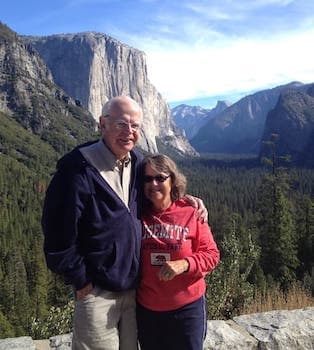
Curated with aloha by
Ted Mooney, P.E. RET
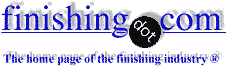
The authoritative public forum
for Metal Finishing 1989-2025
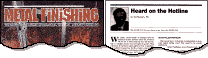
-----
Electroless Nickel Plating on TUNGSTEN-CARBIDE
Q. What chemical cleaning methods could be used to clean tungsten-carbide for an electroless nickel deposit?
Chip Zacchino1997
A. I cannot recommend the proper process for cleaning tungsten carbide, but I can offer one caution. That is to be very cautious with electrolytic alkaline cleaning with this material. If not properly controlled electrolytic alkaline cleaning can cause selective attack of the cobalt binder, leaving a porous layer of carbide particles at the cleaned surface.
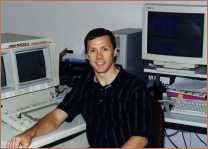
Larry Hanke
Minneapolis, Minnesota
1997
A. Have you tried wet abrasive blasting to clean before plating. This gives you an excellent surface key which provides a uniform plating effect without using environmentally harmful chemicals. Please let me know if you would like further info.
Steve Eyton-Jonesabrasive developments - Berkshire, U.K.
1997
![]() |
? What 'environmentally harmful' chemicals are you alluding to, Steve? ![]() Ted Mooney, P.E. Striving to live Aloha finishing.com - Pine Beach, New Jersey 1997 |
A. Re: alkaline electrocleaning
We use alkaline electrocleaning for tungsten carbide and have patented the process 1. We use it very successfully for preparing the surface for brazing. Part of our testing was to use electroless plating techniques to assess surface condition. We typically see a surface effect to about nine microns.
tom walz- Carbide Processors
1998
Ed. note: In response to our inquiry, Mr. Walz supplied the following info about the patent:
1 --Patent Number 5,624,626
Date of Patent Apr. 2---
Walz et al.
METHOD OF TREATING A CERAMIC BODY TO FORM A WETTABLE SURFACE
Q. How can I do the electroless nickel plating on the PR!
How to clean the PR and let it be hydrophilic? Please help me!
Thanks very much!
*^_^*
Ping-Ching Sun- Soochow University - Taiwan
1998
Ed. note: We don't know what 'PR' stands for in this context; I hope some other reader does.
Q. What detergents/cleaners are used that cleans the tungsten carbide surface without leaching the cobalt binder. If anyone knows a company that has a cleaning product out that is specifically formulated for cleaning carbide substrates, I would be most thankful to hear about them. Thanks in Advance, Mark
Mark Eastep1999
A. Cleaning carbides is precarious situation. Cobalt leaching is typically caused by an acid attacking the cobalt binder, or a reverse electrolytic process removing the cobalt (again leaching). I have worked with 3 PVD coating companies and the only process I have found that has worked is an ultra-sonic cleaning in an alkaline solution, rinsed in deionized water, and hot air dried immediately after rinsing. I have seen ultra-sonic in trichlorethylene used but you have to make sure the pH is not acidic.
Lou Lechner- West Chicago, Illinois, USA
2001
Electroless nickel on tungsten titanium (adhesion problem)
Q. Dear all,
We are recently given a silicon wafer onto which a tungsten/titanium coating had been sputtered with a request that it be electroless nickel plated. The W/Ti has 10% Ti composition. I am able to plate Ni on W/Ti. But the adhesion is a big problem. The plated Ni can be easily peeled off. If anyone of you have experience plating Ni on W/Ti, please give me some suggestions how I can improve the adhesion. I would be grateful for any thoughts you may have.
Many thanks,
Bin Zou- Colorado Springs, Colorado
2002
A. See Durney's Electroplating Engineering Handbook ⇦ this on eBay, AbeBooks, or Amazon [affil links] for plating cycles for tungsten.
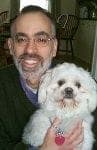

Tom Pullizzi
Falls Township, Pennsylvania
2002
A. It is a common practice to deposit a very thin layer of Ti for adhesion followed by W as a barrier layer and then Ni for solderability as three separate layers in electronic circuits. This is all done typically using sputtering. Are you sure it is a W-Ti alloy and not pure W on the surface?
Mandar Sunthankar- Fort Collins, Colorado
2002
Q. Hello guys, it seems like I am encountering related situation.
I am figuring why are there delayed-stains after post treatment washing of my tungsten alloy after nickel plating. These delayed stains takes a few days to appear. Are these stains related to the cobalt leaching? or other reason.
These stains can be taken out by rubbing blue-tach on the parts.
Please help me. Thank you
- Singapore
May 24, 2011
A. Hi Kenneth. I strongly doubt that cobalt is 'leaching'. But delayed staining like this is a commonplace when plating a sintered material because of its porosity. If you are able to significantly improve the rinsing it should help. It is also possible to vacuum impregnate the sintered material to reduce its porosity. Good luck.
Luck & Regards,
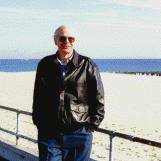
Ted Mooney, P.E.
Striving to live Aloha
finishing.com - Pine Beach, New Jersey
Multiple threads merged: please forgive chronology errors and repetition 🙂
How to electroless plate Ni onto Tungsten
June 3, 2015Q. Hello,
I am new to this forum and this is my first post.
I'm trying to electroless plate nickel on Tungsten but there doesn't appear to be too much literature on how to do this. Specifically, I am having a hard time locating a procedure for activating the Tungsten surface without the use of current. This is important - no current.
Does such a process exist?
I found a procedure in the "Electroless Plating -- Fundamentals and Applications (1990)" book as follows.
1. Alkaline potassium ferrocyanide
⇦ this on
eBay
or
Amazon [affil links]
soak, 215 g/L in 75 g/L potassium hydroxide, room temperature, for one min.
2. Rinse.
3. Boil in 10 percent potassium hydroxide for 10 min.
4. Rinse.
5. Dip in 10 percent hydrochloric acid for 30 sec.
6. Rinse.
7. Activate with palladium chloride (0.1-0.5 g/L in 1-3 mL/L hydrochloric acid).*
8. Rinse.
9. Electroless nickel plate.
The problem with this process is it uses palladium and I cannot afford palladium since I'm just working out of my parents' garage. Basically ... how can I activate the surface of Tungsten for electroless Ni plating without current or the use of expensive chemicals?
Thanks - I apologize if these conditions seem ridiculous or unfeasible. I'm still new at this and learning.
Hobbyist - Los Angeles, California USA
A. Hi Glenn. I believe that the basic issue is that electroless nickel plating will only happen on surfaces that are catalytic to it like palladium, iron, and nickel. You might search the web and scholar.google.com for "catalyst for electroless nickel" to see if there is a less expensive solution.
You might take a look at "ELECTROLESS NICKEL PLATING ON TUNGSTEN" at
www.sharrettsplating.com/blog/electroless-nickel-plating-tungsten/
Readers may find thread 0350, "Electroplating onto tungsten-carbide" interesting as well.
Luck & Regards,
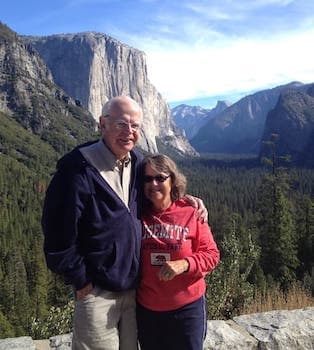
Ted Mooney, P.E. RET
Striving to live Aloha
finishing.com - Pine Beach, New Jersey
Q, A, or Comment on THIS thread -or- Start a NEW Thread