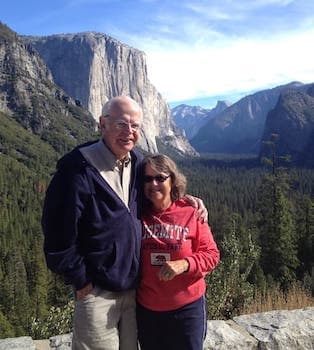
Curated with aloha by
Ted Mooney, P.E. RET
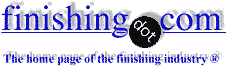
The authoritative public forum
for Metal Finishing 1989-2025
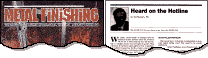
-----
Need black anodizing that is UV-proof

Q. I have seen this issue posted previously but have not been able to find an answer.
I manufacture a product from 6061 aluminum that is cnc machined, bead blasted and then anodized black. It is a "car ornament" and thus sees a lot of UV light.
The main issue we get is the black fading to a bronze/brown color, within about 1 year it seems.
The anodizer is overseas and to date all we have specified on the drawings are "Black Type 3 Anodize with UV resistance". After trying to do more research I have more questions than answers.
1. What anodize spec should I call out on the drawing if I want it to be UV fade resistant? (ideally I would like to to last 5 years without signs of fading)
-Dye with fade resistance of 8 or more?
-Type 2?
-Metallic or organic dye?
-Process for sealing?
-etc?
2. What test should be performed on the anodize finish before it goes into the next phase of production to ensure the UV resistance is going to last many years?
-UV light test? (too long?)
-Seal test? Are there instructions on how to perform a specific test for this application?
Hope I am not asking for a miracle finish and that this can be accomplished. I appreciate any help! Thanks!
- Carlsbad California
January 26, 2023
A. Hello Scott
You've gotten yourself into spot of bother here it seems. Let's see if we can help you just a pinch.
1. "What anodize spec should I call out on the drawing if I want it to be UV fade resistant? (ideally I would like to to last 5 years without signs of fading)"
ANSWER: Well, you are mentioning Type II and Type III anodizing, so I assume you are dealing with MIL-A-8625 / MIL-PRF-8625
[⇦ this spec on DLA] already, which isn't a bad way to go about it. Though one thing that should be noted is, that Type III is more of a technical anodizing than decorative. More on that later.
"-Dye with fade resistance of 8 or more?"
ANSWER: There are definitely variance in the lightfastness of various dyes. Some are better than others, however, if you want to be certain that you get a Lightfast Black? Metallic and/or Electrolytical coloring is the way to go.
"-Type 2?"
ANSWER: As mentioned above, Type II is a more suitable anodizing for decorative pieces. Now black isn't the -worst- color in terms of color density when working with Type III, mostly because it should have a dark-grey base color depending on alloy. However, the reason Type II is much better for Decorative pieces is that Type II has a lot more pores than Type III, which is where the color is held. Meaning that you will have a lot more metal or dye particles on the same surface, giving you a better coloring.
"-Metallic or organic dye?"
ANSWER: If you need Lightfastness, Metallic. Organic Dye's might offer some measure of lightfastness but they will fade over time, and I'd be very hesitant to suggest a non-metallic dye and promise anyone that it'd last for 5 years without any significant fading.
"-Process for sealing?"
ANSWER: I have no personal experience in regards to Cold Sealing, so I won't say if it is better or worse. But for hot sealing (98 °C), 3 minutes per µm (You'll have to excuse my EU-ness here), is the norm. And that will protect the dye, and help some in regards to lightfastness, but it isn't a fix-all solution.
2. "What test should be performed on the anodize finish before it goes into the next phase of production to ensure the UV resistance is going to last many years?"?
ANSWER: Well, you are in luck, as you are half way there already, by specifying MIL-A-8625 / MIL-PRF-8625
[⇦ this spec on DLA], Type II / III, Class 2. See, this very specification offers some guidance in this regard, check out section 4.5.4! It has a whole array of information regards to this.
"-UV light test? (too long?)" SEE ABOVE!
"-Seal test? Are there instructions on how to perform a specific test for this application?"
ANSWER: Yes! Anodizing is has luckily move past the ancient days where people were just sticking aluminium into random things and added a lick of power to it. So, some things are standardized and with great methodology behind it. Alas, as mentioned before, I'm from the EU, and we rely on ISO 3210 for a Mass Loss test (You basically weight a test piece for and after removing the sealing with a chemical process, divide it be the surface area and get a value. Preferably this should give a result that is less than 30 mg/dm2.
If your head isn't spinning yet? Welcome to anodizing! And may your path forward be full of knowledge!
- Horsens
March 1, 2023
A. Hiya Scott,
You have a big project! Have you considered an electrolytic type dye?
It's not the standard Azo dye with embedded chromium in the organic molecule that you then seal with Na-acetate and/or HWS; it becomes almost like part of a microalloy on the surface, if that makes sense? Closer to a conversion coating?
I've been talking for years with different OV coordinators for a big customer who wants a peroxide-proof black to go through medical sterilization and keep telling them the same thing :) ... the Azo black (HBL) will eventually turn blue, then grey, and slowly fade ... but the anodize is still good.
If they want architectural level of Pretty, they gotta step up to an actual electrolytically deposited black finish.
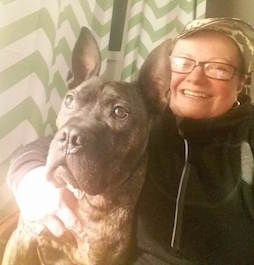
Rachel Mackintosh
lab rat - Greenfield, Vermont
June 9, 2023
⇩ Related postings, oldest first ⇩
Q. We are looking for a method for black anodizing which is UV-proof for optical use. Furthermore we would like to know if there is a method to direct black anodize without use of organic dye. Thank you for Your answers.
P.Moors- Netherlands
1998
A. We are evaluating a new type of anodizing/hardcoating process. It utilizes high voltages in a non-acid electrolyte. Its properties are similar to sulfuric acid anodizing without the loss of fatigue strength. However, it is possible to develop integral colors, such as black. Preliminary testing indicates excellent optical characteristics.
Chris Jurey, Past-President IHAALuke Engineering & Mfg. Co. Inc.

Wadsworth, Ohio
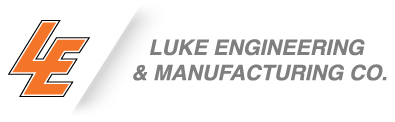
A. We currently use a two step black electrolytic color anodizing, first sulfuric acid anodizing and then AC electrolytic coloring which basically is stannous sulphate. I know by experience the color won't fade against UV if it was processed within certain limits.
Saludos desde Mexico
Guillermo Luna- Mexico City, Mexico
Q. I'm really interested in this topic, and I would like to do a couple of runs using the electro coloring process, the only thing I'm not sure about is what concentration do you use, is this a non acid bath? and how much AC current is needed I for how long
Alejandro Arriaza- Guatemala City, Guatemala
February 1, 2008
Multiple threads merged: please forgive chronology errors and repetition 🙂
Q. We have parts we manufacture anodized type II, class 2 black. The material is both 6061 and cast tool plate. The thickness is about .2 to .4 mil, and the dye is organic. Our anodizing supplier has used nickel to seal our parts, then changed to Teflon at our request. The problem is almost all parts have exhibited a change in color over time from black to a bronze/muted gold. This change is inhibited by a lack of air or residual oil around some tapped holes(fingerprints can help stop it). Parts in plastic bags in the stock room only exhibit discoloring where protruding from the bag.
We had our vendor change to Teflon seal; delays the problem some, doesn't prevent it. He changed dye manufacturers when first notified of the problem. He has checked the acid concentration, cleaned his tanks, etc.; nothing seems to help. Uses large city tap water to rinse (chlorine?). Has anyone seen this type of discoloration before?
Dave Braumann- Sauk City, Wisconsin
2002
A. Color fastness of dyed aluminum anodizing is strongly correlated to seal quality. Poorly sealed parts can fade or change color due to UV exposure, over-the-counter ammonia ⇦ this on eBay or Amazon [affil links] based cleaners, etc. That being said, I have also seen organically dyed black parts fade to gold rapidly at elevated temperatures (even with a good seal!).
Victor Waldman- Naugatuck, Connecticut
Q. That being said what if the part is not at an elevated temperature. What is the best coating to avoid color change due to UV?
Michael Jefferson- Derby Connecticut USA
2007
A. Hi Michael.
Sorry, I am not quite clear if you require black or just no color change, Michael. The familiar dark bronze anodized coatings that are regularly used on buildings and architectural products are extremely stable, involving as they do metal particles rather than organic dyes. Guillermo Luna says you can do this electrolytic two-step process in black, although I'm not personally familiar with its reliability in black. You can get reasonably lightfast organic black dyes if you specify them and seal them well, or you can "overdye", i.e., use the electrolytic inorganic coloring method first, then dye it with a UV-stable black dye.
Good luck!
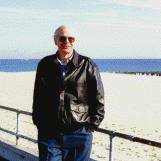
Ted Mooney, P.E.
Striving to live Aloha
finishing.com - Pine Beach, New Jersey
Multiple threads merged: please forgive chronology errors and repetition 🙂
Q. I'm new in anodizing business. Blackening anodizing is new stuff for me. The question is what is the good way to coloring a aluminium part, using dye or electrolytic coloring. If it electrolytic process, what metal should I use?
Thanks,
P.T REXOL - Bandund, West Java, Indonesia
2003
A. Hi Royal,
I wasn't aware aware of electrolytic/2-step treatment giving a good black but Guillermo Luna says you can do electrolytic two step black fine if you're careful. I would guess there are proprietary hybrid blackening methods which would include electrolytic coloring as close to black as you can get, then overdyeing with an organic dye though.
But electrolytic dyeing is expensive and designed primarily for architectural use and strong UV light. For most parts, organic dyes with a good lightfastness rating are sufficient.
Remember that thick anodizing is required for saturated colors, and black is very saturated. 0.005" anodizing is about the minimum, and sometimes even as thick as 0.008" is used.
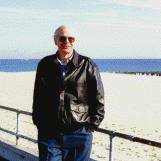
Ted Mooney, P.E.
Striving to live Aloha
finishing.com - Pine Beach, New Jersey
Multiple threads merged: please forgive chronology errors and repetition 🙂
Our black anodizing is not UV stable
Q. Our product was exposed in sunlight. The cover of our product is made from Aluminum with hard anodizing. It passed salt spray test (120 hours) but we found the cover color (black) faded recently. I guess sealing is ok because it passed salt spraying test. I guess the dye of anodizing may not be UV stable but I'm not so sure of it. Our vendor mentioned that dye of anodizing are 100% not be UV-stable so that color fading is reasonable. I need your advise to find the root cause of it. Thanks!
Liu Stephenbuyer - Taiwan
November 11, 2009
![]() |
A. All organic dyes fade in sunlight. Two-Step tin plated anodizing does not fade. Architectural anodizing does not fade. ![]() Robert H Probert Robert H Probert Technical Services ![]() Garner, North Carolina ![]() A. Liu, Aerospace - Yeovil, Somerset, UK |
Q, A, or Comment on THIS thread -or- Start a NEW Thread