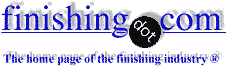
-----
Woods nickel plating (for Barrel, STS substrate )
1998
Dear reader! Sorry, my English is not perfect.
substrate : STS
type: pinplating
process : electroless nickel - hard gold
Problem:
1. Rack plating is impossible.
2. Woods nickel strike is barrel plating with difficulty.
Wanted:
1. Woods nickel plating composition (for barrel)
2. STS activation solution
Thank you.
Kim kyoung min- Seoul, Korea
It would be helpful if you gave us the processing cycle that you are presently using. Solutions, time, temperature, current density, amperes/gallon of solution, the size of the pins, etc.
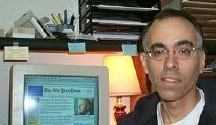

Tom Pullizzi
Falls Township, Pennsylvania
1997
1997
Kim sonsaeng-nim,
annyong ha shimnikka?
Plating pins in a barrel is the worst kind of job, especially STS, no matter what you try. The biggest problem is that all the pins roll together as a big ball. Then none on the inside of the ball get plated and end up passivating. Depending on your pin size and barrel size, the question is how to load the barrel with pins and tumbling media such that all the pins roll quickly and freely for uniform exposure to plating? I have had good luck using the following procedure:
1. Get a glass fish aquarium that the barrel can fit into. Use a beaker for micro barrels.
2. Load the barrel with parts, place into the aquarium and turn on the motor. Observe the tumbling. Generally with long thin pins, you cannot load the barrel more than 1/5 full or they all form a ball. Especially observe how the parts interact with the cathode. You may need to make your own unique cathode if parts tangle in the one you have.
3. Observe the tumbling with different amounts of parts, and with different types and amounts of tumbling media. Realize that some percentage of non-conductive media can be used to conserve Gold. ferromagnetive media can be used for easy separation afterwards.
4. After several such observations, you will determine the proper barrel loading. There really are no fixed rules that you can look up.
5. Observe while tumbling the mass of parts and media in the barrel and estimate its gross surface area as a single part. Use this area as the starting point for your amperage calculation. Using a standard woods strike formulation, begin plating using normal current densities for the gross surface area. Then begin increasing Current Density until you find the acceptable one. Maintain records of surface area of parts, media, etc., and write your own mathematical expression governing the procedure for future reference.
6. If current density can not be pushed far enough, you may have to pump plating solution into the side of the barrel through one of the bearing holes.
Tedious procedure, but it gives excellent results.
Good luck,
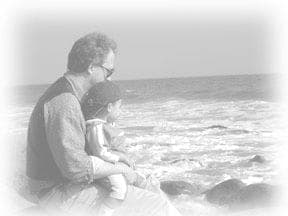
Dave Kinghorn
Chemical Engineer
SUNNYvale, California
What you might want to look into is an electroless nickel strike.I've had great results using this prior to Electroless nickel.
Ray Salchowmetal finishing shop - Cincinnati, Ohio
1997
Q, A, or Comment on THIS thread -or- Start a NEW Thread