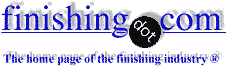
-----
Minimum time before handling chromated parts?
1998
Sirs,
We need, due to a tight schedule, to shorten the time between the application of Alodine process and the mechanical use (assembly) of the treated Aluminum parts.
According to ASTM B449 (7.1) the chromate conversion coatings should be "handled carefully for the first 24 hours after treatment...".
AMSQQP416(6.1.2.2) "require a sufficient period....approximately 24 hours at 70^F to 90 °F...".
Do you have any Good Engineering Practice to decrease the drying time?
Thanks
Asaf Katz
Many shops use a final warm rinse (not over 140 °F), followed by a forced air dryer heated by hot water or steam .
Plenty of air, and not much heat, seem key to accelerating the drying without dehydration of the chromate film.
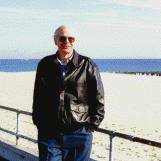
Ted Mooney, P.E.
Striving to live Aloha
finishing.com - Pine Beach, New Jersey
1997
During the first 24 hours the chem film coating is drying from a quasi gel film. Care must be taken not to remove this "gel" Hot water above 140, skin temperatures above 220, and handling will disturb the surface. One of the best ways is forced hot air, the higher the pressure the better. Good luck.
Dan Zinman1997
We found that a couple of hours in direct sunlight (in Florida) really accelerated the setting. My real recommendation is that you start the process one day earlier so that it can set the required 24 hours. It is there for good reasons.
James Watts- Navarre, Florida
1997
We have an automated process line that produces Alodined parts that are fairly immune to scratches. Parts are dipped into a heated D.I. rinse at 140 deg F. for 20 - 30 seconds and then placed into a drying oven set at 135 deg. F. The Alodine coating will become dehydrated if exposed to temperatures in excess of 140 °F. Dehydration of the coating reduces it's corrosion protection, so take care. Also, the heated rinse tends to remove the coating. (referred to as bleaching the part)
Parts with sharp edges still have to be individually wrapped.
Joe D. Allbritten- Greenville, Texas
1997
I have a question about Alodine chemical coatings in small business. Is there any type of filtration system that allows you to reuse this product to cut down on the amount of hazardous waste that is generated? Our system consists of 1 product tank, followed by a rinse tank. The carry over ends up making the rinse tank as dark as the product.
Any suggestions would be greatly appreciated!
Brad Beckham- New London, Connecticut
2001
Q, A, or Comment on THIS thread -or- Start a NEW Thread