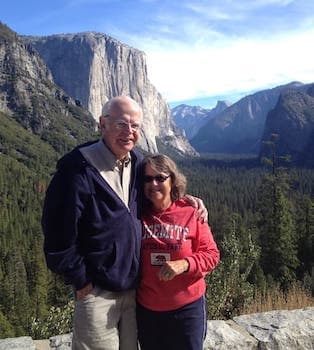
Curated with aloha by
Ted Mooney, P.E. RET
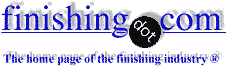
The authoritative public forum
for Metal Finishing 1989-2025
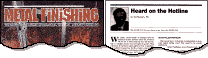
-----
How to activate heat treated Nickel for Nickel Plating
Q. Does anyone have a suggestion on how to activate heat treated Ni to accept Ni sulfamate plate?
Walt Bilous1998
1998
A. Have you tried cathodic electroclean, Rinse, Rinse, 10% H2SO4, Rinse, Rinse, 5 opg NiCl2 Wood's Nickel Strike, 5 minutes (enough current to get some very light bubbling on the cathodic surface, it will look like a lot of gassing in the barrel, of course)
Rinse, Rinse, Plate?
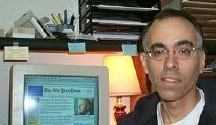

Tom Pullizzi
Falls Township, Pennsylvania
A. My big question is: Heat treated in air, or some other medium, and is the nickel that has been heat treated the base material, an intermediate deposit, or otherwise free from impurities like Cr, Al, Ti, etc. If pure Ni heat treated in air, an oxide a bit too tenacious for the above mentioned treatment may result, and stronger surface preparations involving Chlorides, fluorides, and/or even Cyanide would be required. Hot Cyanide does it every time followed by 30% HCl (rinse before of course!) then Wood's strike.
Regards,
Dave
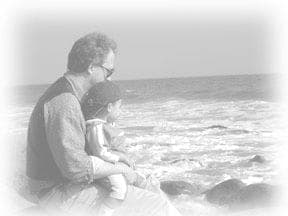
Dave Kinghorn
Chemical Engineer
SUNNYvale, California
1997
A. You are referring to Wood's nickel, or electroless nickel strike, per MIL-C-26074 [⇦ this spec on DLA]. The phosphate content is very high. It can go over 10% by weight and the nickel-phosphate volume can go over 30%. That's a lot. You'r heat treating is causing the intermetallic to form as well as oxidize the surface. I wager even in a vacuum, post H.T. autocatalytic nickel will be hard to plate to. My first suggestion is do not heat treat the nickel platings at all. Also,control your phosphate to a minimum. The high phosphate content make plating to woods nickel difficult. This takes good plating control, pH, temperature, solution, the works, but it is possible. Good platers know how to do this. I like to start out with a copper strike, 10 microns or less per MIL C-14550; followed with the woods nickel strike, 10 microns or less and then immediately electro-plate with nickel per FED-QQN-290 (replaced by AMSQQN290) . I would not dream of heat treating in the middle of this sequence. Now if you are plating for solderability, you'r not done. After a nickel lay-down of 75 to 125 microns, you immediately coat with gold, 50 microns min per MIL-G-45204. Now you'r done. Point of Knowledge, in soldering you solder to the nickel, not the gold and phosphate nickel is very hard to solder to. Sulfonate and sulphate nickel is the standard to solderability. If the part has to be heat treated, do it before plating, pickle and clean off the oxides prior to plating. The surface has to be "squeeky" clean. NEVER HEAT TREAT IN THE MIDDLE OF A PLATING PROCESS AND SURELY NOT AFTERWORD. Heat treating really damages platings. In fact, one of the bond tests uses a 300 °F bake to see if the plating peels off. - - - - - - - - Notice, I didn't ask why !
Lee R. Williams1999
Q, A, or Comment on THIS thread -or- Start a NEW Thread