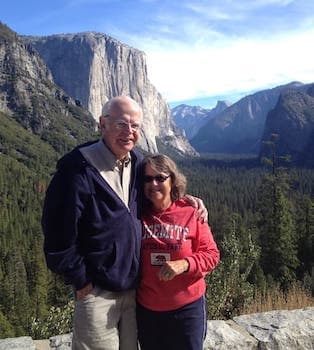
Curated with aloha by
Ted Mooney, P.E. RET
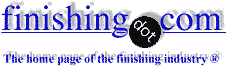
The authoritative public forum
for Metal Finishing 1989-2025
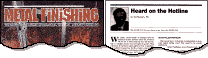
-----
Re-baking to save Hydrogen embrittled fasteners
[editor appended this entry to this thread which already addresses it in lieu of spawning a duplicative thread]
Q. If an embrittlement bake is interrupted -- only baked 4 hrs @ 375 °F, should be 15 hours -- can it be baked again to continue the 15 hours? Or What can be done now
employee - PANORAMA CITY
February 6, 2025
⇩ Related postings, oldest first ⇩
Q. Any thoughts on the risks of accepting electroplated fasteners which have initially failed a hydrogen embrittlement torque test, then rebaked (and finished) then torque-tested again?
Dave Daigle1997
A. On an aircraft, rocket, ordnance or auto -- no. Risk someone else's tail, not mine. There has been some work done on re-embrittlement that would make this frightening. To a certain extent, the damage has been done. The reprocess just mitigated it enough to pass. Of course, this is a personal opinion. I do not think that it is the intent of a Mil Spec to allow this.
James Watts- Navarre, Florida
James, Thanks for your input. The fasteners in question DO NOT go on any aircraft, rockets, ordnance or automobiles. I should have made this clear. But you are correct, I don't see how rebaking would heal any microcracks or microvoids. Rebaking is not an option we accept, and the problem has not come up, but one fastener supplier did suggest rebaking as an option to me the other day.
A. Dave,
for a non critical use, stripping, annealing and then hardening including the proper draw might be a tolerable recovery. Jim
James Watts- Navarre, Florida
A. Dave -
The problem you described is more typical than anyone would like to believe. The solution proposed is a common one and can be effective in salvaging material. There seems to be a misunderstanding in the way hydrogen damage or embrittlement works...
If a sample has developed microcracks or microvoids then the proposed fix is of course worthless, but typically fasteners do not show this type of damage until after they have been stressed. The damage that hydrogen causes requires a tensile stress, either residual or applied.
My job over the last 8 years has been performing failure analysis studies. Last year alone we did over 550 failures, many of them dealing with fasteners and hydrogen embrittlement.
The one caution I do have for anyone that does what was suggested is as follows: After stripping, the parts should be given an embrittlement relief because the pickling or stripping operation is a known hydrogen contributor. If this intermediate bake is not performed you can effectively worsen the situation because of the added amounts of hydrogen that can be introduced.
It is not a trivial decision and the follow-up testing needs to be agreed upon before hand....
Hugo Menendezfailure analysis director, Senior Metallurgist
A. The effectiveness of a delayed baking process is dependent on the severity of the embrittlement. Mr. Menendez is correct that stress is required to create nonrecoverable damage from hydrogen. If enough hydrogen is absorbed, even minor residual stresses are enough to cause unrecoverable damage. In my experience, steels with moderate hardness can recover from delayed baking. High hardness steels, 40 HRC, probably will not. The best bet is to try a rebake and redo the testing. If the testing is OK, the parts will probably be acceptable for noncritical applications.
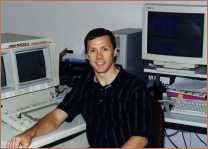
Larry Hanke
Minneapolis, Minnesota
![]() |
I agree that delayed baking and retesting of the parts may alleviate the hydrogen related failures. I would like to suggest the possible use of mechanical plating as an alternative to the electro-deposited coating. If this has been a one time occurrence then some sort of parameter was out of spec when these parts were coated. If this has been an intermittent or ongoing difficulty than the use of mechanical plating method would alleviate this concern. Bob BeaChicago, Illinois 1997 |
Q. I do have a question for the illustrious panel. We manufacture shock absorbers for automobile market. What tests can be performed to confirm whether a batch of piston rods have been through a hydrogen embrittlement process or not?
Srinath Nandyal1998
Q. I have a question to Hugo Menendez in regards to additional hydrogen embrittlement during stripping: you said: "because the pickling or stripping operation is a known hydrogen contributor".
Most of the stripping methods used for stripping coating from high strength steels do not emit any hydrogen while the stripping takes place: these are based on oxidation reactions versus simply dissolving in acid where the metal being stripped (and the base metal too!) substitutes the hydrogen in the acid...
Here are the examples of stripping methods that I consider as not causing any additional hydrogen:
1. Stripping of Chrome plate anodically in alkaline solution.
2. Stripping of Cadmium in ammonium nitrate solution.
3. Stripping of Cadmium, Nickel, Zinc, Tin, Copper, etc. from steels in alkaline nitro-sulphonic acid with cyanide solutions (there are several proprietary and generic variations of this).
4. Stripping of silver plating from steels by anodic treatment in cyanide solutions.
5. Stripping of silver, nickel, cadmium, copper, etc. from stainless steels (in case you wonder, there are several high strength stainless steels susceptible to embrittlement - mostly PH series) by immersing in ~50% nitric acid.
In fact, I am not sure if I can name a stripping method that anyone concerned with embrittlement would use on high strength materials which will emit hydrogen while stripping.
Keeping the above in mind, why do you want to perform a bake after stripping?
Max Steincaptive metal finisher - Montreal, Quebec
1998
A. Most tests for hydrogen embrittlement use a sustained static tensile force. If the test samples fracture or crack, hydrogen embrittlement is indicated. If no cracks occur, the parts are free from embrittlement.
The trick is to determine the magnitude of force and the length of time for the test. For a component like a cylindrical rod, an axial tensile force would be ideal. But without access to an appropriate machine for this, I would probably devise a three-point bend test using a vice or dead-weight loads. A notch in the test sample concentrates the stress and gives a more severe test for embrittlement.
The sample should be bent to just under the material's yield strength. You can determine this by bending and releasing a sample until it maintains a permanent set - for the test use a bend that is slightly less than the smallest bend or load causing a permanent set.
A typical time period for the test would be 200 hours.
Good Luck
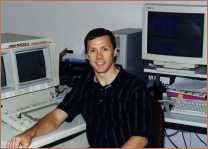
Larry Hanke
Minneapolis, Minnesota
Q. I would like to find from Mr. Hanke, when do they use the 2 million cycle vibration fatigue test for hydrogen embrittlement and what is its purpose. Is the sample under tensile load under those circumstances?
Mandar Sunthankar- Fort Collins, Colorado
1998
A. Although neither a metallurgist nor knowledgable in testing, I sort of disagree on this one! I feel that the testing laboratory may not be privy to the thoughts & plans of the design engineer/design authority, and won't necessarily correctly guess what the designer felt was critical vs. non-critical. S/he is therefore not in a great position to develop a test to verify that a part is satisfactory without the specifier involved in the resolution. Sometimes, perhaps to the opposite of expectation, the factor of safety is 3 or 5 on a non-critical part, and 1.1 on a critical one :-)
Parts are supposed to be hydrogen relieved within a specified period, whether it be 2 hours, 4 hours, or 24 hours. To say that it's okay to relieve them days or weeks or months later, as long as they pass some test sounds dangerous. The B-8 committee of ASTM struggled with this time-delay factor for the better part of a year, and it seemed to have ended in some acrimony. Overriding the standards committees and the designer can be dangerous business as James' warning about potential re-embrittlement should remind us.
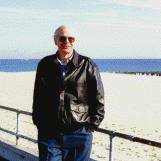
Ted Mooney, P.E.
Striving to live Aloha
finishing.com - Pine Beach, New Jersey
Q. For a number of years now, our company has specified that all chrome plated carbon steel (usually alloy 1050 Rc 40-50) pen clips receive a "hydrogen embrittlement" bake at 500 °F for 8 hrs within 24 hrs following the plating cycle. In testing of complex stamping forms (i.e. sharp transitions and small radius bends), this practice has proven to yield extended flex cycling performance compared with parts which are not baked.
Elimination of the bake process is now being considered for some of our less complex design pen clips. This proposal is because we have found that water spots become permanent stains when the clips are baked. If the parts are not baked, the water stains simply wipe off. We have worked hard to eliminate the visible water spots, but our company standards concerning cosmetic appearances is quite rigorous.
I am concerned about increasing the potential for mechanical failures (hydrogen embrittlement) just to improve cosmetic appearances and manufacturing yields. Can anyone provide any comments or recommendations concerning this issue?
Tom Clem- Lincoln, Rhode Island
2000
A. If the new clips have limited need for flex, you can make make them out of a softer steel, and not bake them.
If they must be this hard, you must continue to bake them unless you decide that (since the clips are not a critical item) you will make the economic decision to trade increased breakage for lower cost.
But I think you're much better off fixing the first problem of rinsing/drying stains, not talking yourselves into creating a second problem of unbaked parts. Good luck.
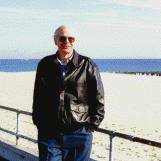
Ted Mooney, P.E.
Striving to live Aloha
finishing.com - Pine Beach, New Jersey
A. I address only the staining issue mentioned by Tom Clem. You could use a commercial demineralizer which would eliminate any visible stains. This assumes you blow-dry the parts after final demineralized rinse to a reasonably dry finish. We used such a device for copper plating and the results were better than we expected. The cost was also reasonable. Hope this helps.
John H. Brown- Damascus, Virginia
Hydrogen Embrittlement bake was NOT performed
Q. We have received parts from a vendor who we asked to process per AMSC26074 Class 1 Grade C. The parts have a hardness result of 40-42 HRC. They did not do the Hydrogen Embrittlement Relief Bake. It has been 9 months since we received them and are now coming out of stock for assembly. Visually inspecting them, the parts don't have any fractures or cracks and the specification does not address this issue. My question is, are these parts acceptable to use?
Carolyne Padilla- Inglewood, California, USA
May 18, 2020
A. Hi Carolyne. Hopefully you'll get personalized responses, but we appended your inquiry to a thread on the same subject so you'll have some opinions you can read in the meantime :-)
Regards,
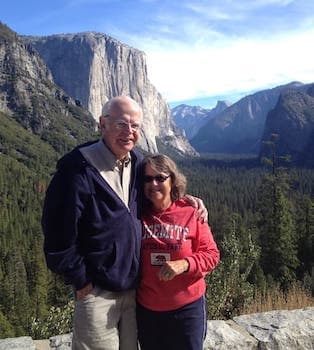
Ted Mooney, P.E. RET
Striving to live Aloha
finishing.com - Pine Beach, New Jersey
A. Hi, Carolyne
AMSC26074 D paragraph 3.4.1 says: Within 4 hours after coating, coated class 1 parts that have a hardness of RC40 or above shall require HE relief bake...
Paragraph 4.1.1 says: All items shall meet the requirements of sections 3 and 5. etc...
If your vendor sent you non-inspected item, this item is non-conforming to the spec.
AMS2759 paragraph 7 says: Parts not heat treated in accordance with specification... will be subject to rejection...
Very sorry...
- Lod, Israel
A. Please keep in mind that baking does not eliminate the risk of hydrogen embrittlement. It does significantly reduce that risk. Visual inspection IMHO will tell you nothing. If you take a couple of dozen of these parts and subject them to the stress or tension that they would be subject to in service you can be fairly sure that they won't fail in the field. A typical test for threaded fasteners would be 75% of proof load. If even one fails, they are toast.
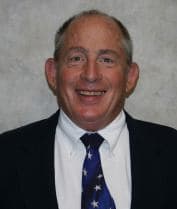
Tom Rochester
CTO - Jackson, Michigan, USA
Plating Systems & Technologies, Inc.

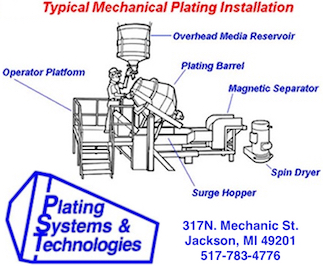
A. Hi Carolyne,
Hydrogen embrittlement is considered a time-dependent effect and the effect happens in hours.
I work in the Aerospace industry, so if these parts were to arrive at my desk for consideration they would rapidly proceed to the scrap bin.
You can test for hydrogen embrittlement, however, the test is destructive. So, if you only have a few parts, it's just not worth testing, but if it's a batch of hundreds or thousands of fasteners, then you may be able to justify testing a percentage, although, if it is for an Aerospace customer I wouldn't bother, as I'd be very surprised if they would accept any testing regime.
- Yeovil, Somerset, UK
A. An option would be to explain the situation to the customer. If non-structural/critical they may be willing to accept the parts at a discount. I work in aerospace. I would not accept these parts for any structural application. I would, however, be pleased with the seriousness and integrity that my vendor applied in this situation.
Andrew Stryker- Xenia, Ohio USA
A. Steel part with hardness 40-42 HRC, after electroless Nickel plating has to be baked for Hydrogen Embrittlement relief as soon as possible (majority of specifications would specify within 4 hours). After that - it is too late, the damage is irreversible and the damage is not detectable visually! (Actually one smart engineer said once that inventor of a non-destructive method to detect Hydrogen Embrittlement will become a millionaire overnight).
*Even more info - spec AMSC26074 is an old spec and it is not updated anymore. It specifies short bake for 3 hours only. Currently, newer AMS specs require 8 hours of bake for such parts after electroless Nickel plating.
- Winnipeg, Canada
September 4, 2020

Q, A, or Comment on THIS thread -or- Start a NEW Thread