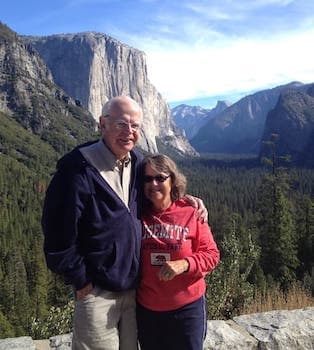
Curated with aloha by
Ted Mooney, P.E. RET
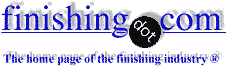
The authoritative public forum
for Metal Finishing 1989-2025
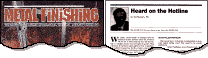
-----
Chemically prepping aluminum/graphite (Al/Gr) composite material for plating
1998
I am seeking a method for chemically prepping aluminum/graphite (Al/Gr) composite material for plating with either copper, silver, or nickel.Graphite reinforcements are continuous fibers in a woven preform within a cast aluminum alloy matrix of either 356 or 6061. The preparation method
should include an appropriate preplating treatment by double zincate or a suitable alternative. If possible please identify a known commercial source.
Al/Gr is a galvanic cell. Therefore, typical chemical etch methods for aluminum oxide removal prior to plating are accelerated by the galvanic cell and the interface zone between the Al matrix and the Gr fibers is over etched. As a result, fibers are often released from the Al matrix creating an unacceptable fuzz effect on the surface. NASA has published a phosphoric acid prep for aluminum which is much less aggressive. If anyone has any experience with this method please contact me, also. If anyone has prepped graphite for plating I would also like to hear from you.
William De La Torre- Research Opportunities, Inc.
Gawrilov's Chemical Nickel Plating, 1979, Portcullis Press, Redhill (England) mentions that in preparation of cast irons with 2-4% carbon, that the acid etching is a critical step, for the liberated graphite remains as a grey, greasy layer.
He also says that graphite can be prepped with palladium chloride with citrate as a buffer, and a reference to N.C.W. Judd (Composites 1, (1970) Dez., 345) "discusses the importance of non-electrolytically deposited nickel and copper layers on carbon fibres." "These thin layers serve as adhesive media during the manufacture of the promising compound materials metal matrix-carbon fibre or polymer matrix-carbon fibre". He also mentions that heat treating between plating steps may diffuse C atoms into the previous plate.
If you could further explain the mechanism of the galvanic action, I would appreciate it. Are you sure you are not just exposing the fuzz of graphite by simple chemical etching of the aluminum? You don't have to remove a lot of aluminum metal to clean off the oxide.
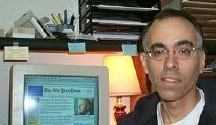

Tom Pullizzi
Falls Township, Pennsylvania
1997
Have you considered using the wet blasting process for pre-plating preparation. This process can be very gentle (unlike dry/sand blasting) and simultaneously degreases your component without having the environmentally damaging effect of chemicals. If you would like more info or have already evaluated this process please let me know.
Steve Eyton-Jonesabrasive developments - Berkshire, U.K.
1998
1998
I was reading your articles and hope you can help me. I am rebuilding an old Land Rover and the body, which is made of aluminum, has some areas where corrosion from electrolysis has taken place.
Is there a chemical available that will dilute or soften up the hard powder byproduct of this corrosion process?
I have tried Duro by Loctite (for rust), vinegar ⇦in bulk on eBay or Amazon [affil links] , and a product used to clean mag wheels. None seem to soften the corrosion.
I am interested in knowing more about the wet blasting process mentioned by Steve Eyton-Jones. Sand blasting distorts the aluminum.
Michael KingHi,
The company I work for is making a product using an aluminum graphite. I would love to know if there is a safe chemical we could use to get rid of the burrs.
Thank you,
Kim Lemerise- Fall River, Massachusetts
2001
I just finished a training class on silver plating aluminum. The cleaning process, for what we do anyway (power industry), is 3 steps.
1- Electrocleaning you need a 30 amp power pack set to 10-12 volts in forward polarity.
2- etching 10-12 volts in reverse polarity
3- desmutting 10-18 volts all need rinses in between.
Three more steps in plating. 1- nickel acid (bonding solution) 2- copper bond 3- silver ... there's too much info for a forum ... I believe this will help you: Sifco.
- Fort Myers, Florida
June 18, 2011
Q, A, or Comment on THIS thread -or- Start a NEW Thread