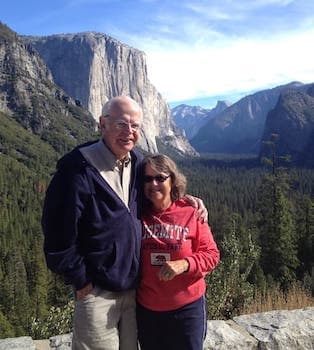
Curated with aloha by
Ted Mooney, P.E. RET
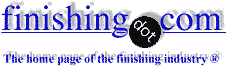
The authoritative public forum
for Metal Finishing 1989-2025
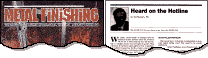
-----
Need CLEAR hard anodize coating
Q. Seeking information CLEAR hard anodize coating (Reynolds?)
Does anyone have information on a CLEAR hard anodizing process for aluminum developed by Reynolds? I worked on a project 20 years ago using 5051 aluminum where we had an almost perfectly clear hard anodize coating.)
Robert S [last name deleted for privacy by Editor]1998
A. We do hardcoat here, but even when left undyed it is not clear or colorless. It turns colors from bronze to grayish black depending on the alloy and thickness of coating we apply.
There are proprietary chemical additives on the market that produce colorless coatings.
I believe the ANODAL EE additive which Sandoz aka Clariant [Charlotte, NC] markets is for clear hardcoat.
David A. Kraft- Long Island City, New York
1997
A. I have an old reprint from the Aluminum Co. of America, Alcoa, on Martin Hard Coating, that's not Reynolds, is it?
Bulletin No. 6, January 1952.
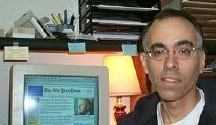

Tom Pullizzi
Falls Township, Pennsylvania
1997
1997
A. I spoke with our founder, W.P.Hayduk, about "clear" hardcoating. He has worked in hardcoat anodizing since 1953 and was involved with many of the process developments. He has never seen a "clear" anodized coating which could meet the minimum requirements for thickness(2.0 mils +-20%) and wear resistance(TWI < 1.5) of MIL-Spec hardcoating. Conventional low temperature (32 F) hardcoating on normal aluminum alloys results in a dark bronze, gray, or black color. This appearance can be lightened by the following methods:
1)Alloy Selection- Generally, the purer the aluminum the lighter the color. The alloying elements Mg and Zn also contribute to lighter appearing hardcoatings.
2)Coating Thickness- Hardcoatings up to 0.6 mils are almost clear. Rapid darkening occurs from 0.7 mils to 1.6 mils. In this range, small differences in thickness can make large shade differences. Over 1.7 mils, the coating becomes quite dark.
3)Electrolyte Temperature- The higher the temperature the lighter the coating. Higher temperatures are also associated with softer coatings.
4)Bath Composition- Acid concentration, dissolved metals, and bath additives can have an effect on the final appearance.
In the 1960's, Reynolds developed a multipurpose anodizing electrolyte process. Some of the bath additives sold today are based on this process. At 2 mils, this process does not result in a colorless coating.
If someone has developed a clear MIL-Spec hardcoating, I would like to supply free test panels for evaluation.
Chris Jurey, Past-President IHAALuke Engineering & Mfg. Co. Inc.

Wadsworth, Ohio
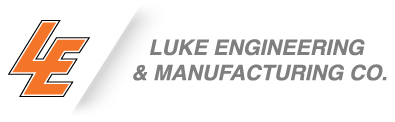
A. Thanks for the great post, Chris. I guess the overall conclusion is that, if done right, a clear anodize coating is achievable but you won't get it thick enough to be considered actual hard coating without it coloring up.
Regards,
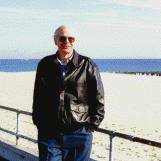
Ted Mooney, P.E.
Striving to live Aloha
finishing.com - Pine Beach, New Jersey
January 3, 2009
Q. Can you tell me, what Caine anodize is.
"Hard Coat Anodize per MIL-8625, TYPE III, CLASS I. No DYES AND DO NOT SEAL .0020-.0025" thick. 'Martin Hard Coat Dark' or equivalent".
Thank you, Erves.
ceramics - Fremont, California, USA
October 14, 2013
A. Hi Erves. Sorry, "Caine" means nothing to me. Could be a company name, a typo -- just about anything. Please put it in the context you saw or heard it in. Thanks.
Regards,
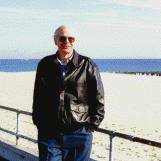
Ted Mooney, P.E.
Striving to live Aloha
finishing.com - Pine Beach, New Jersey
October 16, 2013
A. Martin Hardcoat is an early hardcoating process developed by Glenn L. Martin Co, then Martin-Marietta Co., and now Lockheed-Martin. It uses a low temperature sulfuric acid electrolyte saturated with carbon dioxide.
Chris Jurey, Past-President IHAALuke Engineering & Mfg. Co. Inc.

Wadsworth, Ohio
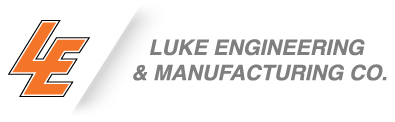
October 16, 2013
Q, A, or Comment on THIS thread -or- Start a NEW Thread