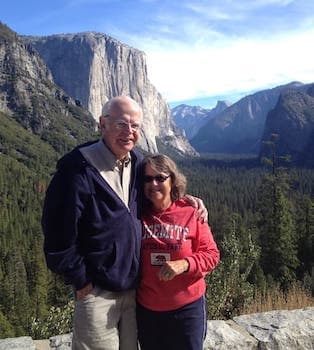
Curated with aloha by
Ted Mooney, P.E. RET
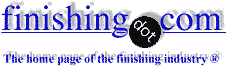
The authoritative public forum
for Metal Finishing 1989-2025
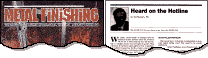
-----
Zinc plating of powdered metal parts
Q. We want to zinc plate + black oxide seal some powder metal (MPIF 35, F-0008-25) parts. We need the black to look good aesthetically and not fall off in our hands. We need the parts to pass a fifty-hour salt spray test. The parts are small, about on cubic inch, and all have a 1/2 inch through hole.
Grant Bryantmfgr. - Indiana
1998
A. I have never heard of black oxide on zinc. It may be done, but I doubt it. Are you asking for a black chromate on it?
James Watts- Navarre, Florida
1997
A. Zinc and black chromate will easily pass a 50-hour salt spray test when applied to a suitable substrate, Grant. However, depending on the quality of the powdered metal parts, they will probably be very porous, and could basically be unsuitable for plating onto. I'd suggest that you may need to investigate vacuum impregnation with a supplier to prepare the parts before plating.
Good luck.
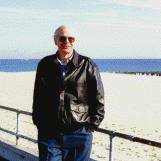
Ted Mooney, P.E.
Striving to live Aloha
finishing.com - Pine Beach, New Jersey
---
A. Message for Mr Grant Bryant
Vacuum Impregnation is an important prerequisite prior to any kind of plating operation for a sintered component. Vacuum Impregnation helps to seal the porosities in the components , so that the plating acids do not pose a problem of leaching after the plating operation is completed .
Best regards,
Mr Saibal Sen / Mr Probal SenPune, India
1999
Q. Hello All!
I have to process the sintered porous metal with zinc plating.
Material density is 6.6 g/cc.
After plating black patches were formed and a liquid substance is oozing out from the part.
How to get out of the problem?
Sintering Solutions Pvt Ltd - Chennai, Tamil nadu, India
March 1, 2018
A. Hi Balasundaram. We added your question to a thread which already addresses the subject. You probably will not be successful in zinc plating these parts without vacuum impregnating them to remove the porosity which wicks up the chemical treatment solutions.
Regards,
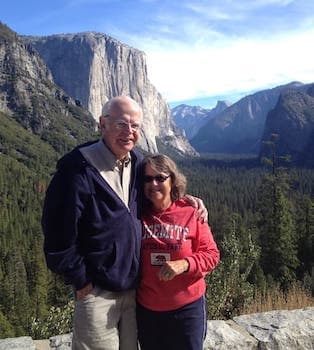
Ted Mooney, P.E. RET
Striving to live Aloha
finishing.com - Pine Beach, New Jersey
April 4, 2018
A. Many sintered parts (powder metal parts) have been - and continue to be - mechanically plated with zinc without impregnation. The void volume needs to be below about 15% which would seem to be the case here. Careful rinsing and COMPLETE drying after passivation are mandatory.
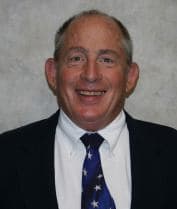
Tom Rochester
CTO - Jackson, Michigan, USA
Plating Systems & Technologies, Inc.

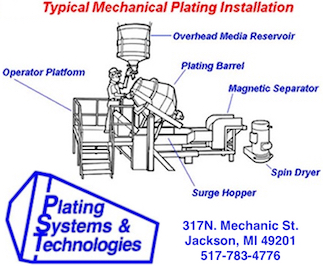
April 2018
Q. Hello this is Ed Reszenski Engineering Manager for an OEM. We are considering going to a powder metal part on a key component in one of our products. We were told by the potential supplier that zinc with a trivalent conversion coating can be applied after impregnation with a plastic material. They provided samples of parts made from a similar material that were impregnated prior to zinc plating by their supplier who is supposedly an expert at plating powder metal components. After 96 hours of salt spray we are seeing excessive white corrosion, no red rust but a lot of corrosion. This is a small U shaped piece with an arm that moves inside of the U. It is critical that nothing inhibit the movement of this arm as it is critical to the function of the product. Because of this I do not want any corrosion for this critical sub assembly. Is it that difficult to plate powder metal to meet the 96 hour salt spray without any corrosion white or red?
Ed ReszenskiOEM Switch Manufacturer - Weymouth, Massachusetts
August 13, 2019
A. Hi Ed. One of the strengths of cadmium plating was "freedom from bulky, sticky, corrosion products". Cadmium is dis-recommended today for environmental reasons, but it is possible that one of the alloy zinc platings (zinc-cobalt, zinc-iron, zinc-nickel, tin-zinc) will better satisfy your needs. And, of course, proper chromating is necessary -- but if you are already working with a shop specializing in plating powder metal parts, they know that.
Regards,
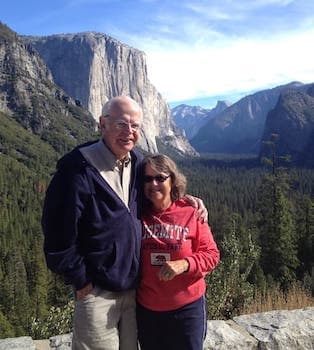
Ted Mooney, P.E. RET
Striving to live Aloha
finishing.com - Pine Beach, New Jersey
December 2019
We tried a sealant over the zinc and trivalent and we passed a 96 hour salt spray.
- Weymouth, Massachusetts USA
December 11, 2019
A. Hi Ed. Yes, sealants are a necessary step with most trivalent chromates. Glad you passed the 96-hour salt spray test. But is passing a 96-hour salt spray test adequate demonstration that the component will be satisfactory in performance? If the previously used parts and the new powdered metal parts perform the same in salt spray (fail after the same number of hours), you're probably okay.
Regards,
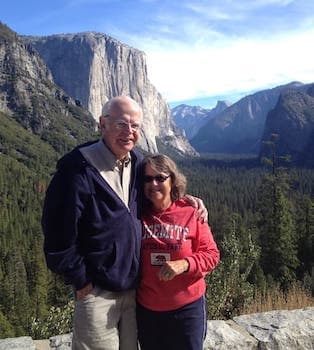
Ted Mooney, P.E. RET
Striving to live Aloha
finishing.com - Pine Beach, New Jersey
December 2019
Thanks Ted, we run control samples in our tests to insure we aren't losing performance.
- Weynouth, Massachusetts USA
December 11, 2019

Q, A, or Comment on THIS thread -or- Start a NEW Thread