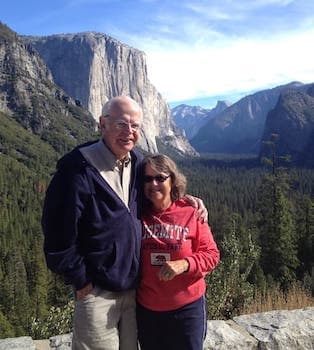
Curated with aloha by
Ted Mooney, P.E. RET
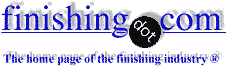
The authoritative public forum
for Metal Finishing 1989-2025
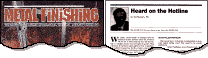
-----
Disposal of Soak Cleaners from plating and metal finishing
I am working on a student project (for completion of a MS -environmental engineering degree) for a metal plating and finishing shop. This small shop currently disposes their soak cleaners as hazardous waste. the local POTW will let them dispose of the cleaners to the POTW but the metals concentrations are too high. They also have a WWTS with precipitation and clarification for their rinses. The chelating agents in the soak cleaner water interfere with the current WWTS. I think they should treat this cleaner separately for metals, maybe emulsion breaking followed by precipitation, or look into different cleaners which have chelating agents that will not interfere with treatment.
1) How do most smaller facilities dispose of soak cleaners?
2) what should I be looking for in a more treatable cleaner?
3) what options have worked for treatment of these cleaners?
I would appreciate any input on this! Thanks.
kim cook1998
Hi, Kim. I can answer question 2 for you. One method which is successful in choosing a cleaner which fits in well with your waste treatment procedures is to take a sample of the cleaner from your supplier and make up a 3% solution. Next, add a copper containing solution such as a used nickel stripper, and waste treat it in your lab. If, upon analysis, you have less than 2ppm of copper you're in pretty good shape.
Many modern cleaner manufacturers make non-chelating cleaners, and you need to make your supplier aware of your needs from the start- he may handle all the preliminary lab work for you.
Hope this helps,
Mike McDonald- Jefferson, Wisconsin
1997
Kim, The first thing I would suggest is switching to a non-chelated cleaner. I have experience treating both, and I believe not only will they be easier to deal with as waste, but they will also outperform the chelated cleaners.
You did not specify if your system is running continuous flow or batch treating. My preferred method is continuous flowing rinse waters, with concentrates routed to a separate dump tank for treatment. After neutralization and the addition of polymer, the concentrates should be pumped through the filter press.
Effluent from the filter press should be routed to the waste rinse water tank for second treatment as well as the dilution effect of any possible remaining residuals. As far as treatment, I have tried several methods of treating waste cleaners. My best luck has been with ferric sulphate and industrial grade hydrogen peroxide. Sulfuric acid should be used to drop the pH until all cleaner is reacted. This may not happen until you reach 2.5-3.0! pH.
From this point the pH should be raised to about 4.5-5.0 pH. For a 300-gallon tank add approximately 4 gallons of ferric sulphate. Follow this with 10 gallons of hydrogen peroxide. After letting the treated cleaner react with the iron and peroxide for about an hour, gradually add caustic soda to raise the pH to 7.0-7.5. With the addition of the caustic, the mixture will foam up so be sure not to over due it. This works very well with non-chelated cleaners.
Good Luck,
Phil Pace- Tulsa, Oklahoma
1997
Kim:
We were faced with a similar problem of treating a highly chelated cleaner in our batch treatment facility. Having tested (and rejected) ferric chloride ⇦ this on eBay or Amazon [affil links] , we had some success with CaCl2 but were not able to reduce the concentration of Ni to our discharge limits (2.4 ppm). Then we finally started working with magnesium hydroxide and this stuff works! Not by itself - in combination with NaOH, but we are treating now a highly chelated cleaner (Enthone Cold Action Cleaner) at, sometimes, a 30% concentration in our wastewater with, at times, 100-200 ppm Ni. The cycle is reported in my reply to question No 565 (using magnesium oxide). Try this stuff - it is good. Knowing how reluctant production people could be to switch cleaners (or, for that matter, change anything in a cycle that works), finding a treatment method that does not require any process changes in plating may be a blessing.
Good luck from PlaterB
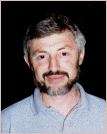

"PlaterB" Berl Stein
NiCoForm, Inc.

Rochester, New York
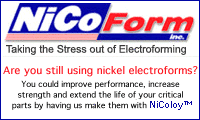
1998
Berl:
Several years ago I read of people who preferred magnesium sulphate to calcium chloride or ferric chloride ⇦ this on eBay or Amazon [affil links] for handling spent cleaners. So I suspect that the benefit of magnesium hydroxide in your application has to do with the superiority of magnesium as a chelate breaker, rather than the long reaction time of magnesium hydroxide slurry compared to caustic. If an occasion suggests, you might try the sulphate.
Phil:
In 1997 I don't believe in continuous treatment of anything. When the settlement agreements between NAMF and EPA were reached 16 years ago and 40CFR said that platers had to be in 'consistent compliance', I think 'consistent' held an accepted meeting of 'the great majority of the time'. Under unceasing environmental pressure, 'consistent' has morphed into 'absolutely and utterly flawless'. Although I am big on hiking, camping, fishing, the Nature Conservancy and Audubon Society, and not opposed to environmental laws, I think the EPA is shamefully playing Humpty Dumpty to our Alice on this one to snooker the platers. Yes, the technology EPA proposed--continuous treatment--offers compliance 'the great majority of the time' but it is the furthest thing in the world from 'flawless'. I think batch treatment, with the ability to test every batch released, is the only safe approach anymore.
Mike:
I'm not so sure that non-chelated cleaners are necessary. I have recently become a convert to the proprietary organo-metallic precipitants. They cost a bit, but they produce a smaller quantity of denser, more filterable, sludge while eliminating most of the worry about non-compliance.
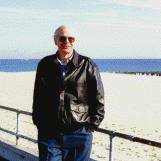
Ted Mooney, P.E.
Striving to live Aloha
finishing.com - Pine Beach, New Jersey
Ted:
The data we obtained developing our cycle seems to indicate that you are right and the main benefit of Mg is its chelate-breaking "power". However, there might be other factors such as the adsorptive properties of magnesium hydroxide sludge that may co-precipitate and, therefore, more fully remove the other heavy metals in the mix.
Help me understand why you are suggesting we try MgSO4 instead of Mg(OH)2. Magnesium hydroxide is so inexpensive, easy to work with and serves the dual purpose of raising the pH, breaking up the chelates and (maybe) co-precipitating the sludge without contributing additional ions (sulphate) in the treated water that I think it is the right substance to use.
Thank you, Berl
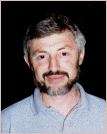

"PlaterB" Berl Stein
NiCoForm, Inc.

Rochester, New York
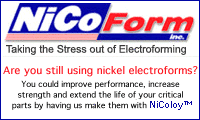
1998
Berl: You've apparently developed a treatment cycle that works fine. You are right about the advantages of magnesium hydroxide, and there is no reason for you to change your process at all.
My point was perhaps more applicable for others: magnesium hydroxide slurry has the one big disadvantage of long reaction time, and where people are seeking the magnesium for its complex-breaking power, they may be able to eliminate that disadvantage of long treatment time by using a soluble magnesium salt in place of the slurry.
Yes, magnesium hydroxide may also tie up metals by adsorption; I don't know. And, while magnesium sulphate may break the chelate, and quickly -- it probably can't be expected to contribute to filterability the way magnesium hydroxide does.
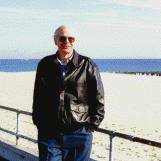
Ted Mooney, P.E.
Striving to live Aloha
finishing.com - Pine Beach, New Jersey
1998
Can you please explain in detail how to use the Mg(OH)2 to
treat cleaners. If possible the treatment process. I
really need your help on this. Since I need to solve the
similar issues at my workplace. Thanks for any assistance given.
Thank You,
finishing - JB, Malaysia
August 1, 2011
Hi, Hafiz.
You reduce the pH to the point where the magnesium can become highly soluble, say about pH 5. Then you add a good bit of magnesium salt or hydroxide, certainly more than a stoichiometric amount for the metals you are trying to drive out. Then you raise the pH up to about 10 or 11. You do this in beakers in the laboratory, measuring things, and carefully scale it up to your full batch size after you have achieved satisfactory lab results. Good luck.
Regards,
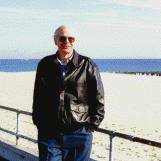
Ted Mooney, P.E.
Striving to live Aloha
finishing.com - Pine Beach, New Jersey
August 3, 2011
Q, A, or Comment on THIS thread -or- Start a NEW Thread