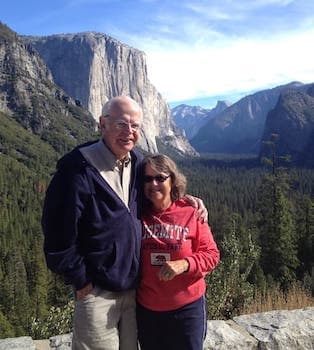
Curated with aloha by
Ted Mooney, P.E. RET
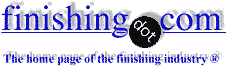
The authoritative public forum
for Metal Finishing 1989-2025
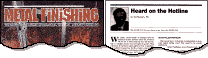
-----
How to get good adhesion of polymer concrete onto aluminum
1998
I am looking to fill an aluminum extruded beam with an epoxy polymer concrete for vibration/cost benfits for a machine tool application. The polymer concrete is a mixture of a two part epoxy resin and silica sand. My problem is in promoting good adhesion between the aluminum and epoxy. It seems a common anodized finish is too slick for a good bond. What finishes would give the best adhesion:
-some type of anodize
-chromating (is chromating cheaper than anodize, what are environmental hazards),
-sandblasting
-any other chemical finish
Digital Cybermation
1997
Chromating is cheaper than anodizing. There is a general movement is industry to try to eliminate hexavalent chromium such as is used in chromating, so it may not be the best long-term solution anyway.
But the answer most probably is phosphoric acid anodizing. This is used in the aircraft industry for "adhesive bonding" of aluminum. You should be able to locate ASTM or MIL specs covering the process.
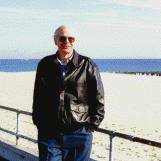
Ted Mooney, P.E.
Striving to live Aloha
finishing.com - Pine Beach, New Jersey
1997
Hi Richard,
I am going to take a guess that the problem is not the anodize. A two part epoxy gets quite hot when it is curing. Many plastics have a cooeficient of expansion about 10 times metal. I think that it is getting hot, expanding and then cooling and shrinking in size and pulling away from the wall of the pipe. Concieveably it could slide out if it got cold enough.
Alternate plan. One of your local hardware stores or builder supply stores sells a concrete patching mix that is single component. It might give you a satisfactory solution. You could play with mixtures of sand or used grit to cut down on the cost.
It might be slow to cure in the pipe.
You might want to check out 5 gal pails of something like Bondo ⇦ this on eBay or Amazon [affil links] from the manufacturer. It also will have a problem with heat if there is a lot poured at one time.
There are lead/antimony/bismuth very low melting (under 200F) metals that actually expand when cooling.
James Watts- Navarre, Florida
There is one idea might help your problem. In order to fill an aluminum extruded beam with an epoxy polymer concrete, you have to lay one layer of silicone glue in side of the aluminum beam and let it dry for 20-24 hours. Then, mix and fill epoxy. Anyway it will be easier if you use composite pipe which have their property very close to aluminum (stucture). If you could give me more information what you really need it might be much more helpful.
I'm working at the resin, composite manufacture company in THAILAND. So, If you have any questions please feel free to ask. I will be very happy to share you some idea it might help.
Supachoke Samargasevi- Nakhonphathom, THAILAND
2001
Q, A, or Comment on THIS thread -or- Start a NEW Thread