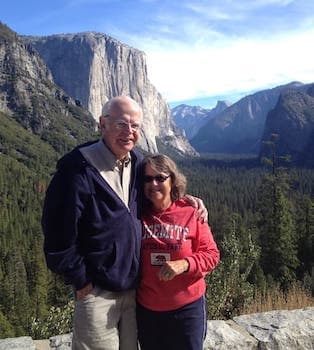
Curated with aloha by
Ted Mooney, P.E. RET
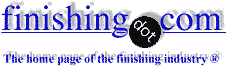
The authoritative public forum
for Metal Finishing 1989-2025
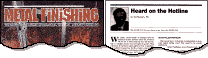
Thread 102/86
Nickel plating bath is plating slow and parts are dark?
Q. In my electroplating tank I am using nickel sulphate, nickel chloride and boric acid solutions. The brighteners used is a combination of Nimac 8127PR, Nimac 33, Nimac 14, and Nimac 12A. The PH is always 4.7 . It is supposed to be 3.9 . Using 50 amps per load of 25 parts, the voltage goes up to 3 volts only, and the parts I've been plating are getting very dark. It plates very slow, and it's never bright.
So...what's my problem with my plating bath? Can you please give me a solution to this problem? Thank you in advance!
- Dearborn, Michigan
2001
publicly reply to Karen S
A. Hi Karen,
You have contamination from copper, tin, aluminium in your nickel solution. You not mentioned about orange surface so the problem should not be iron or too much brightener. You can try to eliminate this if you bring corrugated steel sheet with a low current about 0,3 A / dm2 over one night maybe more you will remove all contamination from your solution. With this method you also remove some brightener and wetting agent because the ampere by hour the solution will be electro cleaned. So what you should do after this removing is to do a analyse by your nickel solution. A good idea is to filter the solution with charcoal cartridge and NP purifier each week.
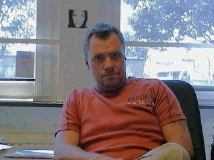
Anders Sundman
4th Generation Surface Engineering
Consultant - Arvika,
Sweden
publicly reply to Anders Sundman
A. You could have Cu, Pb, or Zn contamination, but I doubt it. Try checking the current density; I suspect it is on the low side of where you want to be.
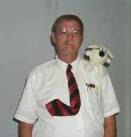
James Totter, CEF
- Tallahassee, Florida
publicly reply to James Totter, CEF
A. The first thing to check is the current. Do you have the anode and cathode set up right. Also your pH is very high for a bright nickel solution. The higher the pH the more active the brightener. If you have very high brightener your parts would be black and the plating rate very slow. Run a hull cell to check the chemistry. If the hull cell is also black you should do a carbon/peroxide treatment of the nickel solution and than run a hull cell to make sure you removed all the brightener. Than add back the brightener and recheck everything.
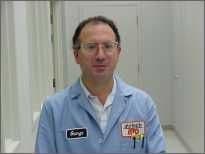
George Shahin
Atotech - Rock Hill, South Carolina
publicly reply to George Shahin
A. Try sulfuric acid 25% to get the pH down.
Then run a Hull cell to find if you have a bright spot in the current density range.
The slow rate would say not enough amps, the darkness may be contamination it may be just too low a current.
If you don't have a Hull cell just play with a jig of parts and start at 55 A per jig and see what they look like after 5 mins, then try 60 A on a fresh jig see what they look like after 5 mins - just play around you should start to see some effects.
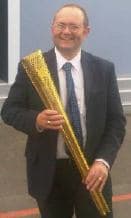
Martin Trigg-Hogarth
surface treatment shop - Stroud, Glos, England
publicly reply to Martin Trigg-Hogarth
A. Your amperage seems to be too low, check your bath temperature, this is also a factor in a slow plating bath. In my opinion, You do not have contamination in your bath.
Regards,
- Mcallen, Texas
publicly reply to Joel Garcia
A. Dear Karen,
As per your observations your pH is always 4.7. For that, check for your boric acid content and adjust pH using sulfuric acid. Regarding you voltage problem, see whether you have sufficient anode area, is your rectifier capacity enough, calculate surface area of components to be plated and plate at 3.0 to 4.0 a/dm2, and check then for your contacts. After these checks please find out whether you operate at optimum temperature and finally go for eliminating your bath contamination.
Regards,
- Kitchener, Ontario, Canada
publicly reply to Venkat Raja
A. With due weight to be given to all the above, which I am sure you have already had sorted out before coming to finishing.com, let me tell you what my friend and colleague Mr. Anil found out.
The brightener system was Coumarin based and did not react with any of the above treatments. He then tried an EDTA treatment which set the bath right. Add 20 ml/lit to a hot bath and air agitate for two hours.
For a full effect, also high current dummy plate with a small cathode area and large anode area for 8 hours.
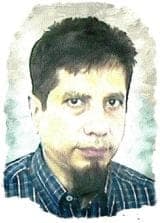
Khozem Vahaanwala
Saify Ind

Bengaluru, Karnataka, India
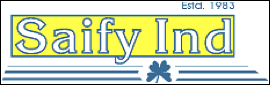
publicly reply to Khozem Vahaanwala
A. Hi,
In my opinion re-activating nickel is very touch and go. We always use a copper strike plate over the existing nickel and then re-nickel and we have never had a problem.
Cheers Craig
England, UK
2005
publicly reply to craig short
A. We have the same composition of nickel plating bath but not with the brightener. The usual range for pH is from 4.2 to 4.6. It would also be best to perform a hull cell using 2.0 A/dm2 and also 0.1 A/dm2. Try to check in what current density did this problem occur. If the finish is good at high current density, then you could probably have a contamination of your nickel plating solution. Try to check if there had been fallen articles in your tank. Remove it and try dummy plating. Use corrugated sheets. Step:
(1) Lower the pH to 4.0 and add 1 ml/L H2O2 and plate using 2.0 A/dm2 for 4 hrs.
(2) Decrease the current by using 0.1 A/dm2 overnight or until the plating shows no black deposits. Copper, Zinc and Lead will be shown in your dummy as dark deposits.
- Lapu-Lapu City, Cebu, Philippines
April 19, 2008
publicly reply to Ryana Lee
A. There are several great responses here to help you find a resolution yourself. You are purchasing a brightener package and the manufacturer is another resource to your problems. They are experts in this specific brightener package and have experience with other customers. They may have information not yet presented here.
Matt Poppe- GUADALAJARA, Mexico
June 3, 2018
publicly reply to Matt Poppe
Q, A, or Comment on THIS thread -or- Start a NEW Thread