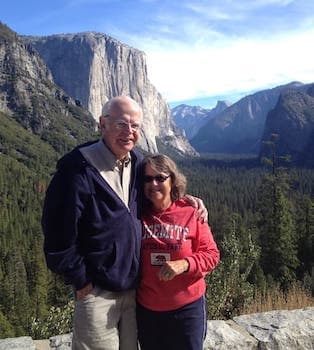
Curated with aloha by
Ted Mooney, P.E. RET
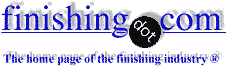
The authoritative public forum
for Metal Finishing 1989-2025
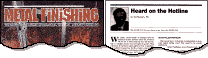
Thread 07/30
Anodized surface for electrical insulation
1998
I'm interested in learning more about anodized aluminum, specifically whether it can reliably be used as an electrical insulator. As I understand the finish, it's primarily aluminum oxide (alumina ceramic) which is a common material for electrical isolation. I'm considering hard anodization, to resist abrasion. Is this a common practice, and to what voltage? Are there specific ways to call out the finish for this application? Any comments would be appreciated.
Charlie Amsdenpublicly reply to Charlie Amsden
Anodize and hardcoat anodize are very good electrical insulators. Dielectric breakdown values greater than 2,000 volts have been reported for hard anodize. Of course, these are laboratory conditions. In practice, the coating quality and thickness, base aluminum alloy, surface finish, sealing method, racking technique, and part geometry all effect the insulating properties. We run a number of jobs in our shop where hardcoat anodize is specified primarily for electrical isolation. Wear and corrosion resistance are secondary benefits. In high performance applications, a two mil (50 um) coating thickness is usually specified. Grounding or part to part continuity can be achieved by masking off contact areas.
Chris Jurey, Past-President IHAALuke Engineering & Mfg. Co. Inc.

Wadsworth, Ohio
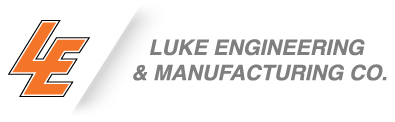
1998
publicly reply to Chris Jurey
Our facility produces oxide insulated aluminum conductors for the electromagnetic industry here in the U.S.. The concept is to produce anodized coils in continuous form that eliminates the need for any organic interleaving in the coils. Produced with a .0002" thick anodic coating, the coils used in separating equipment and sensors is capable of easily withstanding power inputs used in the magnetic industry.
Jason Von Marschner- Pomona, California
2001
publicly reply to Jason Von Marschner
Q, A, or Comment on THIS thread -or- Start a NEW Thread