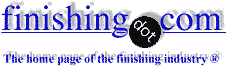
-----
Paint adheres poorly to galvanizing
We are a supplier of top of the line steel poles and outdoor sports lighting fixtures. Occasionally our customers request colored poles to blend in with the surroundings or to match their 'team colors'.
All of our poles are hot-dip galvanized for corrosion protection. If paint is requested, we send the poles to be powder coated over the top of the galvanizing to match the requested colors. (both processes are out-sourced)
Once galvanized, the poles are sent to the painter. Prior to the paint application, the areas on the product that are to be painted are shot blasted with a small steel shot, to give the paint a better surface to adhere to. Afterward, they are primed and painted.
We still seem to have difficulty with getting the paint to adhere to the galvanized surface. If the pole or electrical enclosure are accidentally banged around, the paint will chip, which to some degree is to be expected, but you can then proceed to remove additional paint by picking at it with just a fingernail. In doing this and analyzing the paint chips, the paint is adhered to the primer, but there is no adhesion between the primer and the galvanized surface.
We are looking for assistance in solving this problem. It seems the auto industry has resolved this as most of them are using galvanized sheet metal for various body parts and those paint systems hold up quite well.
Most of the pole sections are 40' in length and range in diameter from 9-1/2" up to 24".
Jim Bernslighting mfgr.
1998
1998
Jim:
The automotive industry has solved most of its problems by using a zinc phosphate pretreatment under its coating system. You could adopt that solution, as well. But I think there's another way. What corrosion resistance standard do these poles have to "adhere to" (pun intended)? Is it absolutely necessary to have ALL the poles hot dip galvanized?
This seems like an extra expense to me. A quality iron phosphate pretreatment and a quality powder coating can go 500 hours or more in salt spray (ASTM B117). It is working well for other lighting and appliance companies that we do business with. Granted with aluminum pole and fixtures, an abrasive treatment (e.g. sand blasting, etc.) does improve adhesion significantly.
Hoping this gets you thinking.
Good Luck!


Craig Burkart
- Naperville, Illinois
Our company manufactures Telecommunications towers, monopoles for many years. Brazilian standards require paint over galvanizing and for many years we had problems. Today we are using one coat epoxy polyurethane with very good results. Our towers are factory painted and touch ups are made in the field without problems.We are researching this area for new products and methods.
Luigi Cosenza- Sao Paulo SP Brazil
1998
Q, A, or Comment on THIS thread -or- Start a NEW Thread