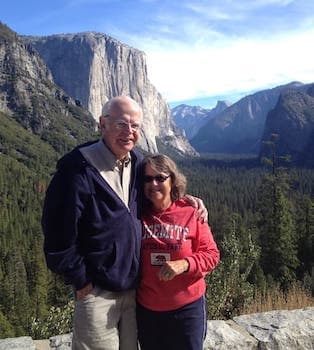
Curated with aloha by
Ted Mooney, P.E. RET
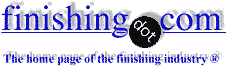
The authoritative public forum
for Metal Finishing 1989-2025
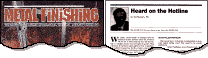
-----
QQP-35C Passivation Treatments For Corrosion Resistant Steel Q&A's about
Q. I am looking for equivalent articles to Federal Specification QQ-P-35C [from DLA] Passivation Treatments For Corrosion Resistant Steel ?
And, looking for corrosion protection treatment process over 302, 304, 316 and 410 Stainless Steel which can stands for more than 2000 hours of neutral salt spray fog test as per ASTM B117 ?
Ricks Lam- Hong Kong
1998
A. We have been using an electropolishing process and achieving great results.
John Simon1997
Thanks, John, I have many times seen references to electropolishing being a better passivation process than passivation itself.
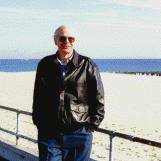
Ted Mooney, P.E.
Striving to live Aloha
finishing.com - Pine Beach, New Jersey
A. Hi Ricks,
As John and Ted said, electropolishing is an effective method for improving the corrosion resistance of stainless steels. According to my experience, pulsely anodized stainless steels in mixed acids can pass the test with respect to ASTM B117.
Ling Hao- Grand Rapids, Michigan
1997
A. Dear Ricks Lam:
Several Organic finishes will provide in excess of 2000 hours salt spray testing on mild steel. I'm certain these coatings would provide adequate protection on stainless steel as well.
Edward Koneczny- Birmingham, Michigan
1998
1997
Q. I have a question. How much can a nitric acid passivation solution tolerate in terms of impurities before one has to dump all or part of the bath? Should be something published out there. I have a copy of QQ-P-35 coming, which may provide some guidance.
Steve SchachameyerEaton Corporation - Milwaukee, Wisconsin
----
Ed. note: We advise with sadness that Mr. Schachameyer, a former AESF President, has since passed away.
A. To: Steve
QQ-P-35C allows a maximum of 7.5 grams / liter iron (Fe) for Type II and Type IV solutions. The maximum allowable interval for checking this is three (3) months. MMA monitors iron (Fe), chromium (Cr) and copper (Cu) content monthly, both to meet the specification requirements, and to ensure proper disposal of the acid when required. The most cost effective method of reducing the contamination content is dilution with new acid solution. If possible, siphon approximately 25 % of the tank from the bottom, much like you would clean an aquarium, and replace with fresh acid.
Matthew Horton- St. Paul, Minnesota
1997
![]() |
Please remember in referencing ASTM ASTM B117 that it does not define failure, or any rating system. B-117 only defines the conditions inside the cabinet and recommended apparatus. ![]() Jeff Watson - Pearland, Texas 1997 |
Q. I am trying to find a simple method to polish stainless steel components, because of their design it is not possible to undertake this process manually/mechanically, if they are coated with nitric acid and then cleaned with a pressure water system it will leave them with a dull appearance, what I am looking for is bright finish.
If anyone can be of help please.
David Tobin1998
A. Hi David, this probably requires electropolishing rather than dipping in a passivation solution. Please read on ...
Regards,
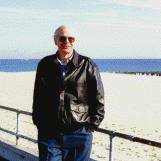
Ted Mooney, P.E.
Striving to live Aloha
finishing.com - Pine Beach, New Jersey
August 2014
Q. Dear Sir,
I do not have anything to contribute to your problems, but is there somebody out there who could help me, to set up a small Electropolishing Plant. And advise me what is required.
We rebuild & refurbish, stainless steel outboard motor propellers, and manufacture stainless steel boating components, and polish units by hand.
Hoping somebody can help!
Yours Faithfully,
Kevin Ypinazar(E-pin-na-zar)welding - Australia
1998
A. Hi Kevin,
Please see if you can get your hands on a copy of the Electroplating Engineering Handbook, which has an excellent chapter on electropolishing, and which will also introduce you to details about the related equipment
I don't think anybody can or will design an electropolishing plant for you for free via casual public responses here. You may wish to hire a consult in this field (some are listed at www.finishing.com/consultants and others may respond to your inquiry when they see it here), or you can ask equipment vendors (www.finishing.com/equipment) to quote you what they think you need.
adv.
Metal Coating Process Corporation is a specialist in this field, and conducts training sessions in electropolishing.
Good luck!
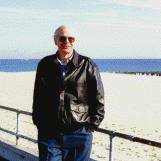
Ted Mooney, P.E.
Striving to live Aloha
finishing.com - Pine Beach, New Jersey
A. Electropolishing of 300 series shall hold good after doing electropolishing. The process is degrease -- rinse well -- dip in 5% phosphoric acid and load to electropolishing anode bus bar with 100% pure lead sheets as cathodes fully covering on either side. Electrolyte consists of Phosphoric acid 85% concentrate and sulfuric acid 1.84 specific gravity. YOU have to add 50% sulfuric acid and 50% phosphoric acid equally mixed in concentrated form -- be sure not to add anything including DM water. Now electrolyze keeping SS job as anode in titanium jigs. Voltage 4 to 7 volts and amperage depends on area of job. Time 2 to 3 minutes depending on area of job loaded. After electropolishing the job has to be rinsed in DM water and then dipped in chromic acid solution 250 grams per litre of DM water to remove the viscous film and to be super bright forever. Finally wipe off in yellow silver oak saw dust for best finish.
chennamallu prakashamconsultancy - Chennai, Tamilnadu, INDIA
August 8, 2014
Q. How do I find/obtain federal spec QQ-P-35C for passivation?
Frank Pagenoble-met, limited
1998
A. QQ-P-35C [from DLA] is cancelled, Frank. But you may wish to use it's replacement, ASTM A967.
Although some people sometimes must work to such "dead" specs, it's a good idea to try to change them because even if it is found that there is something flagrantly wrong with the dead spec, no mechanism exists to change it :-)
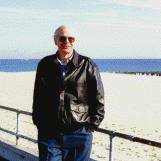
Ted Mooney, P.E.
Striving to live Aloha
finishing.com - Pine Beach, New Jersey
Q. I have been having problems with passivating 316SS after polishing was done. The surface finish is 24 micoinches before being placed in the bath. The bath is a standard 50-2-48 mix, its also a new mix. The problem seems to be in the machining itself. The surface is porous enough to trap the coolant, which reacts with the bath.
Are there any precautions that could be made prevent this, or should we start looking into a different alloy?
We've had this problem before with 400 series stainless and also heat treated stainless.
I've also heard that maybe electropolishing is the way to go. Any comments or suggestions on this subject would be greatly appreciated.
Thank-you,
Kevin LavigneThorlabs
1998
Q. Does anybody know if ASTM A967 contains specs on electropolishing or if there are any standards out there on the process?
Thanks,
Jason Corley- Austin, Texas
1998
Q. I am interested in performing my own passivation in house via citric acid. I am having difficulty finding someone to supply me with the chemicals and any equipment I would need to perform this operation. If someone knows where I could find what I need please let me know. Thank you
Scott Feustel, Q.A. manager- Englewood, Florida
1998
A. You can contact [finishing.com's supporting advertiser] Lee Kremer at Stellar Solutions [a finishing.com supporting advertiser] for whatever type of citric acid you may require. See ya'...
Michael J. Cochara- Springfield, Missouri
2000
Q, A, or Comment on THIS thread -or- Start a NEW Thread