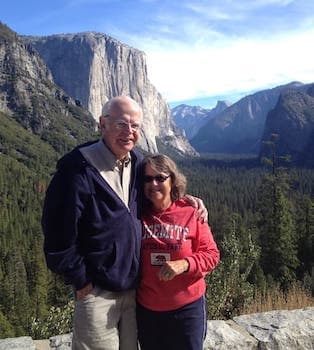
Curated with aloha by
Ted Mooney, P.E. RET
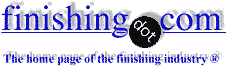
The authoritative public forum
for Metal Finishing 1989-2025
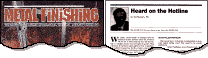
-----
Hard Anodize Problem. 2XXX Aluminum Burning
1998
Q. I would appreciate any help/information in regards to hard anodizing 2024 T3 aluminium to MIL-A-8625 / MIL-PRF-8625 [⇦ this spec on DLA] Type III black.
We are having a problem on some specific parts in which we are attempting to get a minimum of 1.2 mil applied to a bore on a machined part. The part is 5.000 inches OD by 4.250 inches long with a bore diameter that has steps in it from 1.9750 inches to 2.120 inches. Our tank temperature is 57 °F, aluminum content 1.0 , bath concentration 25.9 oz. per gallon. We were applying 16 volts with a initial amperage of 1100 amps.
Richard JohnsonA. Sir,
2024 is a high copper alloy & cannot be hardcoated in conventional hardcoat systems. Here in our facility we use 2 different hardcoat systems, Martin HC & Imperv-X HC. Martin will process most alloys BUT NOT high copper ones. The Imperv-X system is specifically designed for high copper alloys and we hardcoat them daily with no problems.
David A. Kraft- Long Island City, New York
1998
1998
A. Richard,
Your information is not complete which makes an answer difficult or at least required an assumption to be made which is not good.
Al 1.0 oz/gal or g/l or ? Sulfuric Acid ounce by weight or fluid ounce?
Normal hard anodize is 32 °F. Are you using a proprietary or an additive? Straight DC or superimposed AC or pulse?
The high copper content in your alloy makes the anodizing more difficult, but you should be able to get 1 mil.
If your final voltage is 16, you are hard pressed to call it type III anodize, and 1 mil will be very hard to get.
Include all of the process variables and it will be easier for people that are more knowledgeable than me to help you.
Jim
James Watts- Navarre, Florida
A. Your processing parameters are more appropriate for an anodize than a hardcoat. I doubt that this coating would meet the minimum wear requirements for a Type III hardcoating per MIL-A-8625. This could be contributing to your difficulties in achieving the desired thickness. Typical hardcoat anodizes utilize higher voltages and current densities with lower solution temperatures. The trade-off for these harder, thicker coatings is an increased tendency for "burning", particularly in the 2XXX series alloys. Special procedures and process controls can help minimize this phenomenon. Also, proper design and placement of auxiliary cathodes will help with coating uniformity.
Chris Jurey, Past-President IHAALuke Engineering & Mfg. Co. Inc.

Wadsworth, Ohio
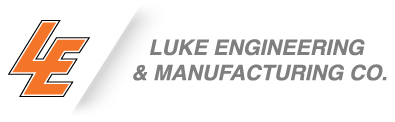
1998
Treatment &
Finishing of
Aluminium and
Its Alloys"
by Wernick, Pinner
& Sheasby
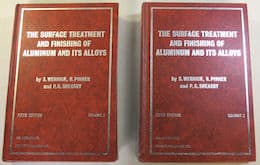
(note: this book is two volumes)
on eBay or
AbeBooks
or Amazon
(affil links)
Q. Dear Reader,
Hello. I am a searcher about "hard anodizing in ambient temperature". Please if you have a article or book about this, send me.
Thank you,
Mehdi Khandan- Qom, Iran
2002
Hi Mehdi.
By far the most complete reference to every type of anodizing is The Surface Treatment & Finishing of Aluminium and Its Alloys. It's a large, expensive, 2-volume book ... but hopefully there's a copy in a public or university library. It covers everything you can imagine .
Regards,
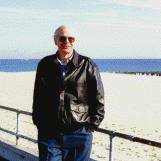
Ted Mooney, P.E.
Striving to live Aloha
finishing.com - Pine Beach, New Jersey
Q. Hello my name is Jake Allen and I am 21 years old. I work for a plating shop in Grove, Ok.
We have recently been sent parts that are 2124 aluminum. The parts are to be hard coated. We have attempted to process a few and some of them come out ok but we have had a few burn. We have good contact and our acid and alumina content are good. Our sulfuric content is 360-390 g/l and alumina is around 7 g/l.
We have tried slowing ramp time and still receive the same results. I would appreciate any help.
Thank you,
Jake
plating shop employee - Grove, Oklahoma, USA
July 16, 2009
Multiple threads merged: please forgive chronology errors and repetition 🙂
Whether aluminium Al2014 grade is compatible to hard anodizing? Or it requires some special chemicals & change in process?
Santosh PatilBuyer - India
March 8, 2010
Hi
2014 is copper Aluminum Alloy, which may give burning problem, may not support much for hard anodizing (Sulfuric Acid electrolyte), where you need higher current density.
- Chennai, India
March 11, 2010
Multiple threads merged: please forgive chronology errors and repetition 🙂
Q. Hello,
I'm French and I try to treat parts as hard anodizing current pulse on a 2024 alloy.
Can you give me informations on the ramps of anodized for this alloy ?
Cordially
Research and Development - Saint-Etienne, France
May 4, 2011
A. 2024 and especially heat treated 2024 requires higher free acid, try 220 gm/L, then maybe 230 gm/L, let us know.
Always ramp 15 minutes up to a pre-determined 24 amps per square foot amperage then switch over to current control and let the voltage climb as the resistant thickness builds.
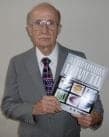
Robert H Probert
Robert H Probert Technical Services

Garner, North Carolina
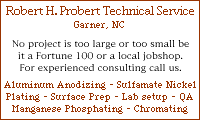
May 4, 2011
Q. HELLO
MY NAME IS ALI, I WORK ON HARD ANODIZING ON PARTS MADE OF 2024 ALUMINUM. I HAVE A PROBLEM WHEN CARRYING HARD ANODIZING IN END TIME IN HIGH VOLTAGE (45-50 V). CURRENT SUDDENLY GOES HIGH AND PART IS BURNING. PLEASE GUIDE ME.
ANODIZER - ESFAHAN, IRAN
August 29, 2011
A. Hi, Ali.
In my very limited experience this is usually caused by poor contact. Thus the item initially gets little or no anodizing thickness, then when the voltage goes high, it breaks through whatever resistance was on the contact surfaces and exposes thinly anodized or non-anodized parts to 45-50 V and large currents, which immediately causes burning.
Regards,
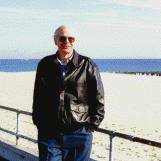
Ted Mooney, P.E.
Striving to live Aloha
finishing.com - Pine Beach, New Jersey
August 29, 2011
Q. Hello,
I'm working on a project that requires 2024 aluminum to be hardcoat anodize and yield a final hardness of 300HV. After many trials I have not been able to achieve the hardness, but wear data and thickness requirements are acceptable. Any suggestions?
- USA
June 7, 2013
A. How are you measuring hardness? When Reynolds published their first work on the glycolic/glycerin additive they got a average of 320 and a max of 365 Knoop on 2024-T3 at 1.8 mils and avg. 347 and max of 376 Knoop at 2.3 mils. So 300 is attainable. Be reminded that the Knoop diamond comes in on the cross section -- if close to the bottom of the thickness where the pore is small it gets a higher thickness, but when it comes in near the top of the inverse taper pore, it crunches and shows a lower thickness.
Now for ways to get a smaller pore (read harder): lower temperature, lower free acid, higher current density, and 4%/vol of a 50/50 glycolic/glycerin additive. Note also that all other allows get harder than the 2000's.
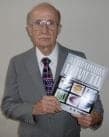
Robert H Probert
Robert H Probert Technical Services

Garner, North Carolina
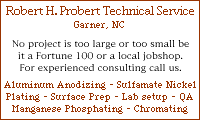
June 12, 2013
Q. Hi,
Thank you for the nice Article, but my main question is, why does the 2024 or 2011 alloys have tendency to burn in hard anodizing process?
What is the scientific reason behind it?
Does it have to do anything with the Electrical resistivity or conductivity of the alloy?
Best Regards
Payam
- Bielefeld Germany
March 29, 2018
Q, A, or Comment on THIS thread -or- Start a NEW Thread