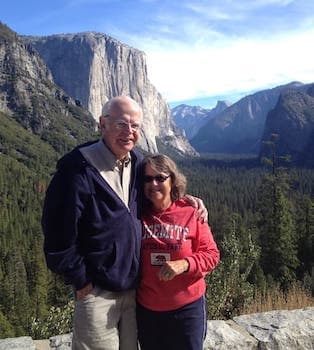
Curated with aloha by
Ted Mooney, P.E. RET
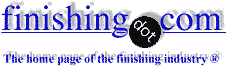
The authoritative public forum
for Metal Finishing 1989-2025
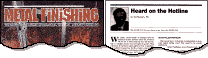
-----
Mu metal plating, coating, and finishing
1998
Q. Any literature out there on how to plate over mu metal?
Thanks,
Greg
A. Don't know of any literature for plating on Mu metal, but I did plate some a few years back.
I first tried anodic sulfuric. 6 V at room temp. Used lead as a cathode. Worked pretty well. Had some spotting and pitting at first, then learned the work had to be dry on immersion into the sulfuric. Followed this with a cyanide copper strike and then cyanide copper plate. Also plated nickel from a Watts solution. As the process evolved, I ended up using an electropolishing formulation for nickel from Electro-Glo.
Good luck
Bob Duvall- Mamaroneck, New York
1997
A. Dave,
As I recall, MU metal is a nickel iron alloy used for magnetic shielding. We used to etch it in a solution of 70 ml H2O, 20 ml HCl,
10 g ferric chloride ⇦ this on eBay or Amazon [affil links] hexahydrate, for 45± 5 sec. at RT. This leaves a very active surface and I suspect you could put a Woods nickel strike over it and then finish plate. Good luck.
Keith Wicklund, CEF-SEavionics - Minneapolis, Minnesota
1997
Does Dr. Seuss fit in somewhere in all this?
A somewhat mumentous occasion: Mumetal listed in Durney's Electroplating Engineering Handbook as 76 Ni, 16 Fe, 6 Cu, 2 Cr, 8.6 g/cu cm..
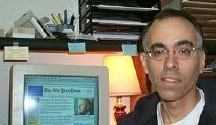

Tom Pullizzi
Falls Township, Pennsylvania
1997
A. Mu metal is used for electromagnetic shielding, its created from a a nickel iron alloy which is then heated in a gas to about 3000 degrees then cooled in stages over about 3 days and costs about £3 per square inch. its very soft and malleable, and is damn good at screening.
Tim Livesey1998
A. To plate mu-metal treat it like any other nickel-iron alloy e.g. INVAR
Peter Vivian- London, U.K.
1998
A. Mumetal is used to realize an external Faraday Cage to protect vacuum tubes from EM noise coming from different surfaces or to realize small metallic boxes used as shielding enclosure for EMI RFI sensitive electronic components. If you need, you can also find specially designed enclosures for vacuum tube shielding.
Regards
Stefano
- Florence, Italy
1998
A. Mu (Greek symbol µ, ASCII character alt 230) metal has many formulations. It is quenched rapidly (several thousand degrees a second) to make it amorphous; there is no identifiable crystallinity. It behaves mechanically, in thin sheets, like flexible glass. Its major claim to fame is the extremely high magnetic permeabilities, which persist up to the microwave region.
doug Dixon- Casa Grande, Arizona
1998
1998
Q. We have a requirement to use Mu-Metal for screening a 100 KHz switching transformer.
Initial tests with hand folded up Mu metal worked well.
For production we had the parts made by a chemical etching process. which was then Electroplated with tin, folded up to shape and spot welded.
Our assumption was that the spot weld would have little effect over the area of interest and this does not seem to be our initial problem. We have done some quick comparative testing between unprocessed and processed material that has not yet been spot welded and found that the post electroplate process material already has no detectable magnetic performance left, As chemical etching has no implied mechanical stress or heat to unalign the crystalline structure I can only conclude that electroplating the non magnetic Tin destroyed the Magnetic field performance.
Question Does any reader have experience with electroplating Mu Metal or Spot welding / soldering etc. and do they have any recommendations?
Thanks,
Stuart Fawcett, Principal Engineer -- Chessington, Surrey, UK.
A. I am sure that you have covered the magnetic properties of plated metals, but just in-case, we used the magnetic properties of electroless nickel to our advantage in 1960 for integrated circuit connection. My memory is a little fuzzy, but as I remember it, the magnetic properties only came from one bath. We had used both baths that utilized the Boron reducing agent, and hypophosphite reduction, but I don't remember which worked. Since the bath with the boron reducing agent plated much faster, I suspect that this was the bath. I would suggest trying this for magnetic shielding, even over plastic.
James H. Gould- Kokomo, Indiana
2000
Black coating on mu metal
I am searching for a supplier and /or information for a black coating/plating on mu metal. The parts are small (.500 dia. or less),and will operate at - 200 °C in liquid nitrogen. The coating or plating can not alter the shielding properties of the material. The application is an optical device. Any information regarding this inquiry will be helpful.
Aaron KriegerMachine Shop - Stuart, Florida, USA
2003
Q. I must reduce the risk of corrosive attack on electronics assembled with mumetal covers. The silver finishing is necessary for solder issues. What type of silver finishing is possible to apply on Mumetal parts. There is a MIL specification ?
Thank you for your attention.
Guido Lozzicommunications equipment - L'Aquila, Italy
2003
2003
A. Mumetal is an unusual alloy that provides shielding from electromagnetic radiation per MIL-N-14411C and ASTM A753. It is nominally 80% nickel and 20% iron, but I found a proprietary composition Permalloy C® Mumetal® Ni77/Fe14/Cu 5/Mo 4. I suggest pretreatment per ASTM B343 and application of a Wood's nickel strike before silver plating, but anyone with experience should feel free to comment.
Silver plating specifications that might apply are QQ-S-365 [from DLA] , available from http://assist2.daps.dla.mil/quicksearch, ASTM B700, available from www.astm.org and AMS2410, AMS2411, AMS2412 & AMS2413, available from www.sae.org
Both QQ-S-365 and ASTM B700 allow chromating the silver for better corrosion resistance, as Grade A and Class S, respectively. I am unfamiliar with the AMS specs.
Ken Vlach [deceased]- Goleta, California

Rest in peace, Ken. Thank you for your hard work which the finishing world, and we at finishing.com, continue to benefit from.
Why coat Mu Metal with MgO?
Q. I am trying to find out why Magnesium Oxide (MgO) is applied to Permalloy 80 (Mu Metal). We have always purchased Permalloy 80 strip (coil) stock that was coated with MgO. However, the vendor (Spang Specialty Metals) has since gone out of business. Why is it coated with MgO and ...
Where can we get it done? Please advise.
RICK FABRIZISpecialized Electronics Manufacturer - LANESBORO, PENNSYLVANIA, U.S.A.
2004
2004
A. Rick, one reason I can guess at is that perhaps the MgO serves as a barrier to keep the parts from sticking together when they are annealed. Nickel iron parts are annealed after final forming / machining to give them the best soft magnetic properties, at about 2100 to 2200 °F. If you just dump parts in a hydrogen, argon, or vacuum furnace they'll stick together after a few hours at temperature, and the follow-up hammering to separate them can adversely affect dimensions.
Again, this is a guess, but a reasonable one. If you're sourcing your material from CarTech, I can attest to the competence of their customer service staff.

Lee Gearhart
metallurgist - E. Aurora, New York
A. The material is coated to reduce eddy current loss in inductor application. Standard procedure in my industry.
Tom Bui- Marengo, Illinois, USA
2004
A. MuMetal® is a registered brand of Magnetic Shield Corporation. Although historically mumetal was the generic name used for magnetic shielding material, it does have a specific chemical composition.
MuMetal can be finished with paint or plating - however certain precautions must be taken to maintain grain structure of the material so it provides maximum field attenuation.
Mark Wickler- Bensenville, Illinois
April 12, 2010
April 13, 2011
Q. Is MgO coating similar to Magnesium Methylate coating?
Can some tell me who can help me do such coating.
I have mumetal strip @ 0.05 mm and want to coat 10 micron thickness of MgO on both sides.
After coating I want to cut them into tiny pieces and then anneal them. Is this OK???
Please HELP!!!
Thanks a lot!
Susan
- Taiwan
Q, A, or Comment on THIS thread -or- Start a NEW Thread