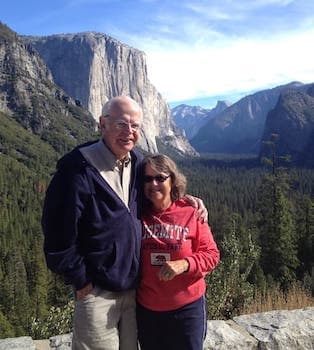
Curated with aloha by
Ted Mooney, P.E. RET
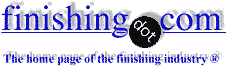
The authoritative public forum
for Metal Finishing 1989-2025
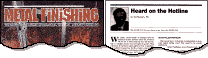
-----
Barrel Plating, using conductive media / ballast / shot
Q. I currently oversee a Watts nickel and tin electroplating operation for barrel plating very small parts (about 3 mm dimensions). I want to characterize our particular plating operation so I can optimize processing parameters (like current, load size, etc.) but I haven't found a good way to calculate the plating surface area of the load. I would like to talk to anyone who has dealt with this problem before. (One other bit of information: half of the load is steel plating media)
Also, are there any good references on barrel plating factors and guidelines?
Mark Carper1998
A. How critical are your thickness parameters? I have experience with an automatic barrel plating line with tin. Are you plating long runs of the same size parts? My first suggestion would be to use weight as a gauge of load size. Make a few trial runs to decide the deposition rate for that size load at a certain amperage. If you run consistent size loads, you could determine an optimum setting from the ratio of the amperage and time to the thickness achieved. A good system of process control will also help to get maximum production. Although I have not seen any good guidelines for barrel plating, there may be some out there. Hope this helps.
Phil Pace- Tulsa, Oklahoma
1997
1997
A. I have been working with plating process setups for over ten years, for both barrel and rack. My current job entails managing a shop where we plate about 100,000 parts a week in 2x4 and 4x4 barrels. We also do copper electroforming. Here's the recipe:
1) Get the surface area of the part
2) Get an accurate count
3) Figure the total area from 1) and 2). Don't forget to add the area of ballast (shot) and danglers.
4) Determine the plating spec (what layers and how thick each is).
5) Calculate the amps for each layer based upon 3) and 4)
6) Calculate the plating time for each layer based upon 4) and your bath ratings
7) See if your calculations are correct by doing the plating.
8) Inspect the parts immediately to make sure they are what you wanted.
9) Keep good records of everything you just did.
The best way to make this easy is to let your PC do it. If you don't have a PC and the right program, buy them.
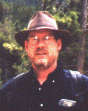
Bill Vins
microwave & cable assemblies - Mesa (what a place-a), Arizona
A. In plating parts of this size in the barrel for nickel, tin and electroless nickel, I used to calculate the surface area of each load using simple formulas like cylinders, spheres, cones, etc. to approximate the shape, and to weigh a small sample. 1 ampere/square foot for plating is a good first cut, if you want very good plating distribution between and within parts. Include the surface area of the plating media. Fill the barrels to one/third to one/half full
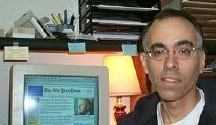

Tom Pullizzi
Falls Township, Pennsylvania
1997
"Don't forget to add the area of ballast (shot) and danglers"
Q. Ballast (shot) is one of major costs of barrel plating. Is there any method or option to barrel plate without ballast (shot)?
Thank you
plating - Sembilan, Negeri, Malaysia
July 13, 2010
A. Hi Misri. One alternative may be vibratory barrels (rather than tumbling in a horizontal barrel, vibration makes the parts skitter around on a perforated plate).
Regards,
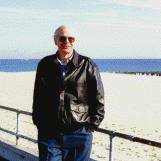
Ted Mooney, P.E.
Striving to live Aloha
finishing.com - Pine Beach, New Jersey
Q. I currently have a job that requires plating. The base metal is BeCu, the plating spec. is Au over Ni-P 50-100 µinch each element. The parts are roughly 0.200 x 0.030 w/slots on both ends. My problem is during both the cleaning and plating operations the parts "MESH" or "NEST" leaving unplated and exposed base metal. I have tried different styles of ballast, more or less parts, etc. I have also tried using a Vibrobarrel with the same results. Does anyone have any great ideas w/o redesigning the part which is not an option?
Thank You,
MARK KRUZEL- El Cajon, California USA
2000
A. Nesting of parts can be dealt with many ways, but there are limits. I don't think the "Vibrobot" is a viable option as its design is not a nesting issue. I assume you are barrel plating in some type of horizontal barrel. Breakers are the most common solution, either full width, or blocks installed. Are you using round barrels? Nesting is sometimes more of a problem with these than hex barrels. A lesser load with a large internal breaker can "flip" the entire load. RPMs can also help sometimes, depending on the part / load size / etc.
Sometimes just redistributing the load can make a huge difference [i.e., different size equipment]
Contact your equipment vendor / distributor with sample parts -- they should be able to provide a viable solution.
Ron Landretteplating equipment supplier - Bristol, Connecticut
2000
Q. Hello!
In what process I should use plating media such as balls?
thank you Sa'ar
saar [last name deleted for privacy by Editor]student - yavne, israel
2000
A. I'm not sure that I understand your question, Saar, but one occasion to include metallic balls or other conductive media in the mix is when the parts you are trying to plate don't have enough plateable area on them to reliably conduct electricity from piece to piece. As a parallel: In the children's game of "tag" there is usually a "home base" where the players are safe, and sometimes the kids join hands to make a chain extending from home base, claiming to be safe via "electricity" (one child gripping hands with another, gripping hands with another. Barrel plating of fully conductive parts works the same way: one part touches another which touches another which touches another which touches the danglers or cathodic contacts.
But when only part of the components are conductive, for example, if you are trying to barrel plate the ends of surface mount components, and only the ends have been made conductive with metallic paint, you may find that filling the plating barrel with such components will not allow a conductive path from piece to piece to piece because the conductive area of one part is only touching the non-conductive area of another. But if you mix in an appropriate quantity of conductive balls, you may have a plateable mix.
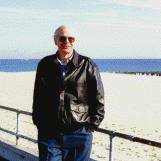
Ted Mooney, P.E.
Striving to live Aloha
finishing.com - Pine Beach, New Jersey
2000
Q We are searching for a barrel plating equipment to be used for small plastic parts or components. Therefore, we would like to contact the manufacturers of this plastic barrel plating for small plastic parts or components. We would like to buy one unit immediately. Thank you!
DR. LIE T [last name deleted for privacy by Editor]- Singapore
1999
Q. I am in my final year Bachelors of Engineering. My project is on electroplating on plastics. I too am interested in technical details pertaining to barrel plating for small plastic parts. It seems details on the process are hard to come by and nobody I know is using it. Someone please be kind and post me some material on the same.
Ronjey Banerjjee- New Delhi, India
2003
A. I have found vendors who are capable of electroless barrel plating on plastic. I'm sure they would be willing to talk with you.
David Zeller- Boston, Massachusetts, USA
2004
Q. Hi,
I'm involved in barrel plating in my company and now have a project in barrel plating of SO8 package. But my problem is the product is floating on dummy during plating/barrel moving. Is there anybody can advise how to settle this issue? If I need special design for this product, can you advise me the barrel design, also the supplier?
regards,
- Seremban, N.Sembilan, Malaysia
March 27, 2012
A. Haslina,
I'm not sure what you mean when you mention that the parts are "floating on a dummy". You may have to "load up" on the barrel media. There is lightweight conductive media available for Barrel Plating that will not bend or scratch the packages. This type of media comes in all weights, shapes and sizes and maintains good conductivity within the barrel. It takes a little experimentation to get the correct mix of parts and media to get the desired plating thickness and to be sure there is no damage to the packages. There is another alternative to conventional barrel plating which is Vibratory Barrel Plating. This technique is often used when delicate parts are not suitable for Barrel Plating. Instead of a tumbling motion, the parts are moved by vibration around the surface of the barrel. Your parts and media may be too lightweight for this process however. Hope this helps!
Engineering - Mesa, Arizona, USA
April 2, 2012
Q. Hello,
QUICK QUESTION. WHAT DO YOU RECOMMEND FOR USING BALLAST BALLS IN A SILVER BARREL PLATING. PARTS ARE SMALL COPPER. WHAT SURFACE AREA RATIO BALLS TO PARTS AND WHAT TYPE OF BALLS TO USE, SILVER PLATED OR COPPER BALLS?
THANK YOU
- ROLLING MEADOWS, ILLINOIS
May 6, 2013
A. Use stainless steel balls that have been run in a nickel chloride strike, then after use, put them in a stainless basket and use for anodes in your silver plating tank, the nickel will not hurt the silver. Be sure to silver strike first to minimize the co-deposition of the copper (which eventually is going to find its way into the silver solution.)
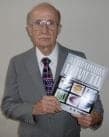
Robert H Probert
Robert H Probert Technical Services

Garner, North Carolina
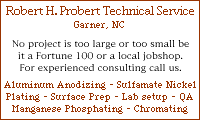
May 9, 2013
A. Uh, what, Robert? You're describing something quite interesting to me, but either you or I misread Al's question.
My take was that he is barrel plating some copper components but feels that the parts can't be successfully barrel plated without conductive media/ballast/shot added to the barrel. You seem to be talking about a way to increase the anode area without a big investment in more silver?
Regards,
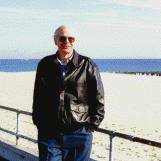
Ted Mooney, P.E.
Striving to live Aloha
finishing.com - Pine Beach, New Jersey
May 9, 2013
A. Ted, what I am trying to say. Use the stainless steel balls in the electroplating barrel, then after he is through with the balls or they are built up too much (chipping and flaking) then put them in stainless basket back in the plating solution and recover the silver.
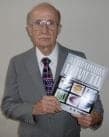
Robert H Probert
Robert H Probert Technical Services

Garner, North Carolina
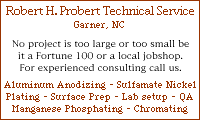
May 10, 2013
Q. Everyone keeps talking about media, shot or ballast. I can't seem to find any companies that supply this on-line. Saw one mentions of Control Products USA. No website.
I need to find a low density ballast to mix with reed switches in an oblique barrel. Plating Tin onto Nickel-Iron alloy.
- Lake Mills, Wisconsin, USA
January 31, 2014
A. Hello Michael,
If you go to www.pfonline.com > suppliers, click on Mass Finishing Media, you will find a list of companies who supply barrel plating media.
Process Engineer - Malone, NY USA
February 3, 2014
Q. Hi,
Wanna ask regarding metal balls sticking to each other in Sn plating. Why this happened and what is the solution?
- Wangsa Maju, Kuala Lumpur, Malaysia
December 10, 2019
A. Hi Wangsa. Your question is a bit vague, but I think you are saying that stainless steel balls you are using as conductive media in barrel tin plating of semiconductor components are plating up and sticking together? I think you must reduce their quantity, or increase the speed of rotation so they are knocked apart before the plating builds up that much, or change their shape or size or finish.
Regards,
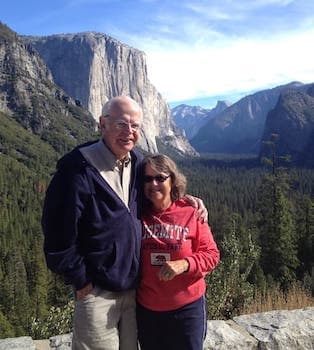
Ted Mooney, P.E. RET
Striving to live Aloha
finishing.com - Pine Beach, New Jersey
December 2019
Q. Hi,
We plate ferrite cores using barrel plating & steel balls. We tested new source of Sn solution. After done Sn plating, steel balls & ferrite cores stick together. Previous solution found no sticking issue. I have no idea.
- wangsa maju, kuala lumpur, malaysia
December 11, 2019
A. Hi again. All I can offer is wild guesses because you are not offering a co-ordinated and detailed description of what your whole situation actually is, but have you switched from bright acid tin (stannous sulfate), alkaline stannate, or MSA bath to one of the other two perhaps?
If you have no idea you'll probably have to retain a plating consultant. Good luck.
Regards,
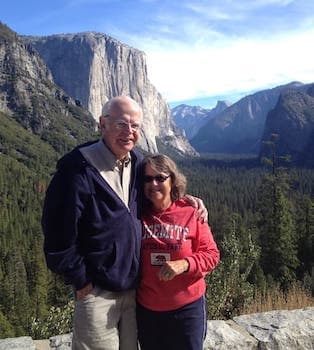
Ted Mooney, P.E. RET
Striving to live Aloha
finishing.com - Pine Beach, New Jersey
December 2019
December 18, 2019
Q. Hi,
Any idea for such problem:
- wangsa maju, kuala lumpur, malaysia