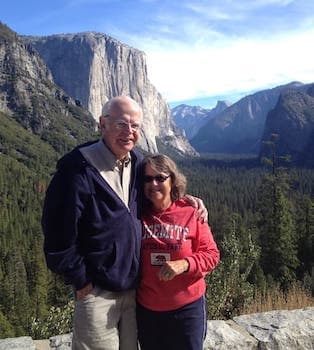
Curated with aloha by
Ted Mooney, P.E. RET
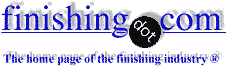
The authoritative public forum
for Metal Finishing 1989-2025
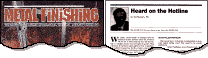
-----
What are Bipolar Anodes, and How are they used in electroplating?
Q. I am interested in finding information about the use of bipolar anodes. I am experimenting with this type of auxiliary anode for use in a chloride zinc-nickel plating bath. Many of the references that I have found only introduce the subject without providing any details. I want to use soluble anodes since the gassing of an inert anode will oxidize a proprietary additive.
John L. Zable1998
1998 A. CORRECTION: Tom Pullizzi pointed out a reference in Lowenheim's "Electroplating" ⇦[this on eBay , Amazon, AbeBooks affil links] that says it will outgas. Also Graham's "Electroplating Engineering Handbook ⇦ this on eBay, AbeBooks, or Amazon [affil links] " p. 103 shows bipolar building on one side. I will concede to the experts. I had used it in sulfamate nickel that was operated at under 4 volts with very little buildup on the negative side and it increased throw into the sharp corner of the part. No attack on the anode. Unable to tell if it outgassed as it was over a foot down in a well agitated solution. No damage noted to the solution, but it is a robust bath. If you are going to the trouble of making it out of soluble material, why not make it a powered aux anode and make it work even better. A second power supply may be required to reduce voltage applied to the anode at the closer space. A voltage reduction circuit could be used also, but this will mess up the amp hours as the circuit wastes the extra electricity as heat. James Watts- Navarre, Florida 1997 Thanks, James. Specialty Testing & Equipment offers a device that may address that ampere-hour meter problem. It's a small 'current controller' that you can power the aux anode from, and it's powered from the main bus bars rather than a separate AC supply. If you put the power draw leads beyond the shunt, and if the device is efficient, it would seem that the ampere-hour meter should remain accurate. ![]() Ted Mooney, P.E. Striving to live Aloha finishing.com - Pine Beach, New Jersey I am not sure if I have seen this device or not. If it has been at Sur-Fin, I have. If it has huge cooling fins of extruded aluminum, it is there to dissipate heat that is generated by the voltage reduction. This heat shows up on the amp hour meter the same as if it were plating. I am not an electronics person, just have not seen any Voltage adjuster that did not generate some heat. It is possible that it is irrelevant or is constant enough that it could be compensated for with a slight increase in amp hours. If it is the one that I have seen, it is really a nice accurate piece of equipment. James Watts- Navarre, Florida 1998 The auxiliary anode can be wired to the main buss with a resistive voltage reduction device. The 'resistor' should not affect the total amp hours as the amp hour measurement is not a measurement of power. It is a measurement of amperage. All components of a series circuit will have the same amperage flowing through them. This means the auxiliary anode will have the same amperage as the resistor. They do not add. The main buss will have the amperage from the bath and the amperage through the auxiliary leg. The heat on the auxiliary resistor can be calculated: watt losses are voltage times amperage. Since amp hour measurements do not use voltage you are safe to use the main shunt as an accurate source of measurement of the total amperage flowing in the tank via whatever path you give it. John BougneitJP Tech, Inc. 1999 |
QUICKSTART:
This "theft" of electrons from the anode converts the anode metal to positively charged, soluble, ions which dissolve into the solution (the anode metal is "reduced"). The positively charged ions migrate through the solution, attracted to the negatively charged workpiece. When the metal ions reach the cathode and rejoin their electrons, the ions are "oxidized" back to metal onto the workpiece.
Lowenheim's piece of metal is item DE, and as reflected in his sketch, because the electrons run through the metal, a shortage of electrons develops at the end nearest the anode (the right hand end of item DE), and a surfeit of electrons builds up at the cathode end (the left hand end of item DE). This bipolar effect can be used constructively, as Lowenheim illustrates, to channel current into the inside cup shape of item C, to produce thick plating there whereas this recess would otherwise be a low current density area. |
Bipolar anodes for hard chrome plating
Q. Hi. Can anybody explain about bipolar anodes used in hard chrome plating?
Manjunath lingan- Mumbai, India
January 5, 2014
A. Hi Manjunath. I have personally never seen bipolar anodes used in hard chrome plating, but I'm certainly not as experienced as some of our readers. So if they have been used, I'd like to hear about it; and if they haven't, I'd like a deeper understanding of what makes them unworkable.
Regards,
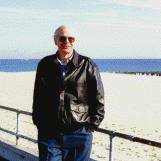
Ted Mooney, P.E.
Striving to live Aloha
finishing.com - Pine Beach, New Jersey
January 2014
Q. Thank you Mr.Ted Mooney, P.E. RET, I am one of your fans; actually much of your advice was excellent and extremely helpful to me.
Here I would wish to ask your advice regarding the bipolar anodes. They have mentioned that to place a piece of metal between anode and cathode which will not be connected to either of the terminals.
If the metal is simply dipped inside the bath are there chances of the metal to dissolve/react, and the metal may develop immersion plating due to galvanic action, or nodules will develop causing the terminals of the positive and negative to touch each other and create short circuit?
Please let me know more on this topic
Special process - Mumbai, India
January 7, 2014
A. Hi again. All of your fears about bipolar anodes are theoretically problematical. The actual case will depend upon whether the anodes are made of soluble material or dimensionally stable material for the plating solution being used, etc.
However, I don't want to leave the impression that bipolar anodes are frequently used because, to my knowledge, they're not. What is much more common is "auxiliary anodes". In the case of auxiliary anodes, the extra piece of metal is actually wired to the anode (rather than electrically floating between the anode and cathode as shown in this modification of Lowenheim's sketch, where I've added the red jumper wire.
Auxiliary anodes are extremely common in chrome plating.
Regards,
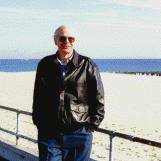
Ted Mooney, P.E.
Striving to live Aloha
finishing.com - Pine Beach, New Jersey
January 7, 2014
Q. Hi Ted. I observed shadow effect of teflon bush when used as an maskant in the hard chrome plating; can teflon behave as an bipolar anode causing distortion?
manjunath lingan [returning]Electroplating - Mumbai, India
February 7, 2014
A. Hi Manjunath. Teflon is non-conductive and thus it cannot function as a bipolar anode. But non conductive materials can act as shields and thereby cause desirable or undesirable distortions.
Shields are often employed in plating, and especially in electroforming. However, shields are rarely used in chrome plating to my knowledge: I suppose it's because in most plating the thickness deposited is proportional to the current density, whereas chrome plating tends to be a go/no-go process whereby if the current density is reduced you get no plating at all rather than proportionally thinner plating.
Regards,
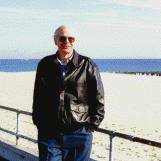
Ted Mooney, P.E.
Striving to live Aloha
finishing.com - Pine Beach, New Jersey
February 2014
Q. We have a continuous plating line for fine tungsten wire, we use copper contact rollers to connect the wire to ground (cathode) before each tank, but for a new high speed application we need to change that concept. I recently came across this patent from Westinghouse US3287238A where they use two steel mesh (one as cathode, one as anode) and passed the wire from above it. Apparently it is able to replace the contact system and polish the wire. Can you explain such a cathode configuration, what is it called, how it works, and how it can be implemented for a complete line?
vedant aggarwal- INDIA
April 12, 2020
April 2020
A. Hi Vedant. Although I have not actually seen contactless electrochemistry like this, I have long heard of it being employed in high-speed electrochemical cleaning of steel strip; the Westinghouse patent could certainly have been gainfully employed.
Something to be remembered in trying to understand how such things can be done is that the conductivity of metal (which electrons can flow through) is many orders of magnitude higher than the conductivity of even a highly conductive metal finishing solution (where the electricity can only flow by the migration of charged ions). Electricity will take the path of least resistance -- so it will flow through the metal rather than the solution if you let it :-)
So if you keep the anode and cathode fairly far apart, but you run the wire close to the anode and then close to the cathode, the current will primarily flow from the anode to the wire, then through the wire, and then from the wire to the cathode.
This means that the wire becomes cathodic when it is near the anode in section "1", and it becomes anodic when it is near the cathode in section 2. Although it is beyond my ability to quickly sketch, there is no reason that the anode and cathode cannot be hollow mesh tubes which the wire runs through the center of.
Regards,
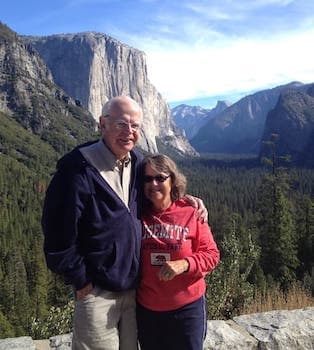
Ted Mooney, P.E. RET
Striving to live Aloha
finishing.com - Pine Beach, New Jersey
April 17, 2020
A. Ted has the right idea but I think the configuration shown may struggle due to the relatively poor conductivity of tungsten.
I designed and ran a contactless system back in the 90s that worked very well.
The wire, in my case tape, ran through a cathodic clean followed by an anodic etch with a small spray rinse between, rinse and blow dry.
The logic of the current flow is shown by ...
I hope these make it clear. I had no idea of the Westinghouse patent when I designed this which is only part of a much larger plant to make battery plate material.
Two small points. Tubular electrodes make loading the cells much more difficult, plates work fine.
The sectioned cell shows electrolyte pumped up from a reservoir and returning via a weir. The baffle over the input is important unless you want to be showered in electrolyte! Test with water first to confirm the flow rate.
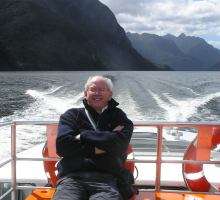
Geoff Smith
Hampshire, England
April 19, 2020
Q. Thanks, ted.
Thanks, geoff.
Does this configuration bring any added advantage during ELECTROPLATING; can it reduce the surface oxidation, before a plating strike (nickel here) is applied on tungsten, so as to create a more adherent surface for plating? This will be beneficial especially for refractory metals which form very tenacious oxides.
Similar to cathodic cleaning (hydrogen gas) during electropolishing mentioned by geoff.
BTW, I found some info about contact-less cathode in "Electroplating Engineering Handbook pg.504, chapter on anode & cathode"
[picture here]
"Another special case in which continuous strip or wire can be alternately given cathodic and anodic treatment in one tank without direct current contact"
Regards,
- DELHI, India
----
Ed. note: In the 4th edition of the Electroplating Engineering Handbook ⇦ this on
eBay,
AbeBooks, or
Amazon [affil links]
that quote and pic are on pp. 631-632.
Q, A, or Comment on THIS thread -or- Start a NEW Thread